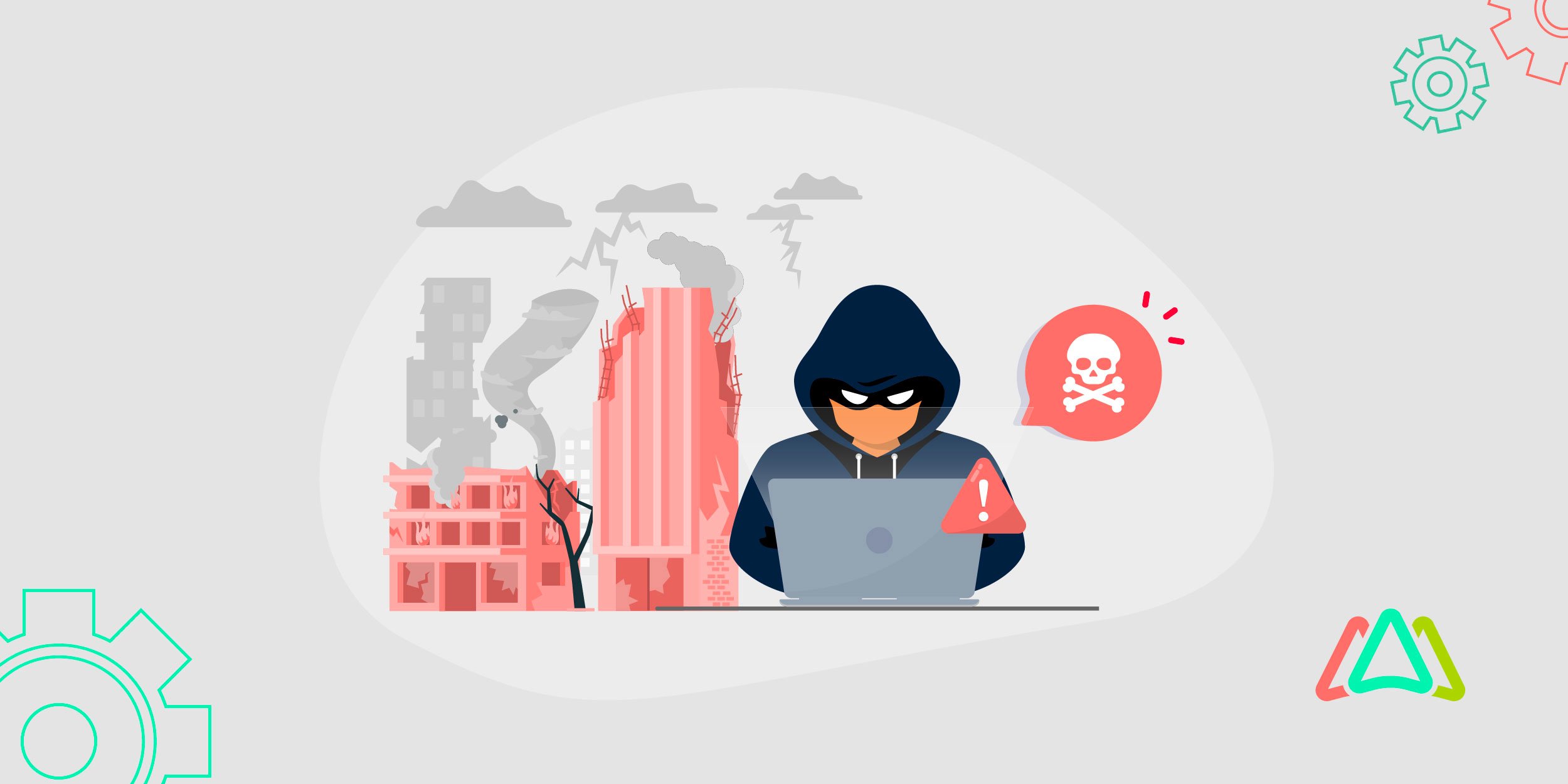
CMMS in Disaster Recovery Planning
Maintenance managers understand that disasters are unpredictable and can have a massive negative impact. Whether it's a cyber attack that cripples your systems, a natural disaster like a hurricane or earthquake that floods or damages your facility, a power outage that shuts down critical equipment, or a pandemic that disrupts your workforce, every unplanned catastrophe threatens to destroy years of operational excellence in mere hours. For an effective maintenance team, the difference between a quick recovery and prolonged downtime often lies in the systems they rely on.
Here's the sobering reality: According to the Federal Emergency Management Agency (FEMA), nearly 43% of small businesses fail to reopen after a disaster, and an additional 29% shut down within two years. These statistics underscore the critical importance of effective disaster recovery planning. But what if your maintenance management system could be the difference between organizational survival and business failure?
Computerized Maintenance Management Systems (CMMS) aren’t just a digital logbook; they also play a fundamental role in minimizing the risk of disasters. They serve as the operational backbone that transforms chaotic disaster scenarios into coordinated recovery operations. CMMS ensures critical assets are restored, teams stay connected, and regulatory compliance is maintained even under the most challenging circumstances. This article explores in detail how CMMS platforms help maintenance teams prepare for the unexpected, respond with precision, and build long-term operational resilience.
What is Disaster Recovery Planning?
Disaster recovery planning (DRP) is the process of preparing an organization to quickly restore operations after unexpected disruptions such as natural disasters, cyberattacks, or equipment failures. It outlines strategies to protect critical assets, ensure data integrity, and maintain essential services. A solid disaster recovery plan helps organizations react to crises with clarity and coordination, minimizes downtime, and lowers financial losses. It is an essential component of operational resilience for maintenance teams.
Challenges in Disaster Recovery
Disasters expose the vulnerabilities hidden within seemingly robust maintenance operations. Maintenance teams face challenges that paralyze even the most experienced organizations when crises strike. Here are the common challenges maintenance teams face during disaster recovery:
Asset Location and Access Disruption
Disasters can damage or displace equipment and block access to facilities. Without clear asset visibility, technicians lose track of what needs fixing and its location, slowing response time.
Communication Breakdowns Across Teams
When power or network systems go down, so does coordination. Teams can’t send or receive work orders, supervisors can’t monitor progress, and third-party support becomes unreachable.
Missing or Inaccessible Documentation
Important records like maintenance logs, warranty details, and inspection histories may be lost or locked in offline systems. This delays insurance claims, audits, and critical repairs.
Resource and Workforce Shortages
Emergencies often reduce the available workforce and disrupt access to tools, parts, or suppliers. Maintenance teams are left scrambling to operate with limited support and increased pressure.
Unplanned Downtime Escalation
Minor disruptions can grow into major outages without fast diagnostics and historical data. Lack of clarity on system health makes it difficult to contain the damage quickly.
Prioritization Under Pressure
Knowing what to fix first becomes overwhelming when multiple failures hit at once. Without a structured system for asset criticality, teams risk wasting effort while vital systems stay down.
How CMMS Transforms Disaster Recovery
Computerized Maintenance Management Systems (CMMS) are not just digital tools for scheduling work orders; they are critical infrastructure for resilience. A well-implemented CMMS can transform disaster recovery, providing maintenance teams with speed, clarity, and control during and after disasters. Here’s how CMMS can be a game-changer in your disaster recovery strategy.
Instant Asset Visibility and Control
A CMMS Software centralizes all asset data, including location, condition, service history, and criticality. In disaster scenarios, this visibility helps teams identify high-priority equipment, determine what’s operational, and locate backup systems or parts without guesswork.
Accelerated Recovery Operations
CMMS systems allow pre-configured emergency workflows, rapid work order generation, and automated task assignment. This speeds up damage assessments, recovery prioritization, and repair execution, minimizing unplanned downtime and chaos.
Maintaining Compliance in Crisis Conditions
Audit trail maintenance becomes automatic through CMMS logging capabilities that capture all maintenance activities, decisions, and resource usage. This systematic approach protects personnel while ensuring regulatory requirements are met, even during emergencies.
Real-Time Communication and Coordination
Today’s CMMS tools make it easier for everyone to stay connected, no matter where they are. With features like mobile access, built-in messaging, and live updates, technicians, managers, and even outside vendors can stay in sync whether they’re on-site, working remotely, or out in the field. This helps prevent the kind of miscommunication that slows things down during an emergency.
Centralized Documentation Access
All critical records, like maintenance logs, inspection checklists, compliance reports, and asset specifications, are stored digitally and securely. Even if physical files are lost, teams can access everything they need from the cloud to support insurance claims, audits, or regulatory reviews.
Data-Driven Decision Making Under Pressure
A CMMS enables informed decisions during emergencies. With access to historical maintenance data, failure trends, and asset criticality ratings, teams can focus resources on the most significant operational impact.
Building Your CMMS Disaster Recovery Plan
Implementing effective CMMS disaster recovery capabilities requires systematic planning that addresses your organization's specific risks and requirements.
Assess Critical Assets and Failure Impact
Start by conducting a comprehensive asset criticality analysis considering production impact, safety implications, regulatory requirements, and replacement costs. Rank all equipment using consistent criteria and document the business impact of each asset's failure. This ranking becomes the foundation for all subsequent disaster recovery planning.
Create detailed asset dependency maps showing how equipment failures cascade through operations. Understanding these dependencies helps predict which systems will be affected by specific disaster scenarios and guides recovery sequencing decisions.
Configure Emergency Workflows and Alerts
Set up automated alert thresholds that trigger emergency notifications when critical equipment parameters exceed safe operating ranges. Configure these alerts to reach appropriate personnel through multiple communication channels with automatic escalation procedures.
Create standardized emergency work order templates for common disaster scenarios, including equipment damage assessment, emergency repairs, and safety system restoration. These templates should include detailed procedures, safety requirements, and resource specifications.
Establish Data Backup and Mobile Access
Set up your system to back up important maintenance data automatically and often. Make sure those backups are saved in secure, off-site locations. Don’t wait for a crisis to find out something’s broken. Run regular tests to confirm your backups are complete, reliable, and can be restored quickly when needed.
Set up mobile access capabilities, enabling field technicians to access CMMS functions even when the primary network infrastructure is compromised. Ensure mobile applications can operate offline and synchronize data automatically when connectivity is restored.
Organizations must be prepared to overcome predictable implementation challenges even with robust planning.
Overcoming Common Implementation Challenges
Even well-planned CMMS disaster recovery implementations face predictable challenges that can undermine effectiveness during emergencies.
Data Access During System Outages
The most immediate challenge during disasters is maintaining access to critical maintenance data when primary systems are compromised. In 2024, organizations reported a mean cost of USD 3.76 million to recover from a ransomware attack, highlighting the vulnerability of connected systems during cyber incidents.
Offline mobile capabilities provide primary mitigation for data access challenges. Modern CMMS mobile applications include robust offline functionality, allowing technicians to access recently synchronized work orders, asset information, and procedural documents without network connectivity.
Cloud redundancy and failover protocols provide system-level protection against data access disruptions. Leading CMMS platforms implement automatic failover systems that redirect users to backup data centers when primary systems become unavailable.
Communication Breakdown During Emergencies
Multi-channel notification systems provide redundancy, ensuring critical messages reach intended recipients despite communication infrastructure failures. CMMS platforms should support automatic message delivery through email, SMS, voice calls, mobile push notifications, and social media channels.
Predetermined communication hierarchies and escalation procedures help maintain the organization when typical supervisory structures are disrupted. CMMS systems should include configurable communication trees that automatically adjust when key personnel are unavailable.
Resource Coordination Under Pressure
Pre-configured emergency resource pools help maintenance managers quickly deploy appropriate personnel and equipment for disaster recovery operations. CMMS platforms should maintain databases of qualified emergency responders, specialized equipment, and approved contractors that can be activated immediately.
Real-time resource tracking capabilities help maintenance managers optimize deployment decisions as situations evolve. CMMS platforms should provide visibility into personnel locations, equipment availability, and task progress to enable dynamic resource reallocation.
Understanding these solutions positions your organization to embrace the emerging technologies that will shape the future of disaster recovery.
Future Trends in CMMS Disaster Recovery
The evolution of CMMS disaster recovery capabilities continues to accelerate, driven by advancing technologies and increasing recognition of maintenance management's critical role in organizational resilience.
Artificial intelligence and machine learning integration will transform disaster recovery from reactive response to predictive preparation. AI-powered CMMS platforms will analyze historical disaster data, weather patterns, and equipment condition trends to predict likely failure scenarios and automatically pre-position resources for optimal response.
IoT sensor integration will provide real-time facility and equipment monitoring, enabling immediate damage assessment and recovery prioritization. Connected sensors throughout facilities will automatically report damage, environmental conditions, and equipment status directly to CMMS platforms.
Digital twin technology will enable virtual disaster scenario testing and recovery optimization. Maintenance managers can model disaster impacts on virtual facility replicas and test different recovery strategies to identify optimal approaches before disasters occur.
These emerging capabilities make it clear that the time for action is now.
Conclusion - Resilience with CMMS Software
Disaster recovery isn’t just about reacting; it’s about building the capacity to adapt and restore operations quickly under pressure. A well-implemented CMMS equips maintenance teams with real-time asset visibility, centralized data, automated workflows, and mobile access.
Evaluate your existing CMMS platform's disaster recovery features or begin the selection process for systems providing robust emergency management capabilities. Implement a phased approach starting with your highest-value, highest-risk assets where avoided downtime delivers the most significant benefits.
The question isn't whether disasters will affect your operations; it's whether your maintenance management systems will be ready to respond effectively when they do.
TABLE OF CONTENTS
Keep Reading
What happens when your most experienced maintenance leader is planning on retiring, taking 20 ...
7 Aug 2025
Today’s maintenance operations have become more complex and sophisticated. Gone are the days ...
5 Aug 2025
Modern warehouses are instrumental to maintaining the smooth operations of supply chains, ...
1 Aug 2025
Computerized Maintenance Management Systems (CMMS) have proven to be essential tools for ...
31 Jul 2025
Sometimes it feels as if technology is expanding at the speed of light. This is an ...
29 Jul 2025
Data Center downtime can have a huge negative impact ranging from damage to the data center’s ...
25 Jul 2025
Whenever a company introduces a new process or technology, it’s followed by a period of ...
24 Jul 2025
Obsolescence often comes unexpectedly, mainly because little attention is given to the ...
22 Jul 2025
Imagine a world where critical assets run smoothly without unexpected downtime, maintenance ...
18 Jul 2025
Imagine you're going through a compliance audit, and the inspector asks for maintenance ...
10 Jul 2025
Asset lifespan is a key concern for executives and maintenance and facility management teams. ...
3 Jul 2025
Your company recently invested funds and time for new CMMS software, and six months later, it ...
1 Jul 2025
As Computerized Maintenance Management Systems (CMMS) become more connected and cloud-based, ...
1 Jul 2025
Edge computing is an innovative technology that enables data to be processed at the source, ...
24 Jun 2025
Facility management has undergone a significant transformation in recent times. Take, for ...
20 Jun 2025
A facility maintenance plan is at the core of a facility’s operations. This organized ...
19 Jun 2025
In the early days, preventive maintenance could be done effectively with a trained eye and a ...
17 Jun 2025
Sticky notes fall off, whiteboard grids get wiped, and spreadsheets never beep when a ...
13 Jun 2025
Handing a slice of your maintenance workload to a contractor is less about “giving up ...
12 Jun 2025
Downtime in enterprise environments doesn’t just mean a stop in operations; it means lost ...
10 Jun 2025