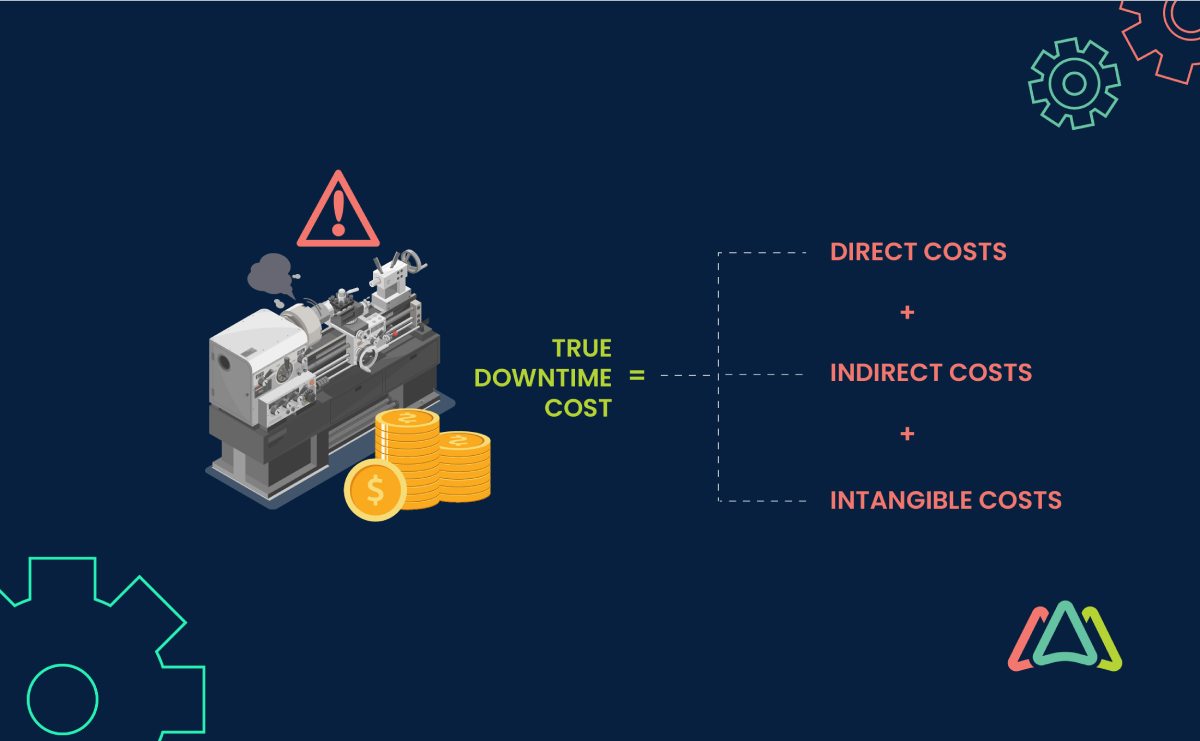
Recognizing & Minimizing True Downtime Cost in Maintenance
Time is money and every minute of equipment downtime, whether planned or unplanned, has a significant impact on an organization's bottom line. This article dives into the importance of recognizing “true downtime cost”, understanding the real impact it has on organizations, how it is calculated, and strategies to minimize it.
Equipment breakdowns, failures, and unscheduled maintenance can lead to costly disruptions in production and operations. These examples of equipment downtime can range from a few minutes to hours or even days, depending on the severity of the issue.
In the pursuit of maximizing equipment uptime and reducing costs, true downtime cost analysis is a valuable tool. The concept of true downtime cost goes beyond obvious expenses incurred during equipment breakdowns and repairs. It encompasses both the direct and indirect costs associated with downtime events, providing a comprehensive picture of the financial implications faced by maintenance professionals and their organizations.
What is the True Downtime Cost?
True Downtime Cost refers to the comprehensive assessment of all expenses incurred during equipment downtime. Unlike conventional approaches that merely account for obvious repair costs, true downtime considers hidden, less obvious costs. In other words, true downtime cost encompasses both direct and indirect expenses associated with the disruption of equipment or asset operations.
Direct costs include tangible expenses directly linked to the repair and restoration of the equipment. These costs may involve labor, spare parts, and external service charges. On the other hand, indirect costs are less apparent and include expenses such as lost production revenue, overtime wages, administrative overhead, and even intangible factors like damage to the organization's reputation.
Understanding true downtime cost enables maintenance professionals and organizations to make informed decisions about maintenance strategies, resource allocation, and risk mitigation. By quantifying the financial impact of downtime events, managers can optimize their approaches, reduce downtime incidents, and maximize operational efficiency.
Impact of Downtime on Maintenance Operations
Downtime is an inevitable aspect of maintenance operations, and its impact can be far-reaching, affecting multiple facets of an organization's functioning.
Firstly, it disrupts production schedules, leading to delays in meeting customer demands and fulfilling contractual obligations. This can result in financial penalties, loss of market share, and even damage to customer trust and loyalty.
Secondly, unplanned downtime often leads to reactive maintenance, where maintenance teams are forced to handle emergency repairs, causing additional stress and strain on resources. This reactive approach is typically more time-consuming and expensive than planned maintenance, affecting the overall efficiency of the maintenance department.
4 Key Factors that Influence True Downtime Cost
1. Equipment Criticality and Failure Impact Analysis
1.1 Identify Critical Equipment
Not all assets are equal in terms of their impact on operations and revenue. Identifying critical equipment is an important step in understanding true downtime cost. Critical equipment refers to assets that, if they were to fail, would significantly disrupt production, affect safety, or have severe financial implications.
Maintenance professionals can use the Equipment Criticality Assessment Matrix to conduct a criticality analysis by assessing factors such as asset function, its role in the production process, historical failure data, and safety considerations. By prioritizing maintenance efforts on critical equipment, organizations can effectively manage risks associated with equipment downtime and allocate resources more efficiently.
1.2 Evaluate the Impact of Equipment Failure
The consequences of equipment failure extend beyond repair costs. Maintenance professionals need to conduct a thorough analysis of the impact to understand the true implications of potential failures. This analysis should consider factors like lost production revenue, labor costs during downtime, and the potential for safety incidents. Understanding the broader impact of equipment failure enables better decision-making and risk mitigation strategies.
2. Mean Time Between Failures (MTBF) and Mean Time to Repair (MTTR)
2.1 Calculate MTBF
MTBF is a vital reliability metric used to assess the average time between equipment failures. It is calculated by dividing the total operational time of the equipment by the number of failures during that period. A higher MTBF indicates increased equipment reliability and longer periods of uninterrupted operation.
2.2 Reduce MTTR through Efficient Maintenance Practices
MTTR represents the average time it takes to repair a failed piece of equipment and return it to full functionality. Reducing MTTR is critical for minimizing downtime costs. Efficient maintenance practices, such as implementing standardized repair procedures, ensuring technicians have access to necessary tools and spare parts, and offering continuous training, can significantly decrease MTTR.
3. Maintenance Planning and Scheduling
3.1 Importance of Effective Planning
A well-structured maintenance plan includes scheduled preventive maintenance, predictive maintenance, and calibration activities. By planning maintenance tasks in advance, maintenance professionals can ensure that resources, equipment, and spare parts are readily available when needed, reducing downtime and disruptions.
3.2 Optimize Scheduling for Reduced Downtime Cost
Organizations can implement techniques like condition-based maintenance, which involves planned maintenance activities based on equipment condition data rather than fixed time intervals. This proactive approach reduces the likelihood of equipment failure during operation, minimizing downtime and its associated costs.
4. Spare Parts Management
4.1 Avoid Stock Outages and Excess Inventory
Having the right spare parts readily available eliminates delays in repairs. However, excessive inventory ties up capital and increases carrying costs. Effective spare parts management strikes a balance between ensuring availability and minimizing excess inventory.
4.2 Implement Just-in-Time (JIT) Inventory Strategies
JIT involves procuring spare parts and materials just before they are needed, reducing storage costs and the risk of obsolescence. Adopting JIT principles ensures that the right parts are available precisely when required, improving maintenance efficiency and reducing downtime cost.
Calculating True Downtime Cost
Accurately calculating true downtime cost goes beyond direct repair expenses by including indirect costs as well as intangible factors. Let's explore the steps involved in calculating true downtime cost:
1. Direct Costs Calculation
1.1 Labor Costs
Labor costs include the wages and benefits paid to maintenance technicians and other personnel involved in equipment repairs. To calculate labor costs during downtime, multiply the number of hours each technician spent on repairs by their hourly wage.
1.2 Equipment Repair or Replacement Costs
This includes the expenses incurred in restoring or replacing damaged or faulty parts. Calculate the total cost of the repair or replacement, including the cost of spare parts, materials, and any additional equipment necessary for the restoration.
1.3 Spare Parts Costs
Downtime often requires the use of spare parts. Calculate the total cost of the spare parts used during the maintenance activity, including their purchase cost and any associated shipping or handling fees.
1.4 External Service Costs
In some cases, maintenance tasks may require outsourcing to external service providers or 3rd party vendors. Include the charges of these external services in the direct cost calculation.
2. Indirect Costs Calculation
2.1 Lost Downtime Revenue
One of the most significant components of true downtime cost is the revenue lost during the period of equipment downtime. To calculate lost revenue, multiply the hourly production rate (units produced per hour) by the number of downtime hours. Then, multiply this value by the average revenue generated per unit.
2.2 Overtime Costs
During downtime, organizations might require employees to work overtime to compensate for lost production time. Calculate the overtime costs by multiplying the number of overtime hours by the overtime pay rate.
2.3 Administrative Overhead
Downtime events demand administrative efforts to coordinate repairs, manage communications, and reschedule production. Estimate the cost of these administrative activities during downtime.
3. Factoring in Intangible Costs
3.1 Reputation Damage
Downtime incidents can lead to negative publicity, customer dissatisfaction, and damage to the organization's reputation. While challenging to quantify precisely, consider the potential long-term impact on brand image and customer loyalty. One can look at negative reviews or customer references that resulted in loss of business. Another example is canceled orders due to damaged reputation.
3.2 Safety Incidents and Insurance Costs
Downtime can increase the risk of safety incidents, leading to additional expenses such as worker compensation claims and potential insurance premium hikes. Account for these potential costs in the intangible cost calculation.
By summing up the direct costs, indirect costs, and factoring in the intangible costs, you can arrive at the true downtime cost. To improve the accuracy of your true downtime cost calculations, maintain detailed records of maintenance activities, equipment downtime, labor hours, and expenditures. Regularly review and update these calculations to reflect changes in production rates, labor costs, and other factors that may influence downtime cost over time.
Strategies for Reducing True Downtime Cost
1. Implement Preventive Maintenance
1.1 Benefits of Preventive Maintenance
Preventive Maintenance is a proactive approach that involves regularly scheduled inspections, repairs, and replacements to prevent equipment failures before they occur. The key benefits of preventive maintenance include increased equipment reliability, extended asset lifespan, reduced downtime incidents, and minimized maintenance costs over time.
1.2 Establish a Preventive Maintenance Plan
To implement an effective preventive maintenance plan, start by conducting an equipment risk assessment and criticality analysis. This will help identify high-priority assets that require regular inspections and maintenance. Develop a detailed maintenance schedule, create maintenance checklists and SOPs, and document all maintenance activities to ensure consistency and accountability.
2. Condition-Based Maintenance
2.1 Apply Predictive Maintenance
Condition-Based Maintenance (CBM) relies on real-time data and predictive analytics to assess equipment health and determine the optimal time for maintenance. Utilizing sensors and monitoring equipment, CBM continuously tracks key parameters such as temperature, vibration, and fluid levels to detect anomalies and potential failures before they happen.
2.2 Monitoring and Data Analysis
Investing in advanced monitoring technologies and data analysis tools is important for effective CBM implementation. Regularly monitor equipment data and analyze trends to identify patterns that may indicate early signs of deterioration or impending failures.
3. Root Cause Analysis and Failure Mode Effect Analysis (FMEA)
3.1 Identify Root Causes of Failures
Root Cause Analysis (RCA) involves investigating the underlying reasons for equipment failures rather than just addressing the symptoms. By identifying the root causes, maintenance professionals can implement targeted corrective actions to prevent future occurrences.
3.2 Mitigate Failure Risks through FMEA
Failure Mode Effect Analysis (FMEA) is a systematic approach used to identify potential failure modes and their effects on equipment. By analyzing failure risks, maintenance teams can prioritize actions to reduce the probability and severity of failures. This approach enhances equipment reliability and minimizes unplanned downtime.
4. Training and Skill Development
4.1 Continuous Education for Maintenance Professionals
Keep maintenance professionals up-to-date with the latest industry practices, technologies, and equipment-specific training. Continuous education programs, workshops, and certifications empower maintenance technicians with the knowledge and skills needed to perform their tasks more efficiently. Check out our Maintenance Management Glossary for an easy to use resource that allows maintenance professionals to stay on top of the latest terminology.
4.2 Build a Skilled Workforce
Invest in talent development and career growth opportunities to foster a skilled and motivated maintenance workforce. Providing mentoring programs and cross-training opportunities enables employees to gain expertise in multiple areas, leading to a more versatile and adaptable team.
5. Implement CMMS Software and Technology
5.1 CMMS
CMMS software streamlines maintenance processes, enabling maintenance professionals to plan, schedule, and track maintenance activities more effectively. CMMS systems help automate work orders, manage spare parts inventory, and maintain comprehensive maintenance records, reducing administrative overhead and improving overall maintenance efficiency.
5.2 Internet of Things (IoT) and Sensor Technology
Leverage IoT and sensor technology to enable remote monitoring and real-time data collection from equipment. Sensors can provide critical data on equipment health, performance, and potential failures, allowing maintenance professionals to make data-driven decisions and perform maintenance proactively.
The journey towards reducing true downtime cost requires dedication and commitment from maintenance professionals and executives. By adopting effective downtime cost management practices, maintenance teams can pave the way for improved operational efficiency, reduced downtime, increased customer satisfaction and enhanced equipment reliability.
As technology continues to evolve and industries become more competitive, organizations must prioritize downtime cost management as a strategic imperative. Proactive maintenance approaches, continuous training, and the implementation of advanced technologies will set organizations on a path to success, where downtime incidents become the exception rather than the norm.
TABLE OF CONTENTS
Keep Reading
Computerized Maintenance Management Systems (CMMS) have increasingly become the go-to tools ...
19 Aug 2025
It doesn’t seem to matter which energy provider you choose; the bottom line is that energy ...
15 Aug 2025
In FDA-regulated industries such as pharmaceuticals, medical devices, biotechnology, and food ...
14 Aug 2025
B2C businesses, such as retail, hospitality, and food service, operate in a highly ...
8 Aug 2025
What happens when your most experienced maintenance leader is planning on retiring, taking 20 ...
7 Aug 2025
Today’s maintenance operations have become more complex and sophisticated. Gone are the days ...
5 Aug 2025
Modern warehouses are instrumental to maintaining the smooth operations of supply chains, ...
1 Aug 2025
Computerized Maintenance Management Systems (CMMS) have proven to be essential tools for ...
31 Jul 2025
Sometimes it feels as if technology is expanding at the speed of light. This is an ...
29 Jul 2025
Data Center downtime can have a huge negative impact ranging from damage to the data center’s ...
25 Jul 2025
Whenever a company introduces a new process or technology, it’s followed by a period of ...
24 Jul 2025
Obsolescence often comes unexpectedly, mainly because little attention is given to the ...
22 Jul 2025
Imagine a world where critical assets run smoothly without unexpected downtime, maintenance ...
18 Jul 2025
Imagine you're going through a compliance audit, and the inspector asks for maintenance ...
10 Jul 2025
Maintenance managers understand that disasters are unpredictable and can have a massive ...
4 Jul 2025
Asset lifespan is a key concern for executives and maintenance and facility management teams. ...
3 Jul 2025
Your company recently invested funds and time for new CMMS software, and six months later, it ...
1 Jul 2025
As Computerized Maintenance Management Systems (CMMS) become more connected and cloud-based, ...
1 Jul 2025
Edge computing is an innovative technology that enables data to be processed at the source, ...
24 Jun 2025
Facility management has undergone a significant transformation in recent times. Take, for ...
20 Jun 2025