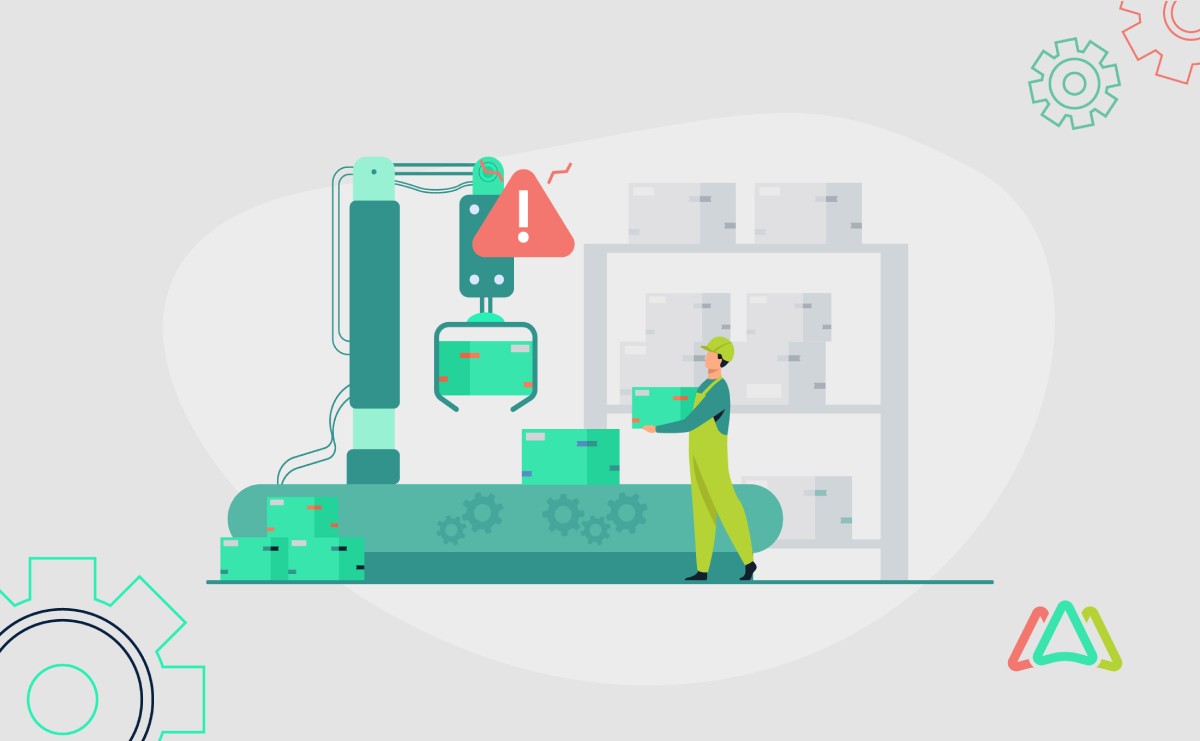
The Impact of Fault Tolerance on Equipment Reliability
In maintenance operations, fault tolerance refers to the ability of a system, equipment, or process to continue functioning without interruption, even in the presence of faults or failures. It's like having a backup plan to ensure that essential operations don't come to a halt when something goes wrong.
Fault tolerance is about proactively mitigating the impact of unexpected issues and ensuring maintenance professionals can maintain operations smoothly, especially in critical industries like manufacturing, healthcare, energy, and more. For maintenance professionals, fault tolerance is critical because it directly affects their ability to keep equipment and systems running efficiently.
This article covers the intricate relationship between fault tolerance and equipment reliability, offering valuable insights to maintenance professionals and anyone interested in ensuring the seamless operation of machinery and systems. It explores how fault tolerance strategies and practices significantly enhance equipment reliability, leading to improved performance, reduced costs, and increased safety across various industries.
Significance of Equipment Reliability
Equipment reliability is the cornerstone of operational success for any organization. It refers to the ability of machines, systems, and processes to consistently perform their intended functions without failure. The significance of equipment reliability can hardly be overstated:
- Reduced Downtime: Reliable equipment is less likely to break down, reducing downtime and improving productivity.
- Consistent Output: In manufacturing, reliable machinery consistently ensures that products meet quality standards.
- Safety: Equipment reliability is important for safety. Think of the importance of reliable brakes in a vehicle or life support systems in hospitals.
- Cost Savings: Maintaining and repairing equipment proactively is more cost-effective than dealing with costly breakdowns.
Understanding Fault Tolerance
To truly grasp the significance of fault tolerance, it's essential to delve into its underlying concepts. At its core, fault tolerance is about ensuring the reliability and continuity of critical systems, even in the face of adversity. The following are two fundamental concepts that make up the underlying foundation of fault tolerance:
1. Redundancy
Redundancy is a key principle in fault tolerance. It involves the duplication or triplication of critical components within a system or process. The purpose of redundancy is to create backups or fallback mechanisms that can seamlessly take over if the primary component fails. Think of it as a spare tire in your car or a backup generator in a data center. Redundancy manifests in various forms, including hardware redundancy and software redundancy:
- Hardware Redundancy: In this approach, organizations duplicate hardware components such as servers, power supplies, or sensors. If one component fails, another identical one can take its place without disrupting operations.
- Software Redundancy: This involves replicating software processes or applications across multiple servers or systems. If one instance encounters issues, another can continue executing the task without interruption.
2. Error Detection and Correction
Error detection and correction mechanisms are another critical aspect of fault tolerance. These mechanisms are designed to identify and rectify errors or faults that may occur during system operation. They play a proactive role in ensuring data integrity and equipment's seamless functioning. Key components of error detection and correction include:
- Error Codes and Checksums: These are techniques used to verify data integrity. By adding error-checking codes or checksums to transmitted data, errors can be detected and corrected at the receiving end.
- Parity and RAID Systems: In the context of data storage, parity and RAID (Redundant Array of Independent Disks) systems use redundancy to protect against data loss due to disk failures. These systems can reconstruct data from the redundancy information even when one or more disks fail.
Error detection and correction mechanisms are essential for maintaining the accuracy and reliability of data, especially in critical sectors like energy, healthcare, and aerospace.
Fault Tolerance in Various Industries
Fault tolerance is not a one-size-fits-all concept; it adapts to the specific needs and demands of various industries.
1. Healthcare
The healthcare industry relies heavily on fault tolerance to ensure patient safety and the efficient delivery of medical services. In this context, fault tolerance manifests in several ways:
- Medical Devices: Life-critical medical devices, such as ventilators, heart monitors, and infusion pumps, must operate flawlessly. Fault tolerance mechanisms, including redundant sensors and alarms, ensure these devices continue functioning even if a component fails.
- Electronic Health Records (EHRs): In healthcare IT systems, fault tolerance is essential for maintaining access to patient records. Redundant servers and data storage systems guarantee that doctors and healthcare professionals can retrieve critical patient information anytime when needed.
In healthcare, the consequences of equipment failures can be life-threatening. Fault tolerance is not just a convenience but a necessity to safeguard patient well-being.
2. Manufacturing and Industrial Equipment
Fault tolerance is the backbone of manufacturing and industrial processes. Ensuring continuous production and minimizing downtime is essential in these sectors:
- Automated Assembly Lines: Manufacturing plants often employ redundant robotic systems. If one robot malfunctions, another can take over to prevent production interruptions.
- Quality Control: Fault tolerance is essential in quality control systems, where sensor redundancy and error correction mechanisms identify and rectify defects during the production process.
- Power and Energy Systems: In power plants and energy generation facilities, fault tolerance maintains electrical grid stability. Redundant generators and automatic load transfer switches prevent blackouts.
Manufacturing and industrial processes can incur massive losses in the event of equipment failures. Fault tolerance strategies ensure uninterrupted production and contribute to cost savings and product quality.
Role of a CMMS and Understanding the Link Between Fault Tolerance and Equipment Reliability
The link between fault tolerance and equipment reliability is symbiotic. Fault tolerance mechanisms act as the proactive shields that safeguard equipment reliability, while CMMS systems serve as an invaluable tool for maintenance professionals to implement these mechanisms effectively. Together, they help organizations reduce downtime, save costs, enhance safety, and ensure the continuity of their vital operations.
1. Importance of Equipment Reliability
Equipment reliability enables seamless functioning of critical processes and systems.
1.1 Reduced Downtime
When equipment fails unexpectedly, there’s downtime, resulting in lost production hours and missed deadlines. Reliable equipment keeps downtime to a minimum by operating consistently and predictably.
How a CMMS Helps:
A Computerized Maintenance Management System (CMMS) assists in scheduling preventive maintenance, which can identify and rectify potential issues before they lead to downtime. CMMS software also facilitates real-time monitoring, enabling maintenance professionals to respond swiftly to emerging problems.
1.2 Cost Savings
Equipment failures come with a hefty price tag. Emergency repairs, replacement parts, and overtime wages increase operational costs. Equipment reliability helps organizations save money by avoiding these unexpected expenses.
How a CMMS Helps:
CMMS software enables organizations to track maintenance costs, analyze historical data, and make data-driven decisions about equipment maintenance and replacement. This proactive approach can significantly reduce overall maintenance costs.
1.3 Safety Enhancement
In many industries, equipment reliability is directly tied to safety. When equipment functions reliably, it reduces the risk of accidents and injuries. For example, in manufacturing, a reliable machine is less likely to malfunction and cause harm to operators.
How a CMMS Helps:
CMMS software can help organizations implement safety protocols and track compliance with maintenance procedures that ensure equipment operates within safe parameters. It also provides a historical record of maintenance activities, which is often necessary for safety audits and investigations.
2. Role of Fault Tolerance
Fault tolerance serves as a proactive mechanism to uphold the dependability of critical systems and processes. Here is how fault tolerance contributes to equipment reliability:
2.1 Mitigating System Failures
Systems and equipment can experience failures due to various factors, such as component wear, software glitches, or environmental conditions. Fault tolerance strategies, like redundancy, are designed to mitigate these failures. Redundancy ensures that if one part of a system fails, a backup component takes over seamlessly, preventing system-wide breakdowns.
How a CMMS Helps:
CMMS can be integrated with fault detection sensors and alarms. When a fault is detected, the CMMS can trigger maintenance workflows automatically. This integration ensures that maintenance professionals are promptly notified and can address the issue before it escalates into a critical failure.
2.2 Minimizing Unplanned Downtime
Fault tolerance mechanisms, including error detection and correction, help identify and resolve issues before they lead to unplanned downtime. By addressing faults proactively, organizations can maintain operational continuity.
How a CMMS Helps:
CMMS software helps organizations establish preventive maintenance schedules based on equipment usage and performance data. This ensures that maintenance tasks are conducted regularly, reducing the likelihood of unexpected equipment failures.
2.3 Ensuring Continuity of Operations
In critical industries like healthcare, aerospace, and manufacturing, continuity of operations is essential. Fault tolerance ensures that critical systems can continue functioning even in the face of equipment failures, preventing disruptions and maintaining productivity.
How a CMMS Helps:
CMMS provides a centralized platform for managing maintenance processes. This streamlines communication, enables efficient resource allocation, and ensures that maintenance teams are well-prepared to address equipment issues promptly, contributing to operational continuity.
Benefits of Implementing Fault Tolerance
Fault tolerance isn't just a safety net; it's a strategic advantage. Organizations implementing fault tolerance strategies reap many benefits that directly impact their operational efficiency and bottom line. The following are the key advantages of integrating fault tolerance into your systems and processes:
1. Improved Reliability Metrics
Implementing fault tolerance leads to enhanced reliability metrics, which are essential for assessing the performance of equipment and systems:
1.1 Mean Time Between Failure (MTBF)
MTBF measures the average time a system or component operates without experiencing a failure. Implementing fault tolerance increases MTBF significantly because redundant components and error detection mechanisms reduce the likelihood of failures. This extended MTBF directly contributes to improved equipment reliability.
Calculate MTBF for your use case:
Mean Time Between Failure (MTBF) Calculator
[Total Uptime (in hours) / # Number of breakdowns]
Our approach to managing work orders is radically different from other CMMS products in the market.
Learn more about the MTBF Calculator.
1.2 Mean Time to Repair (MTTR)
MTTR measures the average time it takes to restore a system or component to working condition after a failure. Fault tolerance strategies streamline the repair process by identifying faults quickly and providing redundancy options. As a result, MTTR is reduced, minimizing downtime and associated costs.
Calculate MTTR for your use case:
Mean Time To Repair (MTTR) Calculator
MTTR = (Total Downtime) / (Number of Repairs)
Happy with the result? If not, we could help.
Learn more about the MTTR Calculator.
2. Improved Performance
Beyond reliability metrics, fault tolerance also brings about improvements in overall system performance:
2.1 Consistent Output
Fault tolerance ensures that systems and equipment consistently deliver their intended output. In manufacturing, this means consistently producing high-quality products. For data centers, it means maintaining uninterrupted data services. This consistency enhances customer satisfaction and trust in your organization.
2.2 Scalability
Fault-tolerant systems are inherently scalable. Adding redundancy and error detection mechanisms to your infrastructure allows businesses to expand operations without compromising reliability. Whether scaling up your manufacturing capacity or accommodating a growing user base for digital services, fault tolerance provides a foundation for growth.
3. Cost Reduction
Fault tolerance isn't just an expense; it's an investment that yields cost-saving benefits:
3.1 Lower Maintenance Costs
Fault tolerance reduces the frequency and urgency of maintenance activities. By proactively addressing issues before they lead to catastrophic failures, organizations can schedule maintenance during planned downtime, reducing the need for costly emergency repairs.
3.2 Reduced Production Losses
In manufacturing and industrial settings, downtime can result in significant production losses. Fault tolerance minimizes unplanned downtime, ensuring that production lines keep running smoothly. This directly translates into reduced losses and increased revenue.
By improving reliability metrics, enhancing performance, and reducing costs, fault tolerance becomes a key driver of operational excellence and a competitive advantage.
Strategies for Implementing Fault Tolerance
Implementing fault tolerance is a critical endeavor involving strategies and technologies to ensure the continuous and reliable operation of systems and equipment. Below, we explore various strategies for implementing fault tolerance and how to leverage a CMMS to maximize their effectiveness.
1. Redundancy
Redundancy is a cornerstone of fault tolerance, involving the duplication or triplication of critical components to provide backups in case of failure. There are different types of redundancy, each suited to specific use cases:
- Active-active Redundancy: In an active-active setup, all redundant components are actively processing tasks simultaneously. This configuration ensures high availability and load balancing. For example, in a data center, multiple servers share the workload, distributing traffic evenly.
- Active-passive Redundancy: Active-passive redundancy involves one primary (active) component and one or more backup (passive) components that come into play if the active component fails. This setup is commonly used in critical systems where immediate failover is unnecessary, but reliability is essential. For instance, a backup generator can be passive until the primary generator fails.
Leveraging a CMMS:
A CMMS can help manage the maintenance and monitoring of redundant hardware components. By scheduling regular inspections and maintenance tasks through the CMMS, organizations ensure that redundant components remain in top condition. Additionally, CMMS software can provide real-time notifications of hardware failures, enabling swift action to activate redundant components.
2. Error Detection and Correction Mechanisms
Error detection and correction mechanisms are vital for maintaining data integrity and system stability:
- Error Codes and Checksums: Error detection techniques like error codes and checksums involve adding extra bits of data to transmitted information. This additional data allows the recipient to verify the integrity of the received data. If errors are detected, the recipient can request retransmission or apply correction algorithms.
Leveraging a CMMS:
CMMS systems can integrate with equipment and sensors that use error detection mechanisms. When errors are detected, the CMMS can initiate workflows for maintenance work orders and tasks to address the underlying issues promptly.
- Parity and RAID Systems: In data storage and computing, redundancy is achieved through Parity and RAID (Redundant Array of Independent Disks) systems. Parity involves the use of redundant bits to check and correct data errors. RAID arrays use multiple disks to store data redundantly, ensuring data availability even if one or more disks fail.
Leveraging a CMMS:
CMMS software can monitor the health of storage systems and generate alerts when disk failures or errors occur. Maintenance teams can use these alerts to replace faulty disks and ensure data reliability.
3. Failover and Load Balancing
Failover and load balancing are essential for ensuring continuous service availability:
- Automated Failover Processes: Failover is the process of automatically switching to backup components or systems when a primary component fails. Automated failover processes are essential for minimizing downtime and ensuring service continuity.
- Load Balancers in Data Centers: Load balancers distribute incoming network traffic across multiple servers to prevent overloading a single server and ensure optimal resource utilization. If a server fails, a load balancer can redirect traffic to healthy servers.
Leveraging a CMMS:
CMMS systems can be integrated with network monitoring tools to detect server failures and trigger automated failover processes. Maintenance teams can use CMMS software to schedule load balancer maintenance and ensure they function optimally.
By implementing these fault tolerance strategies and integrating them with a CMMS, organizations can improve equipment reliability, minimize downtime, and ensure the continuous operation of critical systems. CMMS software plays an important role in managing maintenance tasks, monitoring redundant components, and responding promptly to faults and failures, ultimately contributing to fault-tolerant operations.
Challenges and Considerations
While the benefits of implementing fault tolerance are substantial, organizations must navigate several challenges and considerations when planning and executing fault tolerance strategies. Here are key factors to keep in mind:
1. Cost vs. Benefit Analysis
Before investing in fault tolerance systems, organizations must conduct a thorough cost vs. benefit analysis. While fault tolerance can save money by reducing downtime and maintenance costs, it also involves expenses, such as redundant hardware, software licenses, and ongoing monitoring.
- Costs: These include purchasing redundant equipment, software licenses, training for personnel, and ongoing maintenance expenses. Organizations must evaluate whether the upfront and ongoing costs justify the potential benefits of reduced downtime and improved reliability.
- Benefits: Benefits include reduced downtime, improved reliability metrics, enhanced performance, and cost savings through lower maintenance expenses and production losses.
Organizations should carefully assess their specific needs and risk tolerance to determine the optimal level of investment in fault tolerance.
2. Complexity of Implementation
Implementing fault tolerance can be complex and require significant changes to existing systems and processes. The complexity can manifest in several ways:
- Technical Complexity: Integrating redundant components, error detection mechanisms, and failover processes can be technically challenging. Organizations must ensure that their IT and maintenance teams have the expertise to manage and maintain fault-tolerant systems.
- Operational Complexity: Managing redundant systems and monitoring for faults requires additional operational overhead. Organizations must allocate resources and establish procedures for ongoing maintenance and monitoring.
3. Maintenance and Monitoring
Fault-tolerant systems require vigilant maintenance and monitoring to ensure their effectiveness. Considerations in this area include:
- Regular Inspections: Maintenance professionals must regularly inspect redundant components to ensure they are in good working order. CMMS systems can help schedule and track these inspections.
- Real-time Monitoring: Organizations must implement real-time monitoring solutions to detect faults and trigger failover processes when necessary. CMMS software can integrate with monitoring tools to facilitate this.
- Training and Expertise: Maintenance teams must be trained to effectively manage and troubleshoot fault-tolerant systems. Continuous training and skill development are essential to maintaining the reliability of these systems.
4. Compatibility and Integration
Ensuring compatibility and seamless integration of fault tolerance mechanisms with existing systems and processes is important:
- Legacy Systems: Organizations with legacy systems may face compatibility challenges when implementing fault tolerance. Upgrading or replacing older systems may be necessary.
- Integration with CMMS: For maximum effectiveness, fault tolerance mechanisms should be integrated with a CMMS. This integration streamlines maintenance workflows, improves response times to faults, and enhances overall reliability.
- Vendor Compatibility: Organizations often use equipment and software from different vendors. Compatibility and interoperability between these components must be carefully assessed to avoid integration issues.
The Ongoing Importance of Fault Tolerance in Equipment Reliability
In the ever-evolving industrial landscape, fault tolerance remains a paramount element in ensuring the continued reliability of equipment. As machinery and systems become increasingly complex, fault tolerance serves as an indispensable safety net. It allows organizations to effectively manage the intricacies of modern technology by providing redundancy, error detection, and correction mechanisms.
In an era where data integrity is important for informed decision-making, fault tolerance safeguards against data corruption, supporting data-driven operations. Furthermore, amid ongoing digital transformations and the reliance on interconnected systems and IoT devices, fault tolerance has transitioned from a choice to a necessity. It’s a safeguard against disruptions, ensuring the uninterrupted operation of digital assets. In safety-critical sectors like healthcare, aerospace, and automotive, equipment reliability is not just a matter of efficiency but a life-or-death concern, making fault tolerance indispensable.
Across global operations, fault tolerance ensures consistent performance regardless of location, reinforcing organizations' competitive advantages by boosting customer satisfaction, reducing operational costs, and securing market positions.
TABLE OF CONTENTS
Keep Reading
The world of IoT is growing rapidly in almost every aspect of life across a variety of ...
29 Aug 2025
The adoption of Computerized Maintenance Management Systems (CMMS) presents a puzzling ...
28 Aug 2025
For the sake of repetition, a CMMS (Computerized Maintenance Management System) is the hub ...
26 Aug 2025
Too often, production and maintenance departments operate in silos, resulting in a lack of ...
22 Aug 2025
Many organizations struggle with scaling maintenance operations, mainly because some don’t ...
21 Aug 2025
Computerized Maintenance Management Systems (CMMS) have increasingly become the go-to tools ...
19 Aug 2025
It doesn’t seem to matter which energy provider you choose; the bottom line is that energy ...
15 Aug 2025
In FDA-regulated industries such as pharmaceuticals, medical devices, biotechnology, and food ...
14 Aug 2025
B2C businesses, such as retail, hospitality, and food service, operate in a highly ...
8 Aug 2025
What happens when your most experienced maintenance leader is planning on retiring, taking 20 ...
7 Aug 2025
Today’s maintenance operations have become more complex and sophisticated. Gone are the days ...
5 Aug 2025
Modern warehouses are instrumental to maintaining the smooth operations of supply chains, ...
1 Aug 2025
Computerized Maintenance Management Systems (CMMS) have proven to be essential tools for ...
31 Jul 2025
Sometimes it feels as if technology is expanding at the speed of light. This is an ...
29 Jul 2025
Data Center downtime can have a huge negative impact ranging from damage to the data center’s ...
25 Jul 2025
Whenever a company introduces a new process or technology, it’s followed by a period of ...
24 Jul 2025
Obsolescence often comes unexpectedly, mainly because little attention is given to the ...
22 Jul 2025
Imagine a world where critical assets run smoothly without unexpected downtime, maintenance ...
18 Jul 2025
Imagine you're going through a compliance audit, and the inspector asks for maintenance ...
10 Jul 2025
Maintenance managers understand that disasters are unpredictable and can have a massive ...
4 Jul 2025