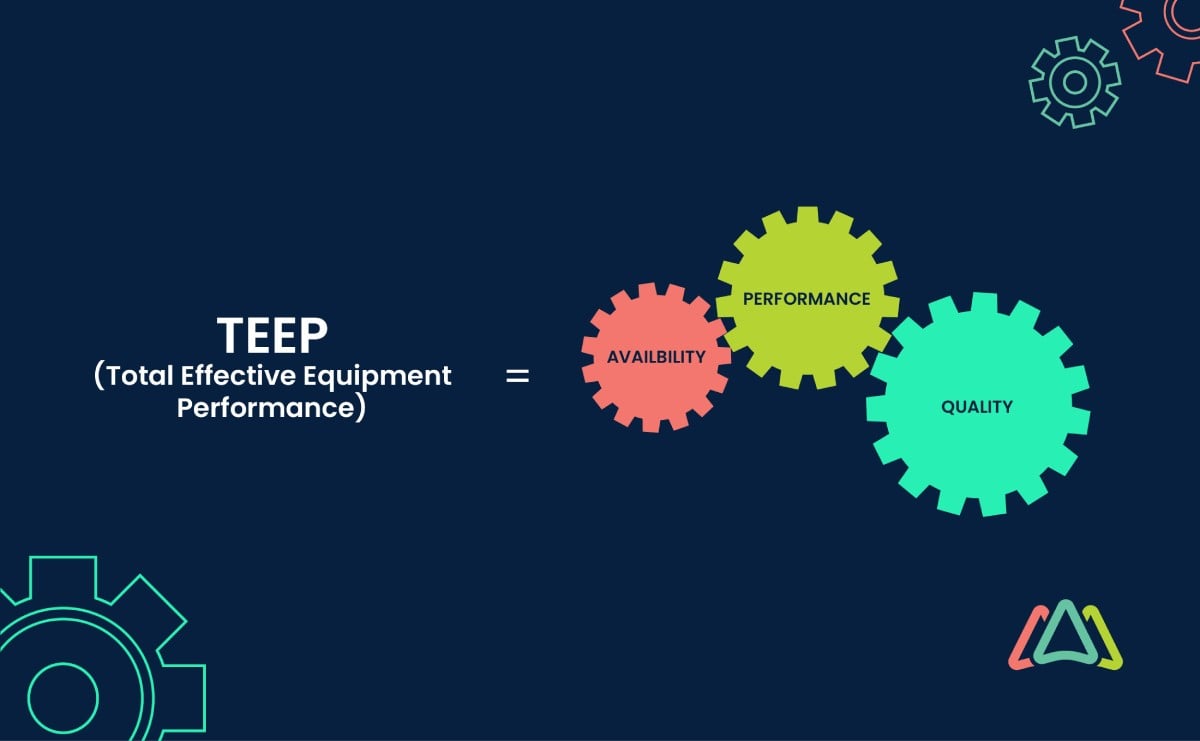
Understanding Total Effective Equipment Performance (TEEP) to Optimize Asset Performance
Total Effective Equipment Performance (TEEP) provides a holistic view of how well equipment performs in terms of availability, performance, and quality, enabling organizations to identify areas for improvement and maximize productivity. TEEP plays an important role in driving success in the manufacturing and production industries. By evaluating the overall equipment effectiveness, TEEP enables businesses to make informed decisions, enhance operational efficiency, and boost profitability. This article explains what TEEP is, how it relates to Overall Equipment Effectiveness (OEE), why it’s important, and best practices for implementing TEEP at manufacturing businesses.
What is Total Effective Equipment Performance (TEEP)?
Total Effective Equipment Performance (TEEP) is a metric used in manufacturing and production industries to assess the overall efficiency and effectiveness of equipment utilization. It provides insights into the performance of equipment in terms of availability, performance, and quality, allowing organizations to identify areas for improvement and optimize productivity.
TEEP takes into account the three key components:
- Availability: This measures the actual operating time of equipment compared to the planned production time. It considers both planned and unplanned downtime, including maintenance, changeovers, and other factors that may impact equipment availability.
- Performance: This component evaluates the actual production output of the equipment in relation to its maximum potential output. It takes into consideration factors such as speed, cycle time, and efficiency to determine how well the equipment performs in delivering its intended production rate.
- Quality: TEEP also considers the quality of the produced goods. It measures the ratio of good products to the total number of products produced, taking into account any defects, rework, or scrap that may occur during the production process.
Combined, these three components provide a comprehensive assessment of equipment performance, enabling organizations to understand the overall effectiveness of their equipment utilization. It helps identify areas of improvement, optimize processes, and make data-driven decisions to increase operational efficiency and lower costs. TEEP is also a valuable tool for monitoring and benchmarking equipment performance over time, enabling organizations to set performance goals, track progress, and implement continuous improvement initiatives.
By striving for higher TEEP levels, businesses can maximize production output, reduce downtime, improve product quality, and ultimately achieve operational excellence in their manufacturing and production processes.
Understanding TEEP in Relation to OEE
TEEP and OEE, (Overall Equipment Effectiveness), are two related metrics used to evaluate and measure equipment performance in manufacturing and production processes.
OEE measures the effectiveness of equipment in relation to planned production. It focuses on three key factors: availability, performance, and quality. OEE is a subset of TEEP and provides a narrower perspective on equipment performance.
Similarities between TEEP and OEE
- Focus on performance evaluation: Both TEEP and OEE are used to assess the performance of equipment in manufacturing and production processes. They provide valuable insights into how effectively equipment is being utilized and where improvements can be made.
- Calculation based on three factors: Both TEEP and OEE take into account the three key components; availability, performance, and quality. These factors provide a comprehensive understanding of equipment performance and identify areas that can be optimized.
- Utilize similar performance indicators: TEEP and OEE both utilize performance indicators to measure and quantify the various components. These indicators include metrics such as planned production time, actual operating time, production output, and product quality.
Differences between TEEP and OEE
While TEEP and OEE are similar, there are notable differences between the two metrics:
- Consideration of losses: TEEP considers all types of losses that can affect equipment performance, including availability, performance, and quality losses. It provides a more comprehensive view of equipment effectiveness by encompassing all aspects of losses.
In contrast, OEE focuses specifically on availability, performance, and quality losses. It excludes certain losses due to planned downtime, such as scheduled maintenance or changeovers, and focuses primarily on unplanned downtime as a measure of availability loss.
- Inclusion of planned downtime: TEEP includes both planned and unplanned downtime in its calculations. This means that scheduled maintenance, setup time, changeovers, and other planned events that impact equipment availability are considered in the TEEP measurement.
OEE, on the other hand, only includes unplanned downtime as a measure of availability loss. It does not factor in planned downtime, as it focuses on the equipment's ability to meet the planned production schedule.
- Scope of measurement: TEEP is a measure of overall equipment effectiveness, providing a comprehensive evaluation of equipment performance that encompasses all losses and factors affecting efficiency.
In contrast, OEE specifically measures equipment effectiveness in relation to planned production. It focuses on how well equipment performs against the planned production rate and doesn’t provide a broader assessment of overall equipment performance.
While TEEP provides a more comprehensive view, OEE offers a narrower focus on equipment effectiveness in relation to planned production schedules.
How to Calculate TEEP?
The calculation of Total Effective Equipment Performance (TEEP) involves multiplying the three components: availability, performance, and quality.
Formula
The formula for TEEP is as follows:
TEEP
= Availability × Performance × Quality
Each component represents a specific aspect of equipment performance, and when combined, they provide a comprehensive measure of TEEP.
Steps to Calculate TEEP
To calculate TEEP, follow these steps:
1. Calculate Availability
Availability is the ratio of the actual operating time of the equipment to the planned production time. It takes into account both planned and unplanned downtime. To calculate availability, use the following formula:
Availability
= (Actual Operating Time / Planned Production Time) × 100
2. Calculate Performance
Performance measures the actual production output of the equipment compared to its maximum potential output. It considers factors such as speed, cycle time, and efficiency. To calculate performance, use the following formula:
Performance
= (Actual Production Output / Maximum Potential Output) × 100
3. Calculate Quality
Quality evaluates the ratio of good products produced by the equipment to the total number of products produced. It takes into account any defects, rework, or scrap that may occur during the production process. To calculate quality, use the following formula:
Quality
= (Number of Good Products / Total Number of Products) × 100
4. Multiply the three components to get the TEEP percentage
Once you have calculated the availability, performance, and quality percentages, multiply them together to obtain the TEEP percentage. Use the following formula:
TEEP
= Availability × Performance × Quality
Calculation Example
Let's consider a manufacturing company in the automotive industry that produces car components.
The company operates 24 hours a day, 7 days a week.
The planned production time for a week is 168 hours.
The maximum potential output of the equipment is 1,000 components per hour.
Over the course of a week, the company produces a total of 150,000 components.
Out of these, 145,000 are good components, and the remaining 5,000 components are defective or require rework.
1. Calculate Availability
In this scenario, the equipment experienced 10 hours of planned downtime for maintenance purposes during the week.
Therefore, the actual operating time is 168 hours - 10 hours = 158 hours.
Availability
= (158 hours / 168 hours) × 100 = 94.05%
2. Calculate Performance
The actual production output of the equipment for the week is 150,000 components.
The maximum potential output per hour is 1,000 components, so the expected production output for the week would be 1,000 components / hour × 168 hours
= 168,000 components.
Performance = (150,000 components / 168,000 components) × 100 = 89.29%
3. Calculate Quality
Out of the 150,000 components produced, 145,000 are good components.
Quality
= (145,000 good components / 150,000 total components) × 100
= 96.67%
4. Multiply the three components to determine the TEEP percentage
TEEP
= Availability × Performance × Quality
= (94.05% × 89.29% × 96.67%)
≈ 80.43%
Benefits of Calculating TEEP
TEEP empowers organizations to make data-driven decisions, optimize equipment performance, and stay competitive in today's fast-paced manufacturing and production landscape. By striving for higher TEEP scores, businesses can move toward their full operational potential.
Here are some reasons why TEEP is important:
1. Optimal Equipment Utilization
TEEP helps organizations identify bottlenecks, inefficiencies, and areas of improvement in equipment performance. By maximizing equipment availability, performance, and quality, companies can achieve higher production output and better meet customer demands.
2. Cost Reduction
TEEP provides insights into potential areas of waste and losses, allowing organizations to minimize downtime, reduce maintenance costs, and optimize resource allocation. By streamlining equipment utilization, businesses can achieve significant cost savings and improve their bottom line.
3. Quality Improvement
TEEP not only considers the availability and performance of equipment, but also evaluates the quality of the produced goods. By focusing on quality metrics, businesses can enhance product consistency, reduce defects, and improve customer satisfaction.
4. Continuous Improvement
TEEP serves as a benchmark for measuring equipment performance and acts as a catalyst for continuous improvement efforts. By monitoring TEEP over time, organizations can implement corrective actions, optimize processes, and promote a culture of continuous improvement.
Improving TEEP through Loss Identification and Mitigation
In manufacturing processes, losses refer to any events that result in reduced productivity, efficiency, or quality of output. These losses can hinder equipment performance and impact overall production effectiveness. It is essential to identify and minimize losses to optimize Total Effective Equipment Performance (TEEP).
Types of Losses to Consider in TEEP Calculations
To accurately calculate TEEP, it’s important to consider the various types of losses that can occur in manufacturing processes:
- Planned downtime losses: Planned downtime includes scheduled maintenance, equipment setup, changeovers, and other planned events that require equipment to be offline temporarily. Although these events are necessary, they still result in reduced availability and affect TEEP.
- Unplanned downtime losses: Unplanned downtime refers to unexpected events such as equipment breakdowns, power outages, or material shortages. These incidents lead to idle time and can significantly impact availability and TEEP.
- Performance losses: Performance losses occur when equipment operates below its maximum potential, leading to reduced productivity. Factors contributing to performance losses include sub-optimal speed, inefficient equipment setup, minor stoppages, or slowdowns in the production process.
- Quality losses: Quality losses involve producing defective or non-compliant products that do not meet the required standards. These losses include rework, scrap, rejects, or any additional work required to bring products up to the desired quality level.
Importance of Identifying and Addressing Losses to Improve TEEP
Identifying and addressing losses is important for improving TEEP and equipment performance. Here's why it's important:
- Optimizing equipment availability: By identifying and reducing planned and unplanned downtime losses, organizations can increase equipment availability. This means more operating time, fewer interruptions, and improved TEEP.
- Minimizing performance losses: Addressing performance losses helps optimize equipment performance. By identifying and resolving issues such as inefficient setup, minor stoppages, or slowdowns, organizations can increase the equipment's productivity and improve TEEP.
- Improving product quality: Quality losses negatively impact TEEP by decreasing the ratio of good products to the total produced. By focusing on reducing defects, rework, scrap, and rejects, organizations can improve product quality, increase customer satisfaction, and positively influence TEEP.
- Continuous improvement and efficiency gains: By regularly monitoring and addressing losses, organizations can implement targeted improvements. By leveraging data and insights, they can identify recurring issues, develop preventive measures, and drive continuous improvement efforts. This leads to long-term efficiency gains and improved TEEP.
TEEP Implementation Strategies
1. Establish a Baseline for Measurement
To effectively implement Total Effective Equipment Performance (TEEP), it is important to establish a baseline for measurement. This involves the following steps:
1.1 Identify key performance indicators (KPIs)
Determine the specific KPIs that align with TEEP. These indicators may include availability, performance, quality, planned and unplanned downtime, maintenance costs, and other relevant metrics. Identify the right KPIs to ensure that the TEEP measurement captures all the essential aspects of equipment performance.
1.2 Collect historical data on equipment performance
Gather historical data on equipment performance, including production output, downtime events, maintenance records, and quality measurements. This data provides the foundation for comparison and helps establish a benchmark for future TEEP measurements.
2. Set Realistic Performance Goals
To drive continuous improvement and optimize TEEP, it’s important to set realistic performance goals. Follow these steps:
2.1 Define desired levels of availability, performance, and quality
Determine the desired targets for each TEEP component - availability, performance, and quality. These targets should be specific, measurable, achievable, relevant, and time-bound (SMART). For example, organizations can aim for a 95% availability rate, 90% performance rate, and 98% quality rate. Make sure targets are realistic and achievable based on past numbers and available resources.
2.2 Align goals with overall business objectives
Ensure that the performance goals are aligned with the overall objectives of the organization. The TEEP goals should support the company's strategic direction, customer requirements, and operational priorities. This alignment ensures that TEEP improvements contribute to the overall success of the business.
3. Track and Monitor TEEP Metrics
Tracking and monitoring TEEP metrics is essential to gauge progress and identify areas for improvement. Consider the following actions:
3.1 Implement a data collection system
Set up a system to collect relevant data on availability, performance, quality, and other associated metrics. This may involve using sensors or manual methods. Ensure that the data collection system captures accurate and real-time information for effective TEEP analysis within a CMMS software.
3.2 Regularly analyze and report TEEP results
Analyze the data to calculate TEEP and review the results on a regular basis. Create reports or visual dashboards to communicate TEEP metrics to key stakeholders. Regularly share TEEP insights with relevant teams to drive awareness and encourage collaboration for improvement initiatives.
4. Identify and Address Performance Gaps
To improve TEEP, it’s important to identify and address performance gaps. Consider the following steps:
4.1 Identify root causes of low TEEP
Analyze the TEEP data and performance metrics to identify the root causes for low TEEP values. Look for patterns, recurring issues, or specific factors that contribute to low performance. This analysis may involve assessing maintenance practices, process inefficiencies, operator training, or other factors.
4.2 Implement corrective actions and continuous improvement strategies
Develop and implement corrective actions based on the identified root causes. This may involve optimizing maintenance practices, streamlining processes, providing additional training to operators, or adopting new technologies. Implement continuous improvement strategies to address performance gaps and drive TEEP enhancements over time.
Improving Equipment Effectiveness through Continuous Monitoring and Improvement
TEEP is not a one-time measurement but an ongoing process. Continuous monitoring of TEEP metrics is crucial to identify performance gaps, track progress, and drive continuous improvement. Regularly analyzing TEEP data and taking proactive measures to address inefficiencies and losses contribute to sustainable growth and operational excellence.
By implementing TEEP, monitoring performance, and addressing losses, businesses in manufacturing can enhance operational efficiency, reduce costs, and stay competitive in today's challenging business environment. Embrace TEEP as a strategic tool and unlock the full potential of your equipment and processes.
TABLE OF CONTENTS
Keep Reading
For the sake of repetition, a CMMS (Computerized Maintenance Management System) is the hub ...
26 Aug 2025
Too often, production and maintenance departments operate in silos, resulting in a lack of ...
22 Aug 2025
Many organizations struggle with scaling maintenance operations, mainly because some don’t ...
21 Aug 2025
Computerized Maintenance Management Systems (CMMS) have increasingly become the go-to tools ...
19 Aug 2025
It doesn’t seem to matter which energy provider you choose; the bottom line is that energy ...
15 Aug 2025
In FDA-regulated industries such as pharmaceuticals, medical devices, biotechnology, and food ...
14 Aug 2025
B2C businesses, such as retail, hospitality, and food service, operate in a highly ...
8 Aug 2025
What happens when your most experienced maintenance leader is planning on retiring, taking 20 ...
7 Aug 2025
Today’s maintenance operations have become more complex and sophisticated. Gone are the days ...
5 Aug 2025
Modern warehouses are instrumental to maintaining the smooth operations of supply chains, ...
1 Aug 2025
Computerized Maintenance Management Systems (CMMS) have proven to be essential tools for ...
31 Jul 2025
Sometimes it feels as if technology is expanding at the speed of light. This is an ...
29 Jul 2025
Data Center downtime can have a huge negative impact ranging from damage to the data center’s ...
25 Jul 2025
Whenever a company introduces a new process or technology, it’s followed by a period of ...
24 Jul 2025
Obsolescence often comes unexpectedly, mainly because little attention is given to the ...
22 Jul 2025
Imagine a world where critical assets run smoothly without unexpected downtime, maintenance ...
18 Jul 2025
Imagine you're going through a compliance audit, and the inspector asks for maintenance ...
10 Jul 2025
Maintenance managers understand that disasters are unpredictable and can have a massive ...
4 Jul 2025
Asset lifespan is a key concern for executives and maintenance and facility management teams. ...
3 Jul 2025
Your company recently invested funds and time for new CMMS software, and six months later, it ...
1 Jul 2025