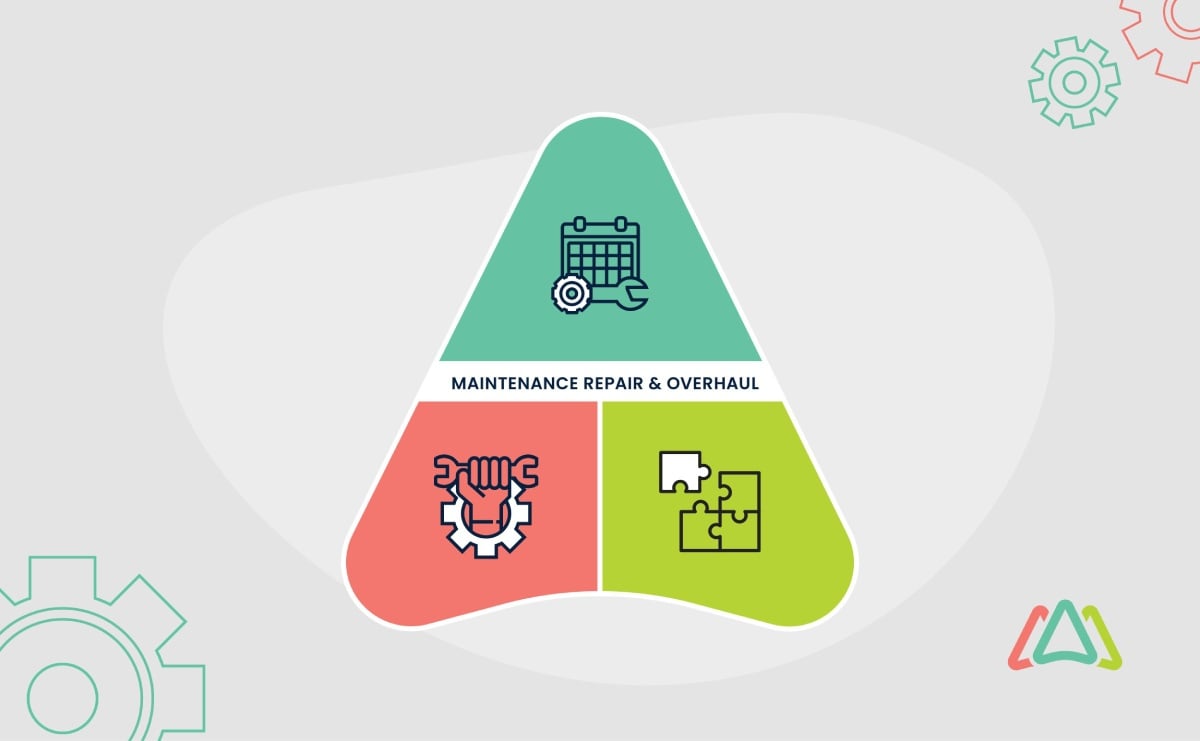
Maintenance, Repair, and Overhaul (MRO) for Sustainable Industrial Operations
Maintenance, Repair, and Overhaul (MRO) ensures the optimal functioning and longevity of machinery, equipment, and infrastructure across various industries. For maintenance professionals, MRO represents a critical framework encompassing the meticulous tasks of maintaining, repairing, and overhauling assets to keep them in their best working condition.
MRO's roots can be traced back to the earliest human innovations. As humans progressed from simple tools to complex machinery, the need for maintaining and repairing these tools became evident. In ancient times, blacksmiths, for example, were akin to early maintenance professionals, ensuring that tools and weapons were in good condition. Over time, as industries advanced and mechanization became widespread, the concept of MRO evolved.
The demands of an increasingly complex and automated world during the Industrial Revolution led to more formalized MRO processes. With the advent of manufacturing and mass production, the need for maintaining machines and equipment at scale became apparent. This historical evolution has led to the development of modern maintenance practices, making MRO a fundamental part across industries today.
What is Maintenance Repair and Overhaul (MRO)?
Maintenance, Repair, and Overhaul (MRO) is a multifaceted set of activities integral to maintaining and optimizing the performance of machinery, equipment, infrastructure, and assets across various industries. MRO encompasses many tasks, from routine inspections and preventive maintenance to more complex repairs and comprehensive overhauls. These activities are meticulously planned, executed, and documented to ensure that assets operate at their peak efficiency, minimize downtime, and extend their operational lifespan.
The scope of MRO goes beyond mere maintenance; it encompasses the entire asset lifecycle management. This includes:
- Maintenance: Routine and preventive actions that aim to keep equipment in good working condition, thus minimizing unexpected breakdowns and disruptions.
- Repair: Corrective measures taken in response to equipment failures or damage. Repairs aim to restore equipment to its operational state efficiently.
- Overhaul: Comprehensive, often periodic, maintenance activities that involve disassembling and refurbishing equipment to extend its useful life.
Key Components of MRO
MRO consists of three primary components, each playing a unique role in ensuring the smooth operation of equipment and assets across industries.
Component 1: Maintenance
- Preventive Maintenance: Preventive maintenance is the foundation of MRO. It involves a systematic and scheduled approach to keep equipment and machinery in optimal working condition. Maintenance professionals perform routine inspections, lubrication, cleaning, and adjustments as prescribed by manufacturers and industry standards. The primary goal of preventive maintenance is to prevent potential issues before they occur, thus minimizing unexpected downtime and costly repairs.
- Predictive Maintenance: Predictive maintenance takes a more data-driven approach. It utilizes advanced technologies, such as sensors and data analytics, to monitor the condition of equipment in real time. By analyzing data patterns, maintenance professionals can predict when equipment will likely fail and schedule maintenance precisely when needed. This approach is highly cost-effective, reducing unnecessary maintenance while ensuring equipment reliability.
- Corrective Maintenance: Corrective maintenance is reactive in nature and comes into play when equipment malfunctions or fails unexpectedly. It involves repairing or replacing faulty components to restore the equipment to operational status. While this maintenance is essential, it is generally less cost-effective than preventive or predictive maintenance due to the unexpected downtime and potential for costly repairs.
Discover the Pros and Cons of Different Maintenance Strategies
Component 2: Repair
Types of Repair Activities
Repairs encompass various activities that address issues affecting the functionality of equipment. Some common types of repair activities include:
- Routine Repairs: Address minor, routine issues to maintain equipment functionality.
- Emergency Repairs: Address critical malfunctions and are performed urgently to minimize downtime.
- Capital Repairs: Involve significant investments to extend the life or improve the performance of equipment.
Importance of Timely Repairs
- Minimizing Downtime: Swift repairs help reduce the duration of downtime, keeping operations running smoothly.
- Preventing Escalation: Neglected minor issues can escalate into major problems, potentially leading to expensive repairs or replacements.
- Safety: In industries like healthcare and aviation, timely repairs are essential to ensure the safety of users and passengers.
Component 3: Overhaul
Overhaul is an extensive maintenance process involving equipment or machinery disassembly, inspection, repair, and reassembly. It is typically performed at predetermined intervals to extend the asset's lifespan, maintain reliability, and improve performance. Overhaul aims to bring the equipment back to "like-new" condition and often involves refurbishing or replacing worn-out components.
Common Overhaul Processes
- Disassembly: The equipment is dismantled to its core components for a thorough examination.
- Inspection: Each component is closely inspected for wear, damage, and defects.
- Repair/Replacement: Worn or damaged parts are either repaired or replaced with new components.
- Reassembly: The equipment is reassembled and tested to ensure it functions correctly.
- Performance Testing: Rigorous testing ensures the overhauled equipment meets specified performance standards.
Overhaul is fundamental in industries where equipment must meet stringent performance and safety standards, such as aviation, where aircraft undergo regular overhauls to ensure safe and reliable operations.
Industries Utilizing MRO
Maintenance, Repair, and Overhaul (MRO) are universal concepts applied across various industries. Here, we explore how multiple sectors rely on MRO to ensure the reliability and longevity of their equipment and infrastructure.
Industry |
Role of MRO |
Key Challenges and Peculiarities |
---|---|---|
Manufacturing |
Maintaining production machinery and equipment for consistent output. |
Diverse machinery, varying production scales, and integration of new technology can complicate MRO. |
Automotive |
Preserving the safety and reliability of vehicles and production equipment. |
Rapid advancements in automotive technology require adaptability in MRO practices. |
Energy & Utilities |
Ensuring the reliability and safety of equipment used in power generation and fuel production. |
High-risk environments, strict environmental regulations, and a focus on energy efficiency set this sector apart. |
Healthcare |
Sustaining the continuous operation of critical medical equipment for patient care. |
Patient safety is paramount, demanding precision and speed in MRO activities. |
Aviation & Aerospace |
Ensuring safety, reliability, and compliance of aircraft and avionics systems. |
Stringent safety regulations, complex avionics, and aging fleets pose unique challenges. |
Maritime |
Maintaining and repairing ships, engines, navigation systems, and offshore platforms. |
Specific concerns include harsh marine environments, corrosion, and safety in remote locations. |
Defense |
Supporting national security by maintaining military vehicles, aircraft, and communication systems. |
National security and strict military specifications drive specialized MRO practices. |
Importance of Effective MRO
The effective implementation of MRO practices offers several advantages, making it an integral part of modern industrial operations.
Enhancing Equipment Reliability
- Sustaining Peak Performance: Effective MRO activities ensure that equipment operates optimally. Routine inspections and preventive maintenance measures identify and address potential issues before they escalate, thus enhancing reliability.
- Extending Equipment Lifespan: Regular maintenance and timely repairs significantly extend the operational life of equipment, reducing the need for premature replacements and preserving capital investments.
Reducing Downtime and Associated Costs
- Minimizing Unplanned Downtime: Unplanned downtime can be costly and disruptive. Well-executed MRO practices reduce the risk of unexpected equipment failures, ensuring operations run smoothly.
- Optimizing Production Schedules: In manufacturing, reducing downtime leads to improved production output, meeting deadlines, and reducing costs.
Ensuring Safety and Compliance
- Meeting Safety Standards: Industries like aviation, healthcare, and energy have stringent safety standards. Effective MRO practices ensure that equipment meets or exceeds these standards, guaranteeing the safety of personnel and the public.
- Regulatory Compliance: MRO practices often require adhering to industry-specific regulations and environmental standards. Compliance not only avoids legal complications but also upholds ethical responsibilities.
Cost Savings and Profitability
- Reducing Maintenance Costs: Effective MRO practices lead to more efficient use of resources. Identifying issues early and performing necessary maintenance reduces costs associated with emergency repairs and replacements.
- Improving Profitability: By improving equipment reliability, reducing downtime, and managing maintenance costs, businesses can operate more profitably. Savings from MRO can be reinvested in growth initiatives.
Best Practices of Maintenance, Repair, and Overhaul (MRO)
Inventory Management
- Just-in-Time (JIT) Inventory: Just-in-time inventory management is a lean practice aimed at reducing inventory costs and minimizing waste. Rather than stockpiling excess spare parts, it involves procuring them as needed, ensuring they arrive just in time for scheduled maintenance or repairs. JIT inventory minimizes carrying costs and storage space while maintaining the availability of essential parts.
- Spare Parts Optimization: Properly optimizing spare parts inventory involves identifying critical components, their consumption rates, and the lead time for replacements. This data-driven approach ensures that the right parts are available when needed, preventing costly delays in maintenance and unnecessary inventory costs.
Technology Adoption
- IoT and Predictive Maintenance: The Internet of Things (IoT) is revolutionizing MRO by providing real-time data from sensors embedded in equipment. Predictive maintenance leverages this data to monitor equipment condition and performance continuously. By identifying trends and anomalies, maintenance can be scheduled proactively, reducing downtime and minimizing maintenance costs.
- CMMS (Computerized Maintenance Management Systems): CMMS software is an invaluable tool for managing maintenance operations. It streamlines work order management, tracks asset histories, and schedules preventive maintenance tasks. CMMS helps organizations optimize their maintenance processes, improve resource allocation, and maintain compliance with regulatory standards.
Streamline Maintenance & Maximize Productivity with Click Maint CMMS
Workforce Skills and Training
- Importance of Skilled Technicians: Skilled technicians are the backbone of effective MRO. They should possess a deep understanding of the equipment they work with and proficiency in the latest maintenance techniques and technologies. Skilled technicians can quickly diagnose and resolve issues, reducing downtime and costs.
- Continuous Learning and Development: Maintenance professionals should engage in ongoing training and development programs to stay current with industry trends and emerging technologies. These programs enhance skills, promote best practices, and ensure technicians are prepared to tackle new challenges in MRO.
Regulatory Compliance
- Industry-Specific Regulations: Different industries have specific regulations and standards that must be adhered to. Understanding and staying compliant with these regulations is essential for safety, quality, and legal purposes. Non-compliance can result in fines, lawsuits, and damage to an organization's reputation.
- Environmental and Safety Standards: Organizations should maintain a commitment to environmental sustainability and safety. Adhering to environmental standards safeguards the environment and ensures compliance with laws and regulations. Safety standards are paramount in industries like aviation and healthcare, where lives depend on equipment reliability and performance.
Incorporating these best practices into MRO operations enables organizations to optimize equipment performance, minimize downtime, and achieve long-term cost savings. Moreover, staying compliant with industry-specific regulations and fostering a skilled workforce ensures that MRO remains efficient, reliable, and future-proof.
Common Challenges in MRO
Budget Constraints
Budget constraints pose a significant challenge to MRO efforts. Organizations often face the dilemma of allocating limited financial resources among competing maintenance priorities. Striking a balance between cost-effectiveness and maintaining high-quality MRO practices can be a complex task. Budget constraints may lead to deferred maintenance, causing issues to escalate and increasing the likelihood of costly breakdowns.
Data Management and Analysis
The digital transformation has brought an influx of data from sensors and IoT devices, providing valuable insights into equipment health. However, managing and effectively analyzing this data can be overwhelming. Without a robust data management and analysis strategy, organizations may struggle to derive actionable insights, potentially missing out on predictive maintenance opportunities.
Availability of Skilled Labor
Skilled technicians and maintenance professionals are essential for effective MRO. However, the availability of skilled labor can be a significant challenge. The workforce shortage in many industries, coupled with the aging workforce, creates a competitive environment for recruiting and retaining qualified MRO personnel.
Challenges within skilled labor availability include:
- attracting new talent to the MRO field,
- addressing the knowledge gap created by retiring experienced technicians,
- and providing continuous training and development opportunities for the existing workforce.
Balancing Short-Term vs. Long-Term Goals
MRO decisions often involve the challenge of balancing short-term priorities with long-term objectives. In some cases, organizations may prioritize cost reduction in the short term, potentially neglecting essential preventive and predictive maintenance. This short-sighted approach can increase long-term costs due to equipment failure and downtime. Conversely, overinvesting in long-term preventive maintenance may strain budgets in the short term without immediate apparent benefits, leading to internal resistance.
Addressing these Challenges:
- Prioritize Preventive Maintenance: Allocating resources to preventive maintenance can help mitigate budget constraints by reducing the likelihood of costly emergency repairs and replacements.
- Implement Robust Data Analysis: Leverage data management systems and predictive analytics tools to derive actionable insights from the data generated by equipment sensors. This data-driven approach enhances decision-making and resource allocation.
- Invest in Workforce Development: Establish training programs and partnerships with educational institutions to attract and develop skilled labor. Encourage a culture of continuous learning and provide advancement opportunities for existing staff.
- Develop a Balanced Approach: Consider the long-term implications of MRO decisions while addressing immediate needs. Striking a balance between short-term cost-saving measures and long-term equipment reliability is essential for sustainable MRO practices.
Future Trends in MRO
Maintenance, Repair, and Overhaul (MRO) is evolving rapidly, driven by technological advancements, changing industry needs, and a growing focus on sustainability. To remain competitive and meet the demands of the future, organizations must embrace these emerging trends in MRO:
Automation and Robotics
Automation and robotics are reshaping the MRO landscape. Drones, autonomous vehicles, and robotic systems are increasingly used for inspections, maintenance, and repairs. These technologies offer several advantages:
- Efficiency: Automation allows faster and more precise inspections and maintenance, reducing downtime.
- Safety: Robots can access hazardous or hard-to-reach areas, improving the safety of maintenance professionals.
- Data Collection: Automated systems can collect vast amounts of data during inspections, enabling better predictive maintenance.
Predictive Analytics and AI
Predictive analytics and Artificial Intelligence (AI) are transforming MRO from a reactive to a proactive discipline. AI systems can analyze large datasets to predict when equipment will likely fail, allowing maintenance to be scheduled precisely when needed. Benefits include:
- Cost Savings: Predictive maintenance reduces unnecessary, costly preventive maintenance and minimizes downtime.
- Increased Reliability: By addressing issues before they become critical, AI-driven MRO improves the overall reliability of assets.
- Data-Driven Decision-Making: AI assists in better decision-making by providing insights into equipment health and performance trends.
3D Printing and Additive Manufacturing
3D printing and additive manufacturing have gained traction in MRO for producing spare parts on demand. This technology offers several advantages:
- Reduced Lead Times: Printing spare parts on-site significantly reduces lead times, minimizing equipment downtime.
- Cost Savings: Traditional manufacturing can be costly for low-volume or obsolete parts; 3D printing offers a cost-effective alternative.
- Customization: 3D printing allows for the creation of customized parts to suit specific MRO needs.
Sustainability and Environmental Concerns
The MRO industry is increasingly adopting sustainable practices to address environmental concerns. This includes reducing energy consumption, minimizing waste, and adhering to strict environmental regulations. Benefits include:
- Reduced Environmental Impact: Sustainable MRO practices contribute to a reduction in an organization's environmental footprint.
- Compliance: Compliance with environmental regulations is ethical and essential to avoid legal issues and reputational damage.
- Cost Efficiency: Sustainable practices often lead to more efficient resource use, ultimately reducing costs.
The Role of Digital Twins in MRO
Digital twins, or virtual replicas of physical assets, are becoming indispensable in MRO. They provide a real-time, digital representation of equipment, enabling:
- Proactive Maintenance: Digital twins allow continuous monitoring and simulation, predicting when maintenance is needed and optimizing performance.
- Reduced Downtime: By identifying issues before they result in equipment failure, digital twins reduce unplanned downtime.
- Streamlined Operations: Data from digital twins aids in making informed decisions about maintenance, improving overall operational efficiency.
These future trends in MRO are reshaping how organizations manage their equipment and assets. By embracing these technological and environmental shifts, companies can enhance efficiency, reduce costs, and remain competitive in an ever-evolving industry.
TABLE OF CONTENTS
Keep Reading
What happens when your most experienced maintenance leader is planning on retiring, taking 20 ...
7 Aug 2025
Today’s maintenance operations have become more complex and sophisticated. Gone are the days ...
5 Aug 2025
Modern warehouses are instrumental to maintaining the smooth operations of supply chains, ...
1 Aug 2025
Computerized Maintenance Management Systems (CMMS) have proven to be essential tools for ...
31 Jul 2025
Sometimes it feels as if technology is expanding at the speed of light. This is an ...
29 Jul 2025
Data Center downtime can have a huge negative impact ranging from damage to the data center’s ...
25 Jul 2025
Whenever a company introduces a new process or technology, it’s followed by a period of ...
24 Jul 2025
Obsolescence often comes unexpectedly, mainly because little attention is given to the ...
22 Jul 2025
Imagine a world where critical assets run smoothly without unexpected downtime, maintenance ...
18 Jul 2025
Imagine you're going through a compliance audit, and the inspector asks for maintenance ...
10 Jul 2025
Maintenance managers understand that disasters are unpredictable and can have a massive ...
4 Jul 2025
Asset lifespan is a key concern for executives and maintenance and facility management teams. ...
3 Jul 2025
Your company recently invested funds and time for new CMMS software, and six months later, it ...
1 Jul 2025
As Computerized Maintenance Management Systems (CMMS) become more connected and cloud-based, ...
1 Jul 2025
Edge computing is an innovative technology that enables data to be processed at the source, ...
24 Jun 2025
Facility management has undergone a significant transformation in recent times. Take, for ...
20 Jun 2025
A facility maintenance plan is at the core of a facility’s operations. This organized ...
19 Jun 2025
In the early days, preventive maintenance could be done effectively with a trained eye and a ...
17 Jun 2025
Sticky notes fall off, whiteboard grids get wiped, and spreadsheets never beep when a ...
13 Jun 2025
Handing a slice of your maintenance workload to a contractor is less about “giving up ...
12 Jun 2025