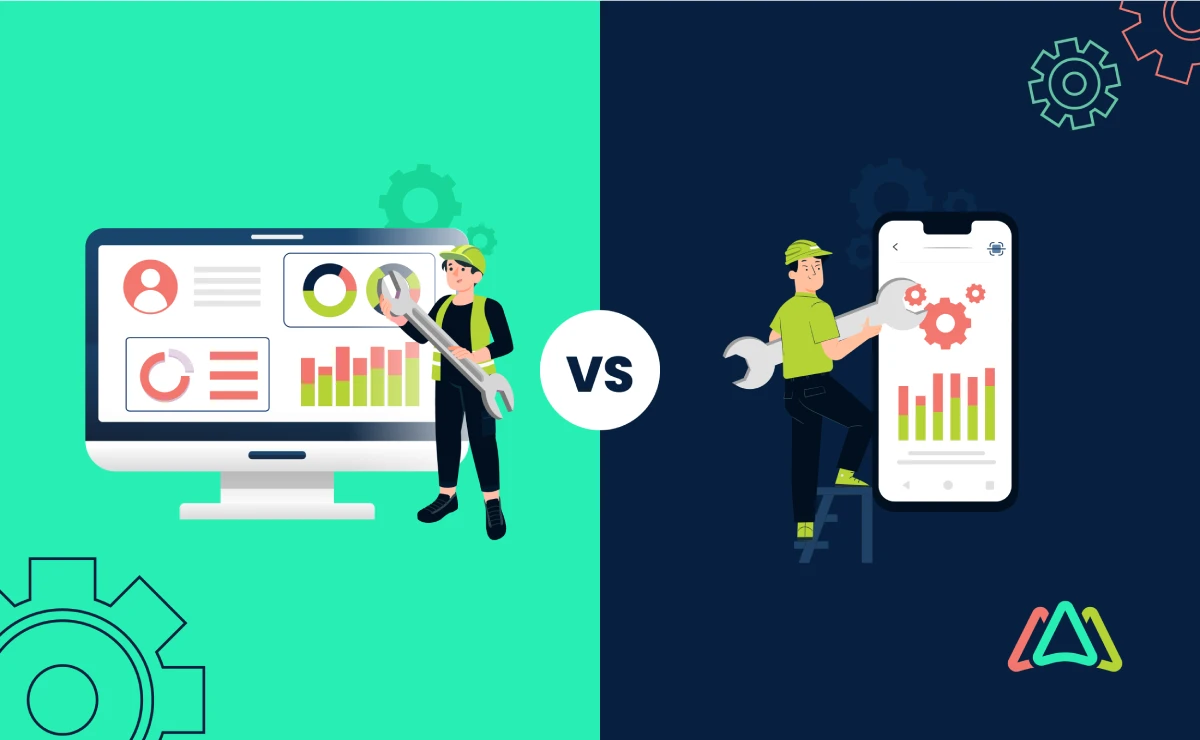
CMMS Feature Differences Between Desktop and Mobile Versions
Computerized Maintenance Management Systems (CMMS) have emerged as indispensable tools for maintenance teams to streamline workflows, optimize asset performance, and minimize downtime. For these reasons, companies worldwide and across industry sectors are adopting CMMS to enhance their operations and increase their bottom line.
For those unfamiliar with CMMS, understanding the breadth of its features and functionality can take time and effort. Let’s begin by saying CMMS encompasses a comprehensive suite of features and modules that streamline maintenance management processes, optimize asset performance, and minimize downtime for organizations across various industries. From managing work orders, scheduling preventive maintenance, and tracking inventory to generating insightful reports and analyzing maintenance data, CMMS is a centralized platform for efficiently guiding maintenance activities.
Those new to CMMS must know that the CMMS software is available in desktop and mobile versions, catering to maintenance teams' diverse needs and preferences. While desktop CMMS offers robust reporting capabilities and extensive configuration options, mobile CMMS enhances on-the-go maintenance efficiency and communication, empowering technicians to perform tasks seamlessly from remote locations. Understanding the distinction between these options is essential for using CMMS software and benefiting from its full potential.
This article focuses on distinguishing between desktop and mobile CMMS by highlighting their unique capabilities and outlining when it's best to utilize each. We’ll also explore some common reservations that maintenance teams may have regarding mobile CMMS adoption and end by making a compelling case for embracing mobile technology in maintenance management.
Mobile CMMS: Enhancing On-the-Go Maintenance Efficiency
Mobile CMMS empowers maintenance technicians and managers to stay connected and productive while offsite. The mobile CMMS is accessible on an app on mobile phones or tablets. The apps are also available in both Android and IOS operating systems. The key features of a Mobile CMMS include
Real-time Communication
One of the primary advantages of mobile CMMS is its ability to facilitate real-time communication between field technicians and the central maintenance team. Whether submitting work orders, updating task statuses, or requesting support, mobile CMMS enables seamless communication, reducing response times and enhancing overall efficiency.
Scanning Capabilities
Mobile CMMS integrates scanning capabilities, allowing technicians to quickly retrieve asset information by scanning QR codes or barcodes. This feature streamlines asset identification, inventory management, and maintenance history tracking, enabling technicians to access pertinent information readily. Additional parts can also be ordered using the mobile CMMS. With QR code scanning, a user can scan an asset, location, or part and access details of the asset, location, or part instantly. QR scanning from a mobile device not only gives users instant access to details eliminating time wasted searching, but also prompts users to perform quick actions like submitting a request or work order, updating open work orders, taking equipment offline, and restocking parts.
Camera Capabilities
Another notable feature of mobile CMMS is its camera integration, which enables technicians to capture images of equipment, parts, or issues encountered during inspections or repairs. These images can be directly uploaded to work orders, providing visual context and facilitating better decision-making. The ability to upload images in real-time to work orders, PMs, and requests is a major advantage of using a mobile CMMS app. It enables users to give additional insight into the state of assets and facilities that was previously not possible. A picture is worth more than 1,000 words. Mobile CMMS apps also allow technicians to work offline, ensuring continuity in maintenance activities even in areas with limited connectivity.
Other Unique Capabilities
Depending on the vendor, mobile CMMS may offer additional functionalities tailored to on-the-go maintenance needs, such as GPS tracking for locating assets, voice-to-text capabilities for hands-free data entry, and offline access to manuals and schematics.
Let’s turn to the CMMS mobile’s counterpart, the desktop CMMS version.
Desktop CMMS: Robust Reporting and Configuration Options
While mobile CMMS facilitates on-the-go maintenance tasks, desktop CMMS offers a comprehensive suite of features for in-depth analysis, reporting, and system configuration. Here are the key features you’ll find in the desktop CMMS:
Reporting Capabilities
Desktop CMMS are known for their advanced reporting functionalities, allowing users to generate detailed reports on asset performance, maintenance activities, inventory levels, etc. These reports are invaluable to maintenance managers and company owners because they provide valuable insights for strategic decision-making, resource allocation, and compliance tracking.
Data Import-Export Capabilities
Desktop CMMS enables seamless import and export of data from external sources, facilitating integration with other enterprise systems such as Enterprise Resource Planning (ERP) software or Building Management Systems (BMS). This interoperability enhances data accuracy, eliminates duplication of functions or data, and promotes synergy across organizational functions.
Setting Configurations
Desktop CMMS offers extensive configuration options, allowing administrators to tailor the system to specific organizational requirements. The following options are available from many CMMS vendors:
- Customization of workflows: Maintenance managers can tailor maintenance processes to align with organizational requirements and industry standards. They can also make adjustments to workflows as and when needed.
- User permissions management: Access levels and privileges can be set for different user roles to ensure data security and compliance.
- Asset hierarchy setup: Maintenance managers can hierarchize assets to facilitate organized asset management and maintenance planning.
- Preventive maintenance scheduling: Preventive maintenance schedules can be established based on asset type, usage patterns, and maintenance best practices. As in the case of workflows, they can also be adjusted.
- Notification settings: Maintenance managers can create automated notifications and alerts for maintenance tasks, work order statuses, and upcoming inspections. Based on their job descriptions and locations, different notifications can be sent to specific team members.
- Integration with external systems: Data import-export functionality can be configured to seamlessly exchange information with other enterprise systems such as ERP or BMS.
- Reporting customization: CMMS desktop allows maintenance managers to customize report templates, parameters, and formats to generate tailored insights and analysis.
- Calibration management: Calibration schedules, tolerance thresholds, and calibration procedures can be configured for measurement equipment and instruments.
- Vendor management: Maintenance managers can manage vendor information, contracts, and service agreements to streamline procurement and maintenance activities or communicate as needed.
- Asset tagging and labeling: Systems and labeling conventions can be configured to facilitate asset identification and tracking.
Choosing the Right Version: When to Use Each?
While desktop and mobile CMMS versions offer distinct advantages, their choice depends on operational requirements and user preferences. Here's a guide to selecting the appropriate version that is best fit for your organization:
Mobile CMMS
The mobile CMMS is ideal for maintenance teams that require flexibility and mobility. Mobile CMMS is well-suited for field technicians, remote sites, and industries with distributed assets such as facilities management, utilities, and telecommunications. It facilitates real-time communication, on-the-go access to critical information, and efficient task management, enhancing productivity and responsiveness.
Desktop CMMS
A desktop CMMS is recommended for organizations prioritizing comprehensive reporting, data analysis, and system configuration. It is indispensable for maintenance managers, administrators, and decision-makers. It offers robust reporting capabilities, seamless data integration, and extensive customization options, empowering users to gain actionable insights, optimize resource allocation, and ensure regulatory compliance.
Mobile and Desktop CMMS are not Exclusive. They Work Together.
Investing in a CMMS does not have to be an either-or decision. Since mobile and desktop CMMS versions are potent tools, each can operate as a stand-alone tool. However, many company owners opt for integrating both mobile CMMS and desktop CMMS versions to harness the combined advantages of flexibility, accessibility, and comprehensive functionality. While desktop CMMS provides robust reporting capabilities, extensive configuration options, and in-depth data analysis, mobile CMMS enhances on-the-go maintenance efficiency, communication, and asset management. By integrating both versions, organizations can empower maintenance teams with the tools and resources to perform tasks seamlessly from any location, ensuring prompt response to maintenance requests, minimized downtime, and optimized asset performance. Moreover, the synergy between desktop and mobile CMMS enables organizations to adapt to evolving business needs, enhance operational agility, and continuously improve maintenance management practices. Embracing both versions facilitates a holistic approach to maintenance management, maximizing productivity, and delivering tangible business value across the organization.
Overcoming Resistance to Mobile CMMS Adoption
A topic often overlooked is maintenance team members’ resistance to adopting a mobile CMMS. Despite the myriad benefits of mobile CMMS, some maintenance teams may resist its adoption. Their shared concerns include
Security Issues
Organizations may express apprehensions regarding the security of mobile devices and data privacy risks associated with remote access. Addressing these concerns requires robust security measures such as encryption, multi-factor authentication, and remote device management to safeguard sensitive information and mitigate security threats. Having these security measures in place will help reassure reluctant maintenance team members.
Comfort with Existing Processes
The saying, why fix what isn’t broken, underlies the reasoning behind maintenance team members being wary about using a mobile CMMS. Many accustomed to traditional paper-based or desktop-centric workflows may be reluctant to embrace change and adopt mobile technology. Overcoming resistance necessitates providing comprehensive training, demonstrating the tangible benefits of mobile CMMS, and fostering a culture of innovation and continuous improvement within the organization.
Making the Case for Mobile CMMS Adoption
Despite initial hesitations, companies can gain numerous advantages from embracing mobile CMMS alone or combined with the CMMS desktop version. The case for adopting a mobile CMMS includes
Enhanced Efficiency and Productivity
Mobile CMMS empowers maintenance teams to work more efficiently, save time, respond promptly to maintenance requests, and minimize downtime through real-time communication and on-the-go access to critical information.
Improved Asset Management
By leveraging scanning and camera capabilities, mobile CMMS enables accurate asset identification, streamlined inventory management, and proactive maintenance, prolonging asset lifespan and reducing operational costs.
Flexibility and Agility
In today's fast-paced and competitive business environment, agility and adaptability are crucial for staying competitive. Mobile CMMS allows organizations to address maintenance needs anytime, anywhere, facilitating agile decision-making and operational responsiveness.
Empowered Workforce
Mobile CMMS provides frontline technicians with the tools and resources to perform their tasks more effectively, fostering employee engagement, satisfaction, and retention.
Both desktop and mobile CMMS versions offer unique features and benefits tailored to specific operational requirements. While desktop CMMS excels in reporting, data analysis, and system configuration, mobile CMMS enhances on-the-go maintenance efficiency, communication, and asset management. By embracing mobile technology, companies can overcome resistance, unlock operational efficiencies, and propel maintenance management practices into the digital age. Still, many companies prefer to have all the benefits each offers, so they choose to opt for both versions. Regardless of your choice, the result will be enhanced operations and an improved bottom line.
TABLE OF CONTENTS
Keep Reading
What happens when your most experienced maintenance leader is planning on retiring, taking 20 ...
7 Aug 2025
Today’s maintenance operations have become more complex and sophisticated. Gone are the days ...
5 Aug 2025
Modern warehouses are instrumental to maintaining the smooth operations of supply chains, ...
1 Aug 2025
Computerized Maintenance Management Systems (CMMS) have proven to be essential tools for ...
31 Jul 2025
Sometimes it feels as if technology is expanding at the speed of light. This is an ...
29 Jul 2025
Data Center downtime can have a huge negative impact ranging from damage to the data center’s ...
25 Jul 2025
Whenever a company introduces a new process or technology, it’s followed by a period of ...
24 Jul 2025
Obsolescence often comes unexpectedly, mainly because little attention is given to the ...
22 Jul 2025
Imagine a world where critical assets run smoothly without unexpected downtime, maintenance ...
18 Jul 2025
Imagine you're going through a compliance audit, and the inspector asks for maintenance ...
10 Jul 2025
Maintenance managers understand that disasters are unpredictable and can have a massive ...
4 Jul 2025
Asset lifespan is a key concern for executives and maintenance and facility management teams. ...
3 Jul 2025
Your company recently invested funds and time for new CMMS software, and six months later, it ...
1 Jul 2025
As Computerized Maintenance Management Systems (CMMS) become more connected and cloud-based, ...
1 Jul 2025
Edge computing is an innovative technology that enables data to be processed at the source, ...
24 Jun 2025
Facility management has undergone a significant transformation in recent times. Take, for ...
20 Jun 2025
A facility maintenance plan is at the core of a facility’s operations. This organized ...
19 Jun 2025
In the early days, preventive maintenance could be done effectively with a trained eye and a ...
17 Jun 2025
Sticky notes fall off, whiteboard grids get wiped, and spreadsheets never beep when a ...
13 Jun 2025
Handing a slice of your maintenance workload to a contractor is less about “giving up ...
12 Jun 2025