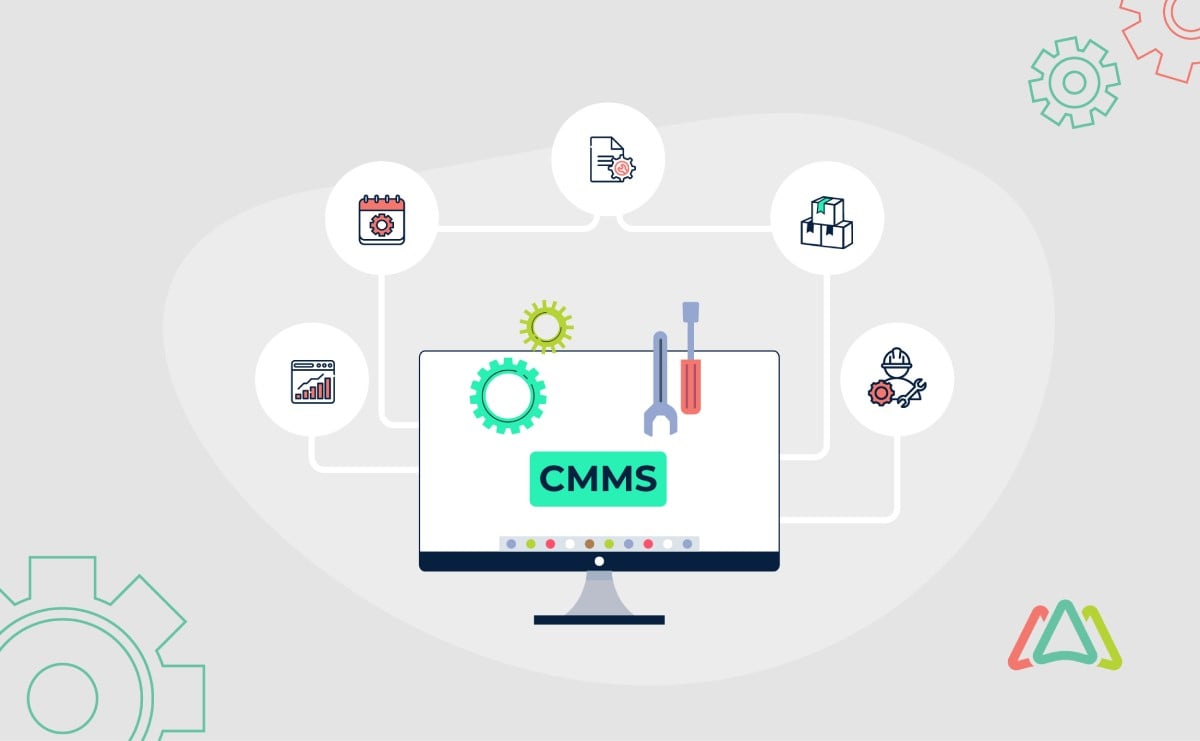
Simplifying Maintenance Operations: The Power of Maintenance Management Tools
Maintenance operations are the backbone of every organization, ensuring the reliability and longevity of critical assets. However, traditional maintenance management can be daunting, with inefficiencies and costly downtime. This scenario is where maintenance management tools step in, revolutionizing how organizations manage their assets and streamline maintenance processes.
Maintenance operations ensure the uninterrupted functionality of equipment, machinery, and infrastructure. These operations are pivotal in industries ranging from manufacturing to healthcare, where the failure of assets can result in costly breakdowns, reduced productivity, and even safety hazards.
Maintenance management tools have emerged as a game-changer, offering innovative solutions to address these challenges and streamline maintenance processes. In this article, we will explore the power of these tools in depth.
Understanding Maintenance Management Tools
Maintenance management tools encompass a wide range of software and hardware solutions designed to facilitate the planning, execution, and monitoring of maintenance activities. Their primary purpose is to optimize maintenance processes and maximize asset performance.
Types of Maintenance Management Tools
- Computerized Maintenance Management Systems (CMMS): The best CMMS helps businesses to efficiently manage work orders, asset databases, and maintenance schedules.
- Enterprise Asset Management (EAM) Software: EAM software goes beyond CMMS by providing comprehensive asset lifecycle management, including procurement, depreciation, and retirement.
- Predictive Maintenance Tools: By leveraging data analytics and machine learning, predictive maintenance tools forecast when equipment is likely to fail, allowing for proactive maintenance.
- Internet of Things (IoT) Sensors and Devices: IoT devices collect real-time data from assets, enabling remote monitoring and condition-based maintenance.
Key Features and Functionalities
- Work Order Management: Efficiently create, assign, and track maintenance tasks.
- Asset Tracking and Management: Maintain a complete record of assets, their history, and performance.
- Inventory Control: Manage spare parts and materials inventory effectively.
- Reporting and Analytics: Generate insightful reports and utilize data analytics for informed decision-making.
- Routine and Predictive Maintenance Capabilities: Optimize preventive maintenance and predict failures to reduce downtime.
Benefits of Using Maintenance Management Tools
Maintenance management tools offer a plethora of advantages. Their benefits include the following:
Increased Efficiency and Productivity
Schedules, work orders, and documentation are automated by maintenance management technologies, improving efficiency and productivity. Streamlining operations and giving technicians real-time data on mobile devices eliminates tedious paperwork and administrative costs.
Teams can focus on key maintenance, respond faster to concerns, and perform jobs more efficiently. This productivity improvement reduces overtime, labor expenses, and operational inefficiency.
Budget Optimization and Cost Reduction
Organizations can precisely plan and perform maintenance operations with proactive maintenance management technologies. By following maintenance schedules, businesses can increase asset life, reduce breakdowns, and eliminate costly emergency repairs.
This proactive approach optimizes resource and budget allocation and reduces repair costs. Better visibility into maintenance needs allows firms to allocate data-based resources, maximizing expenditures.
Enhanced Asset Reliability and Lifespan
Maintenance management tools improve asset reliability and lifespan, a major benefit. Tracking asset performance, maintenance history, and condition-based maintenance data helps organizations recognize and reduce downtime.
This approach avoids unexpected breakdowns and maximizes equipment availability. Prevention and predictive maintenance strategies based on real-time data ensure that assets receive attention, extending their lifespans and reducing replacement costs.
Improved Safety and Compliance
Safety and regulation are important in many sectors. Maintenance management tools are crucial to meeting safety and regulatory criteria. Organizations can prove compliance with these tools' maintenance documents and audit trails.
By permitting preventative maintenance, businesses can reduce equipment failures that could be dangerous. This proactive strategy improves safety and reduces legal and financial risks associated with non-compliance, giving organizations peace of mind.
Streamlined Communication and Collaboration
Maintenance personnel, managers, and stakeholders collaborate through maintenance management technologies. Everyone involved in maintenance can keep informed and aligned with consolidated work orders, asset information, and real-time updates.
Technicians can easily report concerns and progress, management can make data-driven choices, and stakeholders may obtain maintenance information when needed. This improved communication encourages collaboration, decreases miscommunication, and speeds up issue resolution and operational efficiency.
Data-Driven Decision-Making
Organizations seeking data-driven decisions benefit from historical maintenance data and real-time insights. These tools give a wealth of asset performance, maintenance cost, and resource allocation data. By analyzing this data, organizations can detect patterns and enhance and optimize their maintenance programs.
This data-driven method optimizes resource allocation, placing maintenance crews where required. It helps firms make informed capital investment, equipment upgrade, and maintenance prioritization decisions, improving operational efficiency and cost-effectiveness.
Improved Workforce Satisfaction and Retention
While the benefits of maintenance management tools often focus on operational efficiencies, they also significantly improve employee satisfaction and retention. These tools streamline workflows, automate mundane tasks, and reduce the stress of managing reactive maintenance crises. With clear visibility into asset performance and well-organized work orders, technicians can plan their days better, focus on high-value tasks, and reduce unplanned downtime that often leads to pressure-filled situations. Moreover, mobile-enabled tools allow maintenance teams to access data and complete tasks from any location, increasing flexibility and reducing the frustrations associated with paperwork or manual data entry.
By providing real-time support and simplifying job execution, maintenance management tools empower employees to do their jobs more effectively, resulting in a more motivated and engaged workforce. Furthermore, the transparency these tools offer creates a sense of accountability and achievement, as technicians can track their progress and contribution to the company’s goals. In the long run, adopting modern tools leads to improved job satisfaction, reducing turnover and fostering a more stable, experienced maintenance team - a critical asset in industries where skilled labor shortages are a growing concern.
Implementing Maintenance Management Tools: Best Practices
Adopting best practices can significantly increase the chances of a successful implementation and a quick return on investment. Here are some key best practices:
1. Define Clear Objectives and Requirements
Start by defining your organization's maintenance objectives and specific requirements. Understand what issues you want to address and the goals you aim to achieve with the new tool. This clarity will guide your tool selection and implementation strategy.
2. Involve Key Stakeholders
Engage all relevant stakeholders early in the process, including maintenance technicians, managers, IT personnel, and end-users. Their input is essential for identifying needs, addressing concerns, and ensuring buy-in from all parties.
3. Choose the Right Tool
To know if a preventive maintenance solution is right for your business, you must thoroughly evaluate the tool. Choose one that aligns best with your organization's size, industry, and unique needs. Consider factors such as scalability, customization options, ease of use, and compatibility with existing systems.
4. Comprehensive Training and Onboarding
Provide thorough training for all users, from maintenance technicians to managers. Tailor training programs to individual roles to ensure everyone learns how to use the tool effectively. Offer ongoing training and support as needed.
5. Data Migration and System Integration
Ensure a smooth transition by accurately migrating existing maintenance data to the new system. Ensure the maintenance management tool integrates seamlessly with other systems, such as ERP software or asset management systems, to prevent data silos.
6. Set Key Performance Indicators
Establish measurable KPIs to evaluate the success of the implementation. Track vital inventory management KPIs such as efficiency, cost savings, asset reliability, and user satisfaction metrics. Assess progress regularly and make adjustments as needed.
7. Continuous Improvement
Promote an environment where customer suggestions are heard and acted upon, and procedures are continually fine-tuned. Regularly review and update maintenance strategies and workflows to align with industry best practices and changing organizational needs.
Challenges and Considerations
While maintenance management tools offer numerous benefits, they also come with challenges:
Data Security and Privacy Concerns
Maintenance management tools store sensitive asset histories, work orders, and schedules. Security and privacy are crucial for this data. Encryption, access controls, and secure authentication are needed to prevent data breaches and unwanted access.
Organizations must also follow sector-specific data protection laws and standards like GDPR or HIPAA. Maintaining data integrity and confidentiality requires regular audits, risk assessments, and secure data storage and transmission.
Integration with Existing Systems
Many companies have legacy systems to run their operations. New maintenance management technologies can be difficult to integrate with legacy systems. Avoiding data silos and unified maintenance tasks requires continuous data exchange between systems.
This setup needs careful planning, compatible software architecture, and occasionally special development to connect new and old systems. Organizations should examine integration requirements early in the implementation process and consider cost, time, and resources for success.
Maintenance Management Tool Scalability
Organizational maintenance needs and activities may change. Thus, the maintenance management technology must be scalable to meet expansion and changing needs. Scalability includes handling rising data volumes and adding new features as needed.
Organizations should assess whether the tool can expand with growth and technology to prevent limits and costly system migrations. Scalability keeps the technology useful as the company grows.
Employee Resistance and Adoption Challenges
Employees who used to do things the old way may resist new technology, particularly maintenance management systems. Successful implementation requires overcoming this opposition and ensuring easy uptake. Businesses must employ effective CMMS user adoption strategies like teaching employees the new platform's features and benefits through training and education.
Involving employees in decision-making, asking their opinions, and addressing their concerns can also increase buy-in and lessen resistance. Change management tactics like clear communication and incentives for adopting new tools can also help.
The Importance of Ongoing Support and Updates
Maintenance management tools need ongoing upkeep and updates to meet changing maintenance needs. Organizations require a solid support system to resolve difficulties, answer questions, and offer advice.
Software updates and patches are necessary to fix flaws, boost performance, and add functionality. These upgrades keep the product useful and current with industry trends and best practices. Inefficiency, security risks, and tool inefficiency can result from neglecting support and updates.
From Overhaul to Optimization: Unleashing the Potential of Maintenance Management Tools
Maintenance management tools can revolutionize maintenance operations, simplifying processes, reducing costs, and improving asset reliability. Embracing these tools is not just a step forward; it's a leap toward the digital transformation of industries. By investing in the right maintenance management solution and addressing implementation challenges, businesses can ensure their operations function smoothly and efficiently, boosting output, security, and profits.
TABLE OF CONTENTS
Keep Reading
B2C businesses, such as retail, hospitality, and food service, operate in a highly ...
8 Aug 2025
What happens when your most experienced maintenance leader is planning on retiring, taking 20 ...
7 Aug 2025
Today’s maintenance operations have become more complex and sophisticated. Gone are the days ...
5 Aug 2025
Modern warehouses are instrumental to maintaining the smooth operations of supply chains, ...
1 Aug 2025
Computerized Maintenance Management Systems (CMMS) have proven to be essential tools for ...
31 Jul 2025
Sometimes it feels as if technology is expanding at the speed of light. This is an ...
29 Jul 2025
Data Center downtime can have a huge negative impact ranging from damage to the data center’s ...
25 Jul 2025
Whenever a company introduces a new process or technology, it’s followed by a period of ...
24 Jul 2025
Obsolescence often comes unexpectedly, mainly because little attention is given to the ...
22 Jul 2025
Imagine a world where critical assets run smoothly without unexpected downtime, maintenance ...
18 Jul 2025
Imagine you're going through a compliance audit, and the inspector asks for maintenance ...
10 Jul 2025
Maintenance managers understand that disasters are unpredictable and can have a massive ...
4 Jul 2025
Asset lifespan is a key concern for executives and maintenance and facility management teams. ...
3 Jul 2025
Your company recently invested funds and time for new CMMS software, and six months later, it ...
1 Jul 2025
As Computerized Maintenance Management Systems (CMMS) become more connected and cloud-based, ...
1 Jul 2025
Edge computing is an innovative technology that enables data to be processed at the source, ...
24 Jun 2025
Facility management has undergone a significant transformation in recent times. Take, for ...
20 Jun 2025
A facility maintenance plan is at the core of a facility’s operations. This organized ...
19 Jun 2025
In the early days, preventive maintenance could be done effectively with a trained eye and a ...
17 Jun 2025
Sticky notes fall off, whiteboard grids get wiped, and spreadsheets never beep when a ...
13 Jun 2025