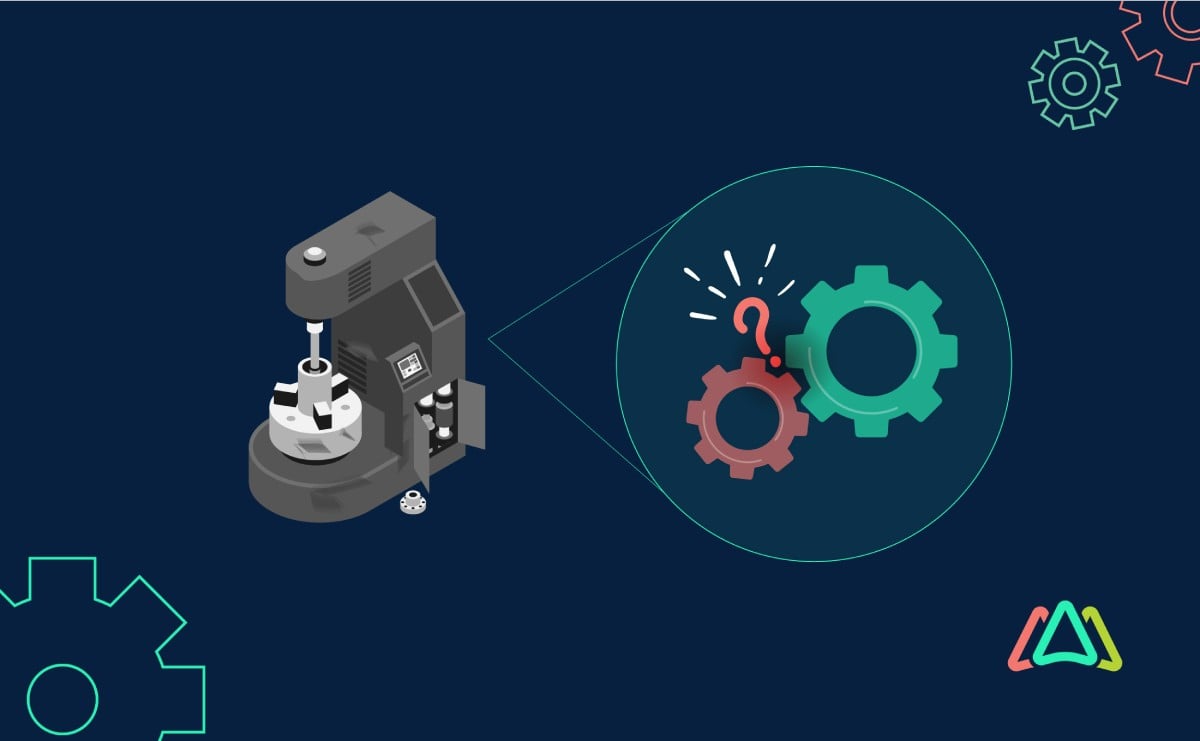
Exploring Equipment Failure Causes and Winning the Battle with CMMS Software
From manufacturing plants and healthcare facilities to transportation services, equipment reliability is the backbone of countless operations. In manufacturing, machines, conveyors, and robotics enable the creation of products. In healthcare, the reliability of medical equipment can be a matter of life and death. Transportation services rely on the consistent performance of vehicles to ensure safe and efficient travel.
Without well-maintained and reliable equipment, the functionality, safety, and competitiveness of any organization can be severely compromised. When equipment falters, it can disrupt operations, lead to costly downtime, increase maintenance expenses, and, in some cases, pose safety risks to personnel. The consequences of equipment failures go beyond mere inconvenience; they can have widespread financial and operational impacts.
The financial and operational consequences of equipment failures are far-reaching and can be financially crippling. Consider the case of manufacturing plants and factories. Equipment breakdowns can disrupt the entire production line, causing delays and hampering the delivery of goods to customers. These disruptions can lead to lost revenue, damaged customer relationships, and decreased market competitiveness.
The True Cost of Downtime Report by Siemens states that the average annual cost of unplanned downtime to each plant operated by a Fortune Global 500 firm is a staggering $129 million USD yearly.
Source: Siemens
This article covers common causes of equipment failure and explores how CMMS software can be instrumental in not only understanding these causes but also preventing them.
Understanding Equipment Failure and its Impact
Equipment failure refers to a situation where a piece of machinery or a device ceases to operate as intended. It marks the moment when equipment reliability breaks down and it no longer fulfills its primary function. Equipment failure can manifest in various ways, ranging from minor disruptions to catastrophic breakdowns.
Equipment failure can result in:
- Downtime: Perhaps the most immediate and apparent consequence, downtime, is the period during which equipment is inoperable. It leads to the suspension of production or services, causing disruptions in workflow and timelines.
- Reduced Productivity: When equipment fails, the efficiency and productivity of workers diminish as they are unable to carry out their tasks. This decrease in productivity affects the bottom line, as less work is completed in a given time frame.
- Increased Costs: Equipment failures often lead to unexpected costs. These include not only the expense of repairing or replacing the equipment but also the cost of idle labor, overtime to compensate for lost time, and expedited shipping for replacement parts.
- Missed Deadlines: Failure to meet production deadlines or service commitments due to equipment breakdown can tarnish a company's reputation and result in customer dissatisfaction. Lost trust may be challenging to regain.
- Safety Risks: Equipment failures can pose significant safety risks to personnel. For instance, a sudden machine malfunction in a manufacturing facility may lead to accidents and injuries.
- Wasted Resources: When equipment fails prematurely, the resources invested in its purchase, installation, and maintenance are wasted, impacting an organization's return on investment.
Common Causes of Equipment Failure
1. Lack of Routine Maintenance
The neglect of routine maintenance can result in a cascade of adverse consequences:
- Costly Repairs: When maintenance is deferred, minor issues often transform into major, costly breakdowns. The financial burden of these unexpected repairs can strain an organization's budget.
- Downtime: Equipment breakdowns stemming from neglected maintenance lead to downtime. This disrupts operations, causes delays, and results in lost revenue. Downtime's ripple effect can be detrimental.
- Reduced Lifespan: Neglecting equipment upkeep accelerates wear and tear, reducing equipment lifespan. This necessitates premature replacements, which can incur substantial capital expenses.
- Safety Risks: Industries where safety is paramount, such as aviation and healthcare, are especially vulnerable to the consequences of maintenance neglect. Equipment malfunctions due to deferred maintenance can pose severe safety hazards.
- Reputation Damage: Frequent equipment failures due to maintenance negligence can tarnish an organization's reputation. Customers may lose trust, and competitors may seize opportunities.
2. Wear and Tear
Wear and tear are inevitable consequences of an equipment's operational life. They occur due to regular use, friction, and the passage of time. While wear and tear are natural, they have a significant impact on the performance and longevity of equipment. Here's how they affect equipment:
- Component Degradation: Over time, moving parts experience friction and minor damage, causing components to degrade. This degradation may result in loose or misaligned parts, leading to diminished performance.
- Reduction in Efficiency: As components wear down, equipment may become less efficient. For instance, a conveyor belt with worn-out rollers may no longer transport materials as smoothly and swiftly as it once did.
- Increased Maintenance Requirements: Equipment experiencing wear and tear often requires more frequent maintenance. This includes lubrication, part replacements, and adjustments to ensure continued functionality.
- Potential for Breakdowns: Severe wear and tear, left unaddressed, can lead to equipment breakdowns. A classic example is a vehicle engine with a worn-out piston, which can seize up and cause severe damage.
Examples of Equipment Susceptible to Wear and Tear
- Conveyor Systems: In manufacturing and distribution facilities, conveyor systems are prone to wear and tear, especially components like belts, rollers, and bearings.
- Vehicles: Automobiles, trucks, and heavy machinery like bulldozers and forklifts are subject to wear and tear, affecting their engines, tires, and moving parts.
- Industrial Pumps: Pumps used in industrial processes often experience wear and tear in seals, impellers, and motor components, leading to reduced efficiency and potential breakdowns.
- Printing Machinery: Printing presses and copiers frequently encounter wear and tear with their rollers, print heads, and other moving components, affecting print quality and consistency.
- HVAC Systems: Heating, ventilation, and air conditioning (HVAC) systems in commercial buildings and residential homes endure wear and tear, leading to diminished heating or cooling efficiency.
- Engines and Motors: In various machines, engines and motors face wear and tear in pistons, bearings, and gears, impacting their performance and longevity.
- Tools and Equipment: Hand tools, power tools, and industrial equipment all experience wear and tear through regular use and exposure to environmental factors, resulting in diminished functionality over time.
3. Improper Use and Handling
Equipment is designed to function optimally under specific conditions and within certain operational parameters. When equipment is subjected to improper use and handling, it can significantly impact its longevity and overall performance. Here's how:
- Accelerated Wear and Tear: Misusing or mishandling equipment can lead to accelerated wear and tear. For example, overloading a vehicle beyond its recommended capacity can strain its engine and suspension, causing premature component degradation.
- Mechanical Stress: Improper usage can subject equipment to mechanical stress it was not designed to withstand. This stress can manifest as excessive vibrations, shocks, or torsion, leading to the breakdown of critical components.
- Inefficient Operation: Operating equipment in ways that deviate from recommended procedures often results in inefficiencies. This inefficiency can translate into increased energy consumption and reduced output quality, directly impacting the equipment's operational costs and reliability.
- Safety Hazards: Mishandling equipment can pose safety hazards to personnel and bystanders. Inadequate understanding of safety protocols can result in accidents and injuries. For example, failing to follow proper procedures when using power tools can lead to accidents.
The Role of User Training in Preventing Mishandling
User training should be an integral part of any organization's equipment management strategy. Here's how it contributes to equipment longevity and safe operation:
- Better Understanding: Training equips users with a comprehensive understanding of equipment specifications, limitations, and safe operating procedures. When users are aware of these critical details, they are less likely to misuse equipment.
- Safety Awareness: Training emphasizes safety protocols and the potential risks associated with improper equipment usage. This heightened safety awareness encourages users to follow guidelines rigorously, reducing the likelihood of accidents.
- Efficient Operation: Properly trained users are more likely to operate equipment efficiently. This leads to a reduction in wear and tear, as equipment is used within its designed parameters. Efficient operation also minimizes energy consumption and improves output quality.
- Maintenance Practices: Training often includes education on routine maintenance tasks and the importance of reporting issues promptly. Users who understand maintenance practices are more likely to contribute to equipment reliability by detecting and addressing problems in their early stages.
- Compliance with Regulations: In some industries, adherence to safety and operational regulations is mandatory. Training ensures users are well-versed in these regulations, preventing violations that can lead to penalties and legal complications.
4. Environmental Factors
Environmental factors, such as temperature, humidity, and dust, can significantly influence the performance and longevity of equipment. These conditions are often beyond an organization's control. They can have various effects:
- Temperature: Extreme temperatures can cause equipment to expand or contract, affecting the fit of moving parts. This can lead to increased friction and wear. Additionally, temperature fluctuations can cause condensation, leading to corrosion and electrical issues.
- Humidity: High humidity can promote rust and corrosion, especially in metallic equipment components. Excess moisture can also lead to short circuits and electrical malfunctions. On the other hand, low humidity can lead to static electricity and brittle components.
- Dust: Dust and particulate matter can infiltrate equipment and clog air filters, leading to overheating and decreased airflow. Dust particles can also cause abrasion, accelerating wear and tear on moving parts. In severe cases, dust accumulation can lead to equipment breakdowns.
Equipment Vulnerability to External Conditions
Outdoor Equipment: Equipment located outdoors, such as construction and agricultural machinery, is exposed to the elements regularly. Rain, snow, UV radiation, and extreme temperatures can deteriorate these machines, impacting their performance and useful life.
- Manufacturing Facilities: In manufacturing, equipment is exposed to various environmental factors, including temperature variations and dust from production processes. The impact of these factors on equipment longevity can be substantial.
- Healthcare: In the healthcare sector, medical equipment must operate in specific environmental conditions to ensure patient safety. For instance, operating rooms require equipment that can withstand high humidity for sterilization purposes.
- Transportation: Vehicles, such as airplanes and ships, face extreme environmental conditions, including fluctuating temperatures and exposure to saltwater. Regular maintenance and protective measures are essential to mitigate environmental impacts.
To address the vulnerability of equipment to external conditions, organizations must implement preventive and protective measures. This can include climate control systems, proper storage facilities, and the regular inspection and cleaning of equipment to ensure it remains in optimal condition. Additionally, it's vital to factor in the environment when selecting equipment for specific applications, as some designs and materials are better suited to withstand harsh conditions.
5. Aging Equipment
As equipment gets older, it becomes increasingly susceptible to failures for several reasons:
- Wear and Tear Accumulation: Over time, equipment accumulates wear and tear from regular use. This gradual degradation affects the performance and reliability of components. Good-condition parts become brittle or weakened, making them prone to failure.
- Limited Availability of Replacement Parts: As equipment ages, the availability of spare parts and components may decrease. Manufacturers may discontinue producing parts for older models, making it challenging to find replacements in the event of a breakdown.
- Reduced Efficiency: Aging equipment operates less efficiently than newer models. Inefficiencies in older equipment can lead to increased energy consumption and decreased output quality, making it more costly to operate.
- Maintenance Complexity: Older equipment may require more intricate maintenance and repair procedures. Technicians may need specialized knowledge and experience to service older models effectively, which can be a limiting factor.
- Obsolete Technology: Older equipment often relies on outdated technology and may lack compatibility with newer systems and software. This technological gap can lead to compatibility issues, making it difficult to integrate older equipment into modern operations.
Challenges of Maintaining Older Machinery
The maintenance and upkeep of older machinery can be challenging due to the following reasons:
- Limited Documentation: Older equipment may lack comprehensive and updated documentation, making it challenging to conduct maintenance and repairs. This absence of documentation can result in more extended downtimes as technicians struggle to diagnose and address issues.
- Parts Availability: The availability of replacement parts for aging equipment can be a significant hurdle. Suppliers may have discontinued production, forcing organizations to source parts from alternative suppliers or fabricate custom components, which can be time-consuming and costly.
- Skill Gap: Skilled technicians familiar with older equipment may be in short supply. As a result, organizations may need to invest in training or hire specialists with knowledge of older machinery, adding to operational costs.
- Cost of Maintenance: Maintaining older equipment can be more expensive due to the need for more frequent repairs and the costs associated with specialized maintenance procedures and parts sourcing.
- Downtime and Production Disruptions: Older equipment is more prone to unplanned breakdowns, resulting in extended downtime and disruptions in production or service delivery. This can lead to financial losses and negatively impact an organization's reputation.
6. Overloading and Overuse
Subjecting equipment to conditions beyond its designed capacity can lead to adverse consequences:
- Structural Stress: Overloading places excessive stress on a piece of equipment's structural components. This stress can lead to deformation, cracking, or even catastrophic failure of critical parts. For example, consistently overloading a forklift beyond its weight limit can result in frame damage and compromised structural integrity.
- Accelerated Wear and Tear: Overuse and excessive loads accelerate the wear and tear of moving parts. This results in increased friction, heat generation, and component degradation. The consequence is a reduced lifespan of the equipment, as components become prone to failure.
- Reduced Efficiency: Overloaded equipment operates less efficiently. For example, an air conditioner designed for a specific room size may struggle to cool a larger space, consuming more energy and offering diminished performance. This inefficiency translates into higher operational costs.
- Increased Maintenance Requirements: Overuse and excessive loads often necessitate more frequent and intensive maintenance. Routine maintenance, parts replacement, and repairs become more common, increasing operational costs.
- Safety Hazards: Subjecting equipment to overloading and excessive usage poses significant safety risks. For instance, overloading a crane may lead to structural failure and dangerous accidents. Overused machinery can be prone to sudden malfunctions, jeopardizing the safety of operators and bystanders.
Real-World Examples:
- Elevators in High-Rise Buildings: Elevators in tall buildings are subjected to excessive usage. Over time, this can lead to accelerated wear and tear, necessitating more maintenance and repairs. In extreme cases, overuse can result in elevator breakdowns, causing inconvenience and potentially posing safety risks to occupants.
- Delivery Trucks: Delivery trucks and vans are often overloaded with cargo, exceeding their designed weight capacity. The consistent overloading can lead to premature suspension and tire wear, affecting fuel efficiency and necessitating frequent maintenance.
- Agricultural Equipment: Farm machinery, like tractors and combine harvesters, is frequently operated for extended hours during peak seasons. Excessive usage can lead to worn-out components, reduced fuel efficiency, and more frequent breakdowns, impacting crop harvesting and overall farm productivity.
- Commercial Refrigeration Units: Refrigeration units in supermarkets and restaurants are often overloaded with perishable goods. This can lead to increased energy consumption, decreased cooling efficiency, and a shorter lifespan of the refrigeration equipment.
- Forklifts in Warehouses: Forklifts are commonly overloaded with heavy loads in busy warehouses. Over time, this can result in structural damage, requiring repairs and affecting the warehouse's productivity.
Leveraging CMMS Software to Prevent Equipment Failure
Following are the core features of CMMS software that contribute to equipment reliability and longevity:
Preventive Maintenance Scheduling
CMMS software automates the scheduling of preventive maintenance tasks, simplifying a complex and time-consuming process. It achieves this through:
- Maintenance Calendar: CMMS software provides a centralized calendar that displays upcoming work orders and maintenance tasks with due dates. This visual representation helps maintenance teams plan their work efficiently.
- Automated Reminders: The software sends automated reminders to maintenance technicians and managers, ensuring that no task goes unnoticed. This proactive approach keeps maintenance on track.
- Predictive Scheduling: CMMS software can predict maintenance intervals based on historical data and equipment performance. This predictive scheduling minimizes the guesswork in maintenance planning.
Asset Tracking and Management
CMMS software keeps a comprehensive record of equipment history, which includes maintenance activities, repairs, replacements, and performance data. This historical record provides valuable insights into the equipment's condition and performance.
By tracking equipment history, CMMS software enables organizations to:
- Spot Trends: By analyzing historical data, organizations can identify trends in equipment performance and reliability. Patterns of deterioration or recurring issues can be addressed proactively.
- Predictive Insights: Data from equipment history allows for predictive maintenance. By recognizing issues before they lead to failure, organizations can address problems in their early stages, minimizing the risk of costly breakdowns.
- Optimize Maintenance: CMMS software helps optimize maintenance schedules and activities based on historical performance data, ensuring that maintenance efforts are effective and efficient.
- Parts Inventory Management: Equipment history informs organizations about the parts and components that are frequently replaced. This data helps maintain an efficient spare parts inventory, reducing downtime and costs associated with parts sourcing.
Work Order Management
CMMS software simplifies work order management by:
- Automated Work Order Generation: It can automatically generate work orders based on scheduled maintenance tasks, reported issues, or predictive alerts.
- Centralized Work Order Tracking: The software provides a centralized platform for creating, assigning, and tracking work orders, streamlining communication and accountability.
Role of Work Orders:
- Prompt Attention: Work orders ensure that maintenance tasks are assigned and executed promptly, minimizing downtime and reducing the risk of equipment failure.
- Detailed Instructions: Work orders provide detailed instructions to maintenance technicians, helping them identify and resolve equipment issues effectively.
Data Analysis and Predictive Maintenance
CMMS software uses historical and real-time data to predict equipment failure by:
- Condition Monitoring: By continuously monitoring equipment conditions, CMMS software can detect deviations from optimal performance, which may indicate impending failures.
- Predictive Analytics: The software employs predictive analytics models that analyze data to forecast when equipment is likely to fail, allowing for proactive intervention.
Predictive maintenance, driven by CMMS software, offers significant benefits:
- Optimized Maintenance: Predictive maintenance allows organizations to focus their resources on equipment that truly requires attention, optimizing maintenance efforts.
- Reduced Downtime: By predicting failures before they occur, organizations can perform maintenance during scheduled downtimes, minimizing disruptions to operations.
- Cost Savings: Predictive maintenance reduces unexpected repair and replacement costs, contributing to significant cost savings in the long run.
CMMS software is a valuable tool for organizations looking to optimize equipment maintenance practices, reduce costs, enhance reliability, and ensure a safe and efficient operational environment. Its capabilities extend to various industries, making it a versatile solution for equipment maintenance needs.
TABLE OF CONTENTS
Keep Reading
What happens when your most experienced maintenance leader is planning on retiring, taking 20 ...
7 Aug 2025
Today’s maintenance operations have become more complex and sophisticated. Gone are the days ...
5 Aug 2025
Modern warehouses are instrumental to maintaining the smooth operations of supply chains, ...
1 Aug 2025
Computerized Maintenance Management Systems (CMMS) have proven to be essential tools for ...
31 Jul 2025
Sometimes it feels as if technology is expanding at the speed of light. This is an ...
29 Jul 2025
Data Center downtime can have a huge negative impact ranging from damage to the data center’s ...
25 Jul 2025
Whenever a company introduces a new process or technology, it’s followed by a period of ...
24 Jul 2025
Obsolescence often comes unexpectedly, mainly because little attention is given to the ...
22 Jul 2025
Imagine a world where critical assets run smoothly without unexpected downtime, maintenance ...
18 Jul 2025
Imagine you're going through a compliance audit, and the inspector asks for maintenance ...
10 Jul 2025
Maintenance managers understand that disasters are unpredictable and can have a massive ...
4 Jul 2025
Asset lifespan is a key concern for executives and maintenance and facility management teams. ...
3 Jul 2025
Your company recently invested funds and time for new CMMS software, and six months later, it ...
1 Jul 2025
As Computerized Maintenance Management Systems (CMMS) become more connected and cloud-based, ...
1 Jul 2025
Edge computing is an innovative technology that enables data to be processed at the source, ...
24 Jun 2025
Facility management has undergone a significant transformation in recent times. Take, for ...
20 Jun 2025
A facility maintenance plan is at the core of a facility’s operations. This organized ...
19 Jun 2025
In the early days, preventive maintenance could be done effectively with a trained eye and a ...
17 Jun 2025
Sticky notes fall off, whiteboard grids get wiped, and spreadsheets never beep when a ...
13 Jun 2025
Handing a slice of your maintenance workload to a contractor is less about “giving up ...
12 Jun 2025