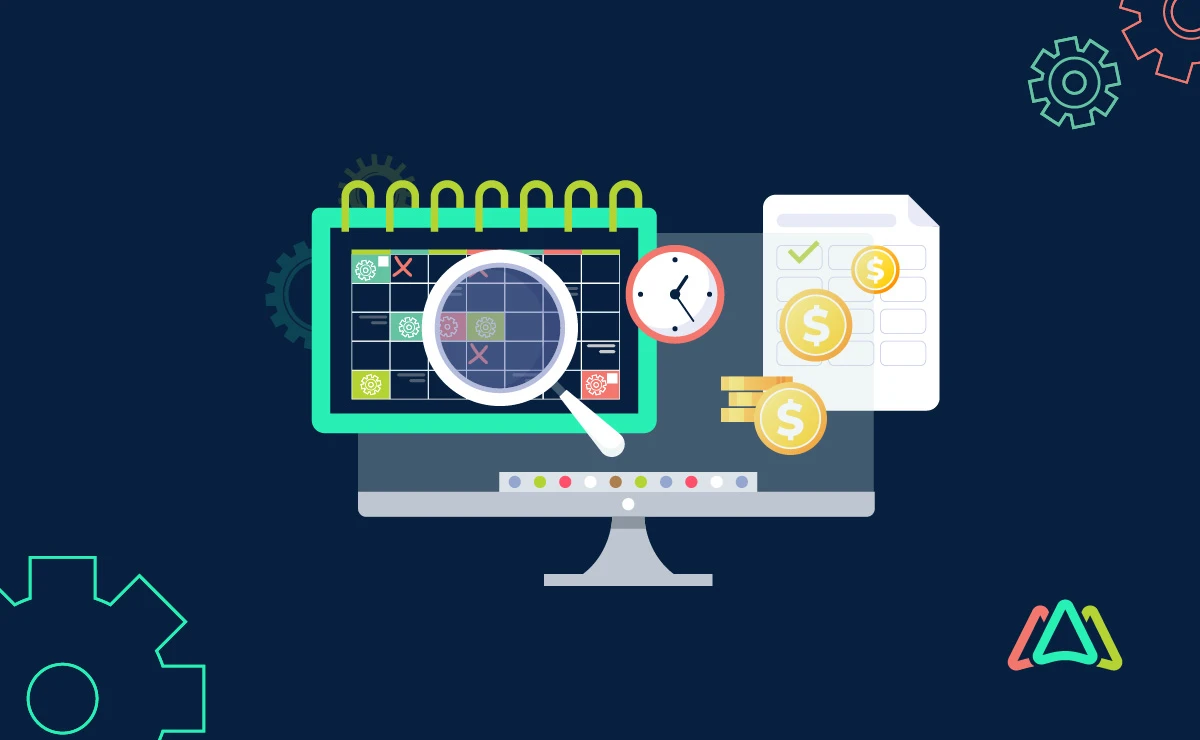
Navigating CMMS Software for Cost-Effective Maintenance Management
Computerized Maintenance Management Systems (CMMS) are recognized for their ability to streamline maintenance operations through instant access to data and automated workflows. Out of all the features that a CMMS offers, preventive maintenance remains the most popular due to its ability to identify and resolve maintenance issues before they become costly breakdowns. The increasing popularity of CMMS in the marketplace confirms that preventive maintenance is one of the best ways to achieve long-term maintenance goals by reducing downtime, increasing productivity, and extending the lifespan of assets.
Despite the benefits of implementing preventive maintenance into the maintenance strategy, it can be a challenging task as there is no exact blueprint available. This is because every organization has its unique combination of assets, workflows, and scheduling demands that require a tailored approach. Consequently, there is no fixed formula for achieving the perfect balance between optimizing resources and ensuring efficient workflows while avoiding unnecessary preventive maintenance. Finding the sweet spot between an optimal approach and overkill requires a bit of research and careful planning.
It's important to avoid costly equipment breakdowns and production delays, but it's also possible to have too much of a good thing. If preventive maintenance is being performed more than needed, unnecessary maintenance costs pile up. So, the question is: when does preventive maintenance become overkill? And how can CMMS software help in finding the right balance?
Using a CMMS for Preventive Maintenance
Preventive maintenance is like a routine check-up for your organization's operational health. It systematically schedules routine inspections, servicing, and repairs to equipment and facilities to forestall breakdowns and maintain optimal performance. Maintenance managers can configure a CMMS to conduct these checks and servicing at set intervals based on manufacturer recommendations, past equipment performance, and the age of certain assets.
Companies using traditional maintenance management practices rely on manual record-keeping and reactive approaches to perform preventive maintenance operations. These approaches often lead to inefficiencies, oversights, and costly equipment repairs or replacements. However, with the introduction of CMMS software, maintenance management has been revolutionized by offering streamlined solutions for planning, executing, and tracking maintenance activities. These automated platforms empower businesses with comprehensive insights, real-time monitoring, and predictive analytics, enhancing decision-making and resource allocation.
Navigating the Threshold: When Does Preventive Maintenance Become Overkill?
There is no doubt that CMMS-guided preventive maintenance is beneficial. However, when preventive maintenance is used indiscriminately, it can lead to over-maintenance, draining resources without any material benefits. Here are key indicators signaling that your preventive maintenance efforts might be veering into overkill territory:
1. Excessive Downtime
If scheduled maintenance activities frequently disrupt operations without yielding substantial improvements in equipment reliability, it may indicate over-maintenance. CMMS software facilitates data-driven analysis to optimize maintenance schedules, ensuring minimal disruption while maximizing asset uptime.
2. Increasing Costs
When maintenance expenses outstrip the potential savings from averting breakdowns, it warrants a reassessment of preventive maintenance strategies. CMMS software enables cost-benefit analysis by tracking maintenance costs, equipment performance, and return on investment (ROI), aiding in informed decision-making. Maintenance managers should consider the value of the asset, replacement cost, and cost to perform PMs vs. repairing. Simply put, if it is less costly to replace or repair an asset compared to regular preventive maintenance, don’t put a preventive maintenance plan in place.
3. Redundant Tasks
Repetitive or unnecessary maintenance tasks consume resources and manpower, diminishing efficiency. CMMS software offers visibility into historical maintenance data, enabling businesses to identify redundant activities and refine maintenance plans for greater efficacy.
4. Ineffective Asset Management
Over-maintenance can impede asset utilization by allocating excessive resources to low-priority equipment or neglecting critical assets. CMMS software facilitates asset prioritization based on criticality, usage patterns, and maintenance history, optimizing resource allocation and prolonging asset lifespan.
Leveraging CMMS Software for an Optimal Maintenance Management Program
In the pursuit of cost-effective maintenance management, CMMS software helps maintenance managers in achieving an optimal preventive management program. The following CMMS features are ways the technology benefits maintenance teams:
1. Streamlined Workflows
CMMS software automates tasks, such as work order generation, scheduling, and asset tracking, streamlining maintenance workflows and minimizing administrative overhead. Businesses can enhance efficiency and responsiveness by automating processes and fostering a proactive maintenance culture.
2. Data-Driven Insights
With CMMS software, businesses gain access to real-time data and analytics, empowering informed decision-making. By analyzing maintenance trends, equipment performance, and downtime patterns, businesses can fine-tune preventive maintenance strategies for best results.
3. Proactive Maintenance
By harnessing predictive maintenance capabilities embedded in some advanced CMMS programs, businesses can more precisely anticipate equipment failures and schedule maintenance activities accordingly. Maintenance managers can minimize downtime and maximize asset reliability with Predictive Maintenance. Predictive analytics, coupled with IoT sensors and machine learning algorithms, enable early detection of anomalies, facilitating proactive interventions.
4. Regulatory Compliance
CMMS software offers comprehensive documentation and audit trails, facilitating compliance with regulatory requirements and industry standards. By centralizing maintenance records, businesses can demonstrate adherence to maintenance protocols and avoid compliance risks, penalties, or legal liabilities.
5. Scalability and Flexibility
CMMS software offers scalability and adaptability to accommodate evolving business needs, whether managing a single facility or a growing enterprise. A CMMS that can accommodate a growing company’s changing needs means that its preventive maintenance program can adjust accordingly. Many CMMS solutions scale with growing enterprises offering features like multi-site management, multi-currency, and multiple languages.
Calculating the ROI of CMMS Investment
While the upfront cost of implementing CMMS software may give businesses pause, the long-term benefits of these systems most often outweigh the initial investment. To understand the ROI of CMMS software, businesses should consider the following factors:
1. Cost Savings
By minimizing downtime, reducing maintenance costs, and optimizing resource utilization, CMMS software delivers tangible cost savings over time. Businesses can quantify these savings by comparing maintenance expenses before and after CMMS implementation, factoring in labor costs, spare parts inventory, and equipment uptime.
2. Improved Efficiency
CMMS software can significantly improve operational efficiency by automating routine tasks, streamlining workflows, and facilitating data-driven decision-making. This can help maintenance managers to focus on maintenance operations rather than spending time creating schedules and deploying employees manually. By measuring key performance indicators such as mean time to repair (MTTR), planned maintenance percentage, and overall equipment effectiveness (OEE), businesses can quantify efficiency gains.
3. Enhanced Asset Performance
By proactively maintaining equipment and optimizing asset utilization, CMMS software prolongs asset lifespan and maximizes return on investment. Businesses can gauge asset performance improvements by monitoring unplanned equipment downtime, failure rates, and mean time between failures (MTBF).
The Bottom Line
The bottom line in determining the optimal preventive maintenance schedule is balancing two critical factors: the risk of equipment failure and maintenance cost. Maintenance managers can identify the likelihood and consequences of potential failures by conducting a thorough risk assessment and considering factors such as asset criticality, historical failure data, and operational impact. These factors can then be weighed against the cost-effectiveness of preventive maintenance tasks, including labor, materials, and downtime, enabling maintenance managers to optimize maintenance intervals and resource allocation. Ultimately, an optimal preventive maintenance schedule minimizes the probability of equipment failures while maximizing the return on investment in maintenance activities, enhancing asset reliability, reducing downtime, and driving overall operational efficiency.
To-Do Checklist: How to Set Up an Optimal CMMS Preventive Maintenance Program
1. Define Maintenance Objectives
Clearly outline the goals and objectives of your preventive maintenance program (reducing downtime, lowering maintenance costs, extending asset life), and aligning them with overarching business objectives such as reducing costs, increasing profits, and improving customer satisfaction and retention.
2. Assess Current Maintenance Practices
Evaluate existing maintenance processes and workflows to identify inefficiencies, pain points, and areas for improvement. Understand the pros and cons of your current approach to guide the design of your CMMS preventive maintenance program.
3. Select the Right CMMS Software
Take the time to research and evaluate CMMS software solutions based on your specific requirements, budget, and future growth needs. Consider factors such as ease of use, scalability, integration capabilities, and support services before deciding on which CMMS software to use.
4. Gather Asset Information
Compile a comprehensive inventory of assets, equipment, and facilities requiring maintenance, including details like location, asset ID, model, manufacturer, BOM, and criticality. Centralize this information within the CMMS software for easy access and management.
5. Develop Maintenance Procedures
Define standardized maintenance procedures for each asset or equipment type, specifying inspection intervals, tasks, bill of materials, and required resources. Document best practices, safety protocols, and troubleshooting guidelines to ensure consistency and compliance.
6. Establish Maintenance Schedules
Create preventive maintenance schedules based on asset criticality, manufacturer recommendations, usage patterns, and historical maintenance data. Utilize the scheduling capabilities of the CMMS software to automate recurring tasks and notifications, and optimize resource allocation.
7. Integrate Predictive Maintenance Techniques
If needed and makes sense, incorporate predictive maintenance techniques such as condition monitoring, sensor data analysis, and predictive analytics into your preventive maintenance program. Leverage the predictive capabilities of CMMS software to anticipate equipment failures and schedule proactive maintenance activities.
8. Train Maintenance Teams
Provide comprehensive training to maintenance personnel on CMMS software, maintenance procedures, and safety protocols. Ensure that team members know how to navigate the software interface, generate work orders, and update maintenance activities. Lean on the CMMS software provider to help with training and support.
9. Monitor and Analyze Performance Metrics
Establish key performance indicators (KPIs) to measure the effectiveness of your preventive maintenance program, such as mean time between failures (MTBF), mean time to repair (MTTR), planned maintenance compliance, and equipment uptime. Utilize the reporting and analytics features of the CMMS software to track performance metrics and identify areas for improvement.
10. Iterate and Refine
Continuously monitor and evaluate the performance of your preventive maintenance program, soliciting feedback from maintenance teams and stakeholders. Identify any bottlenecks, challenges, and opportunities to improve. Leverage the flexibility and scalability of CMMS software to adapt to changing business needs and evolving maintenance requirements. Lean on your CMMS provider to offer advice, make recommendations, and keep your team current on software updates.
More and more businesses are discovering the power of CMMS software to streamline their maintenance operations and propel their businesses toward ongoing success. By following these guidelines and leveraging the capabilities of CMMS software, businesses can move towards an effective preventive maintenance program that optimizes asset performance, minimizes downtime, and drives cost savings. At the same time, businesses should be cautious about overdoing it when it comes to preventive maintenance. There are instances when preventive maintenance is just too much and, in the end, is counterproductive. Assets that are low-cost, not critical, and can be replaced easily are candidates for a run-to-fail approach. Check out this article to learn more about selecting the best maintenance management strategy. By effectively leveraging CMMS software, businesses can avoid over-maintenance and unleash the full potential of preventive maintenance as a strategic asset.
TABLE OF CONTENTS
Keep Reading
What happens when your most experienced maintenance leader is planning on retiring, taking 20 ...
7 Aug 2025
Today’s maintenance operations have become more complex and sophisticated. Gone are the days ...
5 Aug 2025
Modern warehouses are instrumental to maintaining the smooth operations of supply chains, ...
1 Aug 2025
Computerized Maintenance Management Systems (CMMS) have proven to be essential tools for ...
31 Jul 2025
Sometimes it feels as if technology is expanding at the speed of light. This is an ...
29 Jul 2025
Data Center downtime can have a huge negative impact ranging from damage to the data center’s ...
25 Jul 2025
Whenever a company introduces a new process or technology, it’s followed by a period of ...
24 Jul 2025
Obsolescence often comes unexpectedly, mainly because little attention is given to the ...
22 Jul 2025
Imagine a world where critical assets run smoothly without unexpected downtime, maintenance ...
18 Jul 2025
Imagine you're going through a compliance audit, and the inspector asks for maintenance ...
10 Jul 2025
Maintenance managers understand that disasters are unpredictable and can have a massive ...
4 Jul 2025
Asset lifespan is a key concern for executives and maintenance and facility management teams. ...
3 Jul 2025
Your company recently invested funds and time for new CMMS software, and six months later, it ...
1 Jul 2025
As Computerized Maintenance Management Systems (CMMS) become more connected and cloud-based, ...
1 Jul 2025
Edge computing is an innovative technology that enables data to be processed at the source, ...
24 Jun 2025
Facility management has undergone a significant transformation in recent times. Take, for ...
20 Jun 2025
A facility maintenance plan is at the core of a facility’s operations. This organized ...
19 Jun 2025
In the early days, preventive maintenance could be done effectively with a trained eye and a ...
17 Jun 2025
Sticky notes fall off, whiteboard grids get wiped, and spreadsheets never beep when a ...
13 Jun 2025
Handing a slice of your maintenance workload to a contractor is less about “giving up ...
12 Jun 2025