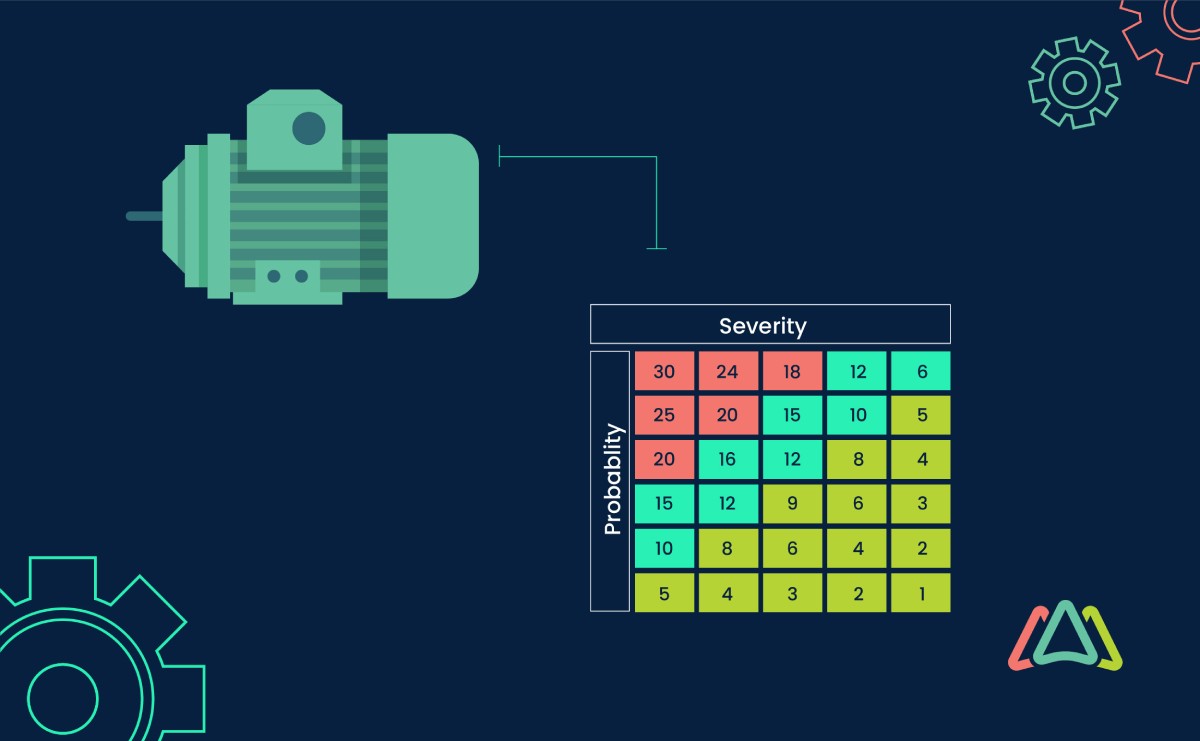
Prioritizing Performance with Equipment Criticality Assessment Matrix
Equipment criticality assessment serves as a fundamental component of effective maintenance management. Conducting an equipment criticality assessment helps organizations identify and focus on the most critical equipment that has a significant impact on production, safety, and business operations for maintenance planning..
This prioritization helps in strategic planning and decision-making, allowing maintenance teams to allocate resources and schedule maintenance activities based on the criticality of equipment. In conjunction with an equipment maintenance software, it enables organizations to proactively address potential failures, reduce downtime, and improve the reliability and performance for their most important assets.
What is an Equipment Criticality Assessment?
Equipment criticality refers to the level of importance and impact that a particular piece of equipment has on the overall operations and performance of an organization. It signifies the degree to which the failure or malfunction of a specific asset can disrupt production, compromise safety, or result in financial losses. The criticality of equipment serves as a key indicator for maintenance management, enabling organizations to prioritize their maintenance efforts and allocate resources effectively.
The significance of equipment criticality lies in its ability to guide decision-making processes in maintenance management. By assessing the criticality of equipment, organizations can identify the assets that require immediate attention and focus their resources on minimizing potential risks and optimizing maintenance activities. This approach helps reduce downtime, enhance reliability, and improve operational efficiency.
Factors Considered in Equipment Criticality Assessment
When conducting an equipment criticality assessment, several factors are taken into account that help evaluate the criticality level of each piece of equipment within the organization. Some of the key factors considered in equipment criticality assessment are as follows:
- Equipment Functionality and Process Impact: This factor evaluates how vital the equipment is for the smooth functioning of critical processes and operations and the extent to which equipment failure can impact overall productivity and output.
- Safety and Environmental Impact: Equipment criticality is higher if failure poses significant safety risks or environmental concerns.
- Repair and Replacement Costs: Higher repair or replacement costs can indicate higher criticality.
- Availability of Spare Parts: If critical equipment relies on scarce or hard-to-find spare parts, its criticality level increases.
- Downtime Impact on Production: Equipment criticality is higher when failure leads to extended periods of downtime, resulting in significant losses.
- Regulatory Compliance Requirements: Non-compliance can have legal and reputational consequences, raising the criticality level.
- Age and Condition of Equipment: Older equipment or assets in poor condition may have a higher probability of failure, thus increasing their criticality level.
By taking these factors into account during the equipment criticality assessment, organizations obtain a holistic understanding of the criticality levels of their assets and are able to make more informed decisions regarding maintenance strategies, resource allocation, and risk mitigation.
What is the Equipment Criticality Assessment Matrix?
An Equipment Criticality Assessment Matrix is a structured tool used to evaluate and prioritize the criticality of equipment within an organization. It provides a systematic approach to assess the importance and impact of equipment failures on operational efficiency, safety, and production. The matrix consists of a grid or table that categorizes equipment based on their criticality ranking, allowing maintenance teams to focus their efforts and resources on the most critical assets.
The matrix incorporates various factors and criteria to assign a numerical or categorical ranking to each piece of equipment. These rankings enable organizations to classify and prioritize equipment based on their criticality levels, facilitating more effective maintenance planning and decision-making.
Steps to Create an Equipment Criticality Assessment Matrix
Step 1: Create an Equipment List
The first step in creating an Equipment Criticality Assessment Matrix is to identify and list all the equipment within the organization that will be assessed. This includes all relevant assets, machinery, systems, and components that play a significant role in the operations and production processes.
A comprehensive equipment inventory should be compiled, including details such as equipment names, identification numbers, location, and any other relevant information that helps in accurate identification and tracking of each item. Many organizations use a CMMS to tag assets with QR codes and store asset information.
Step 2: Define Criticality Ranking Criteria
In this step, criticality ranking criteria are established to evaluate and assess the equipment. It is essential to carefully select and define the criteria based on the organization's specific needs and objectives. The ranking criteria should align with the factors that determine the criticality of equipment in the organization's context.
As discussed above, common examples of criticality ranking criteria include:
- Functionality Impact: The impact of equipment failure on the overall functioning of the processes or operations.
- Safety Risks: The potential safety risks to personnel, the environment, or assets in case of equipment failure.
- Repair Costs: The financial implications associated with repairing or replacing the equipment.
- Downtime Impact: The extent to which equipment failure causes downtime and production losses.
- Regulatory Compliance: The equipment's compliance requirements with applicable regulations and standards.
- Spare Parts Availability: The availability and lead time of spare parts required for maintenance or repairs.
- Age and Condition: The age, condition, and maintenance history of the equipment.
Step 3: Determine Severity Levels
Define Severity Levels
Severity levels represent the degree of impact or consequences associated with the failure of equipment. It is important to define clear and meaningful severity levels that reflect the significance of each ranking criterion. Severity levels can be qualitative (e.g., low, medium, high) or quantitative (e.g., numerical values or percentages).
The definition of severity levels should align with the specific factors being assessed. For example, if safety risks are a ranking criterion, severity levels may range from "negligible" to "catastrophic" based on the potential harm or hazards involved.
Assign Severity Levels to Equipment
Once severity levels are defined, each asset in the inventory should be assigned a severity level for each ranking criterion. This assessment can be based on expert judgment, historical data analysis, or a combination of both. Care should be taken to ensure consistency and accuracy in assigning severity levels to equipment.
Step 4: Establish Probability Levels
Define Probability Levels
Probability levels assess the likelihood of equipment failure occurring within a specific timeframe. These levels quantify the probability of failure based on various factors, such as historical failure data, equipment condition, maintenance practices, and expert opinion.
Probability levels can be qualitative (e.g., low, medium, high) or quantitative (e.g., percentage or values). The selection of probability levels should align with the organization's ability to assess and estimate the probability of equipment failures effectively.
Assess Probability for Each Equipment
For each piece of equipment, an assessment of the probability of failure should be conducted based on the defined probability levels. This assessment involves analyzing historical failure data, conducting a reliability analysis, considering maintenance records, and consulting subject matter experts. The goal is to assign a probability level to each asset based on its likelihood of failure.
Step 5: Create the Risk Matrix
Set Up the Matrix
The final step is to create the Risk Matrix, which visually represents the Equipment Criticality Assessment. The matrix is typically a two-dimensional grid or table, with severity levels plotted on one axis and probability levels on the other axis. The matrix cells represent the intersections of severity and probability levels.
Plot Equipment on the Matrix
Each piece of equipment is plotted on the Risk Matrix based on its assigned severity and probability levels. The intersection of the severity and probability levels determines the criticality ranking of the equipment. This ranking helps prioritize maintenance activities, resource allocation, and decision-making.
Equipment in cells with high severity and high probability represents high criticality, requiring immediate attention and appropriate maintenance strategies. Conversely, equipment in cells with low severity and low probability may have lower criticality and require less immediate attention or resources.
By following these steps, organizations can develop a comprehensive Equipment Criticality Assessment Matrix. This matrix serves as a valuable tool for prioritizing maintenance efforts, allocating resources effectively, and mitigating risks associated with equipment failures.
5 Benefits of Combining an Equipment Criticality Assessment Matrix with a CMMS
1. Better Prioritization of Maintenance Activities
One of the benefits of the Equipment Criticality Assessment Matrix is its ability to prioritize maintenance activities. By utilizing the criticality rankings assigned to equipment, organizations can focus their efforts on addressing the most critical assets first. This prioritization ensures that resources, such as labor and time, are allocated effectively to minimize the risk of equipment failure and its associated consequences.
Maintenance activities can be scheduled and executed based on the criticality rankings. High criticality equipment, located in cells of the matrix with high severity and probability levels, requires immediate attention and proactive maintenance measures. On the other hand, equipment with lower criticality can be addressed accordingly, allowing for a more efficient and targeted approach to maintenance.
A Computerized Maintenance Management System (CMMS) can greatly enhance the effectiveness of the matrix. A CMMS software / preventive maintenance software helps streamline and automate maintenance management processes. It can integrate with the Equipment Criticality Assessment Matrix, allowing maintenance teams to access and prioritize work orders based on criticality rankings. This integration ensures that maintenance activities are executed in a timely manner, reducing the likelihood of equipment failures and maximizing equipment uptime.
2. Resource Allocation and Planning
The Equipment Criticality Assessment Matrix aids in optimizing resource allocation and planning. With the matrix's guidance, organizations can allocate resources, including labor, spare parts, and budget, in a more effective manner. The most critical equipment, which poses higher risks and impacts, receives priority when allocating resources.
Maintenance teams can utilize the matrix to determine the level of resources required for each asset based on their criticality rankings. For example, critical equipment may necessitate a dedicated team or specialized expertise, whereas less critical equipment may require fewer resources. This approach ensures that resources are allocated efficiently, minimizing unnecessary costs and maximizing maintenance outcomes.
A work order software further supports resource allocation and planning by providing visibility into resource availability, work order schedules, and the maintenance backlog. Maintenance managers can use the CMMS to assign appropriate resources based on the criticality rankings and ensure that the necessary personnel, tools, and materials are available when needed. This integration between the matrix and CMMS streamlines resource management, minimizes downtime, and optimizes maintenance efforts.
3. Decision-Making for Maintenance Strategies
The Equipment Criticality Assessment Matrix plays an important role in helping select the maintenance management strategy. Based on the criticality rankings, organizations can determine the appropriate maintenance approach whether preventive, predictive, or reactive for their equipment.
For equipment items that are high on criticality , a preventive maintenance strategy may be implemented to proactively address potential failures and minimize risks. This involves conducting regular inspections, performing preventive maintenance tasks, and adhering to a predefined maintenance schedule.
Moderately critical equipment may benefit from a predictive maintenance strategy. By utilizing condition monitoring techniques, organizations can monitor equipment health and performance, detecting early signs of potential failures and addressing them before they cause significant disruptions.
For equipment with lower criticality, a reactive maintenance strategy may be appropriate. This approach involves addressing issues as they occur, primarily relying on corrective maintenance activities.
A CMMS enhances decision-making by providing historical maintenance data, performance indicators, and real-time equipment condition monitoring. Maintenance managers can analyze this information in conjunction with the criticality rankings to make data-driven decisions about maintenance strategies. A CMMS enables the implementation and execution of these strategies, ensuring that maintenance activities are aligned with the criticality rankings.
4. Set Up Preventive Maintenance Plans
The Equipment Criticality Assessment Matrix facilitates the establishment of preventive maintenance plans.
By using the criticality rankings provided by the matrix, organizations can prioritize the development of preventive maintenance schedules. Equipment with higher criticality levels, located in cells with high severity and probability, should receive more frequent and comprehensive preventive maintenance.
The matrix guides maintenance teams in determining the frequency of preventive maintenance activities for each equipment item. This ensures that critical equipment is regularly inspected, maintained, and monitored to prevent failures and optimize performance.
A CMMS simplifies the setup and management of preventive maintenance schedules by allowing organizations to create maintenance plans based on criticality rankings, define task frequencies, and set up automated reminders and work orders. The CMMS also tracks and records maintenance activities, enabling maintenance teams to adhere to the established schedules and ensure that preventive maintenance tasks are completed on time. By integrating the matrix with the CMMS, organizations can optimize preventive maintenance efforts, extend equipment lifespan, and minimize unplanned downtime.
5. Identification of Critical Spare Parts Inventory
The matrix helps organizations determine which spare parts are crucial to have readily available for the most critical equipment.
Based on the criticality rankings, equipment located in cells with high severity and probability levels necessitates the availability of critical spare parts. Organizations can analyze the maintenance history, failure patterns, and lead times for spare parts to identify the critical parts and materials that should be stocked.
By aligning spare parts inventory with criticality rankings, organizations can ensure faster response times in case of equipment failures, reduce downtime, and improve overall maintenance efficiency.
A CMMS assists in managing the spare parts inventory. It can track inventory levels, provide visibility into stock availability, and generate automated reorder alerts. Maintenance managers can link the criticality rankings to the CMMS, ensuring that the most critical equipment is associated with the necessary spare parts in the system. This integration enables organizations to maintain adequate levels of critical spare parts, reduce lead times, and improve overall equipment availability.
The integration between the matrix and CMMS enhances maintenance management processes, streamlines workflows, and maximizes the reliability and performance of equipment.
Challenges and Considerations
Subjectivity and Bias in Assessments
One of the challenges in using an Equipment Criticality Assessment Matrix is the potential for subjectivity and bias in the assessment process. Different individuals or teams may have varying perspectives on the criticality of equipment, leading to inconsistent rankings. To mitigate this challenge, it is important to establish clear guidelines and criteria for assessment and ensure that assessments are conducted by knowledgeable and experienced personnel. Regular training and calibration sessions can help reduce subjectivity and ensure consistency in the assessment process.
Review and Revision of the Matrix
The Equipment Criticality Assessment Matrix should be periodically reviewed and revised to ensure its effectiveness over time. Equipment criticality rankings may change as the organization evolves, new equipment is introduced, or maintenance practices improve. Organizations should have a structured review process in place to assess the relevance and accuracy of the matrix. Regular feedback from maintenance teams, data analysis, and lessons learned from equipment failures provide great information to be used for revisions and improvements to the matrix.
Integration with Other Maintenance Management Systems
Integrating the Equipment Criticality Assessment Matrix with other maintenance management systems can present challenges. Organizations may already have existing systems for asset management, work order management, and preventive maintenance scheduling. Ensuring seamless integration between these systems and the matrix requires careful planning and coordination. Data transfer and synchronization should be automated to reduce manual efforts and ensure data consistency across systems. It is essential to select compatible software solutions or develop custom integrations to maximize the efficiency and effectiveness of the matrix within the broader maintenance management framework.
Train Maintenance Personnel on Matrix Usage
To get the most out of the Equipment Criticality Assessment Matrix, it is important to train maintenance personnel on its proper usage. Training should focus on understanding the matrix components, conducting assessments, interpreting results, and utilizing the matrix to prioritize maintenance activities. By ensuring that maintenance teams are knowledgeable and skilled in using the matrix, organizations will get better results from this initiative.
TABLE OF CONTENTS
Keep Reading
What happens when your most experienced maintenance leader is planning on retiring, taking 20 ...
7 Aug 2025
Today’s maintenance operations have become more complex and sophisticated. Gone are the days ...
5 Aug 2025
Modern warehouses are instrumental to maintaining the smooth operations of supply chains, ...
1 Aug 2025
Computerized Maintenance Management Systems (CMMS) have proven to be essential tools for ...
31 Jul 2025
Sometimes it feels as if technology is expanding at the speed of light. This is an ...
29 Jul 2025
Data Center downtime can have a huge negative impact ranging from damage to the data center’s ...
25 Jul 2025
Whenever a company introduces a new process or technology, it’s followed by a period of ...
24 Jul 2025
Obsolescence often comes unexpectedly, mainly because little attention is given to the ...
22 Jul 2025
Imagine a world where critical assets run smoothly without unexpected downtime, maintenance ...
18 Jul 2025
Imagine you're going through a compliance audit, and the inspector asks for maintenance ...
10 Jul 2025
Maintenance managers understand that disasters are unpredictable and can have a massive ...
4 Jul 2025
Asset lifespan is a key concern for executives and maintenance and facility management teams. ...
3 Jul 2025
Your company recently invested funds and time for new CMMS software, and six months later, it ...
1 Jul 2025
As Computerized Maintenance Management Systems (CMMS) become more connected and cloud-based, ...
1 Jul 2025
Edge computing is an innovative technology that enables data to be processed at the source, ...
24 Jun 2025
Facility management has undergone a significant transformation in recent times. Take, for ...
20 Jun 2025
A facility maintenance plan is at the core of a facility’s operations. This organized ...
19 Jun 2025
In the early days, preventive maintenance could be done effectively with a trained eye and a ...
17 Jun 2025
Sticky notes fall off, whiteboard grids get wiped, and spreadsheets never beep when a ...
13 Jun 2025
Handing a slice of your maintenance workload to a contractor is less about “giving up ...
12 Jun 2025