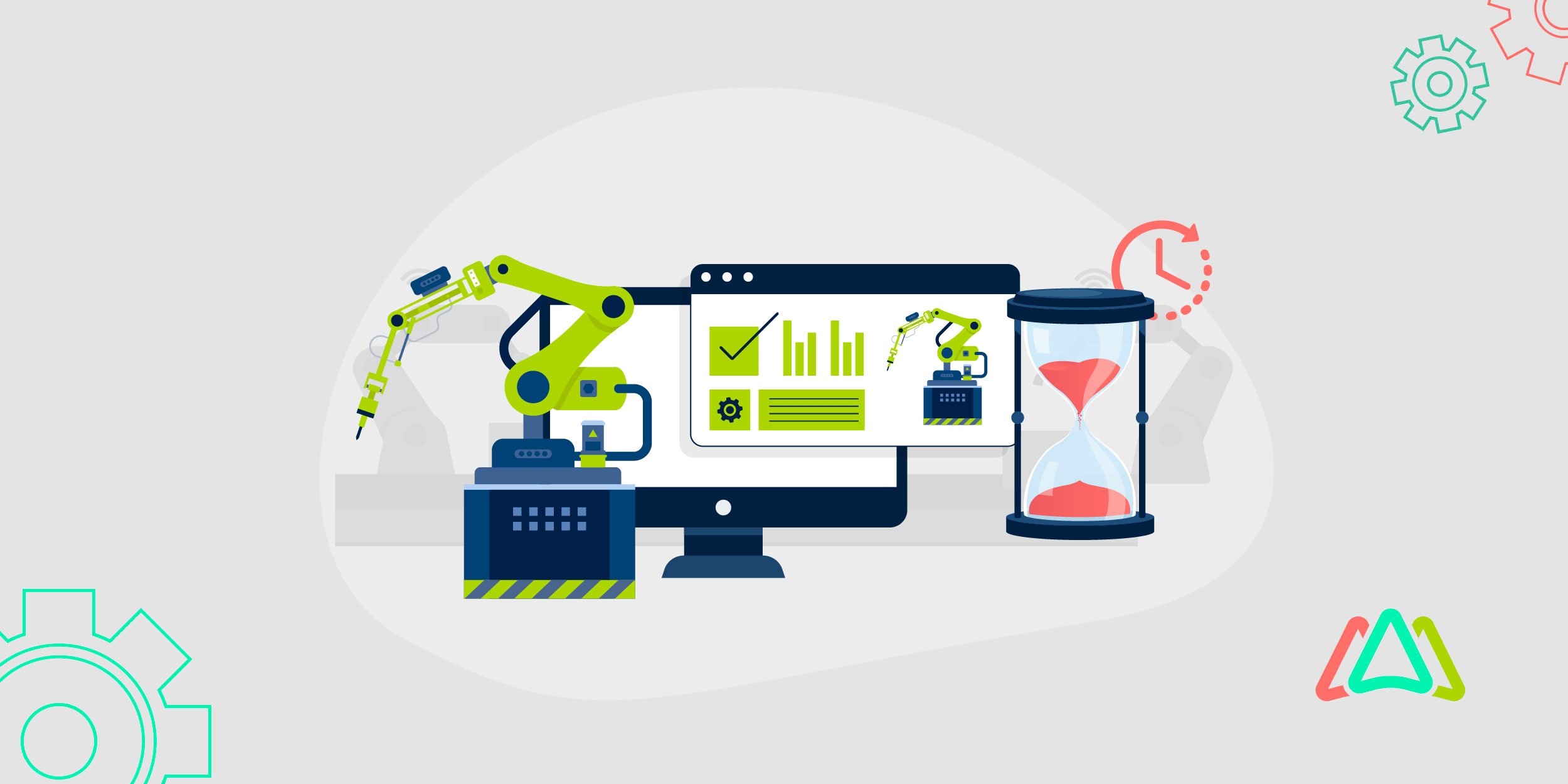
Maximizing Asset Lifespan with CMMS
Asset lifespan is a key concern for executives and maintenance and facility management teams. The longer assets remain functional and efficient, the lower the cost of ownership and the higher the return on investment. Organizations are constantly under pressure to do more with less. That means getting the most out of every machine, system, and piece of equipment in operation.
A CMMS (Computerized Maintenance Management System) helps maintenance teams shift from always putting out fires to actually staying ahead of problems. It makes it easier to keep track of equipment, plan work before something breaks, and manage assets through every stage of their life. The result? Fewer unexpected breakdowns and costs, and better performance over the long haul.
This article explores assets and their lifecycle, common reasons why assets deteriorate, demonstrates how a CMMS software resolves these issues, and provides helpful tips on how to maximize the benefits of your system.
Understanding Assets and Their Lifecycle
An asset is any physical equipment, system, or infrastructure that supports core business functions. This includes machinery, vehicles, HVAC units, production lines, buildings, and anything that requires upkeep to remain operational. Assets are investments, and their ability to deliver value over time depends heavily on how well they are managed and maintained.
Asset Lifecycle
Assets follow a predictable journey from the moment they are acquired to when they are eventually retired. Below are the key stages:
Acquisition
This is the initial stage where the asset is purchased or deployed in response to operational needs. It involves planning, budgeting, and sourcing.
Commissioning
The commissioning stage, which follows acquisition, makes sure the asset is fully operational and safe to use by installing, testing, and preparing it for use.
Utilization
The asset delivers value through production or service when it moves into the normal use phase. To optimize performance during this stage, proper usage procedures are crucial.
Maintenance
In order to maintain dependability, effectiveness, and safety over time, the asset needs preventive, predictive, or corrective maintenance.
Disposal
The asset is taken out of active service after its lifecycle is over. Its performance and condition will determine whether it is replaced, recycled, or retired.
Asset Management and Maintenance
Although they have diverse functions, asset management and asset maintenance are closely intertwined and often used interchangeably. The systematic process of purchasing, monitoring, and improving assets across their whole lifecycle to guarantee they provide the most value over time is known as asset management. Asset maintenance, on the other hand, concentrates on the practical tasks necessary to maintain those assets operating effectively, such as inspections, repairs, and servicing.
A CMMS bridges the gap between both functions by enabling organizations to align long-term asset planning with daily maintenance execution.
Why Asset Lifespan Matters
Since every asset has a finite lifecycle, how it's maintained directly impacts its lifespan and the value it delivers. This makes asset lifespan a critical metric for operational and financial performance.
The Financial Impact of Asset Longevity
Extending the lifespan of assets reduces the need for frequent replacements, saving capital costs over time. For example, maintaining an operational machine to last 12 years instead of 8 could save an organization tens of thousands in avoided reinvestment and downtime.
Operational Risks of Premature Asset Failure
Unexpected failures cause safety risks, lower productivity, and disrupt operations. A single production line failure might result in downtime, which can cost thousands of dollars per hour in lost productivity and inefficient labor.
Sustainability Benefits of Longer Asset Life
Prolonging asset lifespan supports sustainability goals by reducing waste, conserving raw materials, and lowering the environmental impact of manufacturing new equipment.
Focusing on asset longevity is not just smart maintenance; it’s a strategic advantage on the financial, operational, and environmental fronts.
Hidden Factors Shortening Asset Life
Even the most valuable assets can fail early when maintenance practices fall short. Here are the most common causes of reduced asset lifespan and how a CMMS helps eliminate them:
Poor Documentation
Poor recordkeeping causes many businesses to lose track of maintenance work. This results in recurrent failures and ignored warnings. Every service, repair, and inspection is recorded by a CMMS, which offers centralized asset tracking. Maintenance and facility managers may make well-informed decisions that preserve asset longevity when they have access to complete records.
Missed Servicing
When maintenance is scheduled by hand, it’s easy for tasks to slip through the cracks or happen too late. That’s when small issues turn into major breakdowns. A CMMS takes the guesswork out by automatically scheduling preventive maintenance based on time, usage, or runtime data. This keeps servicing consistent, reduces wear, and helps equipment run the way it’s meant to, without unexpected downtime.
Lack of Accountability
Without clear responsibility, maintenance tasks may be delayed or poorly executed. A CMMS maintains detailed logs and audit trails of who performed what task and when. This improves accountability, encourages quality work, and helps identify patterns behind recurring issues.
Overuse or Misuse
Excessive use or improper operation can shorten asset life. Integrating with sensors or manual input, a CMMS delivers real-time usage data and alerts when thresholds are exceeded. This allows teams to correct misuse early and adjust workloads to avoid excessive strain on critical equipment.
The Benefits of Extending Asset Lifespan
Keeping equipment running longer isn’t just good for operations; it’s one of the smartest ways to cut costs and get more out of every investment. With the right CMMS in place, teams can take control of asset care and make each machine last as long as it should. Here's how it works in practice:
Reduced Maintenance and Replacement Costs
When equipment is well taken care of, it lasts longer, and that means fewer big repairs and a lot less money spent on replacements. With a CMMS in place, maintenance gets done on time, which helps prevent unexpected breakdowns and keeps machines running as they should. That extra attention adds up to real savings over time.
Sustained Asset Performance and Output
Efficient assets continue to perform at optimal levels throughout their lifecycle. This consistent uptime means stable production, fewer disruptions, and better use of resources. CMMS tools help ensure performance doesn’t degrade due to neglect or delayed servicing.
Improved Total Cost of Ownership
The Total Cost of Ownership (TCO) includes the initial purchase, maintenance, downtime, and eventual replacement. CMMS reduces all downstream costs by extending asset life and minimizing inefficiencies, improving the overall value of each investment.
Long-Term Return on Investment (ROI)
When maintenance costs go down and output stays consistent, ROI improves. CMMS helps maximize this by aligning maintenance decisions with performance goals, giving organizations more value from every asset over a longer period.
How CMMS Maximizes Asset Lifespan: Key Features and Impact
Preventive Maintenance Scheduling
With a CMMS, preventive maintenance is a top priority. It automatically lines up service tasks based on time, usage, or specific conditions, so equipment gets the care it needs before problems show up. This kind of consistency helps reduce wear, avoid sudden failures, and keep machines running longer. Over time, it’s these small, timely check-ins that protect your investment and keep costs under control.
Real-Time Asset Monitoring
Integrated with IoT sensors, CMMS platforms monitor real-time parameters like temperature, vibration, or pressure. When these indicators deviate from normal ranges, automated alerts allow teams to act immediately. This condition-based monitoring approach helps prevent small problems from turning into asset-threatening failures.
Faster, Smarter Work Order Management
A CMMS digitizes and automates the work order process. Teams receive instant alerts, access checklists, and close tasks in real time, whether in the office or the field. Faster response means issues are resolved before they escalate, preserving the asset’s integrity and performance.
Complete Asset History and Documentation
Every maintenance activity, inspection, or repair is logged into the system. This historical data enables smarter decision-making, including whether to repair or replace an asset. It also supports root cause analysis, trend detection, and long-term planning to keep assets operating longer with fewer disruptions.
Predictive Maintenance and Analytics
Today’s CMMS tools go beyond just keeping maintenance records; they actually help you see what’s coming. By looking at past performance and repair history, they can pick up on patterns that point to future problems. That gives your team a chance to step in early and fix small issues before they grow into something serious.
Mobile Access for Field Efficiency
When your CMMS works on mobile, your team isn’t stuck at a desk. Technicians can pull up asset info, get work orders, and log updates right from the field. It saves time, cuts down on miscommunication, and keeps records accurate.
Reporting and KPI Dashboards
Built-in analytics and customizable reports allow teams to track key performance indicators (KPIs) like mean time between failures (MTBF) or maintenance costs per asset. These insights support continuous improvement and help refine strategies that maximize asset lifespan.
Key Metrics to Track for Asset Longevity
If you want your assets to last longer, it’s not just about doing the work; it’s about tracking the right numbers. A CMMS can help you monitor key metrics that show how well your maintenance efforts are working. For example, MTBF (Mean Time Between Failures) tells you how reliable your equipment is, while MTTR (Mean Time to Repair) shows how fast you’re bouncing back when something goes wrong.
Keeping your Planned Maintenance Percentage above 60% is a good sign that you’re staying ahead instead of always reacting. You’ll also want to keep an eye on maintenance costs per unit of output, how often equipment is used, and how much downtime it’s experiencing. If your maintenance backlog starts to pile up, that’s a red flag.
By regularly checking these numbers, you can make smarter decisions, catch issues early, and help your assets go the distance.
Conclusion: CMMS for Asset Longevity
Getting the most out of your equipment isn’t about quick fixes; it’s about long-term care. When assets are well maintained, they tend to last longer, run better, and cost less to keep going. Fewer breakdowns mean fewer interruptions and real savings over time.
A good CMMS isn’t just another software tool; it’s a smart investment in how your team works. It brings order, visibility, and consistency to your maintenance process. Instead of reacting to problems after they happen, you can plan, track performance, and make decisions that actually extend the life of your assets.
What separates constant equipment trouble from smooth, reliable operations is how you handle maintenance. Waiting for things to break just adds stress and cost. Instead, put a plan in place that keeps your assets running strong over time, protecting not just your machines but also your budget and peace of mind. The right CMMS makes that easier, giving your team the tools to stay ahead and stay in control.
By acting as the bridge between maintenance strategy, people, and performance data, CMMS becomes essential to long-term asset lifecycle management."
TABLE OF CONTENTS
Keep Reading
What happens when your most experienced maintenance leader is planning on retiring, taking 20 ...
7 Aug 2025
Today’s maintenance operations have become more complex and sophisticated. Gone are the days ...
5 Aug 2025
Modern warehouses are instrumental to maintaining the smooth operations of supply chains, ...
1 Aug 2025
Computerized Maintenance Management Systems (CMMS) have proven to be essential tools for ...
31 Jul 2025
Sometimes it feels as if technology is expanding at the speed of light. This is an ...
29 Jul 2025
Data Center downtime can have a huge negative impact ranging from damage to the data center’s ...
25 Jul 2025
Whenever a company introduces a new process or technology, it’s followed by a period of ...
24 Jul 2025
Obsolescence often comes unexpectedly, mainly because little attention is given to the ...
22 Jul 2025
Imagine a world where critical assets run smoothly without unexpected downtime, maintenance ...
18 Jul 2025
Imagine you're going through a compliance audit, and the inspector asks for maintenance ...
10 Jul 2025
Maintenance managers understand that disasters are unpredictable and can have a massive ...
4 Jul 2025
Your company recently invested funds and time for new CMMS software, and six months later, it ...
1 Jul 2025
As Computerized Maintenance Management Systems (CMMS) become more connected and cloud-based, ...
1 Jul 2025
Edge computing is an innovative technology that enables data to be processed at the source, ...
24 Jun 2025
Facility management has undergone a significant transformation in recent times. Take, for ...
20 Jun 2025
A facility maintenance plan is at the core of a facility’s operations. This organized ...
19 Jun 2025
In the early days, preventive maintenance could be done effectively with a trained eye and a ...
17 Jun 2025
Sticky notes fall off, whiteboard grids get wiped, and spreadsheets never beep when a ...
13 Jun 2025
Handing a slice of your maintenance workload to a contractor is less about “giving up ...
12 Jun 2025
Downtime in enterprise environments doesn’t just mean a stop in operations; it means lost ...
10 Jun 2025