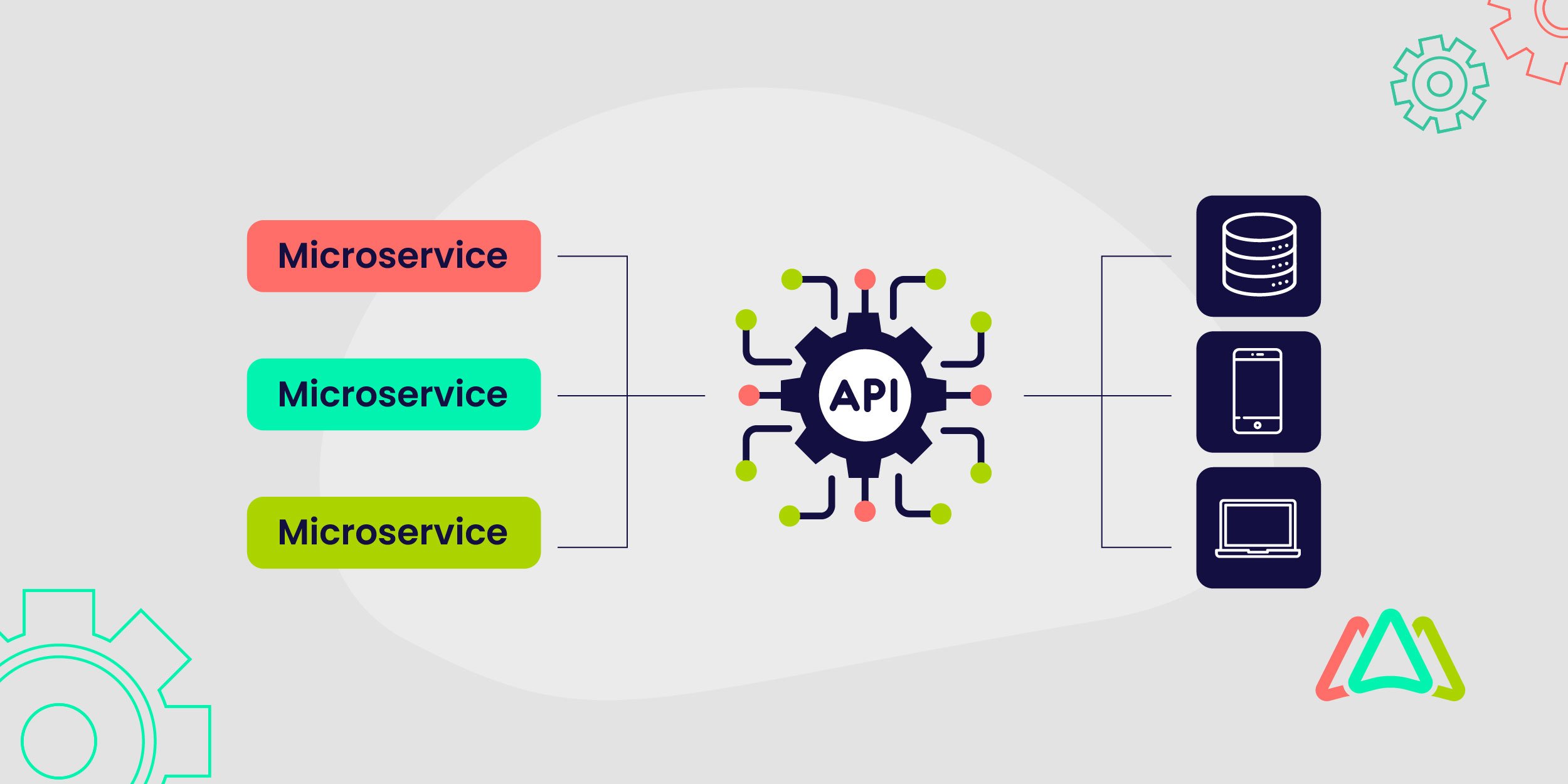
Microservice CMMS Platforms for Flexible SMB Operations
Imagine a world where critical assets run smoothly without unexpected downtime, maintenance tasks are seamlessly managed, and operational costs are consistently optimized, all without the burden of complex, monolithic software. This scenario is no longer outside the realm of possibility for small and medium-sized businesses (SMBs). It is a real opportunity that comes from the shift to microservice-based CMMS.
In today's fast-paced world, survival is contingent upon agility and efficacy. In many cases, conventional CMMS solutions fail to meet the need. Nevertheless, a novel approach enables small and medium-sized enterprises (SMBs) to modify maintenance procedures. They can transition from responding to issues to establishing a proactive and scalable market advantage. The paradigm in question is microservices.
This article explores why microservices matter for SMBs. They help businesses overcome operational bottlenecks. By using modular agility, companies gain real-time performance, leading to a smarter, more scalable approach to maintenance.
What are Microservices, and How are They Reshaping Business Software?
Microservices describe the way in which applications (or software) are designed. It divides complex systems into smaller services that can be deployed independently. Each "micro" service focuses on a business task, such as work order management or asset tracking. It talks to other services through APIs. This modular design enables independent development, deployment, and easier maintenance of individual components.
This approach is very different from traditional ‘monolithic architecture’, where applications are built as a single, tightly coupled unit. While seemingly simpler at first, monolithic systems quickly become fragile and hard to scale as they grow. A failure in one part can influence the entire system, and small changes can also lead to significant risks throughout the codebase.
Microservices solve these problems by allowing fault isolation, quicker updates, and real-time data sharing. Businesses can deploy or scale parts without changing the whole system. This flexibility works well in fast-paced SMB settings, where every minute and dollar matter.
The global microservices architecture market shows strong growth. It was valued at $3.7 billion in 2023 and is expected to hit $11.8 billion by 2032, with a Compound Annual Growth Rate (CAGR) of 13.75%. A focus on customer requirements and digital transformation is driving this growth. Companies endeavour to expedite application delivery, which is revolutionizing enterprise IT. As a result of transitioning to microservices, over 67% of organizations report improvement in their scalability.
For SMBs, using a microservice CMMS is more than a technical choice. It's a wise investment. Using software applications built with microservices helps SMBs stand out in the market and adapt quickly, allowing them to remain flexible and responsive in a competitive environment. Companies that implement software applications that are built on monolithic architecture instead of modular architecture that use microservices may fall behind rivals using these technologies.
The SMB Maintenance Dilemma: Why Traditional CMMS Platforms Fall Short
The microservice approach looks good, but we need to understand why traditional CMMS, often built on older monolithic systems, struggles to meet the changing needs of SMBs. These systems have evolved from mainframe-based setups in the 1960s to modern cloud platforms. Yet, they still face significant operational challenges:
- Inefficiency in Data Entry: Many SMBs remain stuck in manual processes. About 58% of CMMS users still use spreadsheets. Also, 28% don't use any maintenance management software. Manual methods waste time, increase errors, and distract staff from key maintenance tasks.
- Lack of Real-Time Updates: Manual or siloed systems inherently prevent real-time data synchronization. Changes in one record don't show up immediately, making it hard to make quick, informed decisions in fast-paced maintenance settings.
Poor Asset Lifecycle Tracking: When systems are messy, tracking equipment from buying to retirement is tough, which hinders proper maintenance planning and inflates operational costs. - Complexity and Usability Issues: Many traditional CMMS platforms seem too complex and challenging to use, leading to frustration and low user adoption.
- High Implementation Costs: Standard CMMS platforms can have high initial costs, including software, hardware, training, and integration. Such expenses can be a barrier for SMBs with tight budgets.
How Microservice CMMS Solves SMB Pain Points
Microservice platforms directly address the key flaws in traditional CMMS. Their design provides strong and practical solutions. Microservice CMMS platforms are flexible, cost-effective, and reliable for managing maintenance. They use their modularity to tackle the issues mentioned above directly.
- Phased Implementation: Microservices enable SMBs to adopt a "start small and smart" approach. Companies can start small with core features like work order management or asset management software, then scale. Then, they can gradually expand their implementation as needed.
- Resource Optimization: The modular design updates specific parts without affecting the system, which cuts down the time and cost for changes and redeployments. As a result, it improves resource distribution and saves money in the long run.
- API-First Integration: Microservices are designed for seamless communication via clear APIs, which makes connecting with current internal systems and third-party platforms like ERP, HR, and IoT easy. This helps break down data silos, reduce manual data entry, and reduce errors.
- Faster Feature Delivery: Each microservice works independently, letting teams create, test, and launch new features. This decoupled approach speeds up development cycles and cuts the time to market for new features and updates by up to 20%.
Table 1: CMMS Implementation Challenges for SMBs and Microservice Solutions
Challenge |
Description |
Microservice-Based CMMS Solution |
Resistance to Change |
Employee reluctance or fear of new technologies |
Phased implementation with clear internal communication |
Lack of Clear Goals/Strategy |
Undefined objectives leading to inefficiency |
Modular focus on specific business capabilities, incremental value realization |
Insufficient Training and Support |
Overlooked comprehensive training, low user adoption |
Intuitive design, vendor support for onboarding, and mobile accessibility |
High Implementation Costs |
Significant upfront investment for software, hardware, and training |
Cloud-based subscription models, pay-as-you-grow scalability |
Monolith vs. Microservice for SMB Agility
SMBs have a choice between monolithic and microservice architecture for a CMMS. This choice directly impacts their flexibility, growth potential, and long-term efficiency. Monolithic systems are simple to use. However, microservices provide the flexibility and resilience that modern, dynamic businesses need. This key architectural choice significantly affects an SMB's agility, scalability, and long-term efficiency. You can see this in the comparison table below.
Table 2: Monolithic vs. Microservice CMMS for SMB Agility
Feature |
Monolithic CMMS for SMBs |
Microservice CMMS for SMBs |
Impact on SMB Agility |
Initial Setup |
Simpler for very small, unchanging projects. |
Potentially more complex initially due to the distributed nature, but offset by phased implementation. |
Initial complexity is managed through modularity, leading to faster time-to-value for specific functions. |
Deployment and Updates |
Complete application redeployment for any change; slow, risky updates. |
Independent deployment of individual services; faster, less risky updates. |
Enables rapid response to market changes and quick feature rollouts. |
Scalability |
Scales as a whole, often inefficiently, result in resource waste. |
Individual services scale independently and optimize resource use. |
Adapts efficiently to growth without over-provisioning, saving costs. |
Reliability/Fault Isolation |
Single point of failure; the entire app can go down. |
Failure is contained to a specific service; the rest of the app functions. |
Minimizes downtime, ensuring continuous operations even with localized issues. |
Technology Flexibility |
Limited by a single technology stack, vendor lock-in. |
Teams choose the best technology for each service, fostering innovation. |
Allows SMBs to integrate new advancements (AI, IoT) incrementally, future-proofing their system. |
Maintenance and Updates |
The entire application is complex and time-consuming. |
Easier, faster for individual services. |
Ensures continuous improvement with minimal disruption. |
Microservice CMMS Helps Small Businesses Succeed
Let's explore how a medium-sized metal smelting company benefited from a microservice architecture. They used a microservice-ready CMMS to improve their maintenance operations significantly.
Case Study: Streamlining Maintenance at a Metal Smelting Company
The Problem: Like many small businesses, this metal smelting company was stuck in a reactive and manual maintenance cycle. Their maintenance manager and a small team of ten workers were always "fighting fires," causing significant operational challenges.
- Lack of Visibility: Paperwork and scattered records made tracking asset status, work order progress, or maintenance history hard.
- Inefficient Inventory: Poor tracking of spare parts caused stockouts and overstocking, which raised repair times and costs.
- High Downtime: Equipment breakdowns often stop production, causing high costs and missed targets.
- Perceived CMMS Complexity: The company noted a common concern among SMBs. They found that traditional CMMS solutions were often too complex or time-consuming.
Microservice-Ready CMMS Solution: The business found a new CMMS system with an easy-to-use interface that is focused on customers. It had been built on a modular, microservice-ready design. Key aspects of the solution included:
- Risk-Free Trial: Users could create a free account to test the CMMS for two weeks across any device using a web browser, reducing perceived risk and helping them explore it directly.
- Accessibility and Easy Design: The browser-based system was simple to use. Its setup required no technical skills, so users adopted it quickly.
- Built-in Support: A complete help system lets users find answers independently, reducing the need for external help and speeding up learning.
The Impact and Results: The company rolled out the system for 10 users after a brief onboarding session, which brought about significant changes:
- Improved Maintenance Efficiency: The CMMS smoothed operations, reducing paperwork and automating admin tasks. This change led to quicker responses and better overall efficiency.
- Increased Equipment Uptime: Moving from reactive to proactive maintenance cuts unplanned downtime, raising output and profits. The system can predict maintenance jobs by looking at past data, making production more predictable.
- Better Inventory Management: Better control of spare parts reduces stockouts, storage costs, and delays.
- Data-Driven Decision-Making: The CMMS offered important insights to management, allowing for smarter resource use and improved planning.
Microservices: The Future of SMB Maintenance Agility
The era of monolithic, reactive maintenance is over. For SMBs facing tough operational challenges, microservice CMMS platforms are not an upgrade. They are a must-have for small and medium-sized businesses. CMMS with microservices now provides predictive maintenance, automation, and data analytics, replacing the old way of handling reactive and manual tasks.
This shift turns their role into a major driver of efficiency and profit. It helps managers concentrate on strategic tasks, make data-driven decisions, and enhance workflows. Using cloud-based CMMS, AI in maintenance, and IoT integration, businesses can shift to fully integrated, data-driven operations.
For SMBs considering a microservice CMMS, a practical roadmap should guide the transition:
- Start with a Detailed Needs Assessment: First, find the key issues in current maintenance operations. Set clear and measurable big-picture goals. Also, define Key Performance Indicators (KPIs) for the new CMMS to meet.
- Build a Skilled Team: Form a dedicated group with key people from essential departments like maintenance, IT, and operations. Get strong support from executives and include employees in choosing the CMMS to build ownership and reduce resistance to change.
- Choose the Right Microservice CMMS: Focus on options with an easy-to-use interface, good mobile features, flexible reporting, and excellent customer support. Cloud-based solutions are often suggested for SMBs. They offer lower upfront costs and lighten the IT load.
- Plan a Step-by-Step Rollout Strategy: Begin with the key assets or maintenance modules. Clean and standardize the necessary data. Next, gradually expand the system's scope. This approach minimizes disruption and allows for continuous learning and refinement.
- Offer Comprehensive Assistance: Training should be an ongoing process, not a single event. Ensure that all users, from technicians to administrators, are comfortable and proficient in the system's capabilities. Continuous support is essential for optimizing the system's capabilities and increasing user adoption.
- Monitor Adoption and Celebrate Wins: Regularly track user adoption rates and system performance. Identify and address any bad practices early. Celebrate all successes, big or small, which helps reinforce good behaviors and keeps the momentum during the transition.
Businesses can use a modular, agile approach to change maintenance from a cost center to a decisive advantage that ensures resilience, boosts profits, and helps every asset perform at its best. The choice is clear: adapt, innovate, and thrive.
TABLE OF CONTENTS
Keep Reading
The world of IoT is growing rapidly in almost every aspect of life across a variety of ...
29 Aug 2025
The adoption of Computerized Maintenance Management Systems (CMMS) presents a puzzling ...
28 Aug 2025
For the sake of repetition, a CMMS (Computerized Maintenance Management System) is the hub ...
26 Aug 2025
Too often, production and maintenance departments operate in silos, resulting in a lack of ...
22 Aug 2025
Many organizations struggle with scaling maintenance operations, mainly because some don’t ...
21 Aug 2025
Computerized Maintenance Management Systems (CMMS) have increasingly become the go-to tools ...
19 Aug 2025
It doesn’t seem to matter which energy provider you choose; the bottom line is that energy ...
15 Aug 2025
In FDA-regulated industries such as pharmaceuticals, medical devices, biotechnology, and food ...
14 Aug 2025
B2C businesses, such as retail, hospitality, and food service, operate in a highly ...
8 Aug 2025
What happens when your most experienced maintenance leader is planning on retiring, taking 20 ...
7 Aug 2025
Today’s maintenance operations have become more complex and sophisticated. Gone are the days ...
5 Aug 2025
Modern warehouses are instrumental to maintaining the smooth operations of supply chains, ...
1 Aug 2025
Computerized Maintenance Management Systems (CMMS) have proven to be essential tools for ...
31 Jul 2025
Sometimes it feels as if technology is expanding at the speed of light. This is an ...
29 Jul 2025
Data Center downtime can have a huge negative impact ranging from damage to the data center’s ...
25 Jul 2025
Whenever a company introduces a new process or technology, it’s followed by a period of ...
24 Jul 2025
Obsolescence often comes unexpectedly, mainly because little attention is given to the ...
22 Jul 2025
Imagine you're going through a compliance audit, and the inspector asks for maintenance ...
10 Jul 2025
Maintenance managers understand that disasters are unpredictable and can have a massive ...
4 Jul 2025
Asset lifespan is a key concern for executives and maintenance and facility management teams. ...
3 Jul 2025