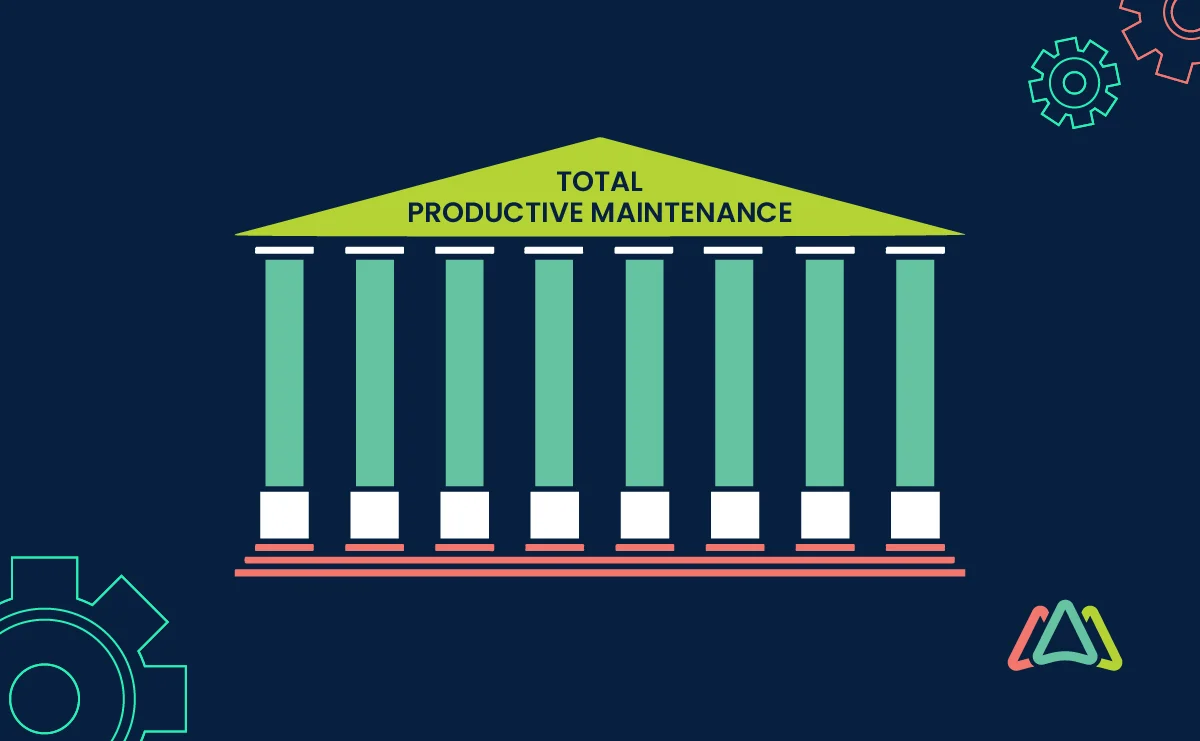
Achieving Operational Excellence with Total Productive Maintenance
Frequent equipment breakdowns, unanticipated downtime, and soaring maintenance costs are issues that are often seen in many organizations. Left unaddressed, the problems will only get worse. The transformative power of Total Productive Maintenance (TPM) offers organizations experiencing operational challenges a way to address them head-on. TPM provides a comprehensive approach that can revolutionize your maintenance practices and drive operational excellence.
At its core, TPM is an integrated maintenance strategy that goes beyond traditional approaches. It aims to eliminate breakdowns, reduce downtime, and enhance overall equipment effectiveness (OEE) by incorporating maintenance into the fabric of your organization's culture.
Instead of simply reacting to equipment failures, TPM emphasizes preventive and proactive measures. It encourages involvement from all levels of the workforce, fostering a collective responsibility for equipment reliability. With TPM, everyone becomes active participants in maintenance activities, starting with top management and all the way to frontline technicians. The core principles of TPM revolve around maximizing equipment efficiency, engaging employees, and driving continuous improvement.
A study conducted on selected SMEs (small and medium-sized enterprises), found that 52% of the organizations implemented Total Productive Maintenance (TPM) to improve its maintenance practices, maximize equipment effectiveness, and achieve world-class operation standards.
The Pillars of Total Productive Maintenance: Building a Foundation for Operational Excellence
Total Productive Maintenance (TPM) is built upon a solid foundation of key pillars that form the bedrock of this powerful maintenance strategy. By understanding these pillars, organizations can establish a robust framework for achieving operational excellence, resulting in ongoing improvements in their operations.
Equipment Reliability
The first pillar of TPM is centered around maximizing equipment reliability. It involves creating a proactive maintenance strategy that focuses on preventing breakdowns and ensuring equipment operates at optimal levels. It emphasizes routine inspections, preventive maintenance, and addressing equipment issues promptly to minimize downtime and improve overall equipment effectiveness.
Autonomous Maintenance
The second pillar involves enabling operators and frontline maintenance teams to oversee equipment care through a series of scheduled and defined checks. By providing training and guidance, operators become actively involved in routine maintenance tasks such as cleaning, lubrication, and basic inspections. This approach fosters a sense of responsibility, increased equipment knowledge, and makes it possible to detect potential problems well in advance.
Planned Maintenance
Planned maintenance emphasizes the importance of systematic and scheduled maintenance activities. This pillar focuses on developing comprehensive maintenance plans, establishing preventive maintenance routines, and conducting equipment overhauls or major repairs during planned downtime. By implementing planned maintenance practices, organizations can reduce reactive maintenance, enhance equipment reliability, and optimize maintenance resources.
Quality Maintenance
Quality maintenance integrates the principles of TPM with a focus on product quality. It focuses on ensuring that equipment will continue to operate within specified parameters to produce consistent, and high-quality output. This pillar emphasizes the role of maintenance in preventing equipment defects, minimizing waste, and driving continuous improvement efforts to meet customer expectations.
Training and Skills Development
A knowledgeable and skilled workforce is essential for effective maintenance practices. This pillar encompasses the ideas of providing relevant training, promoting cross-functional skill sets, and fostering a learning culture to empower employees and enhance their ability to contribute to TPM initiatives.
Advantages of Total Productive Maintenance (TPM)
Total Productive Maintenance (TPM) offers numerous benefits and advantages to organizations looking to optimize their operations and achieve operational excellence. By embracing TPM principles, it is possible to achieve enhanced efficiency, reduced downtime, improved product quality, increased productivity, and a proactive maintenance culture.
Increased Equipment Efficiency
TPM focuses on maximizing equipment reliability through proactive maintenance practices by implementing preventive maintenance, routine inspections, and timely repairs. This results in minimizing unexpected breakdowns, improving equipment uptime, and ensuring consistent productivity. In the end, organizations experience increased operational efficiency and higher overall equipment effectiveness (OEE).
Improved Product Quality
TPM integrates quality maintenance into its framework, ensuring that equipment operates within specified parameters to produce consistent, high-quality output. By minimizing variations and defects, TPM helps organizations achieve higher product quality, meet customer expectations, and reduce waste. This leads to improved customer satisfaction, brand reputation, and market competitiveness. The overall benefit is a higher bottom line for company owners.
Empowered Workforce and Collaboration
TPM fosters a culture of employee empowerment and collaboration. Through autonomous maintenance practices, operators and frontline maintenance teams become actively involved in equipment care and problem-solving. This not only enhances their skills and knowledge but also creates a sense of ownership, engagement, and shared responsibility for equipment reliability.
Cost Savings and Efficient Resource Utilization
Efficient resource utilization is achieved through better planning, reduced reactive maintenance, and optimized maintenance schedules. TPM allows organizations to allocate resources more effectively, streamline workflows, and achieve cost efficiencies in maintenance operations.
Continuous Improvement and Kaizen Mindset
TPM promotes a culture of continuous improvement and encourages the adoption of a Kaizen mindset throughout the organization. With TPM, employees are empowered to identify areas for improvement, suggest innovative solutions, and participate in problem-solving initiatives. This fosters a culture of learning, innovation, and ongoing operational enhancements.
Implementing Total Productive Maintenance in your Organization
Maintenance managers play a crucial role in implementing TPM and ensuring its successful integration into your organization's culture. This guide aims to provide practical insights and steps to effectively implement TPM in any organization.
Gain Management’s Support
Maintenance managers need to educate top management about the benefits of TPM, its impact on operational efficiency, and the long-term advantages it brings. It is essential to engage them in the maintenance process, emphasizing the need for resource allocation, training, and organizational change. Management support is critical in setting the tone for TPM implementation and obtaining the necessary resources for success.
Create a Cross-Functional TPM Team
Forming a cross-functional TPM team that includes representatives from maintenance, production, quality, and other relevant departments is another critical step in implementing this maintenance approach. This team will be responsible for driving the TPM initiative, developing action plans, and ensuring effective communication and collaboration across departments. Encouraging open dialogue, exchange of ideas, and involvement from all team members to foster a sense of ownership and shared responsibility is a key to TPM’s success.
Conduct a Baseline Assessment
Performing a comprehensive assessment of an organization's current maintenance practices, equipment reliability, and performance metrics is a critical starting point. Identifying areas for improvement, bottlenecks, and opportunities for implementing TPM principles will provide a baseline from where to achieve productivity efficiencies.
Develop a TPM Implementation Plan
A TPM plan should be based on the assessment findings and outline specific goals, timelines, and action steps for each TPM pillar. Breaking down the implementation process into manageable phases, and ensuring that each phase aligns with organizational priorities and available resources is a good starting point strategy. Regularly reviewing and adjusting the plan as needed to accommodate emerging needs and challenges should be a routine next step.
Establish TPM Performance Metrics
Defining key performance indicators (KPIs) to measure the effectiveness of TPM implementation are essential monitoring tools. These metrics may include equipment uptime, OEE, mean time between failures, maintenance costs, and others relevant to your organization's objectives. Regularly monitoring and analyzing these metrics make it possible to assess the impact of TPM on overall performance and identify areas for further improvement.
Overcoming Challenges in Implementing Total Productive Maintenance
Implementing Total Productive Maintenance (TPM) within an organization can bring significant benefits, but it is not without its challenges.
Resistance to Change
Challenge
Employees and management may be accustomed to traditional maintenance practices and they may be hesitant when it comes to embracing new methodologies and ways of working.
Solution
Overcoming resistance can be challenging but at the same time, it’s critical to get all team members on board. This can be achieved by creating awareness and communicating the benefits of TPM to all stakeholders. An initial focus should be on providing training sessions to educate employees about TPM principles and how it aligns with organizational goals. By encouraging open dialogue, address concerns, and highlight success stories from organizations that have successfully implemented TPM, initial resistance can be overcome.
Lack of Resources
Challenge
Limited resources may hinder the ability to invest in training, equipment upgrades, and other necessary elements of TPM.
Solution
Developing a persuasive business model that demonstrates the return on investment (ROI) and long-term benefits of TPM will make the case for its value. Exploring partnerships with external training providers or seeking guidance from industry experts will optimize resource utilization and reduce implementation costs.
Inadequate Data and Information Systems
Challenge
Lack of accurate and reliable data, as well as outdated information systems, can hinder effective TPM implementation. Without access to real-time data, it becomes challenging to monitor equipment performance, track maintenance activities, and identify improvement opportunities.
Solution
Investing in modern data collection and analysis tools, such as CMMS software, to capture and analyze critical maintenance data is essential in being able to access the benefits of TCM. Implementing regular data collection processes and training employees to accurately record equipment information and maintenance activities are essential components of its core strategy. Leveraging data analytics to identify patterns, trends, and areas for improvement will help meet organizations’ operational goals.
Sustaining TPM Efforts
Challenge
Sustaining TPM initiatives over the long term can be a challenge, as complacency and regression to old habits can occur. Without ongoing reinforcement and continuous improvement, the gains achieved through TPM may diminish.
Solution
Establishing a system of regular TPM audits and reviewing meetings to monitor progress and identify areas for improvement are key to achieving long term benefits. Encouraging the use of visual management tools, such as performance dashboards and scorecards, to track key metrics and maintaining focus on TPM goals offer ways to adjust maintenance schedules to make them more efficient. Fostering a culture of continuous improvement by celebrating successes, sharing best practices, and facilitating knowledge-sharing sessions enhances team worker compliance.
Total Productive Maintenance (TPM) offers a multitude of benefits to organizations that are striving for operational excellence. By prioritizing equipment efficiency, minimizing downtime, improving product quality, empowering the workforce, achieving cost savings, and fostering a culture of continuous improvement, organizations can unlock the full potential of TPM. Embracing TPM principles paves the way for enhanced operational performance, increased competitiveness, and long-term success in today's dynamic and challenging business environment.
TABLE OF CONTENTS
Keep Reading
For the sake of repetition, a CMMS (Computerized Maintenance Management System) is the hub ...
26 Aug 2025
Too often, production and maintenance departments operate in silos, resulting in a lack of ...
22 Aug 2025
Many organizations struggle with scaling maintenance operations, mainly because some don’t ...
21 Aug 2025
Computerized Maintenance Management Systems (CMMS) have increasingly become the go-to tools ...
19 Aug 2025
It doesn’t seem to matter which energy provider you choose; the bottom line is that energy ...
15 Aug 2025
In FDA-regulated industries such as pharmaceuticals, medical devices, biotechnology, and food ...
14 Aug 2025
B2C businesses, such as retail, hospitality, and food service, operate in a highly ...
8 Aug 2025
What happens when your most experienced maintenance leader is planning on retiring, taking 20 ...
7 Aug 2025
Today’s maintenance operations have become more complex and sophisticated. Gone are the days ...
5 Aug 2025
Modern warehouses are instrumental to maintaining the smooth operations of supply chains, ...
1 Aug 2025
Computerized Maintenance Management Systems (CMMS) have proven to be essential tools for ...
31 Jul 2025
Sometimes it feels as if technology is expanding at the speed of light. This is an ...
29 Jul 2025
Data Center downtime can have a huge negative impact ranging from damage to the data center’s ...
25 Jul 2025
Whenever a company introduces a new process or technology, it’s followed by a period of ...
24 Jul 2025
Obsolescence often comes unexpectedly, mainly because little attention is given to the ...
22 Jul 2025
Imagine a world where critical assets run smoothly without unexpected downtime, maintenance ...
18 Jul 2025
Imagine you're going through a compliance audit, and the inspector asks for maintenance ...
10 Jul 2025
Maintenance managers understand that disasters are unpredictable and can have a massive ...
4 Jul 2025
Asset lifespan is a key concern for executives and maintenance and facility management teams. ...
3 Jul 2025
Your company recently invested funds and time for new CMMS software, and six months later, it ...
1 Jul 2025