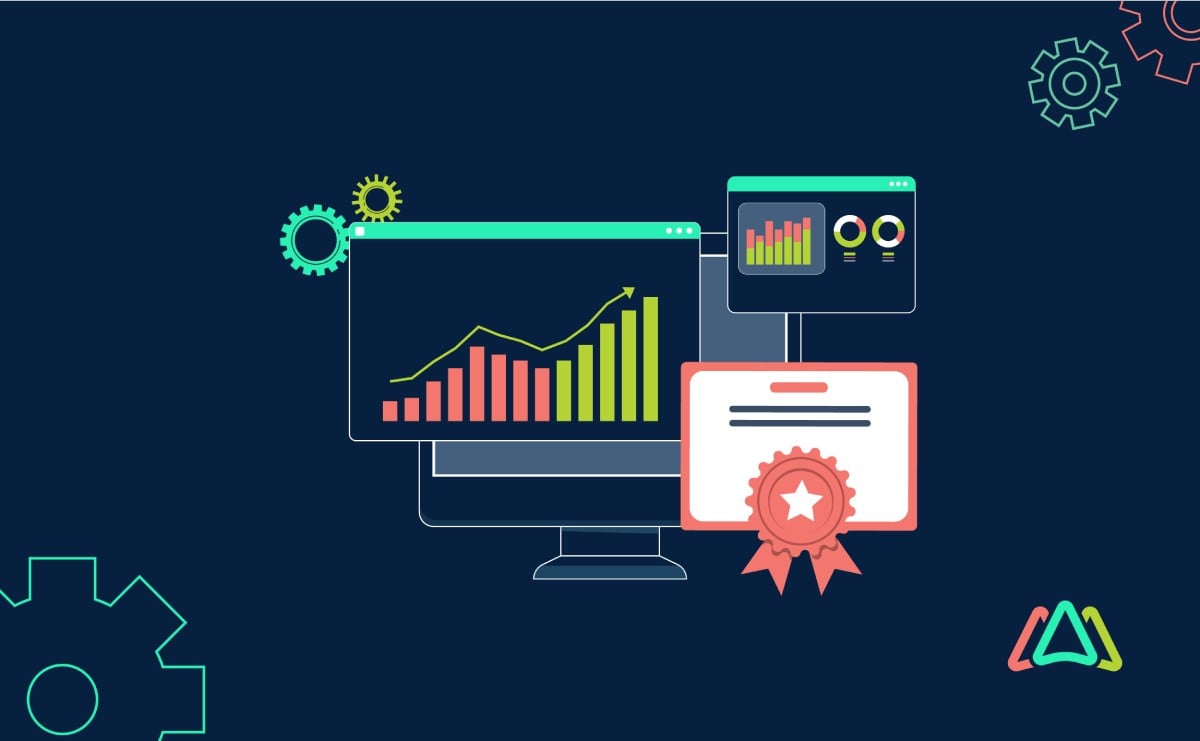
10 Ways CMMS Software Drives Maintenance Excellence
When researching Computerized Maintenance Management Software (CMMS) you’ll find endless amounts of articles covering functionality, best practices for implementation, and technology trends. Interestingly, there’s little written about how a CMMS can drive excellence in a company’s maintenance operations. Perhaps this is because leaders often assume that achieving maintenance excellence is a simple matter of implementing a CMMS and using it regularly.
Achieving maintenance excellence with a CMMS goes beyond implementation and user adoption. This article explores maintenance excellence and how maintenance leaders can achieve it by combining CMMS capabilities with a culture of excellence within an organization.
What is Maintenance and Workplace Excellence?
Maintenance excellence refers to achieving the highest achievable level of effectiveness and efficiency in the management and execution of maintenance activities within an organization. It involves implementing best practices, utilizing advanced technologies, and optimizing processes to ensure that assets and facilities are kept in optimal condition to support the organization's goals and objectives. Achieving maintenance excellence is crucial for organizations seeking to maximize the value and lifespan of their assets, while minimizing operational risks and costs. It requires a holistic approach that combines technology, processes, and a skilled and committed workforce to create a well-balanced and efficient maintenance program.
Excellence in the workplace is an integral component of achieving maintenance excellence, yet it is often overlooked. Workplace excellence involves creating an environment where employees are motivated, empowered, and equipped to perform their best. Before diving into how CMMS software drives maintenance and workplace excellence, let’s break down the critical elements to achieving them.
Key Elements of Maintenance Excellence
- Reliability and Availability: Minimizing unplanned downtime and breakdowns, and maximizing uptime.
- Cost Efficiency: Optimizing allocation of resources, including spare parts and materials, and labor utilization to balance costs with performance.
- Safety and Compliance: Prioritizing the safety of personnel, as well as ensuring that all maintenance activities comply with relevant regulations and standards.
- Asset Performance Management (APM): Implementing strategies to monitor and improve the performance of critical assets over their entire lifecycle.
- Preventive and Predictive Maintenance (PdM): Employing proactive strategies to prevent equipment failures and predict maintenance needs before they occur.
- Data-Driven Decision Making: Utilizing data and analytics to make informed decisions about maintenance strategies, resource allocation, and performance improvement initiatives.
- Continuous Improvement: Processes, technologies, and practices are regularly reviewed and refined with the goal of improving performance.
- Training and Skills Development: Ensuring maintenance personnel are well-trained, up-to-date, and possess the necessary skills and knowledge to perform their tasks effectively.
- Asset Lifecycle Management: Processes put in place from the collection and analysis of asset data to help improve the way a business purchases, uses, and disposes of its assets.
- Sustainability and Environmental Considerations: Incorporating energy efficiency measures and environmentally friendly disposal methods into operations.
Key Elements of Workplace Excellence
- Setting Clear Expectations and Goals: Defining roles, responsibilities, and performance expectations for each employee that are specific, measurable, achievable, relevant, and time-bound.
- Providing Ongoing Feedback: Regular feedback helps employees understand how their work aligns with organizational goals and encourages them to have open communication.
- Training and Development Opportunities: Making programs and resources available that enhance employees' skills, knowledge, and professional growth.
- Recognizing and Rewarding Achievements: Acknowledging and celebrating individual and team accomplishments with meaningful rewards boosts morale and motivation.
- Promoting a Positive Work Environment: Fostering a culture of respect, inclusivity, and collaboration.
- Empowering Employees to Make Decisions: Involving employees in work-related decision-making processes shows their opinions and ideas are valued. It also encourages autonomy, providing opportunities for employees to take ownership of their work.
- Fostering a Growth Mindset: Encouraging employees to view challenges as opportunities for growth and learning. This promotes a mindset that values continuous improvement and innovation.
Achieving Maintenance Excellence with a CMMS
Having reviewed the key elements of maintenance and workplace excellence, let’s look at specific ways a CMMS software plays a critical role in achieving that end.
1. Work Order Management
The CMMS streamlines managing work orders from creation to completion. Work orders cover a variety of activities, including routine maintenance, equipment inspections, repairs, and larger-scale projects. The software oversees the workflow, from assigning tasks, scheduling, tracking progress, optimizing resource allocation, ensuring timely maintenance response, and maintaining detailed records for reference and regulatory compliance purposes. By streamlining work order management, CMMS systems contribute to more efficient and cost-effective maintenance operations, ultimately improving facility performance.
2. Preventive Maintenance Scheduling
Preventive maintenance scheduling refers to the systematic planning and organization of routine maintenance tasks for equipment, machinery, and facilities. Its goal is to proactively prevent potential issues and breakdowns by adhering to a predetermined maintenance schedule. With data-driven insights, CMMS helps optimize resources, ensure compliance with regulatory standards, and extend the lifespan of assets using programming options. Moreover, maintenance teams can more efficiently allocate resources, track maintenance history, and prioritize tasks based on criticality. Together, the result is improved operational efficiency, reduced downtime, and maximization of a company's asset performance.
3. Asset Tracking and Management
CMMS asset tracking involves systematically recording and managing physical assets within an organization. Its comprehensive database stores details about equipment, machinery, facilities, and other valuable assets, including additional information such as location, maintenance history, warranties, and relevant documentation. This feature streamlines the monitoring of asset performance and scheduling of maintenance tasks and helps optimize resource allocation. The benefits of asset tracking include operational efficiency, prolonging the lifespan of assets, reducing downtime, and ultimately improving overall productivity. It also aids in making informed decisions regarding repairs, replacements, and resource investments based on real-time data and historical trends.
4. Inventory and Parts Management
CMMS inventory and parts management refers to the digitalized approach of overseeing and organizing an organization's maintenance-related materials, components, and supplies. Organizations can efficiently track, monitor, and control their inventory levels, including spare parts, tools, equipment, and consumables essential for maintenance activities. This feature streamlines procurement processes, helps set reorder points, tracks usage, and provides valuable insights into inventory trends. Maintenance teams have timely access to the right components, reducing downtime and optimizing resource utilization. It also aids in cost management, helping businesses make informed decisions regarding inventory levels and minimizing overstocking or stockouts.
5. Resource Allocation Optimization
CMMS resource allocation optimization refers to efficiently distributing and utilizing resources within a maintenance management framework. It involves strategically allocating manpower, equipment, time, and budgetary resources to maximize productivity and minimize downtime in a facility or organization. This approach utilizes data-driven insights, historical maintenance records, and predictive analytics to make informed decisions about when and where resources should be deployed. By prioritizing tasks based on criticality and optimizing schedules, the CMMS ensures that maintenance activities are carried out efficiently. The result is improved operational performance and reduced maintenance costs.
6. Data-Driven Decision Making
CMMS data-driven decision-making refers to utilizing information gathered and stored within the software to make informed choices regarding maintenance operations. It relies on analyzing various data points, such as equipment performance, maintenance history, work order completion times, and cost trends, to identify patterns, inefficiencies, and opportunities for improvement. Organizations can use this data to make proactive decisions about maintenance schedules, resource allocation, and equipment replacement, ultimately optimizing asset performance and reducing operational costs. With data-driven decision-making, organizations can move from reactive maintenance strategies to more strategic and cost-effective approaches that enhance overall operational efficiency and extend the lifespan of critical assets.
7. Regulatory Compliance and Reporting
Regulatory compliance and reporting refers to integrating a CMMS with regulatory standards and requirements in various industries. This includes compliance with safety-related laws, environmental protection, quality control, and other pertinent regulations. Apart from helping track and manage maintenance activities, it also generates reports and documentation necessary to demonstrate compliance with these standards. By automating and streamlining the process, this feature helps safeguard the integrity of operations and the well-being of stakeholders while aiding in audits and inspections.
8. Minimizing Downtime
Downtime reduction refers to minimizing or mitigating the time equipment, machinery, or systems are non-operational due to maintenance-related activities. This CMMS feature streamlines maintenance operations, schedules preventative tasks, and swiftly addresses repairs. Benefits include enhanced operational efficiency, increased asset reliability, and, ultimately, reduced overall downtime experienced by their equipment and facilities. The result is improved productivity and cost savings in the long run.
9. Safety and Risk Management
Safety and risk management refers to integrating safety protocols with risk assessment procedures within the CMMS platform. It uses tools and features designed to proactively identify, evaluate, and mitigate potential safety hazards and risks associated with maintenance operations in various industrial settings. Tracking safety-related data, such as incident reports, equipment inspections, and compliance with regulatory standards, is all possible. Preventive measures and allocating resources for maintenance tasks in a manner that prioritizes safety are also included. With this CMMS feature, organizations can enhance their ability to maintain a secure work environment, reduce accidents, and ensure compliance with industry-specific safety regulations.
10. Cost Control and Budgeting
Cost control and budgeting refers to effectively managing and optimizing expenses related to maintenance activities within an organization. It involves tracking, analyzing, and planning maintenance costs to align with allocated budgets and organizational objectives. This includes monitoring expenditures on labor, materials, equipment, and other resources needed for maintenance operations. The goal is to maintain equipment and facilities efficiently while minimizing unnecessary expenses and ensuring maintenance costs stay within predefined limits.
Conclusion
CMMS software is a valuable tool for organizations seeking maintenance excellence. It facilitates efficient work order management, preventive maintenance scheduling, asset tracking, inventory management, resource allocation optimization, data-driven decision-making, regulatory compliance, reducing downtime, safety management, and controls costs. Implementing a CMMS and using its capabilities effectively improves operational efficiency, increases equipment reliability, and reduces maintenance costs.
Remember, driving excellence is an ongoing effort requiring consistent attention and commitment from leaders and employees. By implementing these strategies, you can create a culture of excellence that fosters high performance, employee satisfaction, and organizational success.
TABLE OF CONTENTS
Keep Reading
Computerized Maintenance Management Systems (CMMS) have increasingly become the go-to tools ...
19 Aug 2025
It doesn’t seem to matter which energy provider you choose; the bottom line is that energy ...
15 Aug 2025
In FDA-regulated industries such as pharmaceuticals, medical devices, biotechnology, and food ...
14 Aug 2025
B2C businesses, such as retail, hospitality, and food service, operate in a highly ...
8 Aug 2025
What happens when your most experienced maintenance leader is planning on retiring, taking 20 ...
7 Aug 2025
Today’s maintenance operations have become more complex and sophisticated. Gone are the days ...
5 Aug 2025
Modern warehouses are instrumental to maintaining the smooth operations of supply chains, ...
1 Aug 2025
Computerized Maintenance Management Systems (CMMS) have proven to be essential tools for ...
31 Jul 2025
Sometimes it feels as if technology is expanding at the speed of light. This is an ...
29 Jul 2025
Data Center downtime can have a huge negative impact ranging from damage to the data center’s ...
25 Jul 2025
Whenever a company introduces a new process or technology, it’s followed by a period of ...
24 Jul 2025
Obsolescence often comes unexpectedly, mainly because little attention is given to the ...
22 Jul 2025
Imagine a world where critical assets run smoothly without unexpected downtime, maintenance ...
18 Jul 2025
Imagine you're going through a compliance audit, and the inspector asks for maintenance ...
10 Jul 2025
Maintenance managers understand that disasters are unpredictable and can have a massive ...
4 Jul 2025
Asset lifespan is a key concern for executives and maintenance and facility management teams. ...
3 Jul 2025
Your company recently invested funds and time for new CMMS software, and six months later, it ...
1 Jul 2025
As Computerized Maintenance Management Systems (CMMS) become more connected and cloud-based, ...
1 Jul 2025
Edge computing is an innovative technology that enables data to be processed at the source, ...
24 Jun 2025
Facility management has undergone a significant transformation in recent times. Take, for ...
20 Jun 2025