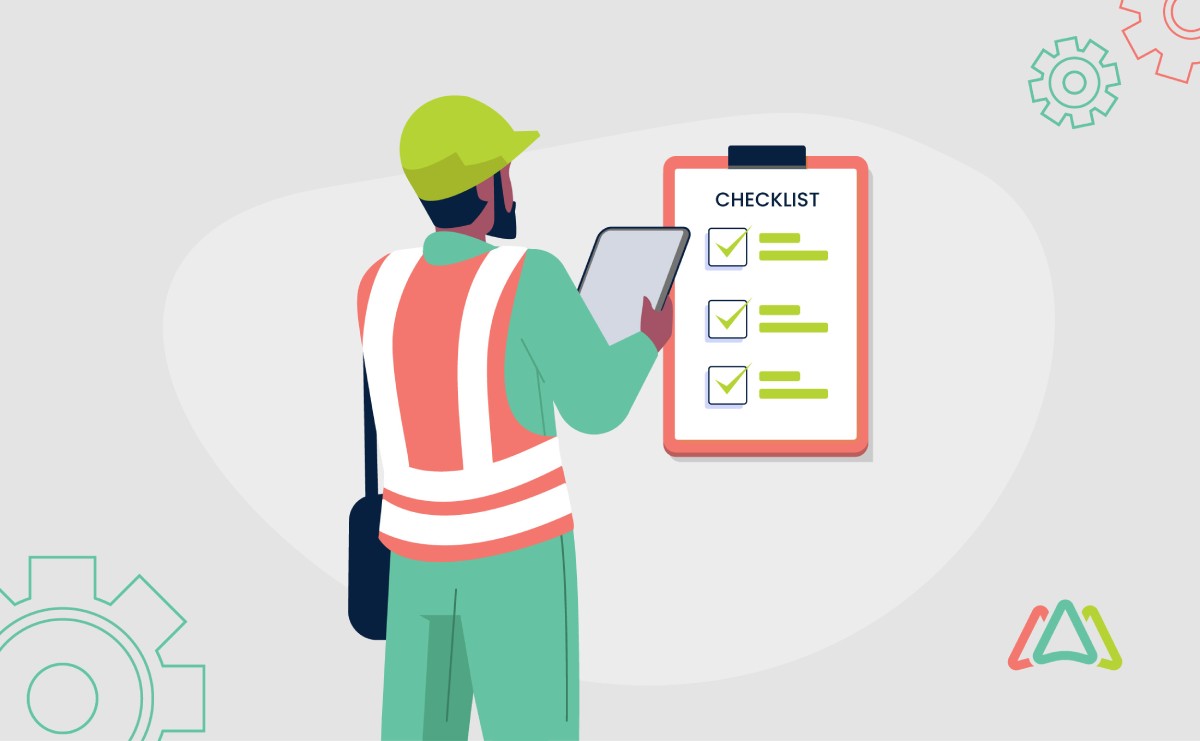
Preventive Maintenance Checklist: The Key to Proactive Maintenance
Preventive maintenance is a proactive approach that aims to prevent unexpected breakdowns and minimize downtime. It is also an effective strategy for businesses to reduce costs and extend the life of assets. At the core of an effective preventive maintenance strategy lies the preventive maintenance checklist, a comprehensive tool that guides maintenance teams in carrying out essential maintenance tasks.
Preventive maintenance involves the regular inspection, cleaning, and servicing of equipment before any issues arise. According to a research by Pacific Partners Consulting Group, postponing $1 worth of maintenance can potentially lead to a 4X increase ($4) in capital renewal costs in the future. By adhering to a well-structured preventive maintenance checklist, organizations can stay ahead of potential problems, increase equipment reliability, and prevent this exponential increase in replacement or downtime costs.
The purpose of implementing a preventive maintenance checklist is to systematically identify, prioritize, and execute maintenance tasks based on predefined schedules or triggers. This checklist serves as a roadmap that outlines the specific maintenance activities required for each asset or equipment category. By following this checklist diligently, organizations can positively impact their operations.
Nielsen conducted a survey of 101 manufacturing executives in the automotive industry, from parts suppliers to engine makers to automakers. Participants surveyed say the cost of stopped production can be as high as $22,000 per minute.
A preventive maintenance checklist helps minimize downtime by proactively identifying and addressing maintenance needs. By conducting regular inspections, servicing, and parts replacements, organizations prevent unexpected breakdowns and keep equipment running smoothly. This reduces costly downtime and its negative impact on productivity and customer satisfaction.
The 5 Benefits of Using a Preventive Maintenance Checklist
1. Clear and organized workflow
A checklist provides a clear and organized workflow, guiding technicians and operators through each step of the maintenance process. They can easily follow the checklist to determine which tasks need to be completed, in what order, and with what tools or materials to use. This eliminates confusion and minimizes time spent on figuring out the next steps.
2. Standardized procedures
A checklist standardizes maintenance procedures, promoting efficiency and reducing guesswork. Technicians follow predefined steps, saving time and ensuring consistency. Troubleshooting steps in the checklist help diagnose and resolve equipment issues quickly, minimizing downtime.
3. Prioritization of tasks
A preventive maintenance checklist helps prioritize tasks based on their importance and urgency. Technicians can easily identify high-priority tasks that require immediate attention, allowing them to allocate their time and resources efficiently. This prevents time wasted on less critical tasks when more critical issues are at hand.
4. Elimination of unnecessary tasks
A well-designed checklist includes only essential maintenance tasks, eliminating redundant or unnecessary activities. Technicians and operators can focus on critical tasks that directly contribute to equipment performance and reliability, saving time by avoiding non-value-added activities
5. Enhanced communication and collaboration
A checklist promotes effective communication and collaboration among maintenance teams. Technicians can easily communicate task status, share information, and collaborate on complex maintenance activities. This streamlines teamwork, prevents duplication of efforts, and ultimately saves time for everyone involved.
By leveraging the benefits of a preventive maintenance checklist, organizations can optimize equipment performance, reduce costs, enhance safety, and ensure smooth operations, ultimately leading to long-term success and competitiveness in the market.
Steps to Create an Effective Preventive Maintenance Checklist
STEP 1: Categorize Equipment
Here's how to effectively manage equipment inventory and categorization:
1.1 Conduct a Comprehensive Inventory
Document all the assets and equipment that require maintenance. Include machinery, vehicles, tools, and any other equipment relevant to the organization's operations. Capture essential details such as equipment name, model number, serial number, location, and installation date. This comprehensive inventory provides a clear picture of the scope of the assets that require preventive maintenance and inspections.
1.2 Categorize Assets Based on Criticality
Once the inventory is complete, use the equipment criticality assessment matrix to categorize assets based on their criticality to the organization's operations. Identify equipment that directly affects production, safety, or has a direct impact on customer satisfaction. Assign a priority level to each asset, considering its impact on business continuity and overall performance. This categorization helps allocate resources effectively and prioritize maintenance tasks accordingly.
STEP 2: Determine Maintenance Frequencies
Once equipment inventory and categorization are complete, the next step in creating an effective preventive maintenance checklist is determining the maintenance frequency for each asset. Here's how to determine maintenance frequencies:
2.1 Refer to Manufacturer Guidelines
Manufacturers often provide guidelines regarding recommended maintenance schedules for their equipment. These guidelines outline the frequency of inspections, servicing, and parts replacements. Review the manufacturer's documentation and incorporate their recommendations into the preventive maintenance checklist. Documentation can easily be found on the manufacturer’s website and O&M manuals. If the equipment is custom built, ensure that the manufacturer provides clear documentation and training for maintaining it.
2.2 Consider Usage Patterns
Evaluate how frequently each asset is used and the workload it handles. Equipment subjected to heavy usage may require more frequent maintenance to ensure optimal performance. Conversely, equipment with lighter usage may have longer intervals between maintenance activities. Consider the equipment's operational hours, cycles, and production volume to determine appropriate maintenance frequencies.
2.3 Assess Environmental Factors
Environmental conditions can impact equipment performance and maintenance needs. Factors such as temperature, humidity, and exposure to dust and corrosive substances can affect the wear and tear of equipment. Take into account the environmental conditions in which assets operate and adjust maintenance frequencies accordingly. Equipment in harsh environments may require more frequent inspections and cleaning.
2.4 Incorporate Inputs from Maintenance Professionals
Seek input from maintenance professionals and technicians and operators who have hands-on experience with the equipment. Their expertise and observations can provide valuable insights into the maintenance needs of specific assets. They can offer recommendations for optimizing maintenance frequencies based on their tacit knowledge of equipment behavior and failure patterns.
STEP 3: Identify Critical Maintenance Tasks
Identify and define specific maintenance tasks for each equipment type and category to ensure that all necessary maintenance activities are included and that nothing is overlooked. Here's how to identify critical maintenance tasks:
3.1 Define Maintenance Activities
Begin by listing the maintenance activities required for each equipment type or category. This can include tasks such as inspections, cleaning, calibration, parts replacement, and testing.
3.2 Tailor Tasks to Equipment Types
Different equipment types may have specific maintenance needs. For example, a motorized vehicle may require regular oil changes and filter replacements, while a manufacturing machine may need periodic alignment and adjustment. Customize the maintenance tasks based on the unique requirements of each equipment type. Consider safety, operational complexity, and the impact of tasks on equipment performance.
3.3 Prioritize Tasks Based on Criticality
Prioritize maintenance tasks based on their criticality to the organization's operations. Identify tasks that directly impact safety, compliance, and the overall performance of assets. Assign higher priority to tasks that, if neglected, could result in equipment failure, production delays, or safety hazards. Ensure that tasks essential for regulatory compliance are given appropriate attention.
3.4 Consider Safety Concerns
Safety should be a top priority in maintenance activities. Identify tasks that address safety concerns, such as inspections of safety devices, electrical connections, and emergency shut-off systems. Include tasks related to the maintenance and testing of safety equipment, such as fire extinguishers or ventilation systems. Prioritize these tasks to mitigate potential risks and create a safe working environment.
STEP 4: Schedule and Plan Maintenance Activities
Once the critical maintenance tasks have been identified, the next step is to establish a preventive maintenance schedule and plan to execute. Here's how to effectively schedule and plan maintenance activities:
4.1 Establish a Preventive Maintenance Plan
Create a plan that outlines the frequency of each maintenance task for each asset or equipment category. Develop a calendar-based schedule or a system that triggers maintenance activities based on specific time intervals, or on equipment usage, operational hours (meter-based).
4.2 Allocate Resources and Timeframes
Determine the resources required for each maintenance task, including manpower, tools, and materials. Consider the skills and expertise needed to perform specific tasks and assign responsibilities accordingly. Allocate sufficient timeframes for each task, considering the complexity and duration of the activity.
5 Components of an Effective Preventive Maintenance Checklist
1. Inspection and Condition Monitoring
Here are key aspects to consider:
1.1 Conduct Visual Inspections
Perform visual inspections of equipment to detect signs of wear, damage, or abnormalities. Look for loose or frayed wires, leaks, cracks, rust, or any other visible indications of potential problems. Visual inspections help identify issues that may require further investigation or maintenance actions.
1.2 Utilize Condition Monitoring Techniques
In addition to visual inspections, utilize advanced condition monitoring techniques to assess equipment health. This can include techniques such as vibration analysis, thermal imaging, oil analysis, or ultrasonic testing. These techniques enable early detection of abnormalities, allowing for timely intervention before major failures occur.
2. Component Cleaning and Calibration
Clean and calibrate equipment components to ensure optimal functionality and accuracy. Include the following tasks in the preventive maintenance checklist:
2.1 Clean and Remove Debris
Remove dirt, dust, and debris from equipment components. Clean air filters, cooling fins, fans, or any other parts susceptible to accumulation. Regular cleaning helps prevent overheating, clogging, or other issues caused by obstructed airflow.
2.2 Calibrate Sensors, Gauges, or Control Systems
Calibrate sensors, gauges, or control systems to ensure accurate readings and proper equipment performance. Calibration helps maintain precision, reliability, and safety in equipment operation.
3. Electrical System Checks
Electrical systems play a crucial role in equipment performance and safety. Incorporate the following tasks to ensure electrical system reliability:
3.1 Inspect Electrical Connections, Wirings, and Grounding
Check electrical connections, wirings, and grounding for signs of wear, loose connections, or corrosion. Ensure that all connections are secure and properly grounded to prevent electrical hazards.
3.2 Test Electrical Circuits, Switches, and Safety Mechanisms
Test electrical circuits, switches, and safety mechanisms to verify they are operating safely and as expected. This includes conducting tests on emergency shut-off systems, circuit breakers, or overload protection devices. Electrical testing helps identify and address potential issues that may compromise equipment functionality or safety.
4. Parts Replacement and Upkeep
Regularly inspect equipment for worn-out or faulty parts and ensure timely replacements or repairs. Consider the following tasks:
4.1 Identify Worn-out or Faulty Parts
Keep an eye on equipment components that are prone to wear and tear or have a limited lifespan. Identify parts that require replacement based on manufacturer recommendations or observed deterioration. Examples of parts that experience wear and tear include belts, bearings and seals.
4.2 Track Spare Parts Inventory
Maintain an organized spare parts inventory to ensure availability when replacements are needed. Regularly update the inventory and proactively replenish stock of spare parts to avoid delays in maintenance activities. Effective spare parts management helps minimize equipment downtime and ensures efficient maintenance execution. Using a CMMS is an effective way to track and maintain adequate inventory levels for frequently used parts.
5. Documentation and Record-Keeping
Accurate documentation and record-keeping are essential for tracking maintenance activities, identifying trends, and making informed decisions. Include the following practices:
5.1 Maintain Detailed Records of Maintenance Activities and Findings
Document all maintenance activities performed, including dates, tasks, and personnel involved. Record any findings, observations, or issues encountered during inspections or repairs. Detailed records provide a historical perspective and aid in troubleshooting or analyzing equipment performance.
5.2 Log Equipment History, Repairs, Maintenance Trends, and Performance Metrics
Keep a log of equipment history, including repairs, replacements, or significant maintenance events. Track maintenance trends and identify patterns that may indicate recurring issues. Monitor performance metrics such as equipment uptime, failure rates, or energy consumption. Analyzing these metrics helps optimize maintenance strategies and improve overall equipment reliability.
Implementing and Optimizing the Preventive Maintenance Checklist
1. Use Preventive Maintenance Software
Implementing preventive maintenance software, or a CMMS can significantly enhance the execution and tracking of the preventive maintenance checklist.
Utilize a CMMS to digitize the preventive maintenance checklist and streamline its execution. Input the checklist tasks, schedules, and associated documentation into the CMMS. This enables maintenance teams to access the checklist digitally, follow task instructions, and record completion status. A CMMS also provides visibility into maintenance activities, tracks progress, and generates reports for analysis. Almost all PM or CMMS software today have mobile apps allowing techs and operators to perform inspections and preventive maintenance from mobile devices. Inspections and PMs have checklists embedded making this process very easy and well documented. Paper and spreadsheets are things of the past.
2. Regular Execution and Performance Monitoring
Consistent execution of the preventive maintenance checklist is essential to ensure its effectiveness. Monitor performance to identify areas for improvement.
Adhere to the established maintenance schedule and execute the checklist activities as planned. Encourage consistency in following the checklist to avoid missed tasks or delayed maintenance activities. Regular execution ensures that equipment receives timely attention, reducing the risk of unexpected failures.
Establish key performance indicators (KPIs) to measure the effectiveness of the preventive maintenance checklist. These can include metrics such as equipment uptime, mean time between failures (MTBF), or maintenance costs. Continuously monitor and analyze these KPIs to assess the impact of the checklist on equipment performance, downtime reduction, and cost optimization.
3. Training and Skill Development
To ensure the successful implementation of a preventive maintenance checklist, it’s important to provide training and skill development opportunities for maintenance teams.
Conduct training sessions to familiarize maintenance personnel with the preventive maintenance checklist. Explain the purpose, components, and proper execution of the checklist. Train them on how to document findings, record maintenance activities, and follow the established schedule. This training ensures that teams understand the checklist's importance and can effectively implement it.
4. Continuous Improvement and Optimization
To maximize the benefits of the preventive maintenance checklist, embrace a culture of continuous improvement. Actively seek feedback and refine the checklist from time to time or as needed. Consider the following:
- Analyze Maintenance Data and Feedback: Regularly analyze maintenance data, including work order records, equipment history, and feedback from maintenance teams. Look for patterns, recurring issues, or areas for improvement. Identify root causes of equipment failures or breakdowns and adjust the checklist accordingly.
- Refine the Preventive Maintenance Checklist: Based on the analysis and feedback, refine the preventive maintenance checklist to make improvements. Update task frequencies, adjust priorities, or add / remove tasks as necessary. Incorporate lessons learned from past maintenance experiences to enhance the accuracy and relevance of the checklist. Continuously strive for improvement to ensure that the checklist aligns with evolving maintenance needs and industry best practices.
A proactive approach to maintenance not only extends equipment lifespan but also reduces costs and enhances operational efficiency.
Examples of Preventive Maintenance Checklist Templates
1. Template for a CNC Machine (Manufacturing)
Image: CNC Machine (Manufacturing)
Frequency |
Maintenance Task |
Completed? |
Daily |
Inspect the machine for any visible damage or abnormalities |
|
Check coolant levels and top up if necessary |
||
Clean the machine surfaces and remove any debris or chips |
||
Verify proper functioning of safety interlocks and emergency stop buttons |
||
Check and replenish lubrication levels as per manufacturer recommendations |
||
Inspect and clean the tool holders and remove any built-up residue |
||
Inspect and clean the work area, removing any chips or debris |
||
Weekly |
Clean the machine's filters and ensure proper airflow for cooling |
|
Inspect and clean the spindle taper and remove any accumulated dirt or debris |
||
Verify the accuracy of machine axes using calibration equipment |
||
Check and tighten any loose bolts or fasteners |
||
Inspect and replace worn-out or damaged cutting tools as necessary |
||
Verify the functionality of coolant pumps and nozzles |
||
Review and update machine tool offsets as needed |
||
Monthly |
Inspect and clean or replace air filters, if applicable |
|
Check and clean electrical cabinets, removing any dust or debris |
||
Inspect and clean the coolant tank and filters |
||
Verify and adjust the machine's backlash compensation |
||
Calibrate and check the accuracy of machine tools and probes |
||
Check and clean the chip conveyor and remove any built-up chips |
||
Review and update machine programs and parameters as needed |
||
Quarterly |
Conduct a thorough inspection of electrical connections and cables |
|
Inspect and clean the machine's spindle and spindle bearings |
||
Perform a comprehensive check of the machine's lubrication system |
||
Verify and adjust the machine's alignment and geometry |
||
Inspect and replace worn-out or damaged seals, gaskets, or belts |
||
Review and update the machine's preventive maintenance documentation |
||
Semi - Annual |
Perform a detailed inspection and cleaning of the machine's coolant system |
|
Verify and calibrate the machine's tool measurement and tool-setting systems |
||
Inspect and clean the machine's electrical cabinets and control panels |
||
Conduct a thorough examination of the machine's pneumatic systems |
||
Verify and update machine software, drivers, and firmware as necessary |
||
Conduct a comprehensive review of the machine's documentation and manuals |
||
Annual |
Schedule a professional inspection and maintenance service by qualified technicians |
|
Conduct a thorough examination of the machine's spindle and motor system |
||
Perform a comprehensive inspection of the machine's electrical and electronic components |
||
Verify and update machine backups and software versions |
||
Conduct a detailed examination of the machine's coolant system, hoses, and fittings |
||
Review and update the machine's maintenance schedule and documentation |
||
Ongoing |
Monitor machine performance, including temperature, vibration, and noise levels |
|
Keep a record of maintenance activities, repairs, and any issues encountered |
||
Train operators on basic machine maintenance tasks and best practices |
||
Respond promptly to any abnormal machine behavior or error messages |
||
Stay up to date with manufacturer's recommendations and guidelines |
2. Template for HVAC Systems (Facilities Management)
Image: HVAC Systems (Facilities Management)
Frequency |
Maintenance Task |
Completed? |
Daily |
Check and record the temperature and humidity levels in different zones |
|
Monitor and listen for any unusual noises or vibrations coming from the HVAC system |
||
Check and record the performance of supply and return air fans |
||
Inspect for any signs of water leaks around the HVAC equipment |
||
Verify proper functioning of thermostat settings and controls |
||
Monitor and record any unusual odors or smells in the air |
||
Weekly |
Inspect and clean accessible air filters as needed |
|
Check and clean supply and return air grilles or diffusers |
||
Verify that all vents and registers are open and unobstructed |
||
Check the status of HVAC system control panels and alarms |
||
Verify that the condensate drain lines are draining properly |
||
Test and verify the operation of safety controls and switches |
||
Monthly |
Inspect and clean or replace air filters |
|
Check and clean supply and return air grilles or diffusers |
||
Inspect and clean condensate pans and drains |
||
Verify proper functioning of thermostat settings and controls |
||
Lubricate motors and bearings as recommended by the manufacturer |
||
Inspect and clean fan blades and housing |
||
Quarterly |
Inspect and clean the evaporator and condenser coils |
|
Test and calibrate thermostats for accuracy |
||
Inspect and tighten electrical connections |
||
Check and clean condenser and evaporator fan motors |
||
Inspect and clean outdoor air intakes and louvers |
||
Test and verify the operation of safety controls and switches |
||
Semi - Annual |
Perform a thorough inspection of ductwork for leaks or damage |
|
Clean and calibrate dampers and valves |
||
Inspect and adjust belt tension, if applicable |
||
Check refrigerant levels and inspect for leaks |
||
Verify proper operation of control valves and actuators |
||
Test and verify the operation of all safety controls |
||
Annual |
Schedule a professional HVAC system inspection and tune-up |
|
Clean and inspect combustion chambers, burners, and heat exchangers |
||
Verify and adjust refrigerant charge as necessary |
||
Inspect and clean economizer systems, if applicable |
||
Test and calibrate control sensors and transmitters |
||
Conduct airflow measurements and adjust dampers if needed |
||
Ongoing |
Monitor HVAC system performance and energy consumption |
|
Keep a record of maintenance activities and inspections |
||
Train facility staff on basic HVAC maintenance tasks |
||
Respond promptly to occupant complaints or HVAC system issues |
||
Stay up to date with manufacturer's recommendations and guidelines |
Maximizing Efficiency with Mobile CMMS that Include Preventive Maintenance Checklists
By utilizing preventive maintenance checklists within a CMMS, organizations can create a structured framework that guides maintenance technicians and operators through critical maintenance tasks. This systematic approach reduces the likelihood that essential maintenance activities are overlooked, minimizing the risk of unexpected breakdowns and costly downtime.
According to a study conducted by Plant Services, 19.8% of time is lost due to waiting for instructions. Having the ability to schedule and track maintenance tasks in real-time, teams can efficiently allocate resources, prioritize work orders, and stay on top of maintenance activities.
CMMS mobile capabilities augment the performance of maintenance teams. Technicians armed with smartphones or tablets can access and update maintenance checklists on the go, eliminating the need for manual paperwork, double entry of data, errors and reducing communication delays. They can instantly view assigned work orders, provide real-time updates on task status, and access crucial equipment documentation or diagrams. The seamless collaboration between field technicians and the CMMS enables faster response times, efficient work execution, and improved productivity.
TABLE OF CONTENTS
Keep Reading
The world of IoT is growing rapidly in almost every aspect of life across a variety of ...
29 Aug 2025
The adoption of Computerized Maintenance Management Systems (CMMS) presents a puzzling ...
28 Aug 2025
For the sake of repetition, a CMMS (Computerized Maintenance Management System) is the hub ...
26 Aug 2025
Too often, production and maintenance departments operate in silos, resulting in a lack of ...
22 Aug 2025
Many organizations struggle with scaling maintenance operations, mainly because some don’t ...
21 Aug 2025
Computerized Maintenance Management Systems (CMMS) have increasingly become the go-to tools ...
19 Aug 2025
It doesn’t seem to matter which energy provider you choose; the bottom line is that energy ...
15 Aug 2025
In FDA-regulated industries such as pharmaceuticals, medical devices, biotechnology, and food ...
14 Aug 2025
B2C businesses, such as retail, hospitality, and food service, operate in a highly ...
8 Aug 2025
What happens when your most experienced maintenance leader is planning on retiring, taking 20 ...
7 Aug 2025
Today’s maintenance operations have become more complex and sophisticated. Gone are the days ...
5 Aug 2025
Modern warehouses are instrumental to maintaining the smooth operations of supply chains, ...
1 Aug 2025
Computerized Maintenance Management Systems (CMMS) have proven to be essential tools for ...
31 Jul 2025
Sometimes it feels as if technology is expanding at the speed of light. This is an ...
29 Jul 2025
Data Center downtime can have a huge negative impact ranging from damage to the data center’s ...
25 Jul 2025
Whenever a company introduces a new process or technology, it’s followed by a period of ...
24 Jul 2025
Obsolescence often comes unexpectedly, mainly because little attention is given to the ...
22 Jul 2025
Imagine a world where critical assets run smoothly without unexpected downtime, maintenance ...
18 Jul 2025
Imagine you're going through a compliance audit, and the inspector asks for maintenance ...
10 Jul 2025
Maintenance managers understand that disasters are unpredictable and can have a massive ...
4 Jul 2025