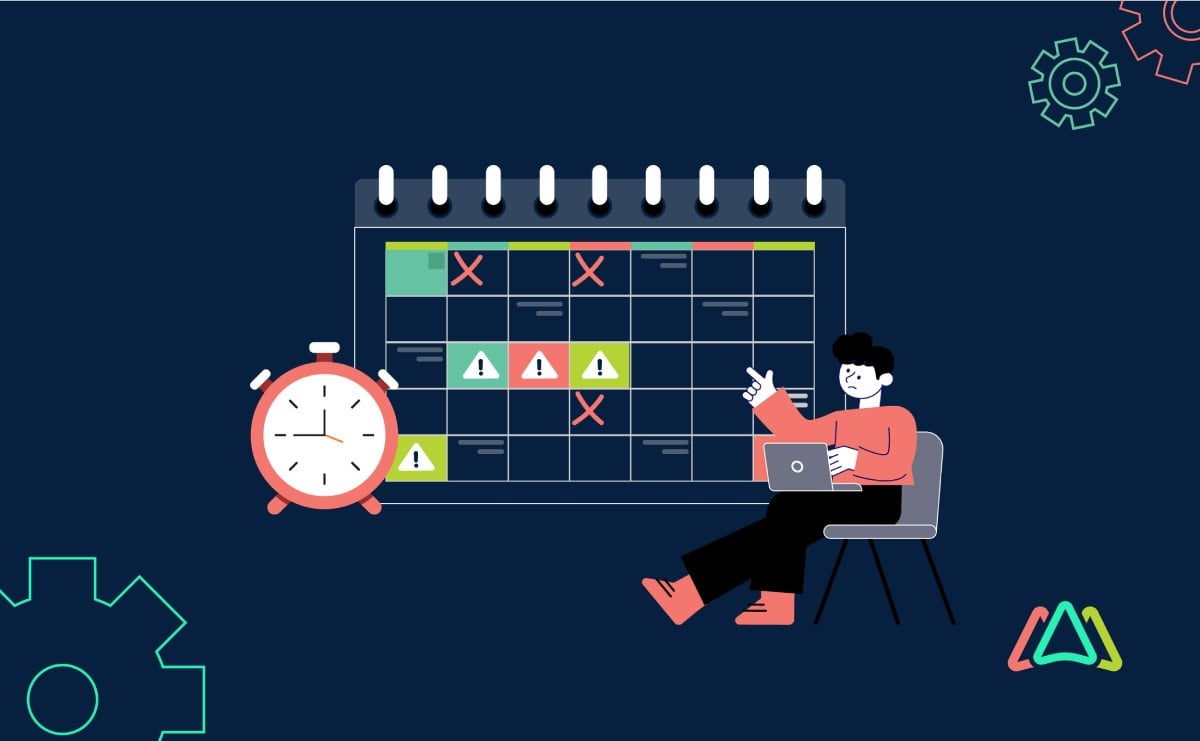
Managing Maintenance Backlogs: Strategies for Efficiency and Effectiveness
Think about all the machines and equipment that keep our world running – from factories making products to hospitals caring for patients. Behind the scenes, there are dedicated teams, the unsung heroes, responsible for making sure these machines work smoothly. We call it maintenance operations, and it’s a big deal.
But here's the catch – even in the best-run operations, you’ll almost always find a Maintenance Backlog.
What is a Maintenance Backlog?
A maintenance backlog is the "to-do" list for maintenance teams. It's a collection of maintenance tasks, repairs, and work orders that have piled up over time and need attention. These tasks range from small repairs to performing critical safety checks. The ‘backlog’ represents a ‘logjam’ or accumulation of work that needs to be completed.
Maintenance backlogs exist in all industries, from manufacturing plants and facilities management to healthcare institutions and transportation services. They arise from a multitude of reasons, including resource constraints, poor planning, inefficient workflows and processes, and unexpected breakdowns. In essence, they represent the gap between the maintenance work that needs to be done and the resources available to do it.
Types of Maintenance Backlogs
1. Preventive Maintenance Backlog
Preventive maintenance backlogs consist of tasks that are planned in advance to prevent equipment failures or performance degradation. These tasks are typically scheduled at regular intervals and aim to keep machinery and systems in optimal working condition. Common examples include routine equipment inspections, lubrication, and calibration.
2. Corrective Maintenance Backlog
Corrective maintenance backlogs involve tasks that are reactive in nature, addressing issues that have arisen unexpectedly. These tasks are often triggered by equipment breakdowns, malfunctions, or safety concerns. Corrective maintenance is performed to fix problems and restore equipment to its normal operational state.
Components of a Maintenance Backlog
A maintenance backlog is comprised of the following key components:
1. Work Orders
These are requests for maintenance tasks or repairs. Work orders contain details such as the type of work needed, the location, asset information, parts needed, assigned technician or vendor, the priority level, and a description of the problem.
2. Task Descriptions
Each item in the backlog should have a clear and detailed description of what needs to be done. This ensures that maintenance teams understand the scope of work.
3. Priority Levels
Not all backlog items are equally important. Prioritizing tasks based on factors like safety, criticality, and resource availability is important. High-priority items should be addressed first.
4. Resource Requirements
This includes information on the tools, equipment, and materials needed to complete each task. It's essential for planning and allocating resources effectively.
5. Due Dates
Some backlog items might have specific deadlines. For instance, preventive maintenance tasks may need to be completed at regular intervals within a specified timeframe. Critical work should be addressed ASAP.
6. Status
Tracking the status of each backlog item (e.g., pending approval, pending review, in progress, on hold, waiting for parts, completed) helps in monitoring progress and ensuring nothing falls through the cracks.
7. History
Maintaining a historical record of completed backlog items can provide valuable insights into maintenance trends and help in future planning.
8. Cost Estimates
In some cases, it's useful to estimate the cost associated with each task. This helps with budgeting and resource allocation.
A visual representation of a simple maintenance backlog table might look like this:
What Causes Maintenance Backlogs?
Understanding the root causes of maintenance backlogs is the first step towards effective management. Here are some common reasons why maintenance backlogs accumulate:
1. Lack of Resources
One of the primary reasons for maintenance backlogs is the shortage of essential resources. Lack of resources comes in many forms:
- Personnel Shortages: If there aren't enough skilled maintenance technicians to handle the workload, tasks pile up.
- Tools and Equipment: Inadequate access to necessary tools and equipment can slow down maintenance work.
- Materials and Spare Parts: Insufficient supplies can lead to delays as maintenance teams wait for necessary components.
Addressing resource shortages is important to prevent backlogs from growing unchecked.
2. Poor Planning
Effective maintenance requires meticulous planning, and when this planning is lacking, backlogs increase:
- Inadequate Scheduling: Failing to schedule regular maintenance or inspections can lead to unexpected breakdowns and failures that require a shift in resources and disrupts schedules and plans.
- Unclear Procedures: If maintenance protocols are unclear or missing, technicians may not know how to tackle tasks efficiently.
Comprehensive planning and scheduling are essential to ensure that maintenance activities are proactive rather than reactive.
3. Equipment Aging
As machinery and equipment age, they often require more attention and maintenance. Here's how aging equipment contributes to backlogs:
- Increased Breakdowns: Older equipment is more prone to breakdowns, requiring more corrective maintenance.
- Reduced Efficiency: Aging machinery may not perform as efficiently, requiring more frequent adjustments.
Regular inspections and preventive maintenance can mitigate the impact of aging equipment on backlogs.
4. Reactive Maintenance
One of the most significant contributors to maintenance backlogs is the practice of reactive maintenance, where maintenance is only performed when something breaks down. Reactive maintenance leads to:
- Unplanned Downtime: Reactive maintenance often results in unexpected downtime, leading to delays in other tasks.
- Higher Costs: Repairing equipment after a breakdown is usually more costly than planned preventive maintenance.
Shifting from a reactive to a proactive maintenance approach can help prevent backlogs by addressing issues before they become major problems.
Impact of Unmanaged Backlogs
When maintenance backlogs are left unattended, they can have severe repercussions on operations and the bottom line.
1. Increased Downtime
A primary consequence of unmanaged maintenance backlogs is increased downtime. When maintenance tasks are delayed or neglected, the probability of equipment breakdowns rises. This leads to:
- Production Halts: Machinery breakdowns can halt production lines, causing delays and revenue loss.
- Resource Inefficiency: Unplanned downtime forces maintenance teams to shift from planned tasks to emergency repairs, disrupting their schedules.
The longer backlogs go unmanaged, the more downtime an organization is likely to experience, affecting overall productivity.
2. Safety Risks
Unattended maintenance backlogs can introduce various safety risks, including:
- Equipment Malfunctions: Neglected maintenance can lead to equipment malfunctions, potentially causing accidents or injuries.
- Environmental Hazards: In industries like chemicals or energy, equipment failures can result in environmental hazards and regulatory issues.
- Worker Well-being: Unsafe conditions caused by unaddressed maintenance issues can impact the physical and mental well-being of employees.
Managing backlogs isn't just about efficiency; it's about safeguarding the well-being of the workforce and the environment.
3. Increased Costs
While it may seem counterintuitive, unmanaged maintenance backlogs often lead to higher costs in the long run:
- Emergency Repairs: When equipment breaks down unexpectedly, repairs are often more costly compared to planned maintenance.
- Replacement Costs: Neglecting preventive maintenance accelerates equipment wear and tear, resulting in premature replacement of parts, components and equipment.
- Regulatory Penalties: In regulated industries, failing to meet maintenance requirements can result in hefty fines.
By managing backlogs effectively, organizations can control costs by preventing costly breakdowns and extending the lifespan of assets.
Case Study: NHS Maintenance Backlog costs £10 Billion
The NHS (National Health Service) in the United Kingdom had been grappling with a significant maintenance backlog. This backlog involved maintenance and repairs required in NHS facilities, including hospitals and healthcare infrastructure.
The backlog was a result of various factors, including:
- Aging Infrastructure: Many NHS facilities were operating with outdated infrastructure and equipment, which required maintenance and modernization.
- Financial Constraints: The NHS faced budget constraints, making it challenging to allocate sufficient funds for maintenance and repairs.
- Increased Demand: The COVID-19 pandemic placed additional strain on healthcare facilities, increasing the need for maintenance and repairs.
- Prioritization: Critical healthcare services took precedence over maintenance activities, leading to the accumulation of backlog requests, work orders and projects.
According to the Guardian, the NHS would have to spend £10.2bn to bring rundown healthcare facilities and equipment up to standard to assess and clear their maintenance backlogs.
How to Assess Your Maintenance Backlog?
Measuring the Size of the Maintenance Backlog
- Number of Pending Work Orders: Counting the number of pending work orders is a straightforward way to measure the size of your maintenance backlog. Each work order represents a specific task or repair that needs attention. By tracking the number of open work orders, you can assess the volume of work that has accumulated.
- Value of Outstanding Repairs: Another valuable metric for assessing your backlog is the total value of outstanding repairs. This involves attaching a cost estimate to each pending task, including labor, materials, and any other associated expenses. Summing up these cost estimates provides an estimate of the financial impact of the backlog.
Prioritizing Maintenance Tasks
Effectively managing a maintenance backlog requires prioritizing tasks to allocate resources wisely and address the most critical issues first. Here are key factors to consider when prioritizing maintenance tasks:
- Criticality: Task criticality assesses the impact of a maintenance task on overall operations. Critical tasks are those that involve assets where failure or downtime have severe consequences, such as safety hazards, production stoppages, or regulatory violations. Prioritize tasks with higher criticality to mitigate risks.
- Safety: Tasks related to safety concerns, whether for equipment or personnel, should be addressed immediately. Neglecting safety-related tasks can lead to accidents and injuries, and legal ramifications.
- Resource Availability: Assess the availability of necessary resources, including skilled personnel, tools, and materials, when prioritizing tasks. Ensure that you have the resources required to complete the task efficiently. If resources are scarce, prioritize tasks that can be done with the available resources.
Strategies for Managing Maintenance Backlogs with a CMMS
1. Establishing Clear Processes
1.1 Work Order Creation and Management
Clear and efficient work order processes are the foundation of effective backlog management. Implementing a standardized system for creating, tracking, and managing work orders ensures that tasks don’t fall through the cracks. This includes capturing important details such as description, priority, due date, asset details, and resource requirements. Modern Computerized Maintenance Management Systems (CMMS) can help in automating and documenting these processes, making work order management a breeze.
A CMMS streamlines work order creation and management by providing a centralized platform where all work orders can be generated, tracked, and managed from request creation, assignment, to completion. Technicians can easily create, update and close out work orders with all details. Even better, Mobile Apps ensure that techs are notified in real-time and can perform tasks, access files, and log activity in the field.
1.2 Task Assignment and Scheduling
Assigning tasks and scheduling them with a consistent process is important to prevent backlog growth. It's about getting the right work to the right people at the right time. Consider factors like skill level, availability, and task priority when assigning work. Most CMMS software comes with calendar views so managers can assign tasks to techs who are available. You can also create workflows within a CMMS to automate task assignment based on criticality, assets involved and skill set required for specific work.
2. Resource Allocation
2.1 Human Resources
Your maintenance technicians are the unsung heroes of backlog management. Ensure you have the right number of skilled technicians to tackle the workload. Training and skill development programs can also improve their capabilities, making them more efficient in handling tasks. Additionally, cross-training team members can help maintain flexibility during high-demand periods.
CMMS systems maintain a database of employee skills, certifications, and availability. This information helps in assigning the most qualified technicians to specific tasks. It also aids in workforce planning, ensuring that you have the right number of skilled staff to handle maintenance demands.
2.2 Equipment and Tools
Equipping the maintenance team with the right tools and equipment is a must. Inadequate tools can slow down tasks and lead to inefficiencies. Regular maintenance of tools and timely replenishment of consumables like lubricants and spare parts are also important. Make sure your team has access to what they need when they need it.
CMMS systems include inventory management features. This allows organizations to keep track of tools, spare parts, and consumables. When a maintenance task is scheduled, the CMMS can automatically check inventory levels and generate purchase orders for necessary materials, ensuring that technicians have access to the required tools and supplies. A CMMS allows managers to set min and max levels for inventory so when levels are low, notifications for restocking are sent to the right people.
3. Predictive Maintenance
3.1 Condition Monitoring
Why wait for something to break when you can catch issues early? Condition monitoring involves continuously assessing the health of equipment through techniques like vibration analysis, infrared thermography, and ultrasonic testing. This proactive approach helps identify potential problems before they escalate.
Many CMMS platforms can be integrated with IoT sensors. These sensors continuously monitor the condition of equipment. When abnormal readings are detected, the CMMS can automatically generate work orders for further inspection or maintenance, allowing organizations to adopt a more proactive approach to maintenance.
3.2 Data Analytics
Analyzing historical maintenance data can unveil patterns and trends that guide decision-making. Predictive maintenance helps forecast equipment failures, allowing for timely preventive action. Modern maintenance relies heavily on data-driven insights.
CMMS systems collect a wealth of historical maintenance data. Advanced CMMS platforms often include built-in analytics tools or can be integrated with business analytics (BI) software. This enables organizations to analyze maintenance data to identify trends, predict equipment failures, and optimize maintenance schedules for more efficient backlog management.
4. Preventive Maintenance
4.1 Planning Regular Inspections
Scheduled inspections are the backbone of preventive maintenance. Routine checks ensure that equipment is operating within safe parameters. Any anomalies detected can be addressed before they become major issues. Well-documented inspection checklists are key for an effective preventive maintenance program.
CMMS software allows organizations to schedule routine inspections and maintenance tasks at specific intervals. The CMMS can automatically generate work orders for these tasks, ensuring that inspections are conducted on time and documented properly.
4.2 Scheduled Maintenance
Planned maintenance, carried out at specified intervals, can significantly extend the lifespan of equipment and reduce unplanned downtime. Develop comprehensive maintenance schedules that account for the manufacturer's recommendations, equipment usage patterns, and historical performance data.
CMMS platforms excel at managing scheduled maintenance. By entering equipment specifications and manufacturer recommendations, the CMMS can generate maintenance schedules that account for usage patterns and historical performance data. This ensures that preventive maintenance is performed at the optimal times to extend equipment lifespan and reduce downtime.
5. Outsourcing Options
5.1 Contract Maintenance
Contracting maintenance services to specialized firms can be a strategic move. These firms often have expertise in specific equipment or industries, and they can handle routine tasks, freeing up your in-house team for more critical work. It's a way to scale resources when needed.
5.2 Third-party Service Providers
Sometimes, a specific task requires specialized knowledge or equipment. In such cases, leveraging third-party service providers can be cost-effective. These providers can quickly address unique challenges and contribute to backlog reduction.
CMMS systems can facilitate the management of external contractors or service providers:
- Organizations can create work orders specifically for outsourced tasks within the CMMS. They can track the progress of outsourced work and receive real-time updates on completion.
- CMMS can help in managing contracts, tracking expenses, and ensuring compliance with service-level agreements (SLAs).
Best Practices for Clearing Maintenance Backlogs
Clearing maintenance backlogs is an ongoing effort that requires a mix of data-driven decision-making, continuous improvement, and a dedicated workforce.
1. Establishing Key Performance Indicators (KPIs)
- Backlog Size: Begin by quantifying the size of your backlog. Count the number of pending work orders or tasks. This metric provides a clear benchmark for your progress.
- Backlog Value: Evaluate the financial impact of the backlog. Calculate the total cost of outstanding repairs, including labor, materials, and any associated expenses.
- Backlog Aging: Analyze how long each task has been in the backlog. Categorize items based on their age to identify areas requiring immediate attention and those that can be managed over time.
- Completion Rate: Measure the percentage of completed work orders against the total number generated. This KPI reflects your team's efficiency in addressing backlog items.
By tracking these KPIs, you can monitor your progress, identify bottlenecks, and make data-driven decisions to expedite backlog clearance.
2. Continuous Improvement
- Root Cause Analysis: Instead of treating the symptoms, delve deeper to identify the root causes of your maintenance backlogs. Is it due to resource shortages, inefficient processes, or unexpected breakdowns? Implement root cause analysis to tackle these issues at their source.
- Lessons Learned: After successfully clearing a backlog, conduct post-mortems to assess what worked well and what could be improved. Document these lessons learned to refine your backlog management strategies. Continuously adapt and evolve your approach based on these insights.
3. Training and Skill Development
Maintenance teams are the backbone of backlog management, so organizations should invest in their skills and knowledge:
- Ongoing Training: Provide regular training to keep technicians updated on the latest maintenance practices and technologies. Consider industry-specific certifications and courses to improve their expertise.
- Cultivate a Learning Culture: Foster an environment of continuous learning, where team members are encouraged to seek personal and professional development opportunities. Support and reward employees who actively pursue skill development.
- Cross-Training: Cross-train technicians to broaden their skill sets. This ensures that your team remains flexible and capable of handling various tasks, even during staff shortages.
4. Collaboration and Communication
- Cross-departmental Cooperation: Backlogs often transcend departmental boundaries. Foster collaboration between maintenance, operations, and other relevant departments. Establish cross-functional teams to prioritize tasks and resolve issues collectively.
- Regular Updates to Stakeholders: Maintain open lines of communication with stakeholders at all levels. Provide regular updates to senior management, department heads, and maintenance teams. Transparency in reporting helps manage expectations and garner support for backlog reduction initiatives.
Maintenance backlogs can disrupt operations, drain resources, and jeopardize safety. But, as we've explored, there are proven strategies and best practices to effectively address and manage maintenance backlogs. By establishing clear processes, utilizing technology solutions like CMMS, prioritizing tasks, fostering continuous improvement, and promoting collaboration, organizations can tackle backlogs systematically and improve overall efficiency. It's about proactive planning, data-driven decision-making, and a commitment to learning from past experiences.
TABLE OF CONTENTS
Keep Reading
Computerized Maintenance Management Systems (CMMS) have increasingly become the go-to tools ...
19 Aug 2025
It doesn’t seem to matter which energy provider you choose; the bottom line is that energy ...
15 Aug 2025
In FDA-regulated industries such as pharmaceuticals, medical devices, biotechnology, and food ...
14 Aug 2025
B2C businesses, such as retail, hospitality, and food service, operate in a highly ...
8 Aug 2025
What happens when your most experienced maintenance leader is planning on retiring, taking 20 ...
7 Aug 2025
Today’s maintenance operations have become more complex and sophisticated. Gone are the days ...
5 Aug 2025
Modern warehouses are instrumental to maintaining the smooth operations of supply chains, ...
1 Aug 2025
Computerized Maintenance Management Systems (CMMS) have proven to be essential tools for ...
31 Jul 2025
Sometimes it feels as if technology is expanding at the speed of light. This is an ...
29 Jul 2025
Data Center downtime can have a huge negative impact ranging from damage to the data center’s ...
25 Jul 2025
Whenever a company introduces a new process or technology, it’s followed by a period of ...
24 Jul 2025
Obsolescence often comes unexpectedly, mainly because little attention is given to the ...
22 Jul 2025
Imagine a world where critical assets run smoothly without unexpected downtime, maintenance ...
18 Jul 2025
Imagine you're going through a compliance audit, and the inspector asks for maintenance ...
10 Jul 2025
Maintenance managers understand that disasters are unpredictable and can have a massive ...
4 Jul 2025
Asset lifespan is a key concern for executives and maintenance and facility management teams. ...
3 Jul 2025
Your company recently invested funds and time for new CMMS software, and six months later, it ...
1 Jul 2025
As Computerized Maintenance Management Systems (CMMS) become more connected and cloud-based, ...
1 Jul 2025
Edge computing is an innovative technology that enables data to be processed at the source, ...
24 Jun 2025
Facility management has undergone a significant transformation in recent times. Take, for ...
20 Jun 2025