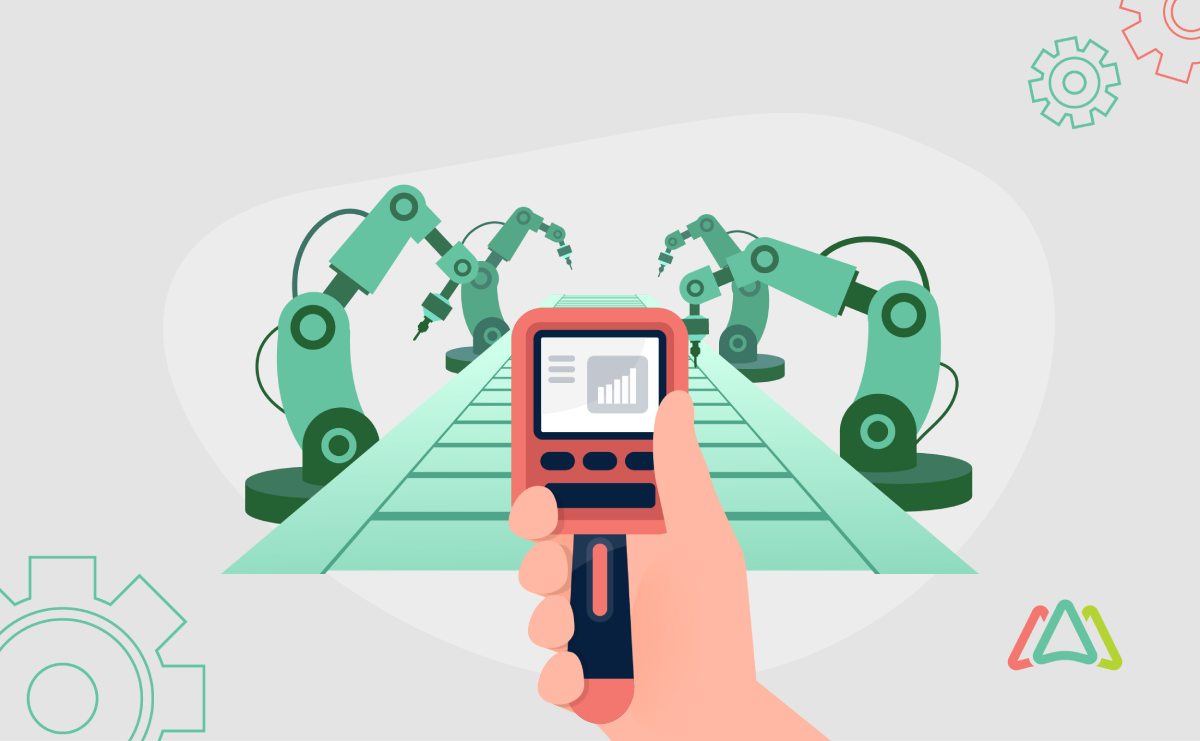
Common Condition Monitoring Techniques
In modern industrial maintenance management, the quest for efficiency and reliability is an endless pursuit. Predictive maintenance, a maintenance management approach that aims to anticipate equipment failures before they occur, has emerged as a game-changer in the industry. At the heart of predictive maintenance lies ‘condition monitoring’ that offers a gateway to a new era of intelligent and data-driven maintenance practices. By continuously monitoring the health of machinery and systems, organizations can go beyond traditional reactive maintenance and embark on a path of predictability and optimization.
Vibration analysis, thermography, oil analysis, ultrasound testing, and other cutting-edge techniques are at the forefront of this transformative journey, each contributing unique capabilities to the arsenal of predictive maintenance. These condition monitoring techniques provide real-time insights into the condition of equipment, enabling maintenance teams to detect early warning signs of faults and address them proactively, ultimately minimizing downtime and maximizing operational efficiency.
Condition Monitoring Technique 1: Vibration Analysis
Vibration analysis is one of the most widely used and effective techniques in condition monitoring. It involves the measurement and analysis of vibrations in machinery to assess its health and detect potential faults. The underlying principle of vibration analysis is based on the fact that all machinery produces vibrations during operation, and these vibrations are reliable indicators about the equipment's condition.
1.1 How Vibration Analysis Works
- Vibration sensors are attached to the machinery at specific areas, capturing vibration data during operation.
- The collected vibration data is then analyzed to identify vibration patterns and frequencies, which are indicative of various machinery conditions.
- Different types of faults, such as misalignment, unbalance, bearing defects, gear wear, and resonance, generate distinct vibration patterns that can be detected and analyzed.
- Advanced vibration analysis techniques use Fast Fourier Transform (FFT) algorithms to convert the time-domain vibration data into frequency-domain spectra, making it easier to identify specific vibration frequencies associated with different faults.
1.2 Where Vibration Analysis is Applicable
- Vibration analysis is commonly applied to rotating machinery, including motors, pumps, compressors, turbines, and fans.
- It is used to assess the condition of bearings, gears, shafts, and other critical components prone to mechanical faults.
- Vibration analysis is valuable in identifying early signs of deterioration and preventing catastrophic failures in industrial equipment.
1.3 Benefits of Vibration Analysis
- Early Fault Detection: Vibration analysis can detect subtle changes in vibration patterns, allowing for the early detection of potential faults, thereby avoiding costly breakdowns.
- Improved Reliability: By identifying and addressing issues before they escalate, vibration analysis improves equipment reliability and performance.
- Predictive Maintenance: Vibration analysis facilitates predictive maintenance, enabling maintenance teams to schedule repairs based on actual equipment condition, optimizing maintenance efforts, and reducing downtime.
1.4 Limitations of Vibration Analysis
- Specialized Training Required: Effective vibration analysis requires skilled personnel with specialized training in data interpretation and fault diagnosis.
- Limited Application for Non-Rotating Equipment: Vibration analysis most often isn’t suitable for non-rotating equipment, such as electrical systems or hydraulic components.
- Environmental Noise Interference: External environmental factors, such as nearby machinery or vibrations, can sometimes interfere with accurate vibration measurements.
1.5 Industry-Specific Use Cases
1.5.1 Oil and Gas Industry
In the oil and gas sector, vibration analysis is employed to monitor critical rotating equipment such as pumps, compressors, and turbines. Continuous monitoring of vibration levels helps detect early signs of mechanical wear, misalignment, and unbalance. By identifying potential issues, maintenance teams can schedule maintenance activities during planned shutdowns, minimizing production downtime and reducing costly repairs.
1.5.2 Aerospace Industry
Vibration analysis is extensively used in the aerospace industry to monitor aircraft engines and other critical components. Monitoring the vibration levels in aircraft engines helps identify potential engine faults or imbalances. This proactive approach allows airlines to address issues before they become critical, ensuring passenger safety and avoiding expensive engine failures.
1.5.3 Mining and Heavy Machinery
In the mining industry, large heavy machinery like excavators, loaders, and haul trucks are subjected to extreme conditions. Vibration analysis is employed to monitor the health of bearings, gears, and other critical components in these machines. By detecting early signs of wear or misalignment, mining companies can reduce unplanned equipment downtime and increase productivity.
1.5.4 Power Generation Plants
Vibration analysis is vital in power generation plants, where turbines, generators, and other rotating equipment are central to operations. Monitoring vibrations in these systems helps identify potential imbalances, misalignments, or mechanical issues. Proactively addressing these faults improves the overall reliability of the power plant and ensures continuous supply of electricity.
1.5.5 Automotive Industry
In the automotive industry, vibration analysis is used to assess the condition of various vehicle components, such as engines, gearboxes, and suspension systems. Monitoring vibrations helps diagnose issues like worn-out bearings or offset components, enabling faster repairs.
1.5.6 Marine and Shipping
Vibration analysis is applied to marine propulsion systems, onboard machinery and equipment, and ship structures. By monitoring vibrations, ship operators can identify propeller imbalances, shaft misalignment, or engine issues. Addressing these problems improves fuel efficiency, reduces maintenance costs, and ensures safe and reliable marine operations.
Condition Monitoring Technique 2: Infrared Thermography
Infrared thermography, often referred to as ‘thermal imaging’, is a non-contact condition monitoring technique that uses infrared cameras to measure and visualize the temperature distribution on the surface of equipment. It is based on the principle that all objects emit infrared radiation based on their temperature. Infrared cameras capture this emitted radiation and convert it into a thermal image, where different colors represent varying temperatures.
2.1 How Thermal Imaging Works
- Infrared cameras detect infrared radiation emitted by the equipment's surface and create thermal images known as thermograms.
- Hotspots, cold spots, or temperature anomalies on the equipment's surface indicate potential issues such as overheating, insulation problems, or cooling inefficiencies.
- The thermal images are analyzed to identify abnormal temperature patterns and anomalies that aren't visible to the naked eye.
2.2 Applications in Predictive Maintenance
Thermography plays a crucial role in predictive maintenance, enabling maintenance teams to proactively identify and address equipment issues. Its applications include:
- Electrical Systems: Infrared thermography is widely used to detect electrical faults, such as loose connections, overloaded circuits, or faulty components. It helps prevent electrical fires and equipment failures.
- Mechanical Equipment: Thermography can detect overheating in bearings, motors, pumps, and gearboxes, signaling potential mechanical faults. Identifying these issues early can prevent costly breakdowns.
- HVAC Systems: In buildings and industrial facilities, thermography is used to assess the performance of heating, ventilation, and air conditioning (HVAC) systems, optimizing energy consumption and identifying duct leaks.
Insulation and Roofing: Thermography is employed to inspect building insulation and roofing systems, helping identify energy losses, water leaks, and areas of poor insulation.
- Steam Systems: In steam pipelines and distribution systems, thermography can detect steam leaks, identifying energy wastage and avoiding potential safety hazards.
2.3 Benefits of Thermography
- Non-Intrusive: Thermography is a non-contact technique, enabling inspections from a safe distance, even during equipment operation.
- Early Fault Detection: It detects anomalies that aren’t visible to the naked eye, allowing for early detection of issues before they escalate.
- Cost-Effective: By preventing unexpected failures and optimizing maintenance schedules, thermography helps reduce downtime and maintenance costs.
2.4 Limitations of Thermography
- Surface-Based Inspection: Thermography is limited to inspecting the surface of equipment, and it may not pick up internal defects or issues.
- Ambient Conditions: Environmental factors, such as ambient temperature, humidity, and reflective surfaces, can affect the accuracy of thermographic readings.
2.5 Industry-Specific Use Cases
2.5.1 Electrical Power Distribution
In electrical substations, thermography is used to inspect high-voltage equipment like transformers and circuit breakers. Hotspots detected on these components can indicate loose connections or faulty components that need immediate attention.
2.5.2 Manufacturing
In manufacturing facilities, thermography is applied to rotating machinery, such as motors and bearings, to identify abnormal temperature patterns that might signal impending failures.
2.5.3 Building Maintenance
In the construction industry, thermography is used for building inspections to assess insulation, identify air leaks, and evaluate the effectiveness of HVAC systems, leading to energy-efficient building operations.
2.5.4 Petrochemical Plants
In petrochemical facilities, thermography is utilized to inspect heat exchangers, steam systems, and storage tanks. Hotspots detected in these systems can indicate leaks, corrosion, or blockages.
Condition Monitoring Technique 3: Oil Analysis
Oil analysis is based on the principle that the condition of lubricating oil is indicative of equipment health. Regular oil sampling and analysis are performed, typically during routine maintenance or at scheduled intervals. The collected oil samples are sent to specialized laboratories for analysis, where various parameters are measured, and results are compared to established standards or previous data.
3.1 How Oil Analysis Works
- Regular oil samples are collected from machinery during routine maintenance or at scheduled intervals.
- These oil samples are sent to specialized laboratories for analysis, where various parameters are measured, including viscosity, Total Acid Number (TAN), Total Base Number (TBN), particle count, wear metals, water content, and additive concentrations.
- The results are compared to established standards or previous data to determine deviations from baseline values.
3.2 Key Parameters Analyzed and Interpretation of Results
Oil analysis involves measuring and interpreting various parameters to assess the oil's condition and the health of the equipment.
3.2.1 Key Parameters
- Viscosity: Measures the oil's thickness, affecting its lubricating ability.
- Total Acid Number (TAN) and Total Base Number (TBN): Indicate the oil's acidity and alkalinity, revealing its potential to neutralize acids.
- Particle Count and Wear Metals: Detect metal particles indicating mechanical wear of components.
- Water Content: Monitors water ingress into the oil, leading to corrosion and reduced lubrication effectiveness.
- Additive Concentrations: Ensures the oil retains its intended properties for performance and protection.
3.2.2 Interpreting the Results
- Significant deviations from established baseline values or recommended limits warrant further investigation and possible maintenance actions.
- Trend analysis over time helps identify changes in oil condition, enabling proactive maintenance planning.
3.3 Benefits of Oil Analysis
- Early Fault Detection: Helps detect equipment issues early, allowing for timely maintenance and preventing costly breakdowns.
- Improved Equipment Reliability: Leads to increased equipment reliability and extended equipment life.
- Proactive Maintenance: Facilitates a proactive approach to maintenance, reducing downtime and minimizing unplanned repairs.
3.4 Limitations of Oil Analysis
- Limited to Oil Condition: Provides insights into oil condition but may not directly detect all equipment issues.
- Expertise Required: Accurate interpretation of results requires trained personnel with expertise in condition monitoring and equipment diagnostics.
3.5 Industry-Specific Use Cases
3.5.1 Aviation Industry
Oil analysis is used for aircraft engines to detect wear, contamination, and potential engine issues, ensuring the safety and reliability of flight operations.
3.5.2 Power Generation Plants
Crucial for transformers, detecting insulation breakdown and identifying potential faults.
3.5.3 Mining and Construction
Monitors the health of engines, hydraulic systems, and gears in heavy machinery, ensuring efficient equipment operation and preventing costly breakdowns.
3.5.4 Marine Industry
Applied to engines, gearboxes, and hydraulic systems, maintaining vessel reliability and performance.
Condition Monitoring Technique 4: Ultrasound Testing
Ultrasound testing is an effective condition monitoring technique that uses high-frequency sound waves to detect and diagnose faults in equipment. It is based on the principle that mechanical defects, such as friction, turbulence, and electrical discharges, emit distinct ultrasonic frequencies that can’t be heard. Ultrasound testing involves the use of specialized ultrasound devices to capture and analyze these ultrasonic signals, allowing maintenance teams to pinpoint equipment issues and prevent failures.
4.1 How Ultrasound Testing Works
- Ultrasound Devices: Ultrasound testing involves the use of specialized ultrasound devices, often called ultrasonic detectors or transducers. These devices generate and receive ultrasonic waves.
- Ultrasonic Waves: To begin the testing process, the ultrasound device generates high-frequency sound waves (ultrasonic waves) typically in the range of 20 kHz to several MHz. These waves are directed towards the equipment or structure being inspected.
- Interaction with Material: The ultrasonic waves travel through the material being inspected, and their behavior is affected by the presence of any flaws or defects. When the waves encounter a defect, such as cracks, voids, leaks, or friction, they are partially reflected back to the transducer.
- Receiving the Reflected Waves: The same ultrasound device that emitted the waves now acts as a receiver. It detects and measures the time taken for the reflected waves to return to the transducer.
- Signal Analysis: The received signals are then analyzed and processed by the ultrasound device's electronics. The device may include software that interprets the signals and displays the results in a visual or audible format.
- Indication of Flaws: Flaws or defects in the material cause changes in the characteristics of the reflected waves. These changes are translated into indications on the display, revealing the presence and location of the flaw.
- Interpretation by the Operator: Trained operators interpret the indications provided by the ultrasound device. The characteristics of the indications, such as amplitude, duration, and location, help determine the type and severity of the detected flaw.
4.2 Where Ultrasound Testing is Applicable
- Leak Detection: Ultrasound testing is widely used to detect and locate gas and other fluid leaks in pipelines, valves, and pressurized systems.
- Bearing Analysis: Ultrasound is used to detect early signs of bearing defects in rotating machinery, such as motors, pumps, and fans.
- Steam Trap Inspection: It helps identify malfunctioning steam traps, which can lead to energy wastage and reduced system efficiency.
4.3 Benefits in Early Fault Detection and Diagnostics
Ultrasound testing as a condition monitoring technique offers numerous benefits especially in early fault detection and diagnostics.
- Early Detection: Ultrasound testing detects minute changes in equipment conditions, allowing maintenance teams to identify faults at an early stage before they escalate into major issues.
- Non-Intrusive: It is a non-invasive technique, allowing inspections to be performed while equipment is in operation, without the need for shutdowns.
- Versatility: Ultrasound testing is applicable to a wide range of equipment and systems, including electrical components, rotating machinery and fluid systems.
- Cost-Effective: Early detection of faults through ultrasound testing helps avoid costly repairs and unplanned downtime, leading to significant cost savings.
4.4 Limitations of Ultrasound Testing
- Requires High Skill Level: Accurate ultrasound analysis requires trained personnel with expertise in interpreting ultrasonic signals and diagnosing equipment issues.
- Limited to Surface Detection: Ultrasound is primarily effective in detecting surface-level defects, and it may not be as reliable for detecting internal faults in equipment.
- Background Noise: Environmental noise can interfere with ultrasound signals, potentially affecting the accuracy of the readings.
4.5 Industry-Specific Use Cases
4.5.1 Manufacturing Industry
In manufacturing plants, ultrasound testing is used for preventive maintenance of critical equipment, such as pumps, motors, and compressors. It detects bearing defects, air and gas leaks, and electrical anomalies, ensuring smooth production operations.
4.5.2 Power Generation Plants
In power plants, ultrasound testing is applied to detect steam and gas leaks in turbines, boilers, and condensers. Early detection of leaks helps optimize energy efficiency and prevent equipment damage.
4.5.3 Petrochemical Industry
In petrochemical facilities, ultrasound testing is utilized for leak detection in pipes, valves, and pressure vessels. Early identification of leaks minimizes product loss and reduces safety risks.
4.5.4 Food and Beverage Industry
In the food processing sector, ultrasound testing is used for quality control and to detect leaks in pressurized systems, ensuring compliance with food safety regulations and minimizing product wastage.
The digital age is here and condition monitoring is part of its evolution. Forward thinking companies that want to strengthen their competitive advantage should look to condition monitoring as a viable business strategy. By investing in state-of-the-art data collection and analytical tools, businesses can harness the power of advanced analytics and machine learning and up their game and take their maintenance management operations to the next level.
Beyond the tangible benefits is the intangible value that truly sets condition monitoring apart from traditional maintenance management strategies. The peace of mind knowing that potential failures are detected before they disrupt operations, the confidence in meeting production targets without unexpected delays, and the knowledge that workplace safety is prioritized are all benefits that aren’t easy to quantify and put a price tag on, but need to be considered.
TABLE OF CONTENTS
Keep Reading
Computerized Maintenance Management Systems (CMMS) have increasingly become the go-to tools ...
19 Aug 2025
It doesn’t seem to matter which energy provider you choose; the bottom line is that energy ...
15 Aug 2025
In FDA-regulated industries such as pharmaceuticals, medical devices, biotechnology, and food ...
14 Aug 2025
B2C businesses, such as retail, hospitality, and food service, operate in a highly ...
8 Aug 2025
What happens when your most experienced maintenance leader is planning on retiring, taking 20 ...
7 Aug 2025
Today’s maintenance operations have become more complex and sophisticated. Gone are the days ...
5 Aug 2025
Modern warehouses are instrumental to maintaining the smooth operations of supply chains, ...
1 Aug 2025
Computerized Maintenance Management Systems (CMMS) have proven to be essential tools for ...
31 Jul 2025
Sometimes it feels as if technology is expanding at the speed of light. This is an ...
29 Jul 2025
Data Center downtime can have a huge negative impact ranging from damage to the data center’s ...
25 Jul 2025
Whenever a company introduces a new process or technology, it’s followed by a period of ...
24 Jul 2025
Obsolescence often comes unexpectedly, mainly because little attention is given to the ...
22 Jul 2025
Imagine a world where critical assets run smoothly without unexpected downtime, maintenance ...
18 Jul 2025
Imagine you're going through a compliance audit, and the inspector asks for maintenance ...
10 Jul 2025
Maintenance managers understand that disasters are unpredictable and can have a massive ...
4 Jul 2025
Asset lifespan is a key concern for executives and maintenance and facility management teams. ...
3 Jul 2025
Your company recently invested funds and time for new CMMS software, and six months later, it ...
1 Jul 2025
As Computerized Maintenance Management Systems (CMMS) become more connected and cloud-based, ...
1 Jul 2025
Edge computing is an innovative technology that enables data to be processed at the source, ...
24 Jun 2025
Facility management has undergone a significant transformation in recent times. Take, for ...
20 Jun 2025