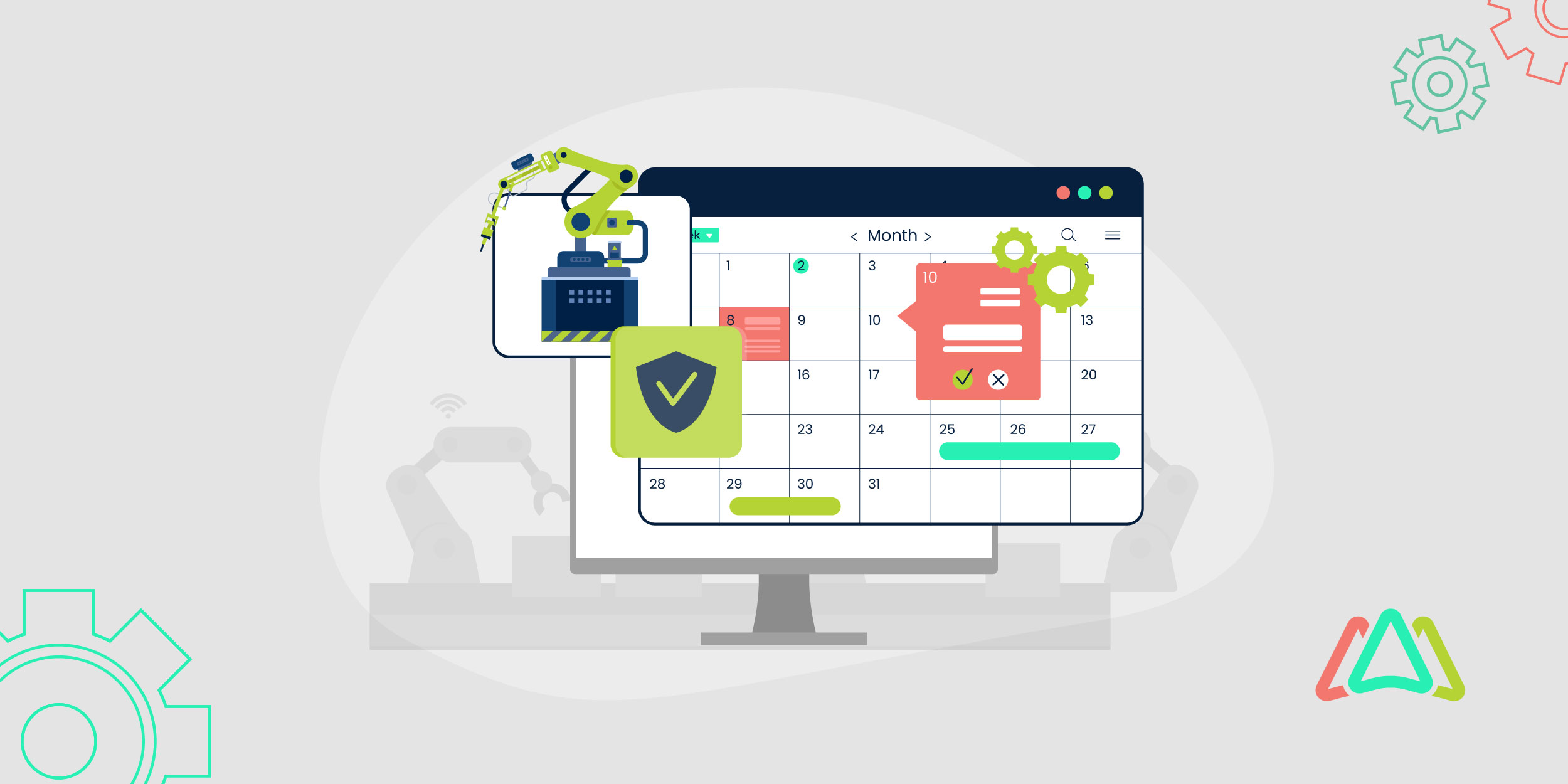
Keep Your Equipment Humming with Preventive Maintenance Compliance!
When was the last time you seriously considered producing a product based on something you felt passionate about?
The conceptual part is just a starting point; putting your passion into action is quite another thing. It is a multi-step process that involves identifying the product, its design, its function, its cost as well as its marketability. Considerable time, energy and resources go into successfully launching any product.
When considering the financial investment required in getting a product off the ground, the sustainability of production assets is often overlooked. Whether you start by using new or used equipment, the cost is considerable. And because your business will depend on them, ensuring that your equipment operates seamlessly is critical.
Your production equipment is the backbone of your business, regardless of your product. With constant use, normal wear and tear are inevitable. Without regular maintenance, equipment breakdowns could occur, often without notice, causing costly repairs and avoidable downtime.
By implementing a system of regular checkups and preventive maintenance on your equipment, you can catch potential problems before they become costly repairs and avoid lengthy downtimes. Your operation will keep running smoothly and your products will continue to be produced without interruption.
But how do you keep a track of this system of routine checkups and maintenance?
Through preventive maintenance compliance.
What is Preventive Maintenance Compliance?
Preventive Maintenance Compliance (PMC) is a crucial maintenance metric that quantifies the extent of adherence to scheduled preventive maintenance schedule, denoting the proportion that has been diligently completed within the stipulated timeframe. PMC provides insights to accurately monitor the efficacy of your regular equipment maintenance schedule, highlighting any potential lag, and thereby aiding in enhancing the reliability and longevity of your assets.
Why is this metric important?
To begin, PM compliance can help you identify areas where you may need to improve your maintenance practices. If your compliance rate is found to be consistently low, it could be a sign that you need to adjust your schedule, improve your communication with maintenance staff, or invest in better equipment that requires less maintenance.
On the other hand, if your compliance rate is high, it’s a sign that your preventive maintenance schedule is working well. A high compliance rate can lead to benefits such as longer equipment lifespan, fewer breakdowns, and increased productivity.
Ultimately, preventive maintenance compliance is a way to measure the effectiveness of your maintenance program. By tracking this metric and striving to improve it over time, you can ensure that your equipment stays in top shape and that your business runs smoothly.
How can you calculate preventive maintenance compliance?
Calculating the preventive maintenance compliance metric is relatively simple.
It involves dividing the number of preventive maintenance tasks completed on time by the total number of scheduled preventive maintenance tasks, and then multiplying the result by 100.
Here's the formula:
Preventive maintenance compliance = (Number of preventive maintenance tasks completed on time / Total number of scheduled preventive maintenance tasks) x 100
By way of an example, consider that over the course of a year, you have scheduled 100 preventive maintenance tasks for your equipment.
Out of those 100 tasks, you complete 90 of them on time. To calculate your preventive maintenance compliance rate, you would use the formula like this
Preventive Maintenance Compliance = (90 / 100) x 100 = 90%
In other words, the above example produced a preventive maintenance compliance rate is 90%.
It's important to note that this calculation only takes into account preventive maintenance tasks that were scheduled in advance. It doesn't take into account any unexpected breakdowns or repairs that occur outside of your regular maintenance schedule.
By tracking your preventive maintenance compliance rate over time, you will be able to identify trends and make adjustments to your maintenance program as needed. For example, if you notice that your compliance rate is consistently low, you may need to schedule maintenance more frequently, and provide additional training to your maintenance staff.
The formula for calculating PM compliance is a simple, but powerful tool for measuring the effectiveness of your maintenance program.
What is considered a “good” Preventive Maintenance Compliance Score?
The answer is not straightforward, as the ideal score can vary depending on factors such as the industry, the type of machinery, and the maintenance program's complexity. However, in general, a preventive maintenance compliance score of 90% is considered good.
Why 90%?
This percentage indicates that the majority of the equipment or machinery has received its scheduled maintenance and repairs, minimizing the risk of unexpected breakdowns and costly repairs. However, businesses can always strive to improve their compliance rate by identifying and addressing any obstacles to proper maintenance, such as scheduling conflicts or a lack of resources.
The goal should be to achieve the highest possible compliance rate. Doing so, not only ensures that the equipment is functioning at its best, but it also leads to improved safety, increased productivity, and reduced downtime.
So, if you're looking to improve your business's preventive maintenance compliance score, start by evaluating your current maintenance program, identifying any gaps or inefficiencies, and implementing a plan to address them. By doing so, you'll be on your way to achieving a "good" and even excellent preventive maintenance compliance score.
Reading the fine print- Limitations of the PMC formula
While PM compliance is a useful preventive maintenance metric for assessing how well your maintenance program is executing planned tasks, it's important to remember that it has its limitations. These too must be considered.
First, the formula only takes into account completed maintenance activities, and does not consider the effectiveness of those activities.
Second, the formula assumes that all maintenance activities are equally important, which may not necessarily be the case. Some maintenance tasks may be more critical to the smooth running of a system than others, and should be given greater weight in the calculation of the PMC score.
Third, the formula does not account for unexpected downtime due to factors outside of maintenance, such as operator error or environmental factors.
One of the main limitations is that it doesn't account for late maintenance which can occur due to various reasons, such as equipment downtime or a lack of available resources.
When preventive maintenance is completed late, it can affect the overall effectiveness of your maintenance program, and the PM compliance formula doesn't provide any insight into this. Specifically, it does not indicate how late a PM task was completed or whether any tasks have become chronically late over time. This means that you may be missing opportunities to improve your maintenance program by identifying and addressing any chronic issues.
How can you mitigate this?
By implementing the golden 10% rule.
Staying compliant with the 10% rule
The rule of 10% is a key component of preventive maintenance compliance and is often used to measure the effectiveness of a maintenance program. It refers to the percentage of preventive maintenance activities that are completed within 10% of the scheduled due date in relation to the PM cadence.
For instance, if a preventive maintenance task is scheduled every 50 days, the 10% rule mandates completing the task within a range of 45-55 days.
However, there is one other issue to be considered.
Take the same example of a 50-day preventive maintenance schedule. You have a leeway of +/- 5 days to finish the maintenance.
Assuming you completed the maintenance early, on the 45th day the last time, you still have some time before the next cycle.
For the next cycle, let’s assume you still have the time, you pick up the maintenance 10 days from now.
The difficulty with this is for the next round, if a problem arises and your team gets busy, it pushes the PM to the end of the cycle. This is illustrated in the following diagram:
Did you notice what happened?
Even though you stayed compliant throughout, your preventive maintenance plan got off track. If problems arose you are left wondering why your equipment keeps breaking down despite a high compliance score. How do you avoid this?
According to Rick Smith’s book, “Preventive Maintenance made Simple”, a company’s PM program should be managed as if it was a controlled experiment.
To control the reliability of your PM program with more accuracy, you've got to control the variables, such as time. Since most PMs are time-based, controlling the variance in your PM schedule can help you make better decisions and in turn, control reliability even better.
Compliance as a competitive edge
Businesses can use the preventive maintenance compliance metric to track the success of their maintenance program by measuring the percentage of completed preventive maintenance tasks within a given time frame. This metric can help businesses identify areas for improvement and optimize their maintenance program. Here are some ways businesses can use the PM compliance metric:
1. Track compliance
The preventive maintenance compliance metric can be used to track the percentage of completed preventive maintenance tasks within a specific time frame. By tracking PM compliance over time, businesses can identify trends and make data-driven decisions to optimize their maintenance program.
2. Identify bottlenecks
Preventive maintenance compliance can help identify bottlenecks in the maintenance process. For example, if a particular piece of equipment consistently has a low PM compliance score, it may indicate that there is an issue with the equipment or that maintenance personnel require additional training.
3. Prepare for audits
PM compliance can help businesses prepare for audits by providing a record of completed preventive maintenance tasks. This can help businesses demonstrate compliance with regulations and industry standards.
4. Fine-tune work order processes
PM compliance can help businesses fine-tune their work order processes by identifying areas where work orders are frequently not completed on time. By addressing the root cause of these delays, businesses can optimize their work order processes and improve PM compliance.
5. Find gaps in maintenance strategy
PM compliance can also help businesses identify gaps in their overall maintenance strategy. For example, if a piece of equipment consistently has a low PM compliance score, it may indicate that the maintenance strategy needs to be revised to better address the needs of that equipment.
By using the preventive maintenance compliance metric, businesses can gain valuable insights into their maintenance program and make data-driven decisions to optimize their operations.
The Maintenance Compliance Checklist
Use the following checklist to ensure that you are staying preventive maintenance compliant:
- Establish a clear preventive maintenance program and communicate it to the team. Plan for regular maintenance activities to ensure that equipment and assets are in good working condition.
- Identify and accurately define (as much as you can) the maintenance tasks that need to be performed.
- Create a schedule for when they should be done. This could include tasks like lubrication, inspection, cleaning, and repair, for example.
- Assign tasks to specific individuals or teams and ensure that they have the necessary skills and resources to perform the tasks.
- Keep track of all maintenance activities and monitor compliance with the preventive maintenance schedule.
- Analyze data on equipment performance to identify trends and potential issues. This could involve tracking equipment downtime, identifying recurring problems, and analyzing data on equipment failures.
- Continuously improve the maintenance program. Use the data collected to make improvements. This could involve updating the maintenance schedule, modifying maintenance procedures, or investing in new equipment.
- Regularly audit the preventive maintenance program to ensure that it is being followed and that compliance is being maintained. This could involve reviewing work orders, conducting equipment inspections, and evaluating performance data.
Can Preventive Maintenance Software help in staying compliant?
Preventive maintenance software can help you keep track of your PM schedule, automatically generate work orders, and track compliance. The software allows you to set up your PM schedule in advance, so you can ensure your equipment is being serviced on time. It also allows you to track compliance by providing you with reports on the status of each PM task, including which ones were completed on time and which ones were missed.
The following are some benefits of using preventive maintenance software to track and improve preventive maintenance compliance:
1. Streamlined and automated maintenance processes
With preventive maintenance software, you can streamline your maintenance processes by automating tasks such as work order generation, scheduling, and task assignment through work order workflows.
2. Real-time data
The software allows you to access real-time data on the status of your equipment, enabling you to make informed decisions quickly.
3. Improved compliance
By using the software to track compliance, you can ensure that all preventive maintenance tasks are being completed on time and that your equipment is operating at peak performance.
4. Improved cost management
By identifying and resolving issues early, you can avoid costly repairs or replacements, resulting in better cost management.
To maximize the benefits of preventive maintenance software, it is important to select the right software for your business needs. Look for software that provides features such as work order management, scheduling, asset management, and compliance tracking.
Uninterrupted operations with preventive maintenance compliance
Preventive maintenance compliance is an essential aspect of any business that relies on equipment and machinery to function. By implementing a PM program and regularly tracking compliance, businesses can reduce downtime, increase reliability, save money, and prepare for audits.
By incorporating automated PM schedules, using work order workflows, and utilizing preventive maintenance software, businesses can stay on top of their maintenance needs and ensure their equipment remains in good working order.
For operations, across all production, service and business sectors, keeping equipment maintained through preventive maintenance compliance is a smart and cost-effective way to keep your assets running efficiently and productively.
TABLE OF CONTENTS
Keep Reading
Computerized Maintenance Management Systems (CMMS) have increasingly become the go-to tools ...
19 Aug 2025
It doesn’t seem to matter which energy provider you choose; the bottom line is that energy ...
15 Aug 2025
In FDA-regulated industries such as pharmaceuticals, medical devices, biotechnology, and food ...
14 Aug 2025
B2C businesses, such as retail, hospitality, and food service, operate in a highly ...
8 Aug 2025
What happens when your most experienced maintenance leader is planning on retiring, taking 20 ...
7 Aug 2025
Today’s maintenance operations have become more complex and sophisticated. Gone are the days ...
5 Aug 2025
Modern warehouses are instrumental to maintaining the smooth operations of supply chains, ...
1 Aug 2025
Computerized Maintenance Management Systems (CMMS) have proven to be essential tools for ...
31 Jul 2025
Sometimes it feels as if technology is expanding at the speed of light. This is an ...
29 Jul 2025
Data Center downtime can have a huge negative impact ranging from damage to the data center’s ...
25 Jul 2025
Whenever a company introduces a new process or technology, it’s followed by a period of ...
24 Jul 2025
Obsolescence often comes unexpectedly, mainly because little attention is given to the ...
22 Jul 2025
Imagine a world where critical assets run smoothly without unexpected downtime, maintenance ...
18 Jul 2025
Imagine you're going through a compliance audit, and the inspector asks for maintenance ...
10 Jul 2025
Maintenance managers understand that disasters are unpredictable and can have a massive ...
4 Jul 2025
Asset lifespan is a key concern for executives and maintenance and facility management teams. ...
3 Jul 2025
Your company recently invested funds and time for new CMMS software, and six months later, it ...
1 Jul 2025
As Computerized Maintenance Management Systems (CMMS) become more connected and cloud-based, ...
1 Jul 2025
Edge computing is an innovative technology that enables data to be processed at the source, ...
24 Jun 2025
Facility management has undergone a significant transformation in recent times. Take, for ...
20 Jun 2025