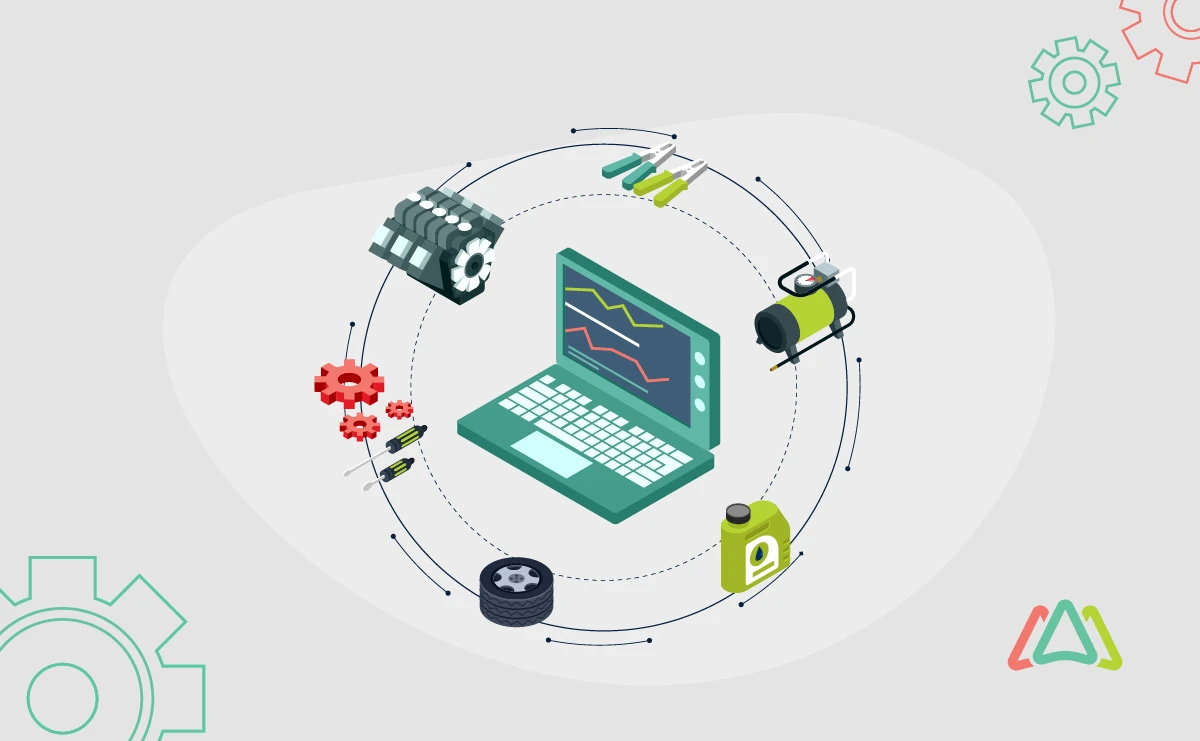
Leveraging a CMMS to Optimize Spare Parts Management
In maintenance, spare parts play an essential role in ensuring the seamless functioning of equipment and minimizing downtime. Spare parts or consumables are critical components that are kept in inventory to address equipment breakdowns or failures promptly. These parts serve as a buffer against unexpected issues, ensuring that maintenance teams can swiftly restore equipment to working condition.
The significance of spare parts extends beyond mere replacements; they are integral to preventive maintenance, minimizing downtime, and extending the lifespan of machinery. Properly managed spare parts inventories contribute to increased equipment reliability, reduced repair times, and, ultimately, enhanced operational efficiency. The effective management of spare parts is not just a logistical necessity; it is imperative for organizations aiming to maintain operational continuity.
The inadequacies in spare parts management can lead to some pretty significant negative outcomes, including increased downtime, higher maintenance costs, and decreased productivity. Recognizing the critical nature of spare parts within the maintenance ecosystem highlights the need for a sophisticated system to oversee their procurement, utilization tracking, and replenishment. CMMS software fills this gap by improving the spare parts management efficiency of an organization.
A CMMS is designed to facilitate the planning, tracking, and management of maintenance activities. It is a centralized platform that enables maintenance teams to organize and optimize their workflows, leading to improved equipment reliability and reduced downtime.
CMMS software is designed with a variety of critical functionalities for maintenance. These include work order management, preventive maintenance scheduling, inventory control, downtime tracking, and reporting. These features collectively contribute to a more systematic and data-driven approach to managing maintenance operations.
Challenges with Traditional Spare Parts Management
Maintenance management practices that rely heavily on manual record-keeping, paper-based systems, spreadsheets, and reactive approaches often lead to increased downtime, higher operational costs, and challenges in properly maintaining spare parts inventories. Traditional spare parts management approaches often come with the following challenges:
- Limited Visibility: Without a centralized system, tracking and monitoring spare parts across multiple locations is challenging, leading to uncertainties in inventory levels.
- Data Discrepancies: Manual record-keeping is prone to errors, resulting in discrepancies between actual inventory and recorded stock levels, leading to confusion and delays in procurement.
- Inefficient Procurement: Lack of real-time data and forecasting tools makes it difficult to anticipate part needs accurately, resulting in either overstocking or frequent stockouts.
- Downtime Impact: In the absence of a structured system, identifying and procuring critical spare parts during equipment breakdowns is time-consuming, exacerbating downtime and impacting productivity.
- Ineffective Maintenance Planning: Traditional methods often fall short in providing insights into future maintenance needs, hindering the development of effective preventive maintenance strategies.
The Impact of Inefficient Spare Parts Management on Overall Operations
Inefficient spare parts management can have far-reaching consequences on an organization's overall operations:
- Increased Downtime: Inadequate spare parts availability leads to prolonged equipment downtime, affecting production schedules and causing financial losses.
- Higher Maintenance Costs: Reactive maintenance, due to a lack of planned spare parts availability, results in increased repair costs and emergency procurement expenses.
- Reduced Equipment Reliability: Unplanned breakdowns and delays in obtaining spare parts contribute to decreased equipment reliability, affecting the organization's reputation and customer satisfaction.
- Strained Resources: Manual tracking and management of spare parts consume valuable time and resources, diverting attention from more strategic and value-driven activities.
How CMMS Overcomes Traditional Maintenance Challenges
Developed to overcome the limitations of manual and paper-based systems, CMMS transformed the way organizations managed their maintenance processes, including the way maintenance teams managed consumables.
- Centralized Data Repository: CMMS software provides a centralized database for storing information related to equipment, maintenance schedules, and spare parts inventory. This eliminates the disjointed nature of manual systems and enhances visibility across the organization.
- Real-Time Tracking and Reporting: CMMS software introduces real-time tracking and reporting functionalities, enabling maintenance teams to monitor spare parts usage, inventory levels, and equipment performance promptly. This allows maintenance teams to know what’s available, reserved and what parts need to be ordered.
- Preventive Maintenance Planning: CMMS facilitates preventive maintenance planning by allowing organizations to forecast future maintenance needs, including the identification of spare parts required for upcoming tasks. This shift from reactive to proactive maintenance marks a significant leap forward.
- Streamlined Procurement Processes: With features like automated reorder triggers and inventory thresholds, CMMS streamlines procurement processes, ensuring that spare parts are restocked in a timely manner. This eliminates the risk of stockouts and improves overall inventory management.
Learn how to avoid common preventive maintenance planning mistakes.
Key Features and Capabilities of Modern CMMS for Spare Parts Management
Modern CMMS systems come equipped with a range of features and capabilities specifically designed to address spare parts management challenges:
- Comprehensive Spare Parts Catalog: A well-organized catalog within CMMS includes detailed information about each spare part, facilitating easy identification, tracking, and management.
- Automated Reorder Triggers: CMMS can be configured to automatically trigger reorder notifications when spare parts reach predefined levels, ensuring timely restocking and minimizing the risk of stockouts.
- Associating Parts with Equipment: CMMS allows organizations to associate spare parts directly with specific equipment, simplifying the identification of required parts during maintenance tasks.
- Detailed Reporting and Analytics: Robust reporting tools enable organizations to analyze spare parts usage, track historical data, and make data-driven decisions for optimized inventory levels and procurement strategies.
- Integration with Work Order Management: CMMS seamlessly integrates with work order management, allowing maintenance teams to review work order reports to identify parts that fail frequently. This information informs strategic decision-making for preventive maintenance and part replacement. Furthermore, some CMMS allow users to identify preferred vendors keeping costs in check while ensuring there’s a fallback. Lead times can also be documented so that expensive rush orders can be avoided.
Benefits of Implementing CMMS for Spare Parts Management
1. Improved Inventory Accuracy and Visibility
CMMS offers a centralized platform for real-time tracking and reporting on spare parts usage and inventory levels. This comprehensive view provides maintenance teams with accurate and up-to-date information, minimizing the risk of stockouts or overstocking. The ability to generate detailed reports enhances transparency and informed decision-making.
2. Enhanced Preventive Maintenance Planning
CMMS software empowers organizations to shift from reactive to proactive maintenance by forecasting future part requirements for preventive maintenance tasks. Through historical data analysis and predictive algorithms, maintenance teams can anticipate the spare parts needed for upcoming maintenance activities, optimizing planning and reducing the likelihood of unplanned downtime.
3. Streamlined Procurement Processes
CMMS streamlines procurement processes by allowing organizations to set automated reorder triggers and predefined inventory thresholds. When spare parts reach these levels, the system generates alerts, ensuring timely restocking. This proactive approach prevents stockouts, minimizes emergency procurement costs, and fosters a more efficient supply chain. Lead times and preferred suppliers can also be documented in the CMMS, ensuring that parts are ordered when needed and purchased at the best price.
4. Cost Savings through Optimized Spare Parts Usage
CMMS facilitates a strategic approach to spare parts usage by enabling the establishment of associations between specific parts and the equipment they support. This linkage ensures that maintenance teams can easily identify the right spare parts needed for each piece of equipment, reducing the likelihood of errors and minimizing unnecessary purchases. This optimization contributes to significant cost savings over time.
5. Increased Equipment Uptime and Reduced Downtime
CMMS integrates seamlessly with work order management, allowing organizations to review detailed reports on past maintenance activities. By examining these reports, maintenance teams can identify parts that frequently fail or require replacement. This insight enables proactive measures, such as preventive maintenance or the sourcing of more reliable spare parts, contributing to increased equipment uptime and reduced overall downtime.
Best Practices for Effective Spare Parts Management with CMMS
Implementing a Computerized Maintenance Management System (CMMS) is not just about adopting technology; it's about optimizing processes and leveraging the system's capabilities to enhance spare parts management. Following are the best practices to ensure effective spare parts management with CMMS:
1. Establishing a Comprehensive List of Spare Parts
One of the fundamental steps in maximizing the benefits of CMMS for spare parts management is creating a comprehensive spare parts list. This involves:
- Detailed Part Information: Populate the list with detailed information for each spare part, including part numbers (suppliers’ and manufacturers’), descriptions, suppliers, lead times, and relevant technical specifications.
- Equipment Associations: Link each spare part directly to the equipment it supports. This association ensures that maintenance teams can quickly identify and locate the required parts during repairs or preventive maintenance.
2. Setting Reorder Triggers and Inventory Thresholds
To maintain optimal inventory levels and prevent stock-outs or overstocking, it is important to set automated reorder triggers and inventory thresholds within the CMMS:
- Automated Reorder Triggers: Define specific reorder points for each spare part. When inventory levels reach these points, the CMMS triggers automatic reorder notifications, ensuring timely restocking.
- Inventory Thresholds: Establish predetermined minimum and maximum inventory thresholds. This helps prevent excess stock or shortages, promoting an efficient and cost-effective spare parts inventory. Be sure to consider supplier lead times when setting minimum quantities. Typically, the longer the lead time and the more critical the part or asset it's used for, the higher the minimum quantity.
3. Utilizing Data Analytics for Demand Forecasting
Harness the power of data analytics within CMMS to predict future spare parts demands. This involves:
- Historical Data Analysis: Leverage historical usage data to identify patterns and trends in spare parts consumption. Analyze past maintenance activities to anticipate future requirements.
- Predictive Analytics: Implement predictive analytics tools within the CMMS to forecast demand based on equipment performance, seasonality, and other relevant factors. This proactive approach ensures that the right parts are available when needed.
4. Implementing a Structured Maintenance Schedule
A well-structured maintenance schedule ensures that preventive and corrective maintenance activities are planned efficiently. This includes:
- Routine Inspections: Schedule routine inspections to assess the condition of equipment and identify potential issues before they escalate.
- Preventive Maintenance Tasks: Integrate spare parts requirements into preventive maintenance schedules. This proactive planning ensures that the necessary parts are available for scheduled maintenance, reducing downtime.
5. Regular Audits and Performance Evaluations
Continuous improvement is key to effective spare parts management. Regular audits and performance evaluations involve:
- Inventory Audits: Conduct periodic audits of spare parts inventory (or cycle counts) to verify accuracy and identify discrepancies.
- Performance Evaluations: Evaluate the performance of spare parts management processes within the CMMS. Assess the system's effectiveness in meeting organizational goals and make adjustments as needed.
By adhering to these best practices, organizations can reap more benefits from their CMMS. Effective spare parts management leads to higher efficiency, and lower costs, and ensures optimal equipment performance.
TABLE OF CONTENTS
Keep Reading
Computerized Maintenance Management Systems (CMMS) have increasingly become the go-to tools ...
19 Aug 2025
It doesn’t seem to matter which energy provider you choose; the bottom line is that energy ...
15 Aug 2025
In FDA-regulated industries such as pharmaceuticals, medical devices, biotechnology, and food ...
14 Aug 2025
B2C businesses, such as retail, hospitality, and food service, operate in a highly ...
8 Aug 2025
What happens when your most experienced maintenance leader is planning on retiring, taking 20 ...
7 Aug 2025
Today’s maintenance operations have become more complex and sophisticated. Gone are the days ...
5 Aug 2025
Modern warehouses are instrumental to maintaining the smooth operations of supply chains, ...
1 Aug 2025
Computerized Maintenance Management Systems (CMMS) have proven to be essential tools for ...
31 Jul 2025
Sometimes it feels as if technology is expanding at the speed of light. This is an ...
29 Jul 2025
Data Center downtime can have a huge negative impact ranging from damage to the data center’s ...
25 Jul 2025
Whenever a company introduces a new process or technology, it’s followed by a period of ...
24 Jul 2025
Obsolescence often comes unexpectedly, mainly because little attention is given to the ...
22 Jul 2025
Imagine a world where critical assets run smoothly without unexpected downtime, maintenance ...
18 Jul 2025
Imagine you're going through a compliance audit, and the inspector asks for maintenance ...
10 Jul 2025
Maintenance managers understand that disasters are unpredictable and can have a massive ...
4 Jul 2025
Asset lifespan is a key concern for executives and maintenance and facility management teams. ...
3 Jul 2025
Your company recently invested funds and time for new CMMS software, and six months later, it ...
1 Jul 2025
As Computerized Maintenance Management Systems (CMMS) become more connected and cloud-based, ...
1 Jul 2025
Edge computing is an innovative technology that enables data to be processed at the source, ...
24 Jun 2025
Facility management has undergone a significant transformation in recent times. Take, for ...
20 Jun 2025