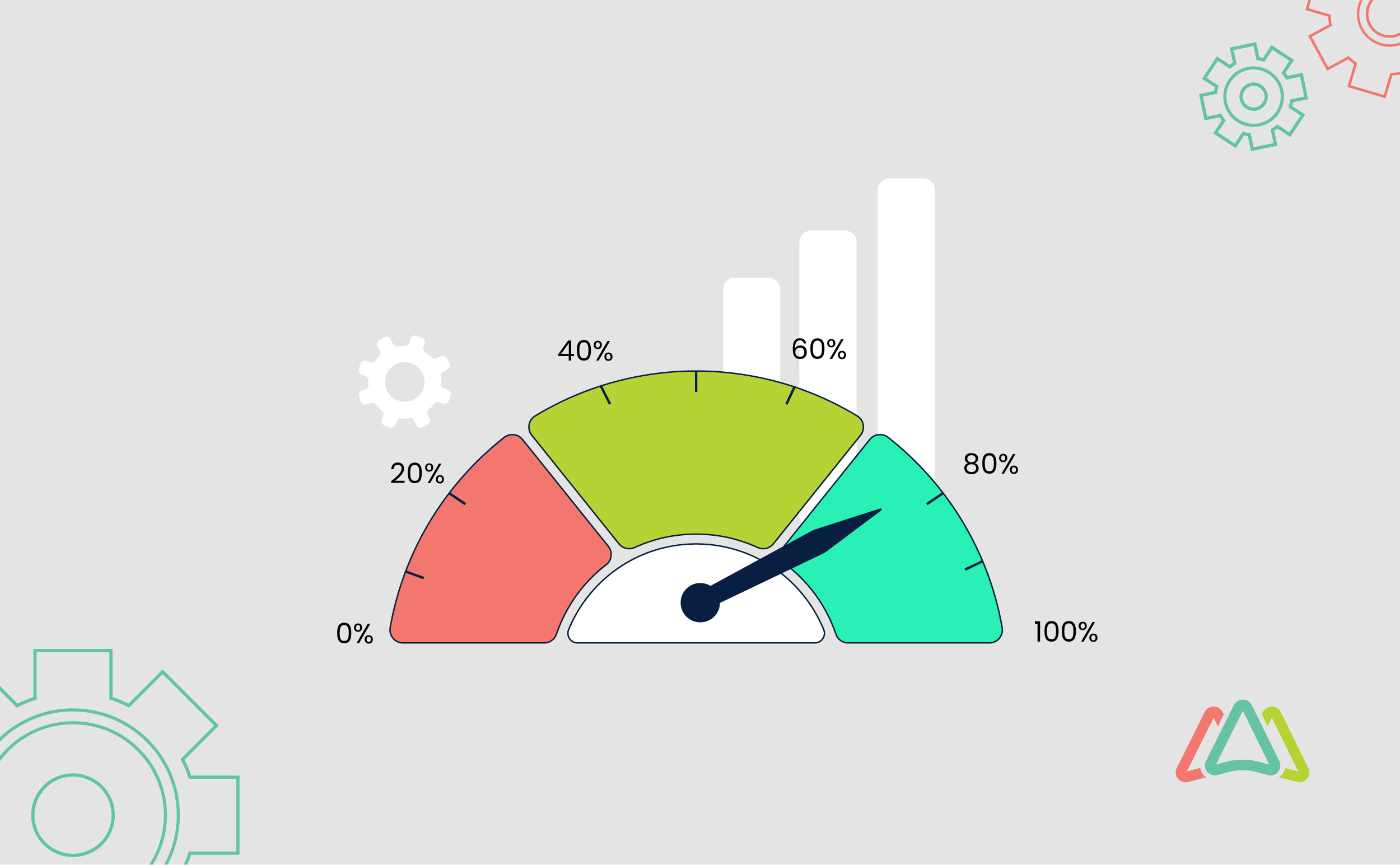
Maintaining a Competitive Edge with Planned Maintenance Percentage
Efficient operations and minimal downtime are vital for businesses across industries. Planned maintenance plays an important role in achieving these objectives. By implementing planned maintenance practices, organizations can anticipate and address maintenance needs before they escalate into costly and disruptive failures.
Planned maintenance percentage reflects the proportion of maintenance efforts that are planned and scheduled in advance, compared to reactive or unplanned maintenance activities. A higher planned maintenance percentage indicates a greater emphasis on proactive maintenance practices which companies should strive for.
Organizations track planned maintenance percentage to assess how effective they are at implementing their planned maintenance strategies. It serves as a performance metric that provides insights into maintenance effectiveness and operational reliability.
What is Planned Maintenance Percentage?
Planned maintenance percentage is a metric that quantifies the proportion of maintenance activities that are planned and scheduled in comparison to the total maintenance efforts performed within a given timeframe. It’s an important indicator of how effective an organization is at managing its maintenance processes and resources.
Planned maintenance involves regular inspections, preventive maintenance tasks, condition-based monitoring, and scheduled repairs. By proactively addressing maintenance needs, businesses can minimize unplanned downtime and unexpected failures which translates in significant cost savings.
Planned Maintenance Percentage Calculation
The formula to calculate planned maintenance percentage is:
Planned Maintenance Percentage = (Planned Maintenance Hours / Total Maintenance Hours) * 100
To obtain the planned maintenance percentage, the total hours dedicated to planned maintenance activities are divided by the total maintenance hours, and the result is multiplied by 100 to express it as a percentage. The higher the percentage the better as it reflects a greater focus on planned maintenance within the overall maintenance efforts.
A higher planned maintenance percentage is what maintenance departments want as it indicates a higher level of preparedness, preventive maintenance, and proactive management. It suggests that maintenance tasks are being scheduled and executed based on predetermined intervals or equipment conditions, resulting in improved equipment reliability, minimized downtime, and optimized asset performance.
Factors Influencing Planned Maintenance Percentage
Understanding the factors that influence the planned maintenance percentage of an organization helps identify areas for improvement and ways to optimize their maintenance practices. Some key factors include:
- Asset criticality: The criticality of assets, equipment, or systems within an organization determines the level of attention and resources allocated to their maintenance. Critical assets often and should receive higher priority for planned maintenance activities, resulting in a higher planned maintenance percentage.
- Maintenance strategy and planning: The organization's maintenance strategy and planning processes play a crucial role in determining the level of emphasis placed on planned maintenance. A proactive approach to maintenance, where preventive and predictive maintenance are used, leads to a higher planned maintenance percentage.
- Maintenance culture and mindset: The culture and mindset within an organization significantly impact the planned maintenance percentage. A culture that promotes proactive maintenance, emphasizes preventive activities, and values regular inspections and condition monitoring is more likely to have a higher planned maintenance percentage.
- Resource availability: The availability of resources, such as skilled maintenance personnel, tools, and spare parts, can influence the ability to plan and execute maintenance activities effectively. Sufficient resources ensure that planned maintenance tasks are scheduled and carried out as intended, contributing to a higher planned maintenance percentage.
- Maintenance data and systems: The utilization of maintenance management systems, such as Computerized Maintenance Management Systems (CMMS), and the effective collection and analysis of maintenance data can positively impact the planned maintenance percentage. These systems enable better planning, scheduling, and tracking of maintenance activities, leading to improved planned maintenance percentages.
Considering these factors and implementing strategies to enhance planned maintenance practices helps organizations increase their planned maintenance percentage and result in benefits like improved asset reliability, reduced downtime, and more efficient operations.
Benefits of Focusing on Planned Maintenance
- Increased equipment reliability: Planned maintenance helps identify potential issues early on and address them before they cause significant disruptions. By adhering to planned maintenance schedules, businesses can optimize the performance and reliability of their equipment, reducing the likelihood of unexpected failures. Consider a power plant that relies on turbines to generate electricity. By implementing a robust planned maintenance program, including regular inspections, lubrication, and component replacements, the power plant minimizes the risk of turbine failures. This ensures a consistent and reliable power supply to the grid, avoiding power outages and potential disruptions to thousands of households and businesses.
- Enhanced productivity: By minimizing unplanned downtime, planned maintenance enables uninterrupted operations, maximizing productivity levels. Well-maintained equipment operates at peak efficiency, resulting in higher output, improved product quality, and streamlined processes. In a busy manufacturing facility, a critical machine is prone to breakdowns due to increased wear and tear. By implementing planned maintenance practices such as scheduled maintenance, timely cleaning, and calibration, the machine's performance and reliability are optimized. This ensures uninterrupted production, eliminates unnecessary downtime, and boosts overall productivity, allowing the company to meet customer demands efficiently.
- Cost savings: Investing in planned maintenance yields significant cost savings in the long run. By preventing major breakdowns and addressing minor issues promptly, businesses avoid expensive emergency repairs and costly production delays. Moreover, planned maintenance helps extend the lifespan of assets, reducing the need for premature replacements. Imagine a fleet management company that operates a large number of vehicles. By adhering to a preventive maintenance program, which includes regular oil changes, tire rotations, and inspections, the company avoids major breakdowns and reduces the risk of costly repairs. This approach extends the lifespan of the vehicles, minimizes the need for premature replacements, and results in substantial cost savings in terms of vehicle maintenance and capital expenditure. In fact, according to a study by Micromain, preventive maintenance not only covers its own costs but also generates an astounding average return on investment of 545%.
- Improved safety: Regular maintenance inspections and repairs carried out as part of planned maintenance contribute to a safer working environment. By identifying and rectifying potential safety hazards, businesses protect their employees by preventing accidents and fostering a culture of workplace safety. Consider a chemical processing plant where safety is of paramount importance. Through planned maintenance, the plant ensures that critical safety systems, such as gas detectors, emergency shutdown systems, and fire suppression equipment, are regularly inspected, tested, and maintained. This proactive approach mitigates the risk of accidents, protects employees and the surrounding community, and maintains compliance with stringent safety regulations.
- Optimized asset management: By tracking and monitoring planned maintenance percentage, businesses gain valuable insights into their asset management practices. This data can guide decision-making related to equipment upgrades, replacements, and resource allocation, ensuring the efficient utilization of assets. Consider a facility management company that tracks its planned maintenance percentage and uses the data to optimize asset management. By analyzing maintenance records and equipment performance metrics, they identify underutilized assets and make informed decisions about equipment upgrades and replacements. This data-driven approach could lead to over 15% reduction in maintenance costs, improved resource allocation, and an increase in overall asset utilization.
Best Practices for Increasing Planned Maintenance Percentage
To improve planned maintenance percentage, organizations should establish a comprehensive maintenance program that covers all aspects of their equipment and assets.
Establish a Comprehensive Maintenance Program
This program ensures that maintenance tasks are planned, scheduled, and executed efficiently. Key elements of this strategy include:
- Develop a maintenance schedule and checklist: Create a detailed maintenance schedule that outlines specific tasks, frequencies, and responsible individuals or teams. This schedule should be based on equipment manufacturer recommendations, industry standards, and historical data. Additionally, develop a comprehensive maintenance checklist that covers all relevant maintenance activities for each piece of equipment.
- Identify critical equipment and prioritize maintenance tasks: Identify the critical equipment that directly impacts production or operational efficiency. Assign a higher priority to these assets and allocate more resources to their planned maintenance. By focusing on critical equipment, organizations can minimize the risk of unplanned downtime and optimize overall performance.
Utilize Condition-Based Maintenance Techniques
Condition-based maintenance (CBM) techniques leverage real-time data and equipment condition monitoring to optimize maintenance activities. By using predictive maintenance technologies and monitoring equipment health, organizations can proactively identify maintenance needs and improve planned maintenance percentage. Key strategies within this approach include:
- Implement predictive maintenance technologies: Utilize technologies such as vibration analysis, thermography, and oil analysis to predict equipment failures. By collecting and analyzing data from these technologies, maintenance teams can identify potential issues and schedule maintenance activities before failures occur.
- Monitor equipment health and performance through sensors and data analytics: Install sensors and monitoring systems on critical equipment to track performance parameters, such as temperature, pressure, or vibration levels. Collect and analyze the data to identify trends, detect anomalies, and make informed decisions about maintenance interventions.
Emphasize Preventive Maintenance Practices
Preventive maintenance is a proactive approach that focuses on regular inspections, lubrication, and component replacements to prevent failures and extend equipment life. By emphasizing preventive maintenance practices, organizations can significantly improve planned maintenance percentage. Key strategies within this approach include:
- Conduct regular inspections, lubrication, and calibration: Implement a schedule of routine inspections to identify potential issues, such as worn-out components, signs of deterioration, or calibration drift. Regular inspections enable early detection of problems, allowing for timely maintenance interventions. Additionally, establish a lubrication program to ensure that equipment is properly lubricated at recommended intervals, preventing friction-related failures. Incorporate calibration checks to verify and adjust equipment settings, ensuring accurate and precise measurements.
- Replace worn-out components before failure occurs: Regularly monitor the condition of critical components, such as belts, bearings, or seals, and replace them based on predetermined criteria, such as wear limits or recommended replacement intervals. By replacing worn-out components, organizations can avoid unexpected failures and extend the life of equipment.
By implementing these strategies, organizations can improve their planned maintenance percentage, enhance equipment reliability, and minimize unplanned downtime.
Train and Empower Maintenance Personnel
- Provide technical training and certifications: Invest in training programs to enhance the skills and knowledge of maintenance personnel. Offer technical training courses and certifications that align with industry best practices and equipment requirements. Empower maintenance teams with the necessary expertise to perform effective planned maintenance tasks.
- Encourage a proactive and safety-focused maintenance culture: Promote a culture of being proactive and encouraging safety within the maintenance department. Emphasize the importance of planned maintenance and highlight its impact on equipment reliability and safety. Encourage maintenance personnel to report potential issues and provide them with the autonomy to take necessary preventive actions.
Collect and Analyze Maintenance Data
- Establish a data-driven approach to maintenance decision-making: Implement systems to collect and store maintenance data, including work orders, maintenance history on assets, and performance metrics. Leverage this data to make informed decisions regarding maintenance priorities, resource allocation, and equipment replacement timelines. Utilize key performance indicators (KPIs) to measure planned maintenance effectiveness and track progress over time.
- Use data analytics to identify trends and optimize maintenance processes: Apply data analytics techniques to analyze maintenance data and identify trends, patterns, and recurring issues. Use this information to optimize maintenance schedules, improve asset reliability, and identify opportunities for efficiency gains. Data-driven insights help organizations fine-tune their planned maintenance strategies for better overall performance.
Continuous Improvement and Feedback Loops
- Regularly review and audit maintenance procedures: Conduct regular reviews and audits of maintenance procedures and practices. Evaluate the effectiveness of planned maintenance activities and identify areas for improvement. Ensure that procedures are up to date, align with industry standards, and reflect the specific needs of the organization. Continuously refine and optimize maintenance processes based on lessons learned and industry advancements.
- Solicit feedback from maintenance teams and incorporate improvements: Encourage maintenance personnel to provide feedback on planned maintenance processes and solicit their suggestions for improvement. Foster a collaborative environment where ideas and insights from the frontline are valued. Actively involve maintenance teams in decision-making and incorporate their feedback to enhance planned maintenance effectiveness. Celebrate successful outcomes and give a shout-out to those that contribute.
Using a CMMS to Track Planned Maintenance Percentage
CMMS software provides valuable features and functionality that enable organizations to track and monitor the planned maintenance percentage effectively. The following are ways a CMMS facilitates tracking planned maintenance percentage:
- Capturing Maintenance Schedules: A CMMS allows users to create and schedule planned maintenance tasks within the system. Maintenance schedules can be set up for specific assets or equipment, defining the frequency and intervals when maintenance should be performed. By capturing and organizing these scheduled tasks, the CMMS provides visibility into the planned maintenance activities and provides insights into how well the maintenance team is performing on meeting timelines and completing tasks.
- Progress of planned maintenance tasks: CMMS software enables the creation and management of work orders for planned maintenance tasks. Each work order represents a specific maintenance task or job, including details such as asset information, maintenance instructions, standard operating procedures, tag and lockout procedures, bill of materials (BOM) and expected completion dates. By tracking and managing these work orders, the CMMS provides insights into the volume and progress of planned maintenance activities.
- Maintenance history and documentation: CMMS systems maintain a comprehensive maintenance history of assets and equipment. This includes records of past planned maintenance tasks, dates of completion, parts used, labor and other costs, and associated documentation such as inspection reports or maintenance logs. By capturing this historical data, the CMMS allows for analysis and reporting on the completion of planned maintenance tasks over time.
- Calculation of planned maintenance percentage: CMMS software offers reporting and analytics capabilities that enable organizations to generate performance reports and metrics related to planned maintenance. These reports include the planned maintenance percentage, showing the ratio of completed planned maintenance tasks to the total number of scheduled tasks within a given time period. By utilizing the reporting features of the CMMS, organizations can track and analyze the planned maintenance percentage and identify trends and patterns to evaluate the effectiveness of their maintenance efforts.
- Tracking planned maintenance percentage: Many CMMS systems allow for the integration and tracking of key performance indicators (KPIs). Organizations can configure the CMMS to capture and monitor metrics specifically related to planned maintenance, such as planned maintenance percentage, adherence to maintenance schedules, or asset uptime. These KPIs provide a clear measure of planned maintenance effectiveness and can be used to track and improve the planned maintenance percentage over time.
To realize the benefits of planned maintenance and maximize the planned maintenance percentage, it is essential for businesses to start evaluating their current maintenance practices and identify areas for improvement. Consider implementing a CMMS to streamline maintenance workflows, track planned maintenance tasks, and gain valuable insights into maintenance performance. And most importantly, promote a culture of continuous improvement.
Standards for Planned Maintenance Percentage
To ensure consistency and effectiveness in planned maintenance practices, various standards and benchmarks have been established. These standards provide guidelines and targets for organizations to measure their planned maintenance percentage and assess their maintenance performance. Some prominent standards for planned maintenance percentage are:
- Industry-specific Standards: Different industries may have their own specific standards for planned maintenance percentage based on their unique operational requirements and equipment characteristics. These standards are developed by industry associations, regulatory bodies, or expert groups. These industry-specific standards take into account factors such as asset criticality, operational demands, and compliance requirements.
- Best Practice Benchmarks: Many organizations use best practice benchmarks to compare their planned maintenance percentage against industry leaders or top performers. These benchmarks are often derived from extensive research, surveys, and studies conducted within the industry. They provide organizations with a reference point to gauge their planned maintenance effectiveness and identify areas for improvement.
According to Reliable Plant, the world-class standard for planned maintenance work is greater than 90%.
- Internal Targets and Goals: Organizations can establish their own internal targets and goals for the planned maintenance percentage. These targets are based on factors such as the organization's maintenance strategy, equipment criticality, and operational objectives. Internal targets provide a framework for measuring planned maintenance effectiveness and enable organizations to track their progress over time.
- Continuous Improvement Principles: While not a specific standard, the principle of continuous improvement is highly relevant to planned maintenance percentage. Organizations are encouraged to continually assess and enhance their planned maintenance processes, striving for incremental improvements. This iterative approach ensures that planned maintenance practices evolve and adapt to changing needs and technologies.
It is important for organizations to align their planned maintenance percentage with relevant standards, benchmarks, and internal goals to ensure they are on track and continuously improving. Regular monitoring, data analysis, and performance reviews help organizations identify gaps and implement corrective measures to achieve or exceed these standards.
Remember, standards are not static; they evolve over time as new technologies and best practices emerge. Stay informed about the latest developments in your industry and adjust your planned maintenance strategies accordingly to meet or exceed the established standards.
TABLE OF CONTENTS
Keep Reading
What happens when your most experienced maintenance leader is planning on retiring, taking 20 ...
7 Aug 2025
Today’s maintenance operations have become more complex and sophisticated. Gone are the days ...
5 Aug 2025
Modern warehouses are instrumental to maintaining the smooth operations of supply chains, ...
1 Aug 2025
Computerized Maintenance Management Systems (CMMS) have proven to be essential tools for ...
31 Jul 2025
Sometimes it feels as if technology is expanding at the speed of light. This is an ...
29 Jul 2025
Data Center downtime can have a huge negative impact ranging from damage to the data center’s ...
25 Jul 2025
Whenever a company introduces a new process or technology, it’s followed by a period of ...
24 Jul 2025
Obsolescence often comes unexpectedly, mainly because little attention is given to the ...
22 Jul 2025
Imagine a world where critical assets run smoothly without unexpected downtime, maintenance ...
18 Jul 2025
Imagine you're going through a compliance audit, and the inspector asks for maintenance ...
10 Jul 2025
Maintenance managers understand that disasters are unpredictable and can have a massive ...
4 Jul 2025
Asset lifespan is a key concern for executives and maintenance and facility management teams. ...
3 Jul 2025
Your company recently invested funds and time for new CMMS software, and six months later, it ...
1 Jul 2025
As Computerized Maintenance Management Systems (CMMS) become more connected and cloud-based, ...
1 Jul 2025
Edge computing is an innovative technology that enables data to be processed at the source, ...
24 Jun 2025
Facility management has undergone a significant transformation in recent times. Take, for ...
20 Jun 2025
A facility maintenance plan is at the core of a facility’s operations. This organized ...
19 Jun 2025
In the early days, preventive maintenance could be done effectively with a trained eye and a ...
17 Jun 2025
Sticky notes fall off, whiteboard grids get wiped, and spreadsheets never beep when a ...
13 Jun 2025
Handing a slice of your maintenance workload to a contractor is less about “giving up ...
12 Jun 2025