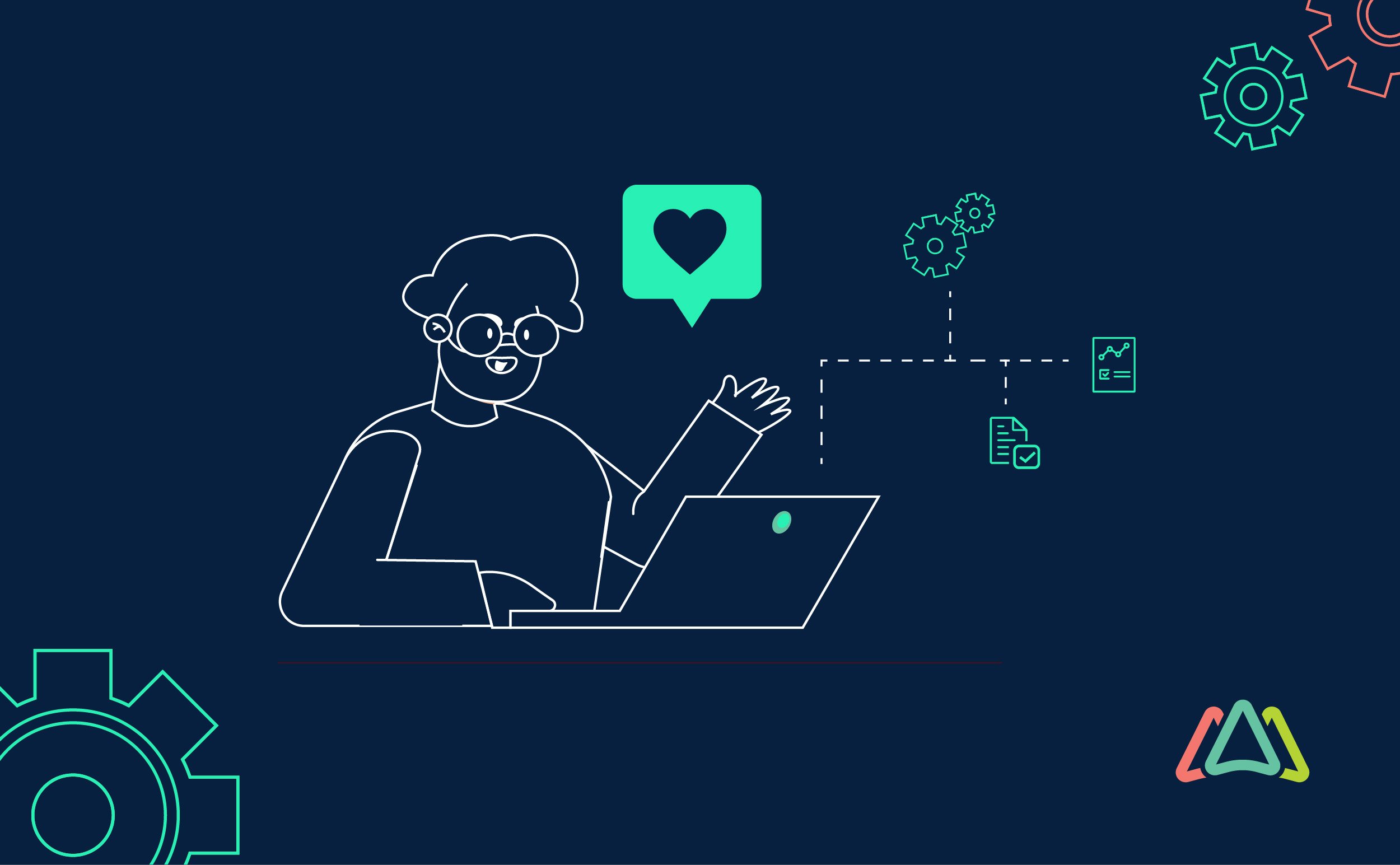
5 Effective Strategies to Improve User Adoption of CMMS Software
In today's fast-paced and technology-driven workplaces, Computerized Maintenance Management Software (CMMS) has become an indispensable tool for streamlining maintenance operations, enhancing productivity, and ensuring the longevity of assets. Since first introduced in the mid 1960s, CMMSs have evolved from its initial math-based systems designed to help document, standardize, and verify manufacturing processes to today’s robust and sophisticated systems capable of managing all facility operations and assets for multiple users maintenance and facilities departments in real time. As proof of CMMSs’ attractiveness to organizations across industry and business sectors, Future Market Insights provided a historical analysis of the global CMMS market and found that it grew at a Compound Annual Growth Rate (CAGR) of 7.0% from 2018 to 2022. It also estimated a growth rate of 9.1% over the next 10 years.
While these are impressive numbers, what they don’t reflect is the high rate of CMMS implementation failure which can range from 50 to 70 percent, depending on the reporting source. One of the primary reasons for the high failure rate is low user adoption. Employees’ resistance to change is a real obstacle for CMMS adoption. So, before getting into the ways business owners can promote user adoption and value CMMS software delivers, let’s examine more closely the reasons for employee resistance to embracing a maintenance management software.
Reasons for Low User Adoption of CMMS Systems
1. Resistance to Change
As is true for most of us, there is comfort in what we already know and what we already do well. This is no different for employees who are comfortable with traditional maintenance management methods that they’ve been doing for years. It makes sense that maintenance staff may be skeptical about the benefits of implementing a CMMS when their company first introduces it.
2. Lack of Familiarity
Employees who are used to working with existing systems and processes may resist change because they feel comfortable and competent with the current process. There is no getting around the learning curve when new technology is brought in. When it comes to a CMMS, employees have to learn new technology, workflows, processes, and hardware. This can be intimidating and overwhelming, especially for those who are not tech savvy.
3. Perceived Lack of Control
When employees are not included in the decision-making process, or do not understand the rationale behind the technology change, they may feel a loss of control over their work environment. This can be incredibly destabilizing and result in resistance to change, as employees value having a sense of autonomy and influence over their work.
4. Disruption to Routines
Change often disrupts established routines and work patterns. Maintenance teams may resist new technology if they believe it will cause disruptions in their daily tasks, leading to temporary productivity declines and increased workload during the transition period.
5. Skepticism about CMMS Benefits
If maintenance staff do not see the immediate tangible benefits of adopting the new technology, resistance to change is likely. They may doubt whether the new technology will truly improve efficiency, productivity, and overall quality or work. Without a clear understanding of the upside, employees may perceive the change as unnecessary, burdensome and not worth the effort in learning.
6. Inadequate Training and Support
Insufficient or inadequate CMMS training and support during the implementation phase of new technology is a recipe for disaster and negatively affects adoption. If employees feel ill-equipped to use the technology or lack access to the necessary resources for learning and troubleshooting, they are likely to resist the change out of frustration or anxiety.
7. Organizational Culture
Some organizations may have a culture that resists change or favors traditional methods. In such environments, employees may resist new technology due to the prevailing norms, attitudes, or resistance from influential individuals or groups within the organization.
8. Fear of Job Loss
Maintenance staff may worry that new technology will automate tasks they currently perform, leading to job redundancy or decreased job security. They may also be concerned about their own ability to adapt to the new technology or acquire the necessary skills to remain valuable in the changing work environment. For some employees, this can be a source of extreme anxiety, and another reason to resist change.
5 Effective Ways to Maximize User Adoption and Value with CMMS Systems
Having identified the key reasons for employee resistance to using a CMMS, the following are actionable strategies organizations can employ to improve user adoption and promote a successful implementation. These strategies enable maintenance departments to leverage their CMMS systems effectively and achieve tangible benefits in a shorter time frame.
1. Define Clear Objectives and Benefits
Start by clearly defining the objectives and benefits of implementing the CMMS system. Communicate these to all stakeholders, emphasizing the positive impact the software will have on their roles and the organization as a whole. By aligning user expectations with the system's capabilities, business owners can generate excitement and enthusiasm for its adoption. Reaching out to all employees through email, texts and posters placed throughout the facility are useful ways of spreading the word while keeping all informed about the process from start to finish.
2. Engage Key Stakeholders
Another way to prevent employee resistance is to involve key stakeholders, including maintenance staff, supervisors, managers, and IT personnel, early in the implementation process. Seek their input, address their concerns, and provide opportunities for early training and collaboration. It’s also a time to identify and prioritize quick wins that demonstrate the immediate value of the CMMS system. By focusing on achievable goals and showcasing anticipated early successes, business owners can increase enthusiasm, build confidence, and encourage broader adoption among users. Once key stakeholders buy-in through their active participation during the early stages of a CMMS introduction, they will be in a better position to confidently promote user adoption, communicate benefits of the technology and ensure a smooth transition.
3. Comprehensive CMMS Training and Onboarding
This is one area where business owners should resist taking shortcuts. Since employee buy-in is essential to a successful CMMS implementation, investing in comprehensive training programs that cover all aspects of the CMMS system's functionality is a must. Consider offering a mix of on-site, virtual, and self-paced training options to accommodate different employee learning styles and schedules. Additionally, provide ongoing support through documentation, FAQs, user forums, and a dedicated support team available to assist users with any questions or challenges they encounter. Consider offering the added capability of mobile access to the CMMS system through dedicated apps. This is another way to reduce employee resistance by inspiring confidence through its real time capabilities. With mobile access, users are able to access and update information or reach out for assistance on the go. This translates into improved productivity, time saved, and a demonstrated CMMS value. Through its user-friendly interface, it becomes easier for users to engage with the system. Finally, continue to maintain open lines of communication with users throughout the implementation, adoption process and beyond. Regularly update employees on system enhancements, new features, and success stories. Encourage users to provide feedback, suggestions, and improvement ideas. Actively incorporate user feedback into system updates and demonstrate that their input is valued and acted upon.
4. Phased Approach to CMMS Implementation
A system launch comes after a lot of planning and hard work. Apart from what’s already been outlined, if an organization has other existing systems such as Enterprise Resource Planning (ERP) systems or equipment monitoring systems, these should be integrated before going live. By taking this important step, it allows for efficient data exchange, automation, and eliminates redundant tasks, making the CMMS system more efficient and valuable to users. When it comes time to roll out the CMMS system company-wide, it’s advisable to conduct a pilot implementation. This means the initial launch is restricted to a specific department or area in a facility. This approach makes it possible to test, refine, and address any issues that may arise on a smaller scale during this process. By fine tuning the system during this pilot phase, it has the benefit of reducing employee frustration that frequently arises from having to deal with nuisance glitches. As a final step, incorporate feedback from pilot users to further fine-tune the system and optimize its usability before expanding the implementation across the organization.
5. Performance Tracking and Incentives
As an ongoing practice, regularly make use of performance tracking mechanisms within the CMMS system to monitor key metrics, such as asset uptime, maintenance response times, and cost savings. The information provided by these checks will provide objective feedback about an organization’s functioning and productivity. It will also provide insights into processes that may need to be refined to improve workflows, resource utilization, preventive maintenance schedules, etc. Share the performance reports with users and teams, while also recognizing and rewarding top performers. By introducing incentives and recognition programs, users will be motivated to consistently use the CMMS as well as recognize the value it offers to their workplace.
Elevate Operational Efficiency with Improved User Adoption
CMMS software offers immense benefits in streamlining maintenance operations, optimizing resource allocation, and reducing downtime. However, organizations often face challenges in achieving successful employee adoption leading to a failure rate in reaping the system's full potential. To overcome these problems and achieve widespread employee adoption of CMMS, a proactive and strategic approach is required. By addressing resistance to change, providing comprehensive training, prioritizing user experience, ensuring compatibility, conducting a stepwise implementation and, providing feedback and acknowledging users, organizations can successfully overcome the challenges associated with CMMS adoption. Introducing this transformative technology using a well-crafted plan will empower employees, enhance operational efficiency, and pave the way for a more efficient and productive process of maintenance planning and scheduling.
TABLE OF CONTENTS
Keep Reading
What happens when your most experienced maintenance leader is planning on retiring, taking 20 ...
7 Aug 2025
Today’s maintenance operations have become more complex and sophisticated. Gone are the days ...
5 Aug 2025
Modern warehouses are instrumental to maintaining the smooth operations of supply chains, ...
1 Aug 2025
Computerized Maintenance Management Systems (CMMS) have proven to be essential tools for ...
31 Jul 2025
Sometimes it feels as if technology is expanding at the speed of light. This is an ...
29 Jul 2025
Data Center downtime can have a huge negative impact ranging from damage to the data center’s ...
25 Jul 2025
Whenever a company introduces a new process or technology, it’s followed by a period of ...
24 Jul 2025
Obsolescence often comes unexpectedly, mainly because little attention is given to the ...
22 Jul 2025
Imagine a world where critical assets run smoothly without unexpected downtime, maintenance ...
18 Jul 2025
Imagine you're going through a compliance audit, and the inspector asks for maintenance ...
10 Jul 2025
Maintenance managers understand that disasters are unpredictable and can have a massive ...
4 Jul 2025
Asset lifespan is a key concern for executives and maintenance and facility management teams. ...
3 Jul 2025
Your company recently invested funds and time for new CMMS software, and six months later, it ...
1 Jul 2025
As Computerized Maintenance Management Systems (CMMS) become more connected and cloud-based, ...
1 Jul 2025
Edge computing is an innovative technology that enables data to be processed at the source, ...
24 Jun 2025
Facility management has undergone a significant transformation in recent times. Take, for ...
20 Jun 2025
A facility maintenance plan is at the core of a facility’s operations. This organized ...
19 Jun 2025
In the early days, preventive maintenance could be done effectively with a trained eye and a ...
17 Jun 2025
Sticky notes fall off, whiteboard grids get wiped, and spreadsheets never beep when a ...
13 Jun 2025
Handing a slice of your maintenance workload to a contractor is less about “giving up ...
12 Jun 2025