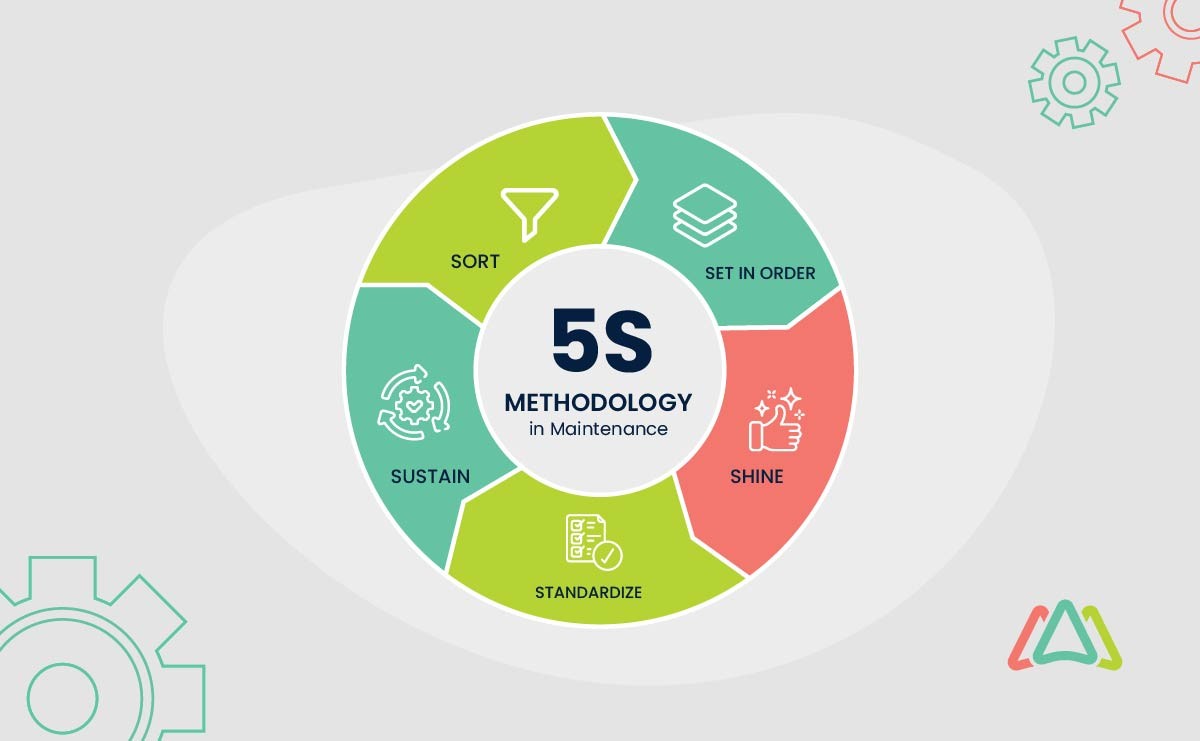
5S in Maintenance: Taking the Principle Beyond Manufacturing
The 5S methodology traces its roots to post-World War II Japan, where it emerged as a key component of the Toyota Production System (TPS). Taiichi Ohno, a Toyota engineer, is often credited with developing the 5S methodology as part of TPS, which later became the foundation for Lean Manufacturing. Over the years, the principles have evolved and transcended their manufacturing origins, finding applications in various sectors, including maintenance.
The 5S methodology has proven to be a transformative approach for organizations seeking efficiency, organization, and continuous improvement. Originating from the Japanese words "seiri," "seiton," "seiso," "seiketsu," and "shitsuke," the 5S principles focus on Sort, Set in Order, Shine, Standardize, and Sustain.
Importance of the 5S Methodology in Maintenance
1. Efficiency and Productivity Improvements
Implementing 5S in maintenance operations leads to streamlined workflows and reduces time wasted. By organizing tools, equipment, and workspaces, maintenance teams can access resources more efficiently, ultimately boosting productivity. This heightened efficiency translates to quicker response times and reduced downtime for equipment maintenance and repairs.
2. Reduction of Waste and Downtime
The 5S methodology targets the elimination of unnecessary items, redundant processes, and inefficient practices. As a result, waste is minimized, and downtime is significantly reduced. This not only optimizes resource utilization but also contributes to cost savings and a more sustainable approach to maintenance operations.
3. Improved Safety and Workplace Organization
A clean and well-organized workplace is inherently safer. The "Shine" principle of 5S emphasizes regular cleaning and maintenance, promoting a hazard-free environment. By adhering to 5S principles, organizations enhance workplace safety, reduce the risk of accidents, and create an organized setting that fosters a sense of order and discipline among maintenance teams.
Understanding the 5S Principles
1. Sort (Seiri) Seiri
The first step in the 5S methodology is "Sort" or "Seiri" in Japanese. This principle revolves around the systematic removal of unnecessary items from the workspace. In the context of maintenance, sorting involves a critical evaluation of tools, equipment, and materials, identifying what is essential for daily operations and what is not. The goal is to create a clutter-free and organized environment where only the necessary items are readily available.
Implementing sorting in maintenance begins with a comprehensive assessment of the tools and materials used in daily tasks. This involves categorizing items into "necessary" and "unnecessary" based on their relevance to the maintenance process. Unnecessary items may include obsolete tools, redundant spare parts, or items that have not been used for an extended period.
Importance of Eliminating Unnecessary Items in Maintenance
The significance of sorting in maintenance cannot be overstated. The benefits of eliminating unnecessary items are:
- Streamlined Workflows: With only essential items at hand, maintenance technicians can work more efficiently, reducing the time spent searching for tools or materials.
- Enhanced Visibility and Accessibility: An organized workspace ensures that necessary tools are easily visible and accessible. This not only speeds up the maintenance process but also minimizes the risk of errors.
- Cost Savings: Removing obsolete or redundant items eliminates the need for storage space and reduces inventory costs. This contributes to overall cost savings for the organization.
- Improved Safety: A clutter-free workspace reduces the likelihood of accidents and injuries. Maintenance areas devoid of unnecessary items create a safer environment for technicians to operate.
2. Set in Order (Seiton) Seiton
The second principle of the 5S methodology, "Set in Order" or "Seiton," focuses on the systematic arrangement of tools, equipment, and workspaces for optimal efficiency. Once unnecessary items have been removed through sorting (Seiri), the goal of setting in order is to establish a logical and structured layout that promotes ease of access, minimizes search time, and enhances overall workflow efficiency.
Seiton involves defining designated locations for each tool and item, ensuring that they are easily visible, accessible, and returnable to their assigned places after use. The aim is to create a visual workplace where anyone can quickly identify the location of tools and materials, contributing to a streamlined and organized environment.
Organizing Tools, Equipment, and Workspaces for Optimal Efficiency
Efficient organization under the Set in Order principle is important for maintaining a smooth and productive workflow in maintenance operations. Key elements include:
- Tool Shadowing: Assigning specific, clearly marked locations for each tool, often outlined by shadows or designated spaces, to enable easy identification and quick retrieval.
- Workflow Zones: Designating specific areas for different types of maintenance tasks, ensuring that tools required for a particular job are conveniently located within the corresponding workspace.
- Visual Labels and Signage: Using visual cues, labels, and signage to clearly mark storage spaces and provide instructions on where tools belong, contributing to a more intuitive and efficient work environment.
- Ergonomic Considerations: Placing frequently used tools and equipment within arm's reach, minimizing unnecessary movements, and optimizing the ergonomic layout of workstations to reduce fatigue and enhance productivity.
3. Shine (Seiso) Seiso
The third principle of the 5S methodology, "Shine" or "Seiso" in Japanese, revolves around the concept of cleanliness and regular maintenance of the workplace. Seiso is not just about tidying up; it emphasizes being proactive and methodical toward keeping the work environment clean to enhance efficiency, safety, and overall morale.
In the context of maintenance, Shine goes beyond merely sweeping floors and dusting surfaces. It involves thorough cleaning of machinery, tools, and workspaces, ensuring that they remain in optimal condition. This proactive cleanliness contributes to the prevention of breakdowns, improves the lifespan of equipment, and fosters a sense of pride and professionalism among maintenance teams.
Importance of Cleanliness in Maintenance Activities
The significance of Shine in maintenance activities extends to various aspects essential for operational success:
- Preventing Equipment Deterioration: Regular cleaning and maintenance prevent the accumulation of dirt, dust, and debris on machinery and equipment. This proactive approach safeguards against corrosion and deterioration, extending the lifespan of assets.
- Improved Safety: A clean and organized workspace is inherently safer. Shine reduces the risk of accidents caused by slipping on spills, tripping over clutter, or working with dirty and malfunctioning equipment. Maintaining a clean environment is a fundamental aspect of ensuring a safe workplace.
- Improving Work Efficiency: Clean and well-maintained tools and equipment operate more efficiently. By incorporating Shine into maintenance practices, organizations can reduce the likelihood of equipment failures, leading to increased operational uptime and efficiency.
- Boosting Morale and Professionalism: A clean and well-maintained workspace creates a positive work environment. Employees are more likely to take pride in their work when surrounded by cleanliness and order, contributing to a culture of professionalism and commitment.
Implementing Regular Cleaning Schedules and Inspections
Implementing Shine in maintenance activities involves the establishment of regular cleaning schedules and inspections:
- Developing Cleaning Checklists: Create comprehensive checklists that outline specific cleaning tasks for each area, equipment, or tool. This ensures a systematic approach and helps maintenance teams stay organized during cleaning activities.
- Assigning Responsibilities: Clearly define roles and responsibilities for cleaning tasks. Assign specific team members or shifts to handle designated cleaning duties, ensuring accountability and a consistent approach to cleanliness.
- Integrating Cleaning into Daily Routines: Make cleanliness a part of the daily routine by incorporating short, focused cleaning activities into shift transitions or work breaks. This helps maintain a consistently clean and organized environment without disrupting overall workflow.
- Conducting Regular Inspections: Schedule regular inspections to assess the effectiveness of cleaning practices and identify areas for improvement. Inspections ensure that cleanliness standards are maintained and provide opportunities for continuous improvement in maintenance processes.
4. Standardize (Seiketsu) Seiketsu
The fourth principle of the 5S methodology, "Standardize" or "Seiketsu" in Japanese, focuses on establishing standardized procedures and practices across the organization. Standardization ensures that the gains achieved through sorting, setting in order, and shining are maintained consistently over time. It involves creating a uniform and systematic approach to tasks, fostering efficiency, reducing variation, and promoting a culture of continuous improvement.
In the context of maintenance, Seiketsu seeks to standardize processes to ensure that best practices are consistently applied. This includes developing standardized maintenance procedures, guidelines, and checklists that contribute to a reliable and predictable maintenance workflow.
Creating Standardized Procedures for Maintenance Tasks
The creation of standardized procedures for maintenance tasks is essential for achieving operational excellence. This involves:
- Documenting Step-by-Step Processes: Clearly document step-by-step procedures for common maintenance tasks. This documentation should include details on tools required, safety precautions, and any specific protocols to be followed.
- Incorporating Industry Best Practices: Utilize industry best practices when developing standardized procedures. This ensures that maintenance tasks are performed in alignment with recognized standards, contributing to the reliability and quality of the work.
- Aligning with Manufacturer Recommendations: Standardized procedures should align with manufacturer recommendations for equipment maintenance. This ensures that maintenance activities not only meet industry standards but also adhere to specific requirements set by equipment manufacturers.
- Considering Safety Protocols: Integrate safety protocols into standardized procedures to ensure that maintenance tasks are performed with the highest regard for the well-being of maintenance personnel and overall workplace safety.
Developing Checklists and Guidelines for Consistent Practices
Standardization is further enhanced through the development of preventive maintenance checklists and guidelines that guide consistent practices:
- Creating Maintenance Checklists: Develop comprehensive checklists that accompany each maintenance procedure. These checklists serve as quick reference guides, ensuring that no steps are overlooked during the execution of maintenance tasks.
- Establishing Inspection Guidelines: Define guidelines for routine inspections, emphasizing key parameters to be monitored. Inspection guidelines contribute to a systematic approach to equipment assessments, reducing the risk of oversight.
- Training Programs for Consistent Practices: Implement training programs to familiarize maintenance teams with standardized procedures, checklists, and guidelines. Training ensures that all team members are on the same page regarding best practices, fostering consistency in execution.
- Continuous Improvement Feedback Loops: Establish feedback loops within the standardization process. Encourage maintenance teams to provide insights and suggestions for improvements to existing procedures, ensuring that standardization is an evolving process that adapts to changing needs.
5. Sustain (Shitsuke) Shitsuke
The fifth and final principle of the 5S methodology, "Sustain" or "Shitsuke" in Japanese, emphasizes the importance of creating a culture of continuous improvement and maintaining the gains achieved through the implementation of the previous four S's. Sustain involves ingraining the 5S practices into the organizational culture, ensuring that they become part of daily routine, not just isolated events. This principle seeks to establish a long-term commitment to excellence and continuous enhancement of processes.
In the context of maintenance, Shitsuke involves sustaining the improvements made in sorting, setting in order, shining, and standardizing. It requires a proactive and ongoing effort to ensure that the 5S practices are ingrained and habitual with maintenance teams.
Emphasizing the Need for Continuous Improvement
Sustaining the 5S practices involves a commitment to continuous improvement:
- Regular Audits and Assessments: Conduct regular audits and assessments to evaluate the effectiveness of 5S practices in maintenance. This ensures that standards are maintained and provides opportunities to identify areas for improvement.
- Feedback Loops and Employee Involvement: Establish feedback mechanisms to encourage input from maintenance teams. Employee involvement fosters a sense of ownership and empowers teams to suggest improvements or adjustments to existing 5S practices.
- Key Performance Indicators (KPIs): Define maintenance KPIs for efficiency, safety, and organization. Regularly monitor KPIs and use the data to identify trends, successes, and areas for improvement within the sustained 5S practices.
- Adaptability to Change: Encourage adaptability to change within the organization. As equipment, processes, and technologies evolve, the sustained 5S practices should be flexible enough to accommodate new challenges and opportunities.
Training Programs and Cultural Changes to Sustain 5S Practices in Maintenance
Achieving sustainability requires a combination of training programs and cultural changes:
- Ongoing Training: Implement ongoing training programs to ensure that new hires are indoctrinated into the 5S principles. Regular refresher courses for existing employees help reinforce the importance of sustained practices.
- Leadership Support and Role Modeling: Leadership plays an important role in sustaining 5S practices. Leadership support and role modeling set the tone for the entire organization, emphasizing the value placed on continuous improvement and adherence to 5S principles.
- Recognition and Rewards: Acknowledge and reward individuals and teams that consistently demonstrate adherence to 5S practices. Recognition reinforces positive behavior and contributes to the establishment of a culture that values sustained excellence.
- Communication and Transparency: Maintain open communication channels to keep all stakeholders informed about the benefits and progress of sustained 5S practices. Transparency fosters a sense of accountability and shared responsibility among team members.
- Cultural Integration: Cultivate a culture that views 5S practices as an integral part of daily operations. Integration into the organizational culture ensures that sustained 5S practices become second nature to maintenance teams.
Using a CMMS to Implement the 5S Methodology in Maintenance
The synergies between CMMS capabilities and the principles of 5S – Sort, Set in Order, Shine, Standardize, and Sustain – enable organizations to create a well-organized, streamlined, and continuously improving maintenance environment.
1. Sort (Seiri): Streamlining Asset Management
A CMMS enables activities aligned with the Sort phase, aiding in the identification and elimination of unnecessary items. Through centralized asset management, maintenance teams can systematically categorize tools, equipment, and spare parts, distinguishing between essential and non-essential items. This ensures that only necessary assets are retained, reducing clutter and improving overall efficiency.
CMMS Benefits:
- Categorization and tagging of assets for easy identification.
- Inventory visibility to assess and manage stock levels effectively.
- Automated alerts for obsolete or rarely used items, facilitating timely removal.
2. Set in Order (Seiton): Organizing Workspaces with Precision
The Set in Order principle is enhanced through the organizational capabilities of a CMMS. Workspaces are optimized for efficiency, and tools and equipment are strategically arranged to minimize search times. A CMMS provides a visual representation of work orders, enabling maintenance teams to plan and allocate resources effectively.
CMMS Benefits:
- Visual work order management to guide tool arrangement based on tasks.
- Centralized database for designated locations, reducing time spent locating assets, inventory, and work orders.
- QR code integration for automated asset and inventory tracking and identification.
3. Shine (Seiso): Proactive Maintenance through Regular Inspections
CMMS functionalities contribute to the Shine principle by incorporating preventive maintenance schedules and inspection protocols. Regular cleaning and maintenance tasks are integrated into the system, ensuring that equipment remains in optimal condition, breakdowns are minimized, and safety standards are upheld.
CMMS Benefits:
- Schedule preventive maintenance tasks to keep equipment in top shape.
- Document cleaning procedures within work orders.
- Real-time data on asset conditions, aiding in proactive maintenance.
4. Standardize (Seiketsu): Establishing Uniform Maintenance Practices
Standardizing maintenance practices is a core strength of a CMMS. The system facilitates the creation of standardized procedures, checklists, and guidelines for maintenance tasks, ensuring consistency in execution. By aligning with industry best practices and manufacturer recommendations, organizations elevate the quality and reliability of their maintenance processes.
CMMS Benefits:
- Document and enforce standardized maintenance procedures.
- Develop checklists and guidelines for consistent practices.
- Training programs integrated into the CMMS for onboarding and continuous education.
5. Sustain (Shitsuke): Embedding 5S Practices into the Culture
The Sustain principle relies on continuous improvement and cultural integration of 5S practices. A CMMS supports sustainability by providing tools for ongoing training, regular audits, and adaptability to change. The system serves as a living repository of knowledge, fostering a culture that values and sustains the gains achieved through the 5S methodology.
CMMS Benefits:
- Ongoing training programs integrated into the system.
- Regular audits and assessments with KPI monitoring.
- Cultural integration through leadership support and recognition programs.
The 5S Methodology: from Vision to Reality
Successfully implementing the 5S methodology in maintenance requires a strategic and well-structured approach. Here's a step-by-step guide that organizations can follow:
1. Getting Leadership Buy-In
- Understand the Value Proposition: Begin by clearly articulating the benefits of implementing 5S in maintenance. Highlight the potential improvements in efficiency, safety, and overall operational effectiveness.
- Build Awareness and Education: Provide leadership with comprehensive information about the 5S methodology. Illustrate how it aligns with organizational goals and contributes to a culture of continuous improvement.
- Demonstrate Success Stories: Share case studies and success stories from industries that have successfully implemented 5S. Demonstrating tangible results helps leadership visualize the positive impact on maintenance operations.
- Commit Resources: Ensure that the necessary resources, including time, personnel, and potential investments in tools or technologies like a CMMS, are committed to the 5S initiative.
2. Employee Training and Involvement
- Educate Teams on 5S Principles: Conduct training sessions to familiarize maintenance teams with the core principles of 5S. Ensure that employees understand the benefits and objectives of the methodology.
- Create a Sense of Ownership: Emphasize the importance of every team member's role in the success of 5S implementation. Encourage a sense of ownership and responsibility for maintaining the newly organized and efficient workspace.
- Facilitate Hands-On Workshops: Organize workshops or practical sessions where employees can actively participate in sorting, setting in order, shining, and other 5S activities. This hands-on approach enhances understanding and commitment.
- Encourage Open Communication: Establish channels for open communication and feedback. Encourage employees to share their insights, challenges, and suggestions throughout the implementation process.
3. Setting up Pilot Projects and Evaluating Results
- Identify Pilot Areas: Select specific maintenance areas or departments to serve as pilot projects for 5S implementation. These areas should be representative of the broader maintenance operations.
- Implement 5S Principles: Begin implementing the 5S principles in the chosen pilot areas. Execute sorting, setting in order, shining, and standardizing activities, following the established procedures and checklists.
- Monitor and Evaluate Results: Regularly assess the impact of 5S implementation in the pilot projects. Use key performance indicators (KPIs) to measure improvements in efficiency, safety, and overall organization.
- Gather Feedback and Adjust: Seek feedback from employees involved in the pilot projects. Use this feedback to make adjustments and refinements to the 5S processes, ensuring they align with the unique needs of the maintenance teams.
- Scale Up and Expand: Once the pilot projects demonstrate positive results and the effectiveness of 5S becomes evident, gradually expand the implementation to other maintenance areas and departments. Share success stories to inspire broader adoption.
By following this step-by-step guide, organizations can lay the foundation for a successful 5S implementation in maintenance, fostering a culture of continuous improvement and operational excellence.
TABLE OF CONTENTS
Keep Reading
What happens when your most experienced maintenance leader is planning on retiring, taking 20 ...
7 Aug 2025
Today’s maintenance operations have become more complex and sophisticated. Gone are the days ...
5 Aug 2025
Modern warehouses are instrumental to maintaining the smooth operations of supply chains, ...
1 Aug 2025
Computerized Maintenance Management Systems (CMMS) have proven to be essential tools for ...
31 Jul 2025
Sometimes it feels as if technology is expanding at the speed of light. This is an ...
29 Jul 2025
Data Center downtime can have a huge negative impact ranging from damage to the data center’s ...
25 Jul 2025
Whenever a company introduces a new process or technology, it’s followed by a period of ...
24 Jul 2025
Obsolescence often comes unexpectedly, mainly because little attention is given to the ...
22 Jul 2025
Imagine a world where critical assets run smoothly without unexpected downtime, maintenance ...
18 Jul 2025
Imagine you're going through a compliance audit, and the inspector asks for maintenance ...
10 Jul 2025
Maintenance managers understand that disasters are unpredictable and can have a massive ...
4 Jul 2025
Asset lifespan is a key concern for executives and maintenance and facility management teams. ...
3 Jul 2025
Your company recently invested funds and time for new CMMS software, and six months later, it ...
1 Jul 2025
As Computerized Maintenance Management Systems (CMMS) become more connected and cloud-based, ...
1 Jul 2025
Edge computing is an innovative technology that enables data to be processed at the source, ...
24 Jun 2025
Facility management has undergone a significant transformation in recent times. Take, for ...
20 Jun 2025
A facility maintenance plan is at the core of a facility’s operations. This organized ...
19 Jun 2025
In the early days, preventive maintenance could be done effectively with a trained eye and a ...
17 Jun 2025
Sticky notes fall off, whiteboard grids get wiped, and spreadsheets never beep when a ...
13 Jun 2025
Handing a slice of your maintenance workload to a contractor is less about “giving up ...
12 Jun 2025