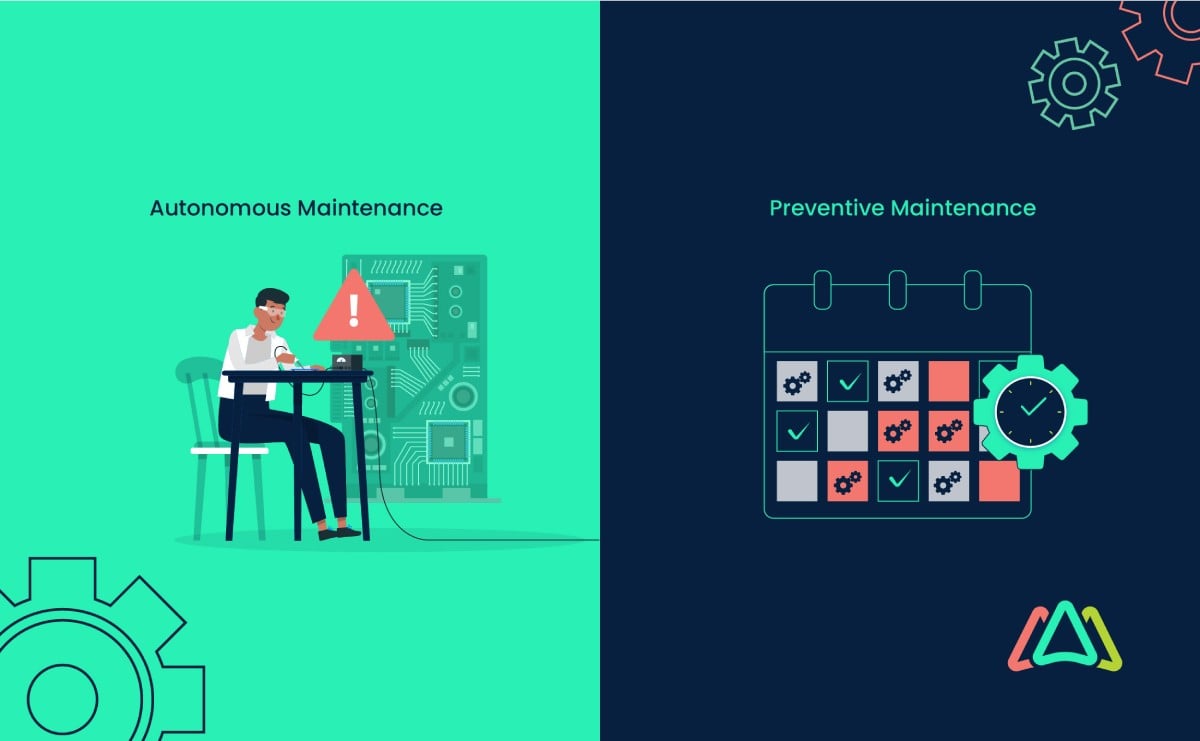
A Deep Dive into Autonomous Maintenance vs. Preventive Maintenance
Maintenance management strategies play a pivotal role in the operational efficiency and longevity of equipment across various industries. These strategies include a spectrum of methodologies designed to ensure the reliability and functionality of equipment. From reactive approaches addressing issues as they arise to proactive measures aimed at preventing failures, the choice of strategy profoundly influences the performance and resilience of industrial systems.
Over the years, two approaches have gained prominence:
- Autonomous Maintenance: Empowering frontline operators to take an active role in maintenance, autonomous maintenance emphasizes routine inspections, defect detection, and proactive interventions. It seeks to reduce dependency on dedicated maintenance teams.
- Preventive Maintenance: In contrast, preventive maintenance involves scheduled tasks, inspections, and part replacements aimed at preventing equipment failures before they occur. This approach aims to extend equipment lifespan, minimize unexpected breakdowns, and streamline maintenance activities through proactive planning.
Understanding the nuances of Autonomous Maintenance and Preventive Maintenance is important for industries seeking to optimize equipment reliability and operational continuity. This article covers the intricacies, advantages, and challenges of these two maintenance philosophies.
Understanding Autonomous Maintenance
Autonomous Maintenance is a proactive maintenance approach that emphasizes empowering frontline operators to take an active role in preserving and enhancing the reliability of equipment. Its core principles revolve around:
- Empowering Operators: Autonomous maintenance seeks to empower operators with the skills and responsibility to conduct routine maintenance tasks. This includes simple inspections, lubrication, and minor repairs, reducing the reliance on specialized maintenance teams.
- Early Defect Detection: The philosophy of autonomous maintenance encourages operators to be vigilant in identifying and addressing potential issues at their earliest stages. By fostering a culture of early defect detection, autonomous maintenance aims to prevent small problems from escalating into major failures.
- Routine Equipment Inspections: Regular inspections become a cornerstone of autonomous maintenance, with operators systematically checking and assessing equipment conditions. These routine examinations are aimed at identifying wear and tear, loose components, or any anomalies that may compromise the equipment's performance.
Benefits of Autonomous Maintenance
Implementing Autonomous Maintenance can yield many benefits for industrial operations:
Increased Equipment Reliability:
By fostering a proactive approach to maintenance, autonomous maintenance contributes to increased equipment reliability. The early detection and resolution of potential issues prevent unplanned downtime and disruptions to production processes.
Reduced Downtime:
The proactive nature of autonomous maintenance minimizes unexpected breakdowns, leading to a reduction in downtime. This enhances overall operational efficiency and allows for more predictable production schedules.
Improved Safety:
With operators actively engaged in equipment maintenance, safety improves. Regular inspections and preventive measures not only contribute to equipment reliability but also create a safer working environment for personnel.
Implementation Challenges and Considerations
While the benefits of autonomous maintenance are substantial, its successful implementation comes with challenges that require careful consideration. These challenges are as follows:
Operator Training and Engagement:
Proper training is essential to ensure that operators are equipped with the skills and knowledge needed for effective maintenance activities. Engaging operators in the process and fostering a sense of ownership is essential for the success of autonomous maintenance.
Balancing Routine Tasks with Autonomous Maintenance Activities:
Operators often have a range of responsibilities beyond maintenance. Balancing routine tasks with autonomous maintenance activities requires careful planning to avoid overburdening operators and ensuring that core production tasks are not neglected.
Measuring and Tracking Success:
Establishing key performance indicators (KPIs) and metrics to measure the success of autonomous maintenance is vital. Tracking improvements in equipment reliability, reduction in downtime, and safety enhancements provides valuable insights for continuous improvement.
Exploring Preventive Maintenance
Preventive Maintenance is a systematic approach to maintenance that involves scheduled tasks, inspections, and part replacements with the goal of preventing equipment failures before they occur. Its key components include:
- Scheduled Maintenance Tasks: Preventive maintenance involves the creation of a maintenance schedule based on manufacturer recommendations, industry standards, and historical data. Routine tasks such as inspections, cleaning, and adjustments are performed at predetermined intervals.
- Replacement of Parts before Failure: A fundamental principle of preventive maintenance is the timely replacement of components that are prone to wear and tear. This proactive approach helps avoid unexpected breakdowns and extends the overall lifespan of equipment.
- Lubrication and Inspections: Regular lubrication of moving parts and comprehensive inspections are integral to preventive maintenance. Lubrication ensures smooth operation and reduces friction, while inspections identify potential issues that may lead to future failures.
Advantages of Preventive Maintenance
Implementing a Preventive Maintenance strategy offers several advantages for industrial operations. The benefits of preventive maintenance are as follows:
Prolonged Equipment Lifespan:
By addressing wear and tear before it leads to failure, preventive maintenance contributes to prolonging the overall lifespan of equipment. This is essential for industries aiming to maximize their return on investment in capital assets.
Reducing Costs over the Long Run:
Despite the upfront costs associated with routine maintenance, the long-term savings can be substantial. Preventing major breakdowns and minimizing the need for emergency repairs contribute to overall cost-effectiveness.
Planned Downtime for Maintenance:
Preventive maintenance allows for the scheduling of maintenance activities during planned downtime, minimizing disruptions to regular production schedules. This planned approach enhances operational predictability.
Drawbacks and Limitations
While Preventive Maintenance offers numerous benefits, it is not without its challenges. These challenges are as follows:
Potential for Over-Maintenance:
The fixed schedule of preventive maintenance tasks may lead to over-maintenance, where components are replaced before reaching the end of their useful life. This can result in unnecessary costs and resource utilization.
Reactive Nature to Potential Failures:
Despite its preventive nature, preventive maintenance can be somewhat reactive. It relies on predetermined schedules rather than real-time data, which may not account for sudden changes in equipment conditions. Issues can occur due to unplanned asset conditions that fixed interval maintenance didn't account for. Preventive maintenance strategies often struggle with predicting the actual condition of equipment. Unexpected failures can occur between scheduled maintenance intervals, especially in rapidly changing operational environments.
Comparative Analysis
1. Cost-Effectiveness
Initial Investment vs. Long-Term Savings:
Autonomous maintenance and preventive maintenance differ in their cost structures. Autonomous maintenance may require significant initial investments in operator training and engagement programs. However, the long-term savings stem from reduced reliance on specialized maintenance teams and minimized downtime. On the other hand, preventive maintenance involves consistent investments in spare parts and routine maintenance tasks, aiming for long-term cost-effectiveness through the prevention of major breakdowns.
Autonomous Maintenance's Focus on Labor vs. Preventive Maintenance's Emphasis on Spare Parts:
Autonomous maintenance places a significant emphasis on utilizing existing labor resources effectively. Operators actively engage in maintenance activities, focusing on skill development and routine inspections. In contrast, preventive maintenance leans towards the investment in spare parts, with a focus on replacing components before failure. The cost-effectiveness of each approach depends on the specific industry, equipment types, and overall operational context.
2. Downtime and Operational Efficiency
Impact on Production Schedules:
Downtime is a critical factor in assessing the effectiveness of maintenance strategies. Autonomous maintenance's proactive nature, with operators continuously monitoring and addressing issues, minimizes unplanned downtime, contributing to enhanced operational efficiency. Preventive maintenance, while planned, may still result in downtime during scheduled maintenance, impacting production schedules. The balance between planned downtime for maintenance and uninterrupted production is essential for overall efficiency.
Balancing Proactive and Reactive Maintenance:
Both autonomous maintenance and preventive maintenance strategies aim to strike a balance between proactive and reactive maintenance. Autonomous maintenance, with its focus on early defect detection and immediate intervention, leans heavily towards proactive maintenance. Preventive maintenance, by its nature, is more proactive than reactive, but the fixed schedules may result in reactive responses to unforeseen issues. The effectiveness of each approach depends on the industry's tolerance for unplanned downtime and the criticality of continuous production.
3. Flexibility and Adaptability
Autonomous Maintenance's Ability to Adapt to Changes in Production:
One of the strengths of autonomous maintenance lies in its adaptability to changes in production processes. Operators, being on the frontline, can quickly adapt maintenance activities to accommodate shifts in production requirements or changes in equipment configurations. This flexibility is particularly advantageous in dynamic industrial settings where production lines evolve.
Preventive Maintenance's Rigid Scheduling and Potential Inflexibility:
Preventive maintenance, due to its fixed schedules, may face challenges in adapting to rapid changes in production demands. The rigid nature of preventive maintenance schedules can result in potential inflexibility, especially in industries with frequent shifts in production priorities. Adjusting schedules to accommodate unexpected changes may be a logistical challenge.
Autonomous Maintenance |
Preventive Maintenance |
---|---|
Strengths |
|
Empowering Operators: Fosters a sense of ownership among operators. |
Prolonged Equipment Lifespan: Systematic replacement of components before failure. |
Early Defect Detection: Vigilant monitoring for early identification of potential issues. |
Cost-Effectiveness: Long-term savings through preventing major breakdowns. |
Flexibility and Adaptability: Adapts well to changes in production processes and configurations. |
Planned Downtime: Enables maintenance scheduling during planned downtime. |
Reduced Downtime: Proactive approach minimizes unplanned downtime. |
Predictability: Enhances overall operational predictability. |
Improved Safety: Operators actively engaged in maintenance contribute to a safer environment. |
Structured Approach: Clear schedules for maintenance tasks. |
Weaknesses |
|
Operator Training: Requires substantial initial investment in operator training. |
Over-Maintenance Risk: Potential for over-maintenance, replacing components before reaching the end of their useful life. |
Over-Maintenance: Operator empowerment may lead to over-maintenance. |
Reactive Responses: Fixed schedules may result in reactive responses to unforeseen issues. |
Equipment Condition Prediction: Challenges in predicting actual equipment condition. |
Difficulty in Prediction: Difficulty in predicting actual equipment condition, relying on predetermined schedules. |
Measurement Difficulty: Difficulty in measuring and tracking success. |
Inflexibility: Potential inflexibility in adjusting schedules to accommodate unforeseen changes. |
Best Practices and Recommendations
1. Integrating a Hybrid Approach for Optimal Results
In the pursuit of maximizing equipment reliability and operational efficiency, industries often find that a hybrid maintenance approach can offer a synergistic solution. Combining elements of both autonomous maintenance and preventive maintenance allows organizations to leverage the strengths of each while mitigating their respective weaknesses.
Operator Empowerment and Scheduled Maintenance:
Integrate operator empowerment from autonomous maintenance with scheduled preventive maintenance tasks. This ensures that routine inspections and proactive interventions by operators are complemented by planned, systematic maintenance activities.
Flexibility and Structured Approaches:
Capitalize on autonomous maintenance's flexibility to adapt to changes in production demands while maintaining the structured approach of preventive maintenance for critical components. This hybrid model allows for a proactive stance in addressing immediate issues while ensuring the longevity of key equipment through scheduled maintenance.
2. Continuous Improvement and Feedback
Continuous improvement is the cornerstone of an effective maintenance strategy. Implementing feedback mechanisms for ongoing improvement ensures that the maintenance approach remains adaptive and responsive to evolving operational needs.
Regular Performance Reviews:
Conduct regular reviews of maintenance activities, analyzing the impact on equipment reliability, downtime, and safety. Use performance metrics to identify areas for improvement and adjust maintenance strategies accordingly.
Operator Feedback and Training Updates:
Establish channels for operator feedback on the effectiveness of maintenance tasks. Use this feedback to refine training programs, ensuring that operators are equipped with the latest skills and knowledge for optimal maintenance performance.
3. Technology's Role in Enhancing Maintenance Strategies
Embracing technology is pivotal in modern maintenance practices. Technological advancements offer tools and solutions that can significantly enhance the effectiveness of both autonomous maintenance and preventive maintenance.
Condition Monitoring and Predictive Analytics:
Implement condition monitoring technologies that enable real-time tracking of equipment health. Predictive analytics can forecast potential failures, allowing for proactive interventions and a shift towards a more predictive maintenance model.
IoT and Connectivity:
Utilize the Internet of Things (IoT) to establish connectivity between equipment and central monitoring systems. This enables remote monitoring, data analysis, and the ability to make informed decisions about maintenance needs.
Digital Twins and Simulation:
Explore the use of digital twins and simulation technologies to create virtual replicas of equipment. This allows for scenario testing, predictive modeling, and optimization of maintenance strategies before implementation in the physical environment.
The Role of CMMS Software in Enhancing Autonomous Maintenance and Preventive Maintenance Strategies
1. Seamless Data Management and Documentation
CMMS software acts as a centralized hub for storing and managing vast amounts of maintenance-related data. For autonomous maintenance, this includes information on routine inspections, defect detection, and operator interventions. For preventive maintenance, it encompasses schedules, part replacement history, and equipment condition records. The seamless data management capabilities of CMMS facilitate easy access to important information, empowering decision-makers to make informed choices based on historical performance and real-time insights.
2. Work Order Automation and Task Management
Identifying opportunities for automation contributes to effective maintenance, reducing manual workload, and enhancing efficiency. In autonomous maintenance, operators can utilize CMMS to automate work orders for routine inspections and minor repairs. For preventive maintenance, scheduled maintenance tasks can be automatically generated, ensuring that no critical maintenance activities are overlooked. This automation streamlines the workflow, allowing personnel to focus on more strategic tasks rather than administrative processes.
3. Predictive Analytics for Proactive Maintenance
CMMS software equipped with predictive analytics capabilities contributes to the proactive nature of both autonomous maintenance and preventive maintenance. By analyzing historical data, CMMS can predict potential failure points, allowing organizations to intervene before equipment breakdowns occur. For autonomous maintenance, this means addressing issues identified during routine inspections promptly. In preventive maintenance, predictive analytics help refine maintenance schedules, ensuring that components are replaced just in time to prevent failures.
4. Resource Planning and Optimization
Effective resource planning is essential for the success of any maintenance strategy. CMMS software assists in optimizing resource allocation by providing insights into labor requirements, spare parts inventory, and equipment availability. This is particularly valuable for organizations implementing autonomous maintenance, where optimal utilization of operator skills is important. For preventive maintenance, CMMS aids in managing spare parts inventory efficiently, ensuring that necessary components are available when scheduled maintenance activities occur.
5. Real-time Monitoring and Reporting
CMMS software facilitates real-time monitoring of equipment conditions and maintenance activities. In autonomous maintenance, this enables operators to track the results of interventions immediately. For preventive maintenance, real-time monitoring ensures that scheduled maintenance tasks are executed according to plan. The ability to generate comprehensive reports on equipment performance, maintenance histories, and compliance metrics enhances the visibility of both autonomous maintenance and preventive maintenance strategies.
6. Streamlined Communication and Collaboration
Ongoing and open communication are critical success criteria for any maintenance program. CMMS software provides a centralized platform for communication and collaboration among maintenance teams, operators, and decision-makers. In autonomous maintenance, operators can communicate issues and resolutions seamlessly. For preventive maintenance, collaboration is streamlined through automated notifications, ensuring that all stakeholders are aware of scheduled maintenance activities and their outcomes.
CMMS not only enhances the efficiency of both autonomous maintenance and preventive maintenance but also paves the way for a more sophisticated, data-driven, and proactive approach to asset management. As organizations strive for operational excellence, the role of CMMS in supporting and optimizing maintenance strategies becomes increasingly indispensable.
TABLE OF CONTENTS
Keep Reading
What happens when your most experienced maintenance leader is planning on retiring, taking 20 ...
7 Aug 2025
Today’s maintenance operations have become more complex and sophisticated. Gone are the days ...
5 Aug 2025
Modern warehouses are instrumental to maintaining the smooth operations of supply chains, ...
1 Aug 2025
Computerized Maintenance Management Systems (CMMS) have proven to be essential tools for ...
31 Jul 2025
Sometimes it feels as if technology is expanding at the speed of light. This is an ...
29 Jul 2025
Data Center downtime can have a huge negative impact ranging from damage to the data center’s ...
25 Jul 2025
Whenever a company introduces a new process or technology, it’s followed by a period of ...
24 Jul 2025
Obsolescence often comes unexpectedly, mainly because little attention is given to the ...
22 Jul 2025
Imagine a world where critical assets run smoothly without unexpected downtime, maintenance ...
18 Jul 2025
Imagine you're going through a compliance audit, and the inspector asks for maintenance ...
10 Jul 2025
Maintenance managers understand that disasters are unpredictable and can have a massive ...
4 Jul 2025
Asset lifespan is a key concern for executives and maintenance and facility management teams. ...
3 Jul 2025
Your company recently invested funds and time for new CMMS software, and six months later, it ...
1 Jul 2025
As Computerized Maintenance Management Systems (CMMS) become more connected and cloud-based, ...
1 Jul 2025
Edge computing is an innovative technology that enables data to be processed at the source, ...
24 Jun 2025
Facility management has undergone a significant transformation in recent times. Take, for ...
20 Jun 2025
A facility maintenance plan is at the core of a facility’s operations. This organized ...
19 Jun 2025
In the early days, preventive maintenance could be done effectively with a trained eye and a ...
17 Jun 2025
Sticky notes fall off, whiteboard grids get wiped, and spreadsheets never beep when a ...
13 Jun 2025
Handing a slice of your maintenance workload to a contractor is less about “giving up ...
12 Jun 2025