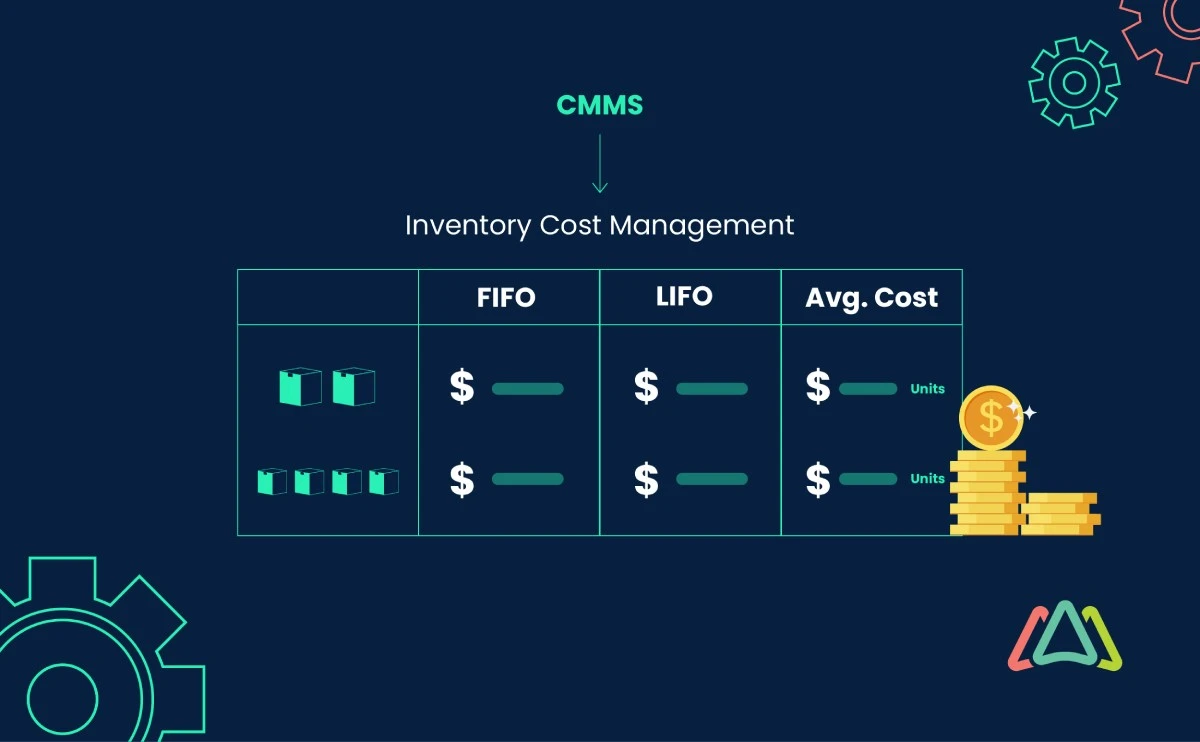
Inventory Cost Optimization for Effective Maintenance Operations
Whether you are a maintenance manager overseeing a team, a CFO responsible for budgetary decisions, or a maintenance professional involved in day-to-day operations, it’s understood that effective management of inventory costs is crucial for maintenance operations across industries.
Inventory costs can significantly impact the overall maintenance budget, profitability, and operational efficiency. By efficiently controlling and optimizing inventory costs, maintenance departments can achieve significant savings, enhance resource allocation, and improve overall productivity. Managing inventory costs involves monitoring and controlling expenses related to holding inventory, ordering inventory, handling shortages, and dealing with obsolescence.
Neglecting inventory cost management can lead to overstocking, stock outages, increased maintenance downtime, excess carrying costs, and potential disruptions to operations. Organizations can’t afford to underestimate its importance in this current competitive business landscape where efficiency, cost-effectiveness, and optimized resource utilization are paramount.
What are Inventory Costs?
Inventory costs refer to the expenses incurred by organizations to acquire, hold, and manage their inventory. In the context of maintenance, inventory costs encompass elements associated with storing, utilizing, and replenishing spare parts and equipment necessary for maintenance activities.
These costs go beyond the initial purchase price of inventory items. They also include expenses related to inventory storage, handling, insurance, depreciation, obsolescence, ordering, spoilage, and potential shortages. Understanding and effectively managing these costs is essential for maintaining a healthy balance between inventory availability and financial efficiency.
Types of Inventory Costs in Maintenance Management and How to Calculate Them
Holding Costs
Holding costs represent the expenses incurred for holding and storing inventory over a certain period. These costs typically include warehousing and security costs, insurance premiums, property taxes, depreciation, and other associated expenses. To calculate holding costs, organizations can consider the average value of inventory and apply a predetermined holding cost rate.
Holding Costs = Average Inventory Value x Holding Cost Rate
Ordering Costs
Ordering costs involve costs associated with placing orders, order processing, supplier communication and shipping. To calculate ordering costs, organizations can consider the number of orders placed over a given period and multiply it by the cost per order. Insurance costs related to transportation and handling of inventory can also be included in this calculation.
Ordering Costs = Number of Orders Placed x Cost per Order
Shortage Costs
Shortage costs arise when inventory is not available when needed, leading to disruptions in maintenance operations. These costs include downtime costs, emergency procurement expenses, expedited shipping fees, and the impact on customer satisfaction.
Calculating shortage costs can be more complex and may involve estimating the potential loss of revenue, customer penalties, and the cost of emergency measures taken to address the shortage. Insurance costs related to potential business interruption or loss due to inventory shortages may also be considered in the calculation.
Obsolescence Costs
Obsolescence costs arise from inventory becoming obsolete or outdated due to technological advancements, changes in product specifications, or shifts in market demand. These costs include write-offs, disposal fees, and the loss of value associated with unusable inventory.
To calculate obsolescence costs, organizations should consider the value of obsolete inventory and any associated disposal costs. Insurance costs related to potential loss due to inventory obsolescence or damage may also be factored into the calculation.
To gain a holistic view of an organization’s inventory management practices, maintenance professionals need to understand how they can utilize appropriate valuation methods to assign a cost to their inventory items.
These costs help companies understand the true cost of their inventory, track changes in inventory value over time, and comply with accounting principles and regulations.
Inventory Valuation Methods and Calculations Used by Maintenance Managers
Inventory valuation methods are used to assign a cost to the inventory items held by a company and are employed for financial reporting purposes, such as determining the value of ending inventory on the balance sheet and calculating the cost of goods sold (COGS) on the income statement.
They are crucial when making informed business decisions, managing cash flow, and assessing profitability. They play a vital role in inventory management, pricing strategies, tax calculations, and financial analysis.
The most commonly used methods are
First-in, First-out (FIFO)
The FIFO method assumes that the first items purchased or produced are the first ones to be sold or consumed. This method aligns with the physical flow of inventory, where older inventory is used or sold before newer inventory.
To calculate the value of ending inventory using the FIFO method, follow these steps:
- Step 1: Determine the cost of the oldest inventory (first items purchased).
- Step 2: Multiply the cost per unit of the oldest inventory by the quantity of inventory remaining from that batch.
- Step 3: Repeat steps 1 and 2 for subsequent batches of inventory, if applicable.
- Step 4: Sum the values obtained in step 2 to calculate the total value of ending inventory.
Consider the following example-
Example Inventory Batches
Batch |
Quantity |
Cost per Unit ($) |
---|---|---|
Batch 1 |
100 |
10 |
Batch 2 |
200 |
12 |
Batch 3 |
150 |
11 |
Calculation of Ending Inventory Using FIFO:
Batch 1: 100 units * $10 per unit = $1,000
Batch 2: 200 units * $12 per unit = $2,400
Batch 3: 150 units * $11 per unit = $1,650Total Value of Ending Inventory = $1,000 + $2,400 + $1,650 = $5,050
Last-in, First-out (LIFO)
The LIFO method assumes that the most recently purchased or produced items are the first ones to be sold or consumed. This method deviates from the physical flow of inventory but can be beneficial in times of rising costs, as it assigns the latest and potentially higher costs to the inventory sold.
Steps to calculate the value of ending inventory using the LIFO method:
- Step 1: Determine the cost of the most recent inventory (last items purchased).
- Step 2: Multiply the cost per unit of the most recent inventory by the quantity of inventory remaining from that batch.
- Step 3: Repeat steps 1 and 2 for previous batches of inventory, if applicable.
- Step 4: Sum the values obtained in step 2 to calculate the total value of ending inventory.
Consider the same example-
Example Inventory Batches
Batch |
Quantity |
Cost per Unit ($) |
---|---|---|
Batch 1 |
100 |
10 |
Batch 2 |
200 |
12 |
Batch 3 |
150 |
11 |
Calculation of Ending Inventory Using LIFO:
Batch 3: 150 units * $11 per unit = $1,650
Batch 2: 200 units * $12 per unit = $2,400
Batch 1: 100 units * $10 per unit = $1,000Total Value of Ending Inventory = $1,650 + $2,400 + $1,000 = $5,050
Weighted Average Cost Method
The weighted average cost method calculates the average cost of all inventory items, taking into account the total cost and quantity of inventory available.
Steps to calculate the weighted average cost per unit
- Step 1: Sum the total cost of all inventory batches.
- Step 2: Sum the total quantity of all inventory batches.
- Step 3: Divide the total cost by the total quantity to obtain the weighted average cost per unit.
Consider the same example again-
Example Inventory Batches
Batch |
Quantity |
Cost per Unit ($) |
---|---|---|
Batch 1 |
100 |
10 |
Batch 2 |
200 |
12 |
Batch 3 |
150 |
11 |
Calculation of Weighted Average Cost per Unit:
Total Cost = ($10 * 100) + ($12 * 200) + ($11 * 150) = $5,050
Total Quantity = 100 + 200 + 150 = 450Weighted Average Cost per Unit = Total Cost / Total Quantity = $5,050 / 450 = $11.22
Calculation of Ending Inventory Using Weighted Average Cost:
Ending Inventory Quantity = Total Quantity
Ending Inventory Value = Ending Inventory Quantity * Weighted Average Cost per Unit Ending Inventory Value
Ending Inventory Value = 450 units * $11.22 per unit = $5,049.90 (rounded to $5,050)
Note: The weighted average cost per unit remains constant, and it is multiplied by the quantity of ending inventory to calculate the total value of ending inventory.
Once organizations have their inventory valuation models in place, it’s important to consider the various factors that can influence inventory costs to optimize their inventory management strategies.
Factors Influencing Inventory Costs in Maintenance Operations
Demand Variability
Unpredictable changes in demand can lead to increased inventory costs. By analyzing historical data, implementing demand forecasting techniques, and optimizing inventory replenishment strategies, organizations can mitigate the impact of demand variability on inventory costs.
Lead Time
Lead time is considered the time it takes for an order to be fulfilled from the moment it is placed. Longer lead times can result in higher inventory costs, as it requires maintaining larger stock levels to account for the time between order placement and receipt. By reducing lead times through effective supplier management, process optimization, and technology adoption, businesses can minimize inventory carrying costs and improve operational efficiency.
Stock Outages and Overstocking
Outages occur when inventory levels are insufficient to meet customer demand, while overstocking happens when inventory levels exceed demand requirements. Both scenarios can have negative effects on inventory costs. Stock outages can lead to lost sales, customer dissatisfaction, and expedited shipping expenses. Overstocking ties up capital, incurs holding costs, and increases the risk of obsolescence. Implementing robust inventory control mechanisms, leveraging demand forecasting can help maintain optimal stock levels.
Equipment Failure Rates
Higher equipment failure rates can lead to increased spare parts inventory and expedited shipping costs that are necessary to minimize downtime. By adopting predictive maintenance technologies, and optimizing spare parts management, businesses can minimize equipment failure rates and associated inventory costs.
Vendor Performance
Late deliveries, quality issues, and unreliable suppliers can disrupt supply chains and cost businesses money. By establishing strong relationships with reliable vendors, conducting performance evaluations, and fostering effective communication channels, maintenance professionals can mitigate the risk of inventory disruptions and optimize costs.
Seasonality and Market Trends
These influence customer demand patterns, necessitating adjustments in inventory levels. Industries experiencing seasonal fluctuations or evolving market trends must account for these dynamics to prevent excess inventory during low-demand periods or stock outs during peak seasons.
By monitoring market trends, collaborating closely with sales and marketing teams, and adopting flexible inventory management strategies, organizations can optimize inventory costs and meet customer demands effectively.
As businesses navigate the factors influencing inventory costs, it becomes evident that effective inventory cost management comes with its own set of challenges.
Challenges with Effective Inventory Cost Management and How to Overcome Them
Lack of Visibility and Data Accuracy
One of the key challenges in managing inventory costs is the lack of visibility and data accuracy for inventory levels, demand patterns, and stock movements. Incomplete or outdated information can lead to inaccurate inventory calculations.
By implementing a robust Computerized Maintenance Management System (CMMS) that provides real-time visibility, automates data collection, and ensures accuracy, organizations can overcome this challenge and make informed decisions.
Inefficient Forecasting and Planning
Ineffective demand forecasting and inadequate inventory planning may lead to stock outages or overstocking. By leveraging historical data, utilizing demand forecasting models, and employing advanced inventory planning techniques, organizations can optimize inventory levels and mitigate the risks associated with inefficient forecasting and planning.
Inadequate Inventory Control and Monitoring
Without proper controls and monitoring, unauthorized stock withdrawals, inaccurate stock counts, and inventory discrepancies may occur, leading to financial losses and operational inefficiencies.
By implementing robust inventory control procedures, conducting regular cycle counts, and employing QR code or RFID technology for accurate tracking, organizations can enhance control and monitoring, thereby reducing inventory costs.
Poor Inventory Replenishment Strategies
Relying on ad-hoc ordering practices or failing to establish reorder points and order quantities can result in stock outs or excessive inventory. By adopting data-driven approaches, implementing just-in-time (JIT) inventory management, and leveraging automated reorder systems, maintenance managers can streamline replenishment processes, reduce costs, and ensure optimal inventory levels.
Limited Collaboration and Communication
Siloed departments, disconnected systems, and inadequate communication channels can lead to delayed information sharing, coordination issues, and suboptimal decision-making. By fostering cross-functional collaboration, establishing clear communication channels, and leveraging CMMS software that enables seamless information exchange, organizations can ensure efficient inventory cost management.
Benefits of Implementing a CMMS Software to Improve Management of Inventory Costs
CMMS software offers a centralized platform for managing maintenance activities, including inventory costs. It provides comprehensive control and visibility over inventory-related activities and enables businesses to efficiently track, manage, and analyze inventory data.
Below are some specific features related to inventory management software that a CMMS provides for.
Centralized Inventory Management
CMMS offers a centralized repository to store and manage inventory data, eliminating the need for disparate spreadsheets or manual record-keeping. This centralization enhances data accuracy, reduces errors, and facilitates streamlined inventory control.
Real-time Inventory Visibility
CMMS provides real-time visibility into inventory levels, allowing maintenance professionals to monitor stock levels, track usage, and identify potential issues promptly. This visibility enables proactive inventory management, preventing stock outages or overstocking.
Demand Forecasting and Planning
By analyzing historical data and using advanced algorithms, CMMS can predict future inventory needs accurately. This helps optimize inventory levels, reduce carrying costs, and ensure that the right quantity of items is available when needed.
Automatic Restocking
CMMS can automate inventory restocking processes based on predefined reorder points or stock thresholds. This feature ensures that inventory is automatically restocked when it falls below a certain level based on historical use, reducing the risk of stock shortages and minimizing manual intervention.
Vendor Performance Monitoring
CMMS allows for vendor performance monitoring by tracking delivery times, product quality, and other relevant metrics. These data enable maintenance professionals to assess and collaborate with vendors effectively, ensuring reliable and timely supply of inventory.
Inventory Reporting and Analytics
CMMS generates comprehensive reports and analytics related to inventory costs, usage patterns, stock levels, and other key performance indicators. These insights enable maintenance managers to identify trends, make data-driven decisions, and continuously improve inventory cost management strategies.
Organizations can achieve effective inventory cost management, enhance operational efficiency, and drive cost savings throughout their maintenance operations through adoption of best practices, CMMS implementation, and data-centric decision-making.
Adopting a mindset of continuous improvement and implementing optimization strategies such as lean principles or Six Sigma methodologies fosters a culture of efficiency and cost-consciousness. Regularly reviewing and refining inventory management practices can yield long-term benefits in terms of cost reduction and process optimization.
TABLE OF CONTENTS
Keep Reading
Computerized Maintenance Management Systems (CMMS) have increasingly become the go-to tools ...
19 Aug 2025
It doesn’t seem to matter which energy provider you choose; the bottom line is that energy ...
15 Aug 2025
In FDA-regulated industries such as pharmaceuticals, medical devices, biotechnology, and food ...
14 Aug 2025
B2C businesses, such as retail, hospitality, and food service, operate in a highly ...
8 Aug 2025
What happens when your most experienced maintenance leader is planning on retiring, taking 20 ...
7 Aug 2025
Today’s maintenance operations have become more complex and sophisticated. Gone are the days ...
5 Aug 2025
Modern warehouses are instrumental to maintaining the smooth operations of supply chains, ...
1 Aug 2025
Computerized Maintenance Management Systems (CMMS) have proven to be essential tools for ...
31 Jul 2025
Sometimes it feels as if technology is expanding at the speed of light. This is an ...
29 Jul 2025
Data Center downtime can have a huge negative impact ranging from damage to the data center’s ...
25 Jul 2025
Whenever a company introduces a new process or technology, it’s followed by a period of ...
24 Jul 2025
Obsolescence often comes unexpectedly, mainly because little attention is given to the ...
22 Jul 2025
Imagine a world where critical assets run smoothly without unexpected downtime, maintenance ...
18 Jul 2025
Imagine you're going through a compliance audit, and the inspector asks for maintenance ...
10 Jul 2025
Maintenance managers understand that disasters are unpredictable and can have a massive ...
4 Jul 2025
Asset lifespan is a key concern for executives and maintenance and facility management teams. ...
3 Jul 2025
Your company recently invested funds and time for new CMMS software, and six months later, it ...
1 Jul 2025
As Computerized Maintenance Management Systems (CMMS) become more connected and cloud-based, ...
1 Jul 2025
Edge computing is an innovative technology that enables data to be processed at the source, ...
24 Jun 2025
Facility management has undergone a significant transformation in recent times. Take, for ...
20 Jun 2025