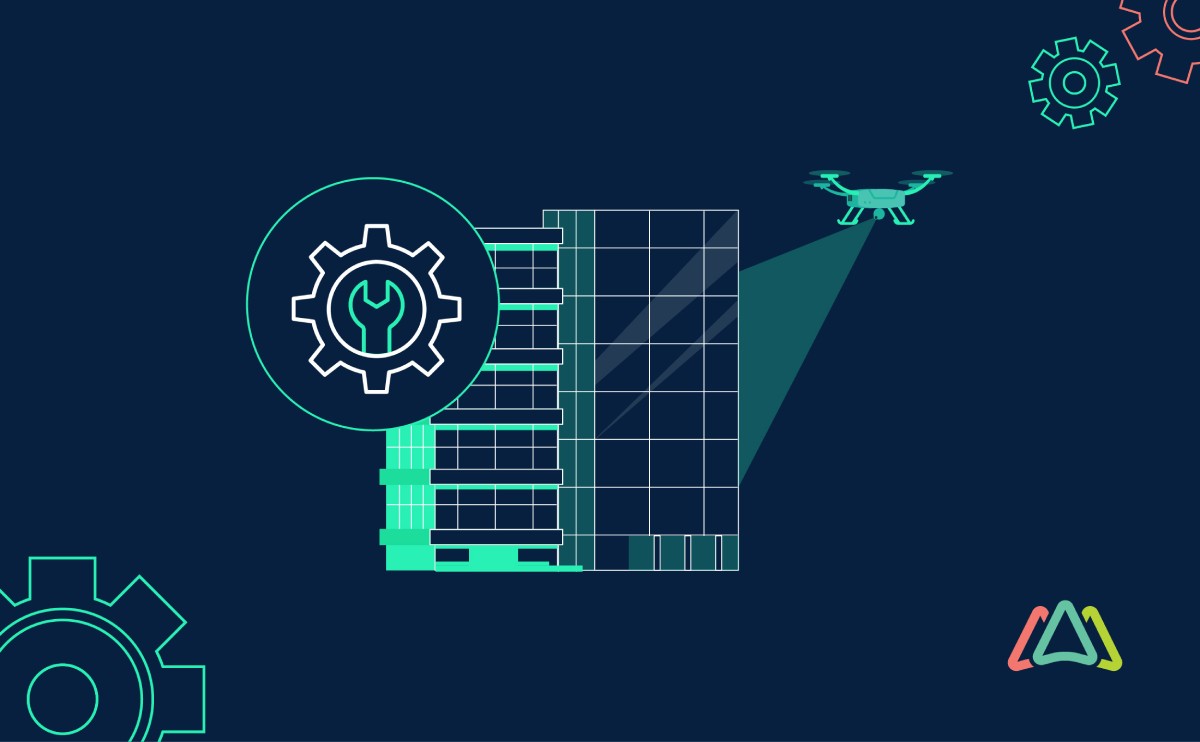
A Comprehensive Guide for Commercial Facilities Maintenance
Commercial facilities maintenance refers to the proactive management and upkeep of various physical assets and systems within commercial properties. It encompasses a wide range of activities aimed at ensuring the proper functioning, safety, and longevity of buildings, equipment, and surrounding environments. This comprehensive approach involves regular inspections, preventive maintenance, repairs, and the implementation of safety and security measures.
According to a report by Fortune Business Insights, the global facility management market experienced substantial growth, reaching a value of $1,260.36 billion in 2022. The market is projected to continue expanding and is expected to reach $1,856.44 billion by 2029, with a compound annual growth rate of 5.7%. These statistics highlight the significance of commercial facility maintenance and the recognition of its importance in driving business success.
Commercial facility maintenance is crucial across diverse industries, encompassing a wide range of tasks aimed at ensuring safety, efficiency, and customer satisfaction. By prioritizing maintenance efforts, businesses can improve productivity, reduce costs, and enhance brand reputation.
Types of Commercial Facilities
Commercial facilities refer to physical structures and spaces used for commercial purposes, encompassing a wide range of buildings and properties. These facilities serve as the operational hubs for businesses across various industries. Commercial facilities maintenance involves the systematic management and upkeep of these spaces to ensure their proper functioning, safety, and longevity. Commercial facilities come in various forms, tailored to the needs of different industries. Some common types of commercial facilities include:
- Office buildings: These facilities house administrative offices, providing spaces for businesses to conduct their operations, hold meetings, and facilitate collaboration among employees.
- Retail stores: These facilities include shopping centers, malls, department stores, and individual retail shops, providing spaces for selling products and services to customers.
- Warehouses and distribution centers: These facilities focus on storage, inventory management, and distribution of goods for businesses involved in manufacturing, e-commerce, logistics, and supply chain management.
- Healthcare facilities: This category includes hospitals, clinics, medical offices, and nursing homes that provide medical care and services to patients.
- Educational institutions: Schools, colleges, and universities fall under this category, where facilities are designed for classrooms, laboratories, libraries, sports facilities, and administrative offices.
- Hospitality industry: Hotels, resorts, restaurants, and event venues are part of the hospitality industry, offering accommodations, dining experiences, and event spaces for guests.
- Industrial facilities: Manufacturing plants, factories, processing plants, and industrial warehouses are commercial facilities dedicated to production, storage, and manufacturing processes.
A Closer Look at the Key Components of Commercial Facilities Maintenance
Building Maintenance
- HVAC Systems: Proper maintenance of heating, ventilation, and air conditioning (HVAC) systems is crucial for maintaining optimal indoor air quality, temperature control, and energy efficiency. Tasks may include regular filter replacements, inspection and cleaning of ductwork, calibration of thermostats, and preventive maintenance for HVAC equipment.
- Electrical Systems: Regular inspections and maintenance of electrical systems are essential to ensure safe and reliable operations. This includes testing and servicing electrical panels, switches, outlets, and lighting fixtures, as well as addressing any electrical malfunctions or potential fire hazards.
- Plumbing Systems: Maintaining plumbing systems helps prevent leaks, water damage, and disruptions to water supply and drainage. Tasks may include regular inspection of pipes, fixtures, and water heaters.
- Structural Maintenance: Structural maintenance involves monitoring and addressing issues that could compromise the integrity of the building. This includes inspections for cracks, leaks, foundation issues, and damage caused by weather conditions. Regular maintenance of roofs, walls, windows, and doors is also necessary to ensure the building's structural integrity and prevent water infiltration.
Equipment and Machinery Maintenance
- Inspection and Testing: Regular inspections and testing of equipment and machinery are crucial to identify any signs of wear, damage, or potential malfunctions. This includes checking for loose connections, abnormal noises, fluid leaks, and irregular performance. Equipment-specific inspections should be conducted according to manufacturer recommendations and industry standards.
- Preventive Maintenance: Implementing preventive maintenance ensures that equipment and machinery are serviced at regular intervals to prevent breakdowns and optimize performance. This may include lubrication, calibration, filter replacements, and system cleaning. Scheduling maintenance tasks proactively can extend the lifespan of equipment and reduce unexpected failures.
- Repair and Replacement: Timely repair and replacement of faulty equipment or components are essential to prevent further damage and maintain operational efficiency. Monitoring equipment performance, tracking maintenance history, and promptly addressing repair needs can minimize downtime and improve overall productivity.
Grounds and Landscaping Maintenance
- Lawn Care and Landscaping: Regular lawn mowing, trimming, and fertilization ensure a well-maintained and visually appealing exterior. Other tasks may include weed control, pest management, and irrigation system maintenance to promote healthy plant growth and a pleasant outdoor environment.
- Parking Lot Maintenance: Parking lots require regular maintenance to ensure safe and convenient access for customers and employees. This includes pavement repairs, re-striping, signage maintenance, lighting checks, and regular cleaning to maintain a well-organized and safe parking area.
- Exterior Building Maintenance: Exterior building maintenance involves cleaning, painting, and repairing the building's exterior surfaces. This includes window washing, gutter cleaning, and addressing any issues related to external walls, roofs, and landscaping features to enhance the overall appearance and longevity of the facility.
Safety and Security Measures
- Fire Safety Systems: Maintaining fire safety systems is crucial for protecting occupants and property from fire hazards. This includes regular inspection, testing, and maintenance of fire alarms, smoke detectors, sprinkler systems, fire extinguishers, and emergency lighting. Fire drills and staff training should also be conducted regularly to ensure preparedness.
- Security and Surveillance Systems: Regular maintenance and monitoring of security systems, such as access control, video surveillance cameras, and intrusion detection systems, help prevent unauthorized access, deter theft, and ensure a secure environment for employees and customers. Equipment checks, software updates, and addressing any issues promptly are essential for maintaining the effectiveness of these systems.
- Emergency Preparedness: Facilities must have emergency plans in place and conduct regular drills to ensure proper response during emergencies such as natural disasters, power outages, or other critical incidents. This includes reviewing evacuation procedures, emergency contact information, and maintaining emergency supplies such as first aid kits and backup power generators.
By prioritizing these key components of commercial facilities maintenance, businesses can ensure the longevity, safety, and efficient functioning of their facilities, promoting a positive environment for occupants and ultimate success of the organization.
Benefits of Regular Maintenance
Cost Savings and Avoidance of Major Repairs
Regular maintenance plays a crucial role in cost savings for businesses. By identifying and addressing potential issues early on, businesses can avoid costly repairs or equipment replacements. For example, routine inspections and maintenance of HVAC systems can prevent breakdowns and the need for emergency repairs, avoiding high repair costs and minimizing disruptions to operations for facility owners, lessors and lessees.
Improved Energy Efficiency
Regular maintenance helps optimize the energy efficiency of equipment and systems within commercial facilities. Well-maintained HVAC systems, for instance, operate more efficiently, reducing energy consumption and lowering utility costs. By cleaning and replacing air filters, checking ductwork for leaks, and ensuring proper calibration of thermostats, businesses can improve energy efficiency and reduce their carbon footprint.
Enhanced Occupant Comfort and Satisfaction
Proper maintenance contributes to a comfortable and pleasant environment for occupants, including employees, customers, and visitors. Regular servicing of HVAC systems ensures consistent temperature control, adequate ventilation, and improved indoor air quality. Well-maintained lighting systems provide optimal lighting levels for productivity and create a comfortable atmosphere. By prioritizing maintenance, businesses can enhance occupant satisfaction and create a positive experience.
Compliance with Regulations and Standards
Commercial facilities are subject to various regulations and industry standards that ensure the safety and well-being of occupants. Regular maintenance helps businesses remain compliant with these regulations, such as fire safety codes, electrical standards, and accessibility guidelines. By conducting inspections, testing equipment, and addressing any non-compliance issues promptly, businesses can avoid penalties, legal liability, and damage to their reputation.
Extended Lifespan of Equipment and Facilities
Proactive maintenance significantly extends the lifespan of equipment and facilities. Regular inspections, lubrication, cleaning, and preventive maintenance measures help identify and address minor issues before they escalate into major problems. By conducting regular maintenance tasks, businesses can prevent premature equipment failure, reduce the frequency of replacements, and extend the overall lifespan of their assets. This not only saves costs but also maximizes the return on investment.
Developing an Effective Maintenance Plan
To develop an effective maintenance plan, it is essential to start with a comprehensive assessment of the facility. This assessment should involve a thorough inspection of all systems, equipment, and structural components.
Conduct a Thorough Facility Assessment
Identify areas that require immediate attention, such as safety hazards, malfunctioning equipment, or deteriorating infrastructure. This assessment will serve as a baseline for understanding the maintenance needs and developing a plan that addresses the specific requirements of the facility.
Identify Maintenance Priorities and Schedules
Once the facility assessment is complete, prioritize the maintenance tasks based on their urgency and impact on operations. Categorize them into critical, high-priority, and routine maintenance activities. Critical tasks, such as addressing safety hazards or repairing essential equipment, should be given the highest priority. Establish schedules for routine maintenance tasks, such as filter replacements, inspections, and system checks. Consider factors such as manufacturer recommendations, industry standards, and the facility's specific needs when determining the frequency of maintenance activities.
Budget for Maintenance Activities
Allocate a budget specifically for maintenance activities. Consider the identified maintenance priorities, the expected costs of materials, labor, and any external service providers. Set aside funds for both routine maintenance and unexpected repairs. A well-planned maintenance budget ensures that necessary tasks are adequately funded, reducing the risk of deferring maintenance or overspending when emergencies arise.
Establish a Preventive Maintenance Program
Identify the equipment and systems that require regular preventive maintenance based on manufacturer guidelines, industry best practices, and historical data. Create a schedule for preventive maintenance tasks, such as lubrication, cleaning, inspections, and component replacements. Utilize technology solutions, such as computerized maintenance management systems (CMMS), to track and manage the preventive maintenance program effectively.
Track and Document Maintenance Activities
Maintain a comprehensive record of all maintenance activities performed in the facility. This includes recording dates, tasks performed, materials used, and any findings or recommendations. Well-documented maintenance history provides valuable insights into the facility's maintenance needs, helps identify recurring issues, and serves as a reference for future planning. It also aids in compliance with regulations and standards, supports warranty claims, and facilitates communication among maintenance staff and external service providers. Best practice is to regularly review and analyze the maintenance records to identify trends, evaluate the effectiveness of maintenance activities, and make informed decisions for future planning and budgeting. Additionally, leverage technology like Click Maint CMMS software to streamline workflow and track all maintenance activities, making it easier to access and analyze maintenance data.
By implementing a well-defined plan, businesses ensure proactive maintenance, optimize resources, and enhance overall reliability and performance of their commercial facilities.
Outsourcing vs. In-house Maintenance
Pros and Cons of Outsourcing Maintenance Services
Outsourcing maintenance services involves hiring external contractors or service providers to handle the maintenance tasks of a commercial facility. Consider the following pros and cons when deciding whether to outsource maintenance:
Pros of Outsourcing
- Expertise and Specialization: Outsourcing allows access to specialized knowledge and skills that may not be available in-house. Maintenance service providers often have expertise in specific areas, such as HVAC, electrical, or landscaping, ensuring high-quality work.
- Cost Savings: Outsourcing maintenance can potentially lead to cost savings. Instead of hiring and training in-house maintenance staff, businesses can contract service providers as needed, reducing labor costs, benefits, and training expenses.
- Flexibility and Scalability: Outsourcing provides flexibility in adjusting the scope of maintenance services based on the facility's changing needs. As the business grows or slows down, it is easier to modify the service level or add specialized services through outsourcing compared to adjusting your internal staffing levels.
- Access to Advanced Technology and Tools: Maintenance service providers often invest in the latest technology, tools, and equipment, which may not be feasible for businesses to acquire on their own. Outsourcing allows access to these resources, enhancing the quality and efficiency of maintenance work.
Cons of Outsourcing
- Lack of Direct Control: Businesses may have limited influence over scheduling, prioritization, and decision-making, which can potentially impact the facility's operations.
- Dependence on Third Parties: Reliance on external service providers introduces a level of dependency. Businesses need to ensure that the chosen service provider is reliable, trustworthy, and capable of meeting the maintenance needs consistently. It is advised to have solid contracts with terms and conditions before engaging in long term arrangements. Having clear terms and conditions help manage expectations and reduce risks.
Factors to Consider When Deciding Between In-house and Outsourced Maintenance
When making the decision between in-house and outsourced maintenance, businesses should consider the following factors:
- Nature and Complexity of Maintenance Tasks: Evaluate the complexity and expertise required for the maintenance tasks. If specialized knowledge or certifications are necessary, outsourcing may be a better option. For more straightforward tasks that can be managed with in-house resources, maintaining an internal team may be more cost-effective.
- Cost Analysis: Conduct a thorough cost analysis to compare the expenses associated with in-house maintenance versus outsourcing. Consider factors such as labor costs, training, equipment, insurance, and the potential for economies of scale that outsourcing can offer.
- Capacity and Workload: Assess the workload and capacity of the existing staff. If the in-house team is already stretched thin or lacks the necessary skills for certain tasks, outsourcing can provide relief and ensure that maintenance needs are met efficiently.
- Risk Assessment: Evaluate the risks associated with maintenance tasks. Consider safety requirements, legal compliance, and potential liabilities. In certain situations, outsourcing may provide access to specialized expertise, reducing the risk of accidents or legal issues.
Best Practices for Managing Outsourced Maintenance Contracts
When outsourcing maintenance services, it is crucial to establish effective management practices to ensure the success of the partnership. Consider the following best practices:
- Define Expectations: Clearly communicate your maintenance requirements, service-level expectations, and key performance indicators (KPIs) to the service provider. Establish a detailed contract that outlines deliverables, response times, and escalation procedures.
- Regular Communication and Collaboration: Maintain open lines of communication with the service provider. Regularly review performance, discuss any concerns, and address issues promptly. Collaboration ensures alignment and enables effective problem-solving.
- Performance Monitoring and Evaluation: Establish a system for monitoring and evaluating the performance of the service provider. Regularly review key metrics, such as response time, completion rates, and customer satisfaction. Conduct periodic performance reviews to identify areas of improvement and recognize outstanding performance.
- Contract Flexibility and Review: Ensure that the maintenance contract allows for flexibility to accommodate changing needs. Conduct periodic contract reviews to assess its effectiveness and make necessary adjustments. This ensures that the contract remains aligned with the evolving requirements of the facility.
- Relationship Building: Foster a positive and collaborative relationship with the service provider. Engage in regular meetings, provide feedback, and recognize the provider's contributions. A strong working relationship promotes trust, commitment, and a shared goal of maintaining the facility effectively.
Businesses should carefully consider the nature of maintenance tasks, cost analysis, capacity, and risk factors when deciding between in-house and outsourced maintenance. By following best practices for managing outsourced maintenance contracts, businesses can establish productive partnerships and ensure effective maintenance of their commercial facilities.
Technology and Innovation in Facility Maintenance
Computerized Maintenance Management Systems (CMMS)
CMMS software helps streamline and automate maintenance management processes. It helps organize maintenance tasks, track work orders, schedule preventive maintenance, manage inventory, and generate reports. By digitizing maintenance operations, CMMS enhances efficiency, reduces paperwork, improves communication, and enables data-driven decision-making.
Internet of Things (IoT) and Smart Building Technology
The Internet of Things (IoT) and smart building technology have revolutionized facilities maintenance. IoT-enabled devices, sensors, and systems can collect real-time data on equipment performance, energy usage, occupancy levels, and environmental conditions. This data is analyzed to identify maintenance needs, optimize energy efficiency, and improve operational performance. Smart building technology also enables remote monitoring and control, predictive maintenance, and automated alerts, empowering maintenance teams to proactively address issues and minimize downtime.
Predictive Maintenance and Data Analytics
Predictive maintenance leverages advanced data analytics to forecast equipment failures and determine optimal maintenance intervals. By analyzing historical data, performance patterns, and sensor readings, predictive maintenance algorithms can identify early warning signs of potential equipment malfunctions. This proactive approach helps businesses schedule maintenance tasks based on actual equipment condition rather than predetermined schedules, minimizing unplanned downtime, and optimizing maintenance resources.
Drones and Remote Monitoring
Drones equipped with cameras and sensors offer a powerful tool for facilities maintenance. They can be used to inspect roofs and other inaccessible areas, capturing high-resolution images or videos. Drones provide maintenance teams with a cost-effective and efficient means of conducting visual inspections, identifying maintenance needs, and assessing the condition of hard-to-reach equipment or structures. Additionally, remote monitoring systems allow real-time monitoring of equipment performance, enabling early detection of anomalies and prompt maintenance interventions.
Mobile Applications for Maintenance Management
Mobile applications have transformed the way maintenance tasks are managed and executed. Work order apps enable technicians to access work orders, update work order statuses, document maintenance activities, and communicate with the central maintenance team in real-time. These apps integrate with web-based CMMS platforms, allowing seamless data synchronization and facilitating efficient collaboration. Mobile applications provide flexibility, improve communication, enhance productivity, and provide instant access to critical maintenance information, enabling technicians to work more effectively while on-site.
The integration of these technologies and innovations into facilities maintenance processes has significantly improved efficiency, accuracy, and effectiveness. As technology continues to advance, it is essential for maintenance professionals to stay updated on emerging trends and adapt their practices to leverage the benefits of these innovations.
Ensuring Sustainable Facilities Maintenance
Implementing Green and Sustainable Practices
- Energy Conservation: Implement energy-saving measures such as installing energy-efficient lighting, utilizing natural lighting where possible, and optimizing HVAC systems for energy efficiency. Regularly monitor and adjust energy usage to minimize waste and reduce greenhouse gas emissions.
- Water Conservation: Implement water-saving measures such as low-flow fixtures, water-efficient landscaping, and leak detection systems. Educate employees on water conservation practices and promote responsible water use throughout the facility.
- Waste Reduction and Recycling: Develop a comprehensive waste management plan that includes recycling programs for paper, plastic, glass, and other recyclable materials. Minimize waste generation through source reduction strategies, such as promoting electronic document sharing and using reusable materials whenever possible.
- Green Cleaning Practices: Use environmentally friendly cleaning products that are non-toxic and biodegradable. Implement cleaning protocols that minimize the use of harmful chemicals and ensure proper disposal of cleaning waste.
Energy-Efficient Upgrades and Retrofits
- Lighting Upgrades: Replace traditional lighting fixtures with energy-efficient LED lights. LED lights not only consume less energy but also have a longer lifespan, reducing maintenance and replacement costs.
- HVAC System Optimization: Regularly maintain and optimize HVAC systems to ensure they operate efficiently. Upgrade to energy-efficient HVAC equipment, such as high-efficiency air conditioners or heat pumps, and use programmable thermostats to regulate temperature settings based on occupancy and operational needs.
- Building Envelope Improvements: Enhance insulation and sealing of the building envelope to minimize energy loss through air leakage. This includes sealing gaps, upgrading windows and doors, and adding insulation to walls and roofs.
Waste Management and Recycling Initiatives
- Recycling Programs: Implement comprehensive recycling programs throughout the facility. Provide clearly labeled recycling bins and educate employees on proper sorting and disposal practices. Partner with recycling vendors to ensure that recyclable materials are properly collected and processed.
- Hazardous Material Management: Develop protocols for handling and disposing of hazardous materials, such as chemicals and electronic waste. Ensure compliance with local regulations and promote safe handling practices among employees.
- Composting and Organic Waste Management: Implement composting programs for organic waste generated in cafeterias or food service areas. This reduces the amount of waste sent to landfills and creates nutrient-rich compost for landscaping or gardening purposes.
Sustainable maintenance not only benefits the environment but also contributes to a healthier and more productive workplace for employees and occupants. Regular monitoring, evaluation, and continuous improvement are essential to ensure the effectiveness of sustainable facilities maintenance practices.
With a commitment to proactive maintenance and continuous improvement, organizations can create resilient, efficient, and future-ready facilities that propel their success in an ever-evolving world. The true value of commercial facilities maintenance lies in its ability to foster growth, enhance operational excellence, and provide a remarkable experience for occupants and visitors alike.
TABLE OF CONTENTS
Keep Reading
The world of IoT is growing rapidly in almost every aspect of life across a variety of ...
29 Aug 2025
The adoption of Computerized Maintenance Management Systems (CMMS) presents a puzzling ...
28 Aug 2025
For the sake of repetition, a CMMS (Computerized Maintenance Management System) is the hub ...
26 Aug 2025
Too often, production and maintenance departments operate in silos, resulting in a lack of ...
22 Aug 2025
Many organizations struggle with scaling maintenance operations, mainly because some don’t ...
21 Aug 2025
Computerized Maintenance Management Systems (CMMS) have increasingly become the go-to tools ...
19 Aug 2025
It doesn’t seem to matter which energy provider you choose; the bottom line is that energy ...
15 Aug 2025
In FDA-regulated industries such as pharmaceuticals, medical devices, biotechnology, and food ...
14 Aug 2025
B2C businesses, such as retail, hospitality, and food service, operate in a highly ...
8 Aug 2025
What happens when your most experienced maintenance leader is planning on retiring, taking 20 ...
7 Aug 2025
Today’s maintenance operations have become more complex and sophisticated. Gone are the days ...
5 Aug 2025
Modern warehouses are instrumental to maintaining the smooth operations of supply chains, ...
1 Aug 2025
Computerized Maintenance Management Systems (CMMS) have proven to be essential tools for ...
31 Jul 2025
Sometimes it feels as if technology is expanding at the speed of light. This is an ...
29 Jul 2025
Data Center downtime can have a huge negative impact ranging from damage to the data center’s ...
25 Jul 2025
Whenever a company introduces a new process or technology, it’s followed by a period of ...
24 Jul 2025
Obsolescence often comes unexpectedly, mainly because little attention is given to the ...
22 Jul 2025
Imagine a world where critical assets run smoothly without unexpected downtime, maintenance ...
18 Jul 2025
Imagine you're going through a compliance audit, and the inspector asks for maintenance ...
10 Jul 2025
Maintenance managers understand that disasters are unpredictable and can have a massive ...
4 Jul 2025