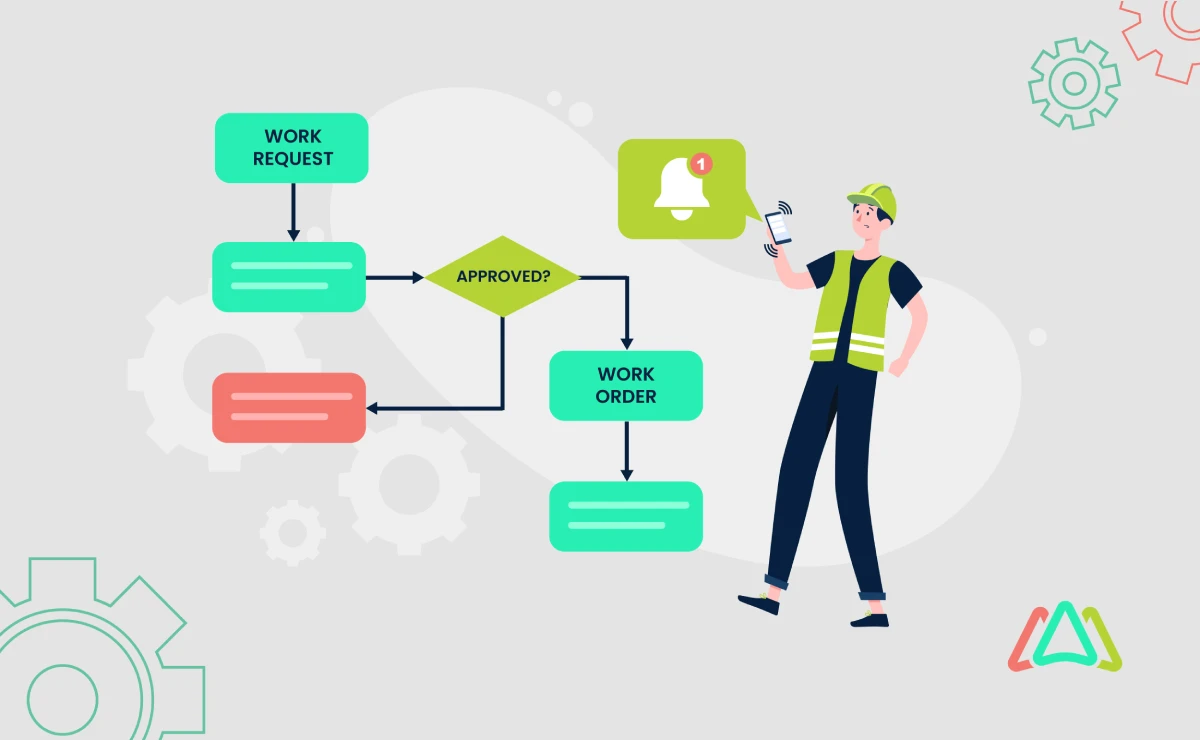
Five Differences Between CMMS Work Orders and Work Requests
Using one term interchangeably with a similar one is common and usually occurs without consequence. That’s mainly because we understand the meaning based on context. However, there are other times when terms, although similar, have very different meanings and, when used incorrectly, can result in negative outcomes.
For example, work orders and work requests may be casually used interchangeably in maintenance management. However, they refer to distinct types of maintenance activities, each with different purposes and impacts. Understanding the differences between these processes is essential for maintenance and facilities management. This is especially true when a Computerized Maintenance Management System (CMMS) is used for managing maintenance operations. Failing to distinguish between these terms causes confusion and has adverse effects.
Let's take a look at the differences between work orders and requests, how they impact maintenance operations, and when each should be used.
1. Work Orders and Work Requests: Definitions and Purposes
What are Work Orders?
A work order is a formal document that authorizes and details the execution of a maintenance task. It is an overall plan that guides technicians through a designated task—from start to completion. For instance, consider the need to conduct routine equipment calibration at a manufacturing facility. A work order would detail the specific equipment and tools, the calibration procedure, an expected timeline, and any relevant safety protocols.
CMMS software provides a structured framework for generating and managing work orders. They clarify the purpose of the task and its execution. CMMS platforms have customizable templates and standardized workflows, making it easy for organizations to define specific task requirements, assign responsible personnel, and establish clear timelines for completion. These features ensure alignment with preventive maintenance schedules, regulatory compliance, and organizational objectives. For example, CMMS software can automate the generation of preventive maintenance work orders based on predefined schedules or asset condition thresholds. These capabilities optimize asset performance and prolong lifespan.
What are Work Requests?
A work request is an initial “ask” for maintenance intervention. A facility occupant or department often submits it. Unlike a work order, a work request lacks the detailed information included in work orders and authorization to take immediate action. Consider a situation where an office's air conditioner is not working properly. An employee submits a work request outlining the issue. A user or group of users receives the work request to review the issue and determine if it should be approved and changed into a work order where it would be assigned to a technician or 3rd party vendor.
CMMS software facilitates the initiation and tracking of work requests. It serves as a communication between facility staff or occupants and maintenance personnel. By offering an intuitive user interface and mobile accessibility, CMMS platforms make it easy for employees to submit work requests easily from any location. This CMMS feature enhances responsiveness and visibility. The CMMS also enables organizations to categorize and prioritize work requests based on urgency, impact on operations, and available resources. This ensures that critical issues are addressed promptly, minimizing downtime and maximizing operational efficiency.
2. Process and Requirements for Work Orders and Work Requests
Work Order Process and Requirements
When maintenance managers receive a work order, the process begins by assessing its urgency and validity. A work order is generated from there, detailing the necessary resources, timelines, and personnel. The work order serves as a formal authorization for a task. The work order streamlines the execution process, ensuring compliance with safety regulations and budgetary constraints. Considering a preventive maintenance scenario, a work order triggers a comprehensive inspection and servicing of critical machinery. By doing so, preventive maintenance can forestall potential unanticipated breakdowns.
CMMS software streamlines the process of generating, executing, and tracking work orders, optimizing resource allocation and task management. The CMMS software provides automated notifications and real-time updates. This way, the CMMS platform informs stakeholders about the status of work orders. These automated notifications make proactive decision-making and coordination possible. Furthermore, some CMMS solutions can be integrated with inventory management systems. This enables seamless procurement of required materials and spare parts that are needed to complete work orders. This way, maintenance technicians can access the necessary resources, minimizing delays and enhancing productivity.
Work Request Process and Requirements
While a work request initiates the maintenance cycle, it lacks the detail and authorization that come with work orders. Instead, it serves as a forerunner, prompting further evaluation and allocation of resources. For example, if a leaky faucet is found in an apartment building unit, the tenant submits a work request. However, the issue remains pending, until an administrator who is responsible for triaging maintenance requests has the chance to review the request and decide if it should be converted into a work order. There are many things to consider before approving a request and creating a work order; a work order already exists, urgency, validity, cost, etc.
CMMS software enhances the validation and escalation process of work requests. This feature ensures that maintenance issues are addressed promptly and efficiently. CMMS platforms can route work requests to appropriate personnel for evaluation and action by providing configurable workflows and approval processes. This prevents bottlenecks and ensures critical issues are flagged and escalated to the relevant stakeholders for prompt resolution. Additionally, CMMS solutions provide visibility into historical work request data, enabling maintenance managers to identify recurring issues and implement appropriate corrective actions to prevent future occurrences.
3. Work Orders and Work Requests Impact on Maintenance Operations
Impact of Work Orders
The fine detail included in a work order promotes operational efficiency and accountability. By documenting precise instructions and resource requirements, CMMS-enabled work order management software streamlines task execution while mitigating downtime and minimizing operational disruptions. Consider this: in preventive maintenance procedures, scheduled work orders ensure timely equipment servicing, preventing serious failures and optimizing asset lifespan.
CMMS software optimizes the impact of work orders on maintenance operations by fostering transparency, accountability, and continuous improvement. By providing real-time insights into work order status, resource utilization, and performance metrics, CMMS platforms enable maintenance managers to monitor progress and identify areas for optimization. Additionally, CMMS software facilitates compliance with regulatory requirements and industry standards by documenting maintenance activities and generating audit trails. This enhances organizational resilience and reduces the risk of financial penalties and shutdowns due to non-compliance.
Impact of Work Requests
Although work requests are essential for asking for maintenance intervention, they lack the authoritative directive required for immediate action. Without a formalized work order, there is a risk of oversight or delay, which can compromise operational continuity and result in escalated maintenance costs.
Because CMMS software centralizes all maintenance operations, it enhances the impact of work requests on maintenance operations by facilitating proactive intervention and resource allocation. CMMS platforms let maintenance managers prioritize work requests based on criticality and available resources by capturing detailed information about maintenance issues, including location, severity, and impact on operations. This ensures that resources are allocated effectively, minimizing downtime and maximizing asset reliability. CMMS systems also enable maintenance managers to track the resolution of work requests and communicate updates to requesters, keeping processes transparent and maintenance and facilities staff accountable.
4. Authorization and Approval for Work Orders and Work Requests:
Work Order Authorization and Approval
A work order requires formal authorization and approval from administrators, such as supervisors, managers, or department heads, before work starts. This approval ensures the required work aligns with organizational objectives, budgetary constraints, and compliance regulations. For example, before starting a major equipment overhaul, a work order requires approval from the finance department to allocate the funds to cover the task.
CMMS software streamlines the authorization and approval process for work orders by managing digital workflows and automated notifications. When a work order is submitted, it can be routed directly to designated approvers, who can review and authorize it promptly within the CMMS. This automation expedites the approval process and ensures transparency and accountability about the task. Additionally, some CMMS platforms feature customizable approval hierarchies that ensure organizations comply with regulatory requirements and internal policies seamlessly.
Work Request Authorization and Approval
As noted, a work request is an initial notification of a maintenance issue. While validation and prioritization are important, work requests typically don’t require the same formal authorization when they are initiated as work orders. For instance, a work request is submitted when a malfunctioning elevator is first identified. The work request prompts further assessment by maintenance personnel without any direct managerial approval.
CMMS software accelerates the validation and prioritization of work requests through its centralized communication channels and facilitates collaboration. Work requests submitted through the CMMS are systematically triaged. This streamlined process ensures that the evaluation and allocation of resources are based on predefined criteria. Some CMMS systems use predictive maintenance capabilities. These advanced features enable automated fault detection and proactive work request generation. The result is further optimization of resource utilization and mitigation of potential downtime.
5. Documentation and Record-Keeping
Documentation as Part of Work Orders
Detailed documentation is at the core of work order management. This information facilitates comprehensive record-keeping and historical analysis. These records capture essential details such as task completion time, resource utilization, and maintenance costs, enabling performance evaluation and trend analysis. For example, reviewing historical work orders helps maintenance managers identify recurring issues and take steps to optimize preventive maintenance schedules accordingly.
CMMS software transforms work order documentation and record-keeping by providing a centralized repository for all maintenance-related data. Each work order is stored within the system and captures essential details such as task descriptions, labor hours, material usage, and associated costs. CMMS platforms offer robust reporting and analytics, allowing maintenance managers to generate comprehensive insights from historical work order data. With a CMMS, organizations can identify trends, evaluate performance metrics, and make data-driven decisions to optimize maintenance strategies and resource allocation.
Documentation as Part of Work Requests
Work requests represent the starting point in the maintenance process. Their documentation is typically less comprehensive than that of work orders. Work requests serve primarily as initial notifications to prompt further evaluation and escalation into formal work orders when needed. They generally lack the granular detail and historical context essential for in-depth analysis and decision-making. For example, a work request for minor repairs may warrant a different level of documentation than a fully authorized work order for major equipment servicing.
CMMS software enhances the documentation and tracking of work requests by digitizing the entire request lifecycle. Work requests are logged and tracked within the CMMS platform from start to finish, ensuring visibility and accountability at every stage. CMMS solutions help organizations establish standardized workflows and escalation procedures for work requests. These features ensure timely resolution and service level agreements (SLAs) adherence. CMMS software helps maintenance managers improve by maintaining a comprehensive record of all work requests, allowing organizations to identify recurring issues, address root causes, and enhance operational efficiency over time.
The differences between work orders and requests underscore how organizations perform maintenance operations. Leveraging CMMS software helps maintenance leaders optimize their operations by streamlining workflows from requests to work order completion while documenting all activities. Organizations can move beyond reactive maintenance practices toward consistent, proactive maintenance processes by using CMMS software to track and manage requests, work orders, and preventive maintenance.
TABLE OF CONTENTS
Keep Reading
What happens when your most experienced maintenance leader is planning on retiring, taking 20 ...
7 Aug 2025
Today’s maintenance operations have become more complex and sophisticated. Gone are the days ...
5 Aug 2025
Modern warehouses are instrumental to maintaining the smooth operations of supply chains, ...
1 Aug 2025
Computerized Maintenance Management Systems (CMMS) have proven to be essential tools for ...
31 Jul 2025
Sometimes it feels as if technology is expanding at the speed of light. This is an ...
29 Jul 2025
Data Center downtime can have a huge negative impact ranging from damage to the data center’s ...
25 Jul 2025
Whenever a company introduces a new process or technology, it’s followed by a period of ...
24 Jul 2025
Obsolescence often comes unexpectedly, mainly because little attention is given to the ...
22 Jul 2025
Imagine a world where critical assets run smoothly without unexpected downtime, maintenance ...
18 Jul 2025
Imagine you're going through a compliance audit, and the inspector asks for maintenance ...
10 Jul 2025
Maintenance managers understand that disasters are unpredictable and can have a massive ...
4 Jul 2025
Asset lifespan is a key concern for executives and maintenance and facility management teams. ...
3 Jul 2025
Your company recently invested funds and time for new CMMS software, and six months later, it ...
1 Jul 2025
As Computerized Maintenance Management Systems (CMMS) become more connected and cloud-based, ...
1 Jul 2025
Edge computing is an innovative technology that enables data to be processed at the source, ...
24 Jun 2025
Facility management has undergone a significant transformation in recent times. Take, for ...
20 Jun 2025
A facility maintenance plan is at the core of a facility’s operations. This organized ...
19 Jun 2025
In the early days, preventive maintenance could be done effectively with a trained eye and a ...
17 Jun 2025
Sticky notes fall off, whiteboard grids get wiped, and spreadsheets never beep when a ...
13 Jun 2025
Handing a slice of your maintenance workload to a contractor is less about “giving up ...
12 Jun 2025