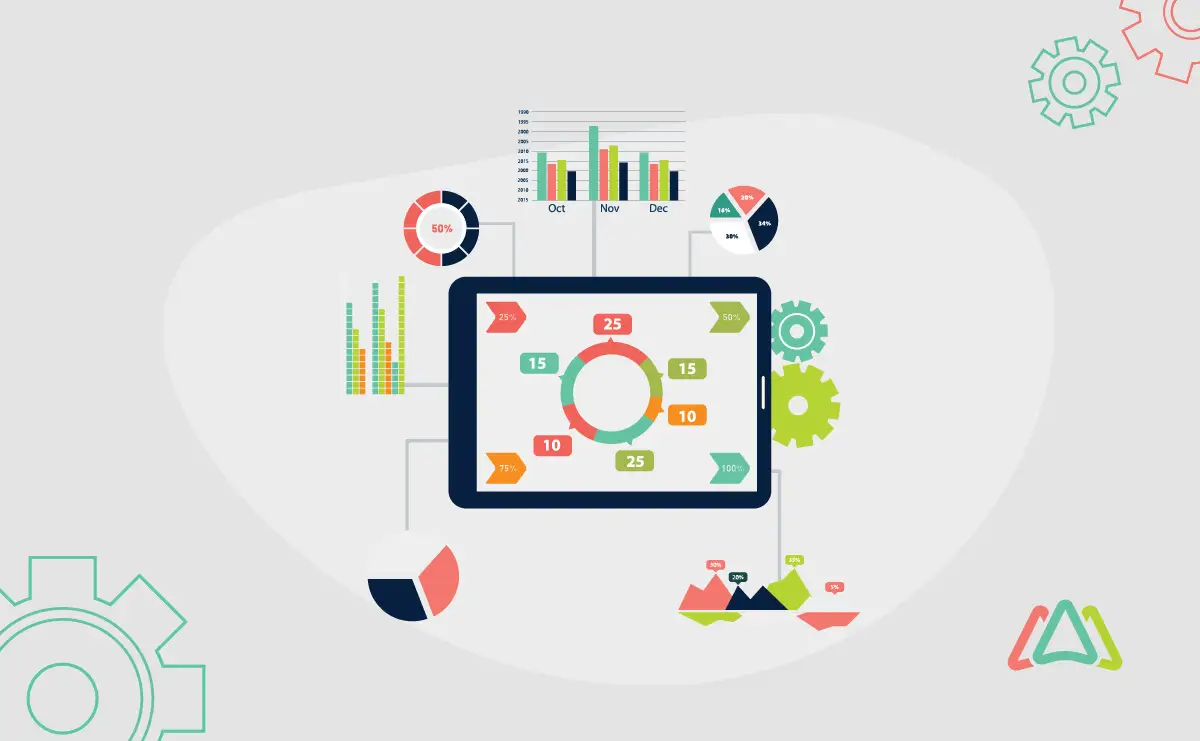
A Guide to Creating and Managing Equipment Maintenance Logs
At the heart of any robust maintenance management strategy lies meticulous documentation of equipment upkeep. An equipment maintenance log serves as a repository of essential information, detailing maintenance activities, inspection records, and repair history. It provides a roadmap for maintenance teams, guiding them through scheduled tasks and ensuring compliance with regulatory standards.
Complementing the traditional maintenance log is the CMMS, a digital solution that optimizes equipment management processes. CMMS software streamlines maintenance operations by automating scheduling, tracking assets, and generating reports. It serves as a centralized hub for maintenance data, offering real-time insights into equipment health and performance. With advanced features like predictive maintenance and inventory management, CMMS software empowers organizations to optimize their maintenance processes and maximize equipment uptime.
This article dives deep into the intricacies of equipment maintenance logs and CMMS, exploring their roles in fostering operational excellence and unlocking the full potential of maintenance management.
What is an Equipment Maintenance Log?
An equipment maintenance log serves as a comprehensive record of all maintenance activities performed on specific machinery or assets within an organization. Its primary purpose is to track and document the maintenance history of equipment, facilitating proactive maintenance planning, performance monitoring, and regulatory compliance. By meticulously recording maintenance tasks and observations, these logs provide insights into the health and operational status of equipment, enabling organizations to make informed decisions regarding repair, replacement, and maintenance planning.
In addition to optimizing equipment performance, maintenance logs play an important role in ensuring compliance with industry regulations and standards. Various industries, such as manufacturing, food production, pharmaceutical, healthcare, and transportation, are subject to stringent regulatory requirements governing equipment maintenance and safety protocols. By maintaining detailed records of maintenance activities, organizations can demonstrate their adherence to regulatory guidelines for impending audits and inspections. Furthermore, equipment maintenance logs help identify areas of non-compliance or potential risks, enabling proactive measures to address deficiencies and avoid regulatory penalties.
Components of an Effective Equipment Maintenance Log
An effective equipment maintenance log is a comprehensive document that serves as a roadmap for the upkeep of machinery and assets within an organization. It comprises various components designed to track maintenance activities, monitor equipment performance, and ensure compliance with preventive maintenance schedules. The following are the key components that make up an equipment maintenance log:
1. Identification of Equipment
The first step in creating an equipment maintenance log is to clearly identify the equipment being monitored. This includes recording essential details such as equipment name or ID, model number, serial number, and location within the facility. A standardized naming convention or labeling system can streamline the identification process and facilitate easy reference when logging maintenance activities. Additionally, including equipment specifications and operating manuals in the maintenance log ensures that maintenance personnel have access to essential information when performing tasks.
2. Documentation of Routine Checks
Routine checks are essential for detecting potential issues and ensuring the smooth operation of equipment. A well-maintained maintenance log includes a schedule of routine checks tailored to the specific requirements of each piece of equipment. This may include daily, weekly, monthly, or quarterly inspections of critical components such as electrical systems, fluid levels, belts, hoses, and safety mechanisms. Maintenance personnel should document their findings in the maintenance log, noting any abnormalities or signs of wear that may require attention.
3. Lubrication Schedules
Proper lubrication is essential for minimizing friction, reducing wear and tear, and extending the lifespan of equipment components. An effective maintenance log includes a lubrication schedule that outlines the type of lubricant to be used, the quantity, and the frequency of lubrication tasks for each piece of equipment. This schedule should be based on manufacturer recommendations, industry best practices, and the operating conditions of the equipment. Regularly documenting lubrication activities in the maintenance log ensures that equipment remains properly lubricated and prevents premature failure due to inadequate lubrication.
4. Record of Inspections
Regular inspections are essential for identifying potential safety hazards, equipment deficiencies, and performance issues. An equipment maintenance log should include a record of all inspections conducted, including the date, time, inspector's name, and findings. This may include visual inspections, functional tests, and measurements of critical parameters such as temperature, pressure, and vibration levels. Any abnormalities or deficiencies discovered during inspections should be documented in the maintenance log, along with any corrective actions taken to address them.
An effective equipment maintenance log is a comprehensive document that includes detailed information about the equipment being monitored, schedules for routine checks and lubrication, and records of inspections and maintenance activities. By diligently maintaining and updating these logs, organizations can ensure the reliability, safety, and performance of their equipment while minimizing downtime and costly repairs.
Benefits of Maintaining Detailed Equipment Maintenance Logs
Detailed equipment maintenance logs serve as invaluable tools for organizations seeking to optimize their maintenance practices, enhance operational efficiency, and ensure regulatory compliance. Below are the key benefits associated with maintaining comprehensive equipment maintenance logs:
1. Proactive Issue Prevention
One of the primary benefits of maintaining detailed equipment maintenance logs is the ability to proactively identify and address potential issues before they escalate into costly failures. By adhering to a scheduled maintenance program outlined in the maintenance logs, organizations can perform routine checks, inspections, and preventive maintenance tasks to detect and rectify minor issues early on. This proactive approach helps prevent unexpected breakdowns, minimize downtime, and extend the lifespan of equipment. Additionally, maintenance logs allow organizations to track equipment performance trends over time, enabling them to identify emerging issues and take corrective action before they impact operations.
2. Compliance Assurance
In many industries, compliance with regulatory standards and guidelines is paramount to ensuring workplace safety, environmental protection, and product quality. Detailed equipment maintenance logs play an important role in demonstrating compliance with regulatory requirements by documenting maintenance activities, inspections, and repairs. By maintaining accurate and up-to-date maintenance logs, organizations can provide evidence of their adherence to regulatory standards during audits, inspections, and certification processes. This not only helps avoid regulatory penalties and fines but also enhances trust and credibility with stakeholders, customers, and regulatory authorities.
3. Performance Monitoring
Maintenance logs serve as a valuable tool for monitoring the performance and health of equipment over time. By documenting maintenance activities, observations, and performance metrics in the logs, organizations can track equipment reliability, uptime, and efficiency. This data allows maintenance managers to identify patterns, trends, and anomalies in equipment performance, enabling them to make data-driven decisions regarding maintenance priorities, resource allocation, and asset management strategies. Additionally, maintenance logs provide valuable insights into equipment usage patterns, maintenance costs, and return on investment (ROI), helping organizations optimize their maintenance processes and maximize the value of their assets.
By leveraging these logs as strategic tools for maintenance management, organizations can enhance operational efficiency, minimize risks, and achieve long-term success in their respective industries.
Steps for Creating an Accurate Equipment Maintenance Log
Creating an accurate equipment maintenance log is a foundational step in establishing an effective maintenance management system within an organization. By following a structured approach and implementing best practices, organizations can ensure the reliability, safety, and performance of their equipment. Below are the key steps to creating an accurate equipment maintenance log:
1. Equipment Identification and Labeling
The first step in creating an accurate equipment maintenance log is to identify and label all equipment within the organization. Each piece of equipment should be assigned a unique identifier, such as a serial number or asset tag, to facilitate easy identification and tracking. Additionally, equipment should be labeled with information such as equipment name or description, model number, manufacturer, and location within the facility. Standardized labeling and identification practices ensure consistency and clarity in equipment documentation, reducing the likelihood of confusion or errors in the maintenance log.
2. Defining Maintenance Procedures
Once equipment has been identified and labeled, the next step is to define maintenance procedures for each piece of equipment. Maintenance procedures outline the specific tasks, inspections, and checks required to ensure the proper functioning and safety of equipment. These procedures should be based on equipment manufacturer recommendations, industry best practices, and regulatory requirements. Key maintenance procedures may include routine checks, lubrication schedules, calibration activities, and preventive maintenance tasks. Clearly defining maintenance procedures ensures that maintenance personnel understand their responsibilities and follow standardized protocols when performing maintenance activities.
3. Setting Maintenance Intervals
After defining maintenance procedures, organizations must establish maintenance intervals for each piece of equipment. Maintenance intervals specify the frequency at which maintenance tasks should be performed to ensure optimal equipment performance and reliability. Maintenance intervals may vary depending on factors such as equipment type, usage, operating conditions, and manufacturer recommendations. Common maintenance intervals include daily, weekly, monthly, quarterly, and annual maintenance tasks. By setting appropriate maintenance intervals, organizations can ensure that maintenance activities are performed at the right time and frequency, minimizing the risk of equipment failure and maximizing equipment uptime.
Challenges in Traditional Maintenance Logging
Despite the importance of maintenance logging, traditional methods often pose several challenges that hinder the effectiveness and efficiency of maintenance management. Below are commonly faced challenges associated with traditional maintenance logging:
1. Manual Record-Keeping
1.1 Time-Consuming Processes
Manual maintenance logging involves labor-intensive processes that consume valuable time and resources. Maintenance personnel must manually record maintenance activities, inspections, and repairs in paper-based logbooks or spreadsheets, which can be time-consuming and prone to errors. This manual data entry process not only increases the administrative burden on maintenance teams but also detracts from their ability to focus on critical maintenance tasks and activities. Moreover, the time required to retrieve and analyze maintenance data from manual logs can delay decision-making and hinder proactive maintenance planning efforts.
1.2 Prone to Human Error
Manual maintenance logging is inherently susceptible to human error, as it relies on individuals to accurately record and document maintenance activities. Typos, omissions, and inconsistencies in data entry can compromise the integrity and reliability of maintenance logs, leading to incorrect information, misplaced records, and misinterpreted data. These errors can have far-reaching consequences, including inaccurate maintenance scheduling, ineffective resource allocation, and compromised equipment reliability. Additionally, manual data entry increases the risk of data loss or damage due to factors such as misplaced or damaged logbooks, further exacerbating the challenges associated with traditional maintenance logging.
2. Lack of Centralized Information
2.1 Difficulty in Data Retrieval
Traditional maintenance logging often results in fragmented and decentralized information, making it challenging to retrieve and access maintenance data when needed. Maintenance records may be scattered across multiple paper-based logbooks, spreadsheets, or filing systems, making it difficult for maintenance personnel to locate specific information quickly. This lack of centralized information hampers decision-making processes, as maintenance managers may struggle to gain a comprehensive overview of equipment maintenance histories, performance trends, and maintenance priorities. Consequently, delays in data retrieval can impede timely maintenance interventions and hinder proactive maintenance planning efforts.
2.2 Limited Accessibility
Traditional maintenance logging systems often suffer from limited accessibility, as maintenance records may be stored in physical formats or spreadsheets that are not easily accessible to all relevant stakeholders. Maintenance personnel may encounter difficulties accessing maintenance logs due to factors such as geographical distance, time constraints, or restricted access to physical logbooks or filing cabinets. This limited accessibility inhibits collaboration, communication, and knowledge sharing among maintenance teams, as critical maintenance information may not be readily available to all stakeholders when needed. Additionally, limited accessibility may hinder regulatory compliance efforts, as auditors or inspectors may encounter challenges accessing maintenance records during audits or inspections.
Advantages of Implementing a CMMS for Equipment Maintenance Logging
1. Automation of Maintenance Schedules
One of the primary advantages of implementing CMMS is the automation of maintenance scheduling processes. CMMS software enables organizations to create and manage preventive maintenance schedules based on equipment manufacturer recommendations, industry best practices, and regulatory requirements. By automating maintenance schedules, CMMS software ensures that maintenance tasks are performed at the appropriate intervals, reducing the risk of equipment failure, minimizing downtime, and extending equipment lifespan. Additionally, CMMS software generates automated notifications and reminders for upcoming maintenance tasks, enabling maintenance personnel to stay ahead of schedule and prioritize critical maintenance activities.
2. Real-Time Monitoring and Alerts
CMMS software provides real-time monitoring and alerts for equipment performance and maintenance activities. Through integration with sensors, IoT devices, and other monitoring systems, CMMS software enables organizations to track equipment health, performance metrics, and operational status in real time. CMMS software generates automated alerts and notifications for equipment failures, abnormalities, and maintenance requirements, enabling maintenance personnel to respond promptly and take corrective action. Real-time monitoring and alerts provided by CMMS software enhance equipment reliability, minimize downtime, and optimize maintenance interventions, ultimately improving operational efficiency and productivity.
3. Data Centralization and Accessibility
CMMS software centralizes maintenance-related data, making it easily accessible to relevant stakeholders across the organization. By storing maintenance records, work orders, equipment histories, and inspection reports in a centralized database, CMMS software ensures data integrity, consistency, and security. Maintenance personnel can access maintenance information from any location with internet access, enabling remote collaboration, communication, and decision-making. Additionally, CMMS software provides customizable reporting and analytics tools that enable organizations to analyze maintenance data, identify performance trends, and make data-driven decisions to optimize maintenance strategies and resource allocation.
In conclusion, CMMS software plays an important role in equipment maintenance management by streamlining maintenance workflows, enhancing data management capabilities, and improving operational efficiency. By leveraging the functionalities and advantages of CMMS software, organizations can optimize maintenance operations, maximize equipment uptime, and achieve long-term success in their respective industries.
TABLE OF CONTENTS
Keep Reading
What happens when your most experienced maintenance leader is planning on retiring, taking 20 ...
7 Aug 2025
Today’s maintenance operations have become more complex and sophisticated. Gone are the days ...
5 Aug 2025
Modern warehouses are instrumental to maintaining the smooth operations of supply chains, ...
1 Aug 2025
Computerized Maintenance Management Systems (CMMS) have proven to be essential tools for ...
31 Jul 2025
Sometimes it feels as if technology is expanding at the speed of light. This is an ...
29 Jul 2025
Data Center downtime can have a huge negative impact ranging from damage to the data center’s ...
25 Jul 2025
Whenever a company introduces a new process or technology, it’s followed by a period of ...
24 Jul 2025
Obsolescence often comes unexpectedly, mainly because little attention is given to the ...
22 Jul 2025
Imagine a world where critical assets run smoothly without unexpected downtime, maintenance ...
18 Jul 2025
Imagine you're going through a compliance audit, and the inspector asks for maintenance ...
10 Jul 2025
Maintenance managers understand that disasters are unpredictable and can have a massive ...
4 Jul 2025
Asset lifespan is a key concern for executives and maintenance and facility management teams. ...
3 Jul 2025
Your company recently invested funds and time for new CMMS software, and six months later, it ...
1 Jul 2025
As Computerized Maintenance Management Systems (CMMS) become more connected and cloud-based, ...
1 Jul 2025
Edge computing is an innovative technology that enables data to be processed at the source, ...
24 Jun 2025
Facility management has undergone a significant transformation in recent times. Take, for ...
20 Jun 2025
A facility maintenance plan is at the core of a facility’s operations. This organized ...
19 Jun 2025
In the early days, preventive maintenance could be done effectively with a trained eye and a ...
17 Jun 2025
Sticky notes fall off, whiteboard grids get wiped, and spreadsheets never beep when a ...
13 Jun 2025
Handing a slice of your maintenance workload to a contractor is less about “giving up ...
12 Jun 2025