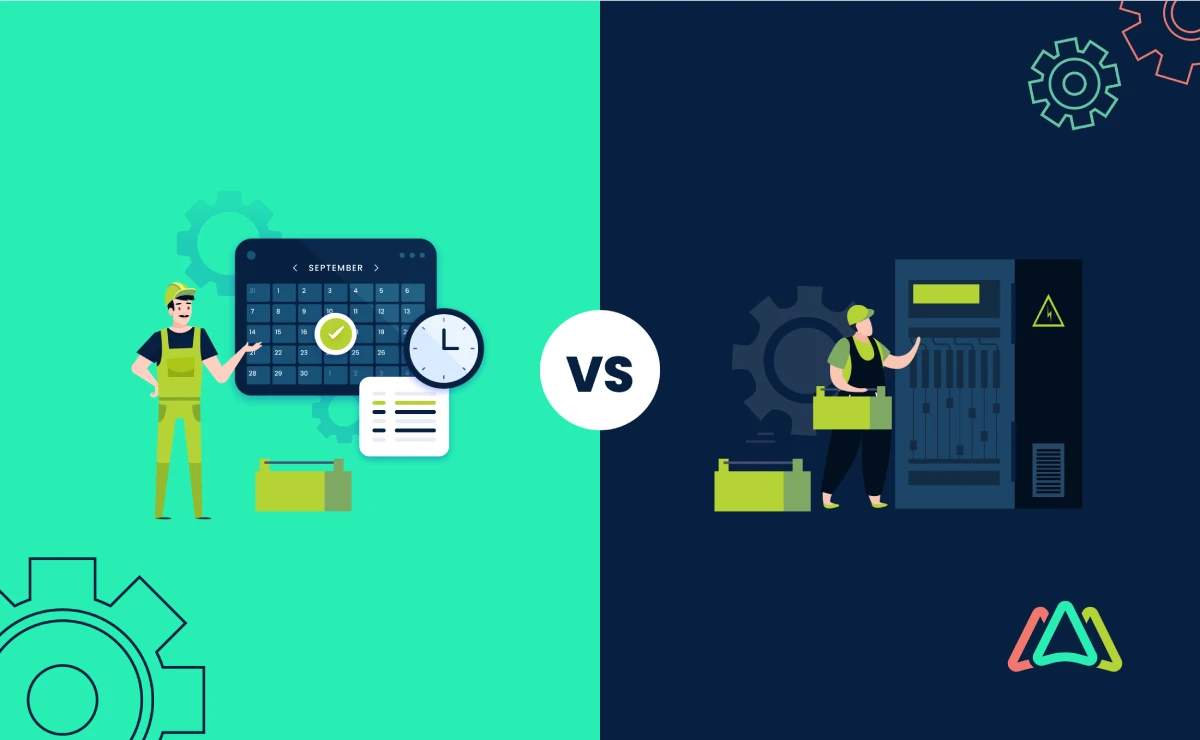
Differences Between Calendar-Based & Meter-Based Preventive Maintenance Work Orders
Introduction
Much of what is written about Computerized Maintenance Management Systems (CMMS) centers on how they streamline maintenance operations. And yes, they do just that, thanks to their sophisticated and robust features and modules. But there’s more to what makes CMMSs the go-to maintenance management solution they are today. Beyond their standard bells and whistles, they also offer a range of options that add further breadth and versatility to a CMMS software.
Here, we’ll focus on one of the function options in preventive maintenance, a CMMS hallmark feature. We’re going to learn that even within preventive maintenance, there are options from which maintenance managers can choose how to implement work orders. Specifically, calendar-based and meter-based preventive maintenance work orders are two approaches used in maintenance management to ensure equipment and assets' smooth functioning and longevity.
Calendar-Based and Meter-Based Preventive Maintenance Defined
Calendar-based preventive maintenance work orders are scheduled to trigger according to specific time intervals, such as weekly, monthly, or annually, regardless of the equipment's usage. This approach ensures regular maintenance tasks are performed to prevent equipment deterioration and minimize unexpected breakdowns. The preventive maintenance work orders trigger based on a set time interval.
On the other hand, meter-based preventive maintenance work orders are triggered by predefined usage thresholds, such as machine runtime hours or mileage. This proactive method optimizes resources by avoiding unnecessary servicing while ensuring critical components are serviced before failure.
Calendar-based preventive maintenance work orders are ideal for routine inspections and lubrication. In contrast, meter-based preventive maintenance work orders are best suited for machines that get regular or constant use. Because the equipment is used so much, basing preventive maintenance tasks on usage helps extend equipment lifespan and reduce downtime.
Triggering Mechanism in Calendar-Based and Meter-Based Preventive Maintenance
Calendar-based PMs trigger according to predefined calendar dates or time intervals, independent of the equipment's actual usage. For instance, maintenance managers might schedule regular inspections every three months regardless of whether the equipment has been extensively used. This method ensures that crucial maintenance tasks are regularly performed for equipment reliability and longevity.
On the other hand, meter-based PMs are activated when equipment reaches predetermined usage thresholds, such as a specific number of operating hours, distance traveled, or production cycles completed. For example, a preventive maintenance task might be triggered when a machine reaches 500 operating hours or a vehicle surpasses 10,000 miles. Meter-based activities focus on equipment's workload and usage patterns. Like calendar-based preventive maintenance, they ensure that procedures are carried out by operators and maintenance technicians precisely to prevent wear and tear, breakdowns, and failures.
Flexibility in Calendar-Based and Meter-Based Preventive Maintenance Work Orders
With calendar-based preventive maintenance, the intervals are predetermined and fixed, typically based on calendar dates or regular time intervals. It provides a structured maintenance plan, and because of that, calendar-based work orders lack the flexibility to accommodate variations in equipment usage. For example, if a piece of equipment experiences fluctuating usage patterns, such as seasonal peaks or unexpected changes in production demand, the fixed maintenance schedule may lead to either under-maintenance or over-maintenance. Under-maintenance risks equipment failures and downtime, while over-maintenance results in unnecessary costs and resource allocation.
In contrast, meter-based preventive maintenance work orders offer more flexibility by adapting maintenance intervals according to their actual equipment usage. This method helps maintenance schedules match equipment usage, using resources better and cutting down on downtime and unnecessary maintenance. For instance, if a vehicle experiences increased usage due to seasonal demands, preventive maintenance tasks will trigger and be carried out more frequently, ensuring timely interventions to maintain optimal performance without overspending on maintenance when it's not needed. The flexibility of meter-based preventive maintenance enables maintenance teams to respond more effectively to changing equipment needs, enhancing operational efficiency and minimizing disruptions. The one challenge that comes with meter-based preventive maintenance is that maintenance managers must log meter readings frequently. This means that maintenance professionals must capture meter readings for all of their assets that are on meter-based preventive maintenance plans. The more assets in the operation, the more time this takes.
Cost Considerations Associated with Calendar-Based and Meter-Based Preventive Maintenance
Cost considerations are crucial in determining the effectiveness of maintenance strategies, whether calendar-based or meter-based. After all, the primary purpose of implementing a CMMS is to improve maintenance operations and save money.
With calendar-based work orders, costs tend to be more predictable because maintenance tasks are scheduled regularly, regardless of equipment usage. This predictability in budgeting and resource allocation offers stability for company owners. However, there is a risk of higher costs if maintenance is performed too frequently when assets are not used a lot, leading to potential waste or “over maintenance.” In this situation, the associated costs may outweigh the benefits if the equipment undergoes minimal usage but is subjected to regular maintenance checks. The old saying “better safe than sorry” fits well and is a reasonable counterargument against over-maintenance.
On the other hand, meter-based preventive maintenance work orders come with more cost variability because maintenance tasks are triggered based on equipment usage, which often fluctuates over time. While this approach may result in unpredictable expenses due to varying usage patterns, it also offers opportunities for cost savings through optimized maintenance schedules. Over time, maintenance managers should be able to forecast and predict what resources they will need, even if they rely heavily on meter-based preventive maintenance for their equipment. Recently, many CMMS software systems have incorporated A.I. and machine learning technology to help predict upcoming maintenance, required resources, and costs.
By aligning maintenance tasks with equipment needs, meter-based scheduling reduces the likelihood of unnecessary tasks. The likely result is savings on labor, materials, and downtime costs. For example, if a piece of equipment experiences lower-than-expected usage, meter-based scheduling would delay maintenance tasks accordingly, preventing unnecessary expenditures and planned downtime. On the other hand, since equipment usage is often less predictable, meter-based preventive maintenance can cause unexpected costs.
While calendar-based PMs offer cost predictability, meter-based approaches can save costs through more efficient resource utilization.
Suitability of Calendar-Based and Meter-Based Preventive Maintenance
Calendar-based PMs are best suited for equipment with predictable failure patterns or consistent usage levels over time. These types of equipment generally require routine maintenance at fixed intervals to maintain optimal performance and reliability. For instance, HVAC systems in commercial buildings often follow calendar-based maintenance schedules, with tasks like filter replacements and system checks performed at regular intervals throughout the year. Calendar-based scheduling is also appropriate for assets like fire suppression systems or emergency lighting, where failure risks are relatively constant, and maintenance needs are time-dependent rather than usage-dependent.
In contrast, meter-based work orders are better suited for equipment with variable usage patterns or where their failure is closely related to usage metrics. This approach ensures that maintenance tasks are performed only when actual equipment is used. In doing so, meter-based maintenance activities optimize resource allocation and reduce the risk of unexpected breakdowns.
For example, meter-based preventive maintenance is commonly used for heavy machinery in manufacturing plants, where maintenance needs are directly correlated with operating hours or production cycles. Similarly, vehicles and heavy construction equipment often follow meter-based maintenance schedules, with tasks like oil changes or tire rotations triggered by mileage thresholds. By tailoring maintenance to equipment usage patterns, meter-based preventive maintenance work orders optimize efficiency and prolong equipment lifespan.
Accuracy of Calendar-Based and Meter-Based Preventive Maintenance
Calendar-based work orders offer a structured approach to maintenance scheduling. However, this approach is less accurate with respect to the equipment’s maintenance needs. Since these tasks are scheduled based on predetermined time intervals rather than actual equipment usage, there's a risk that the maintenance tasks being performed may occur either too early or too late. For example, if equipment experiences higher-than-expected usage between scheduled maintenance intervals, important maintenance tasks might be overdue, leading to an increased risk of failure and downtime. On the other hand, if usage is lower than anticipated, performing maintenance too frequently can result in unnecessary costs and resource allocation.
In contrast, meter-based preventive maintenance work orders offer a more accurate approach as they are directly linked to equipment usage metrics such as operating hours, mileage, or production cycles. By coordinating maintenance tasks with actual equipment usage patterns, meter-based scheduling ensures that maintenance interventions occur precisely when needed to prevent breakdowns or deterioration.
For instance, a meter-based approach for a fleet triggers maintenance tasks like oil changes or part replacements based on mileage thresholds, optimizing resource allocation and minimizing the risk of unexpected downtime. Overall, meter-based preventive maintenance work orders enhance accuracy in maintenance timing by adapting to real-time equipment usage, optimizing and improving operational efficiency and reducing maintenance costs.
Conclusion
Both calendar-based and meter-based maintenance approaches have pros and cons, making them suitable for different situations. These situations depend on equipment type, usage patterns, maintenance needs, and costs.
Calendar-based schedules are straightforward but lack accuracy and can result in over or under-maintenance. In contrast, meter-based preventive maintenance schedules adapt to actual usage, and therefore maintenance intervention is more precise. However, this approach requires more precision and frequent meter log tracking. Combining elements of both methods can offer the best of both worlds, allowing for tailored maintenance plans that optimize reliability, fees, and efficiency. By blending these approaches, organizations can ensure timely maintenance while minimizing downtime and expenses, ultimately enhancing overall operational effectiveness. This hybrid approach allows maintenance programs to adapt to the specific needs of each piece of equipment, optimizing resource allocation and improving overall operational efficiency.
TABLE OF CONTENTS
Keep Reading
Computerized Maintenance Management Systems (CMMS) have increasingly become the go-to tools ...
19 Aug 2025
It doesn’t seem to matter which energy provider you choose; the bottom line is that energy ...
15 Aug 2025
In FDA-regulated industries such as pharmaceuticals, medical devices, biotechnology, and food ...
14 Aug 2025
B2C businesses, such as retail, hospitality, and food service, operate in a highly ...
8 Aug 2025
What happens when your most experienced maintenance leader is planning on retiring, taking 20 ...
7 Aug 2025
Today’s maintenance operations have become more complex and sophisticated. Gone are the days ...
5 Aug 2025
Modern warehouses are instrumental to maintaining the smooth operations of supply chains, ...
1 Aug 2025
Computerized Maintenance Management Systems (CMMS) have proven to be essential tools for ...
31 Jul 2025
Sometimes it feels as if technology is expanding at the speed of light. This is an ...
29 Jul 2025
Data Center downtime can have a huge negative impact ranging from damage to the data center’s ...
25 Jul 2025
Whenever a company introduces a new process or technology, it’s followed by a period of ...
24 Jul 2025
Obsolescence often comes unexpectedly, mainly because little attention is given to the ...
22 Jul 2025
Imagine a world where critical assets run smoothly without unexpected downtime, maintenance ...
18 Jul 2025
Imagine you're going through a compliance audit, and the inspector asks for maintenance ...
10 Jul 2025
Maintenance managers understand that disasters are unpredictable and can have a massive ...
4 Jul 2025
Asset lifespan is a key concern for executives and maintenance and facility management teams. ...
3 Jul 2025
Your company recently invested funds and time for new CMMS software, and six months later, it ...
1 Jul 2025
As Computerized Maintenance Management Systems (CMMS) become more connected and cloud-based, ...
1 Jul 2025
Edge computing is an innovative technology that enables data to be processed at the source, ...
24 Jun 2025
Facility management has undergone a significant transformation in recent times. Take, for ...
20 Jun 2025