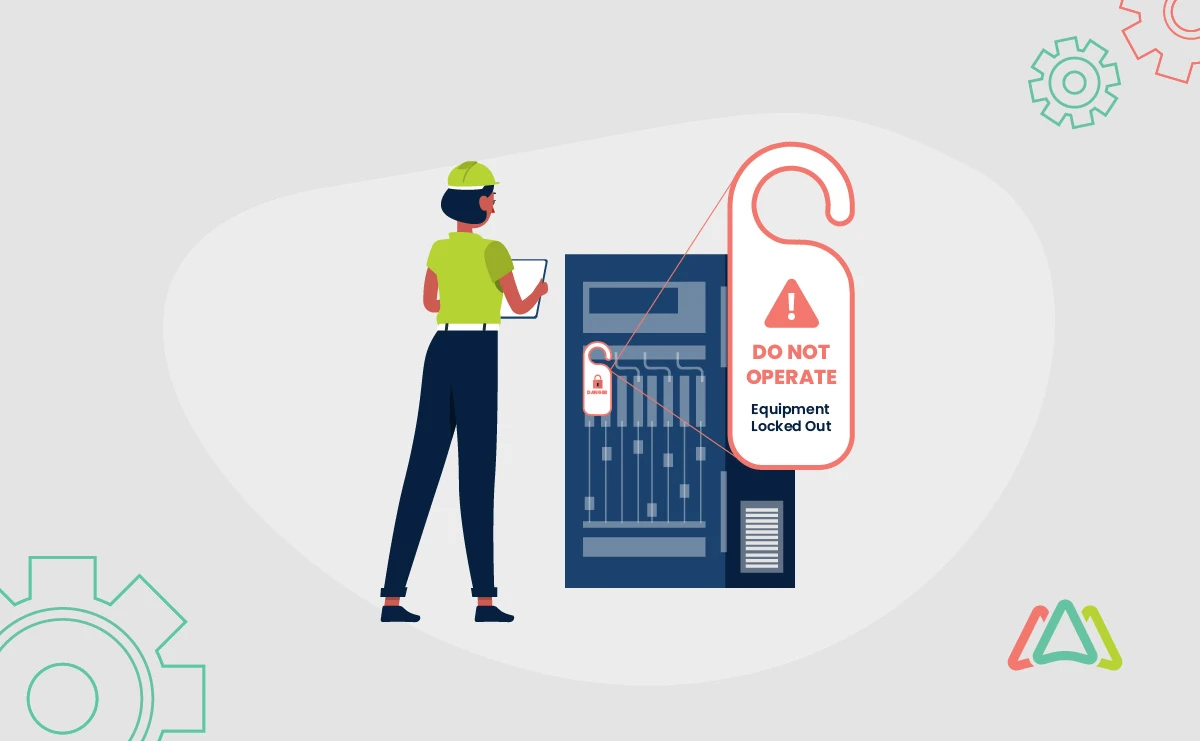
Understanding Lockout Tagout (LOTO) to Maximize Maintenance Safety & Efficiency
In maintenance operations management, ensuring the safety of personnel and preventing accidents is essential. Lockout Tagout (LOTO) is a safety procedure used to control hazardous energy sources during maintenance, servicing, or repair of machinery and equipment. The process involves isolating energy sources, such as electrical, mechanical, hydraulic, pneumatic, or thermal, and ensuring that they are rendered inoperative to prevent unexpected startup or release of energy.
LOTO plays a critical role in safeguarding workers from the dangers associated with hazardous energy. By implementing LOTO procedures, maintenance personnel are protected from accidental contact with energized equipment, which can lead to severe injuries, electrocution, or even fatalities. LOTO also helps prevent equipment damage, production delays, and costly downtime resulting from accidents or unexpected equipment activations.
What is Lockout Tagout (LOTO)?
Lockout Tagout (LOTO) is a safety procedure used to ensure that hazardous energy sources are isolated and rendered inoperative before maintenance work begins. Its primary purpose is to prevent unexpected startup, release of stored energy, or accidental activation of machinery and equipment, which could endanger the lives of maintenance personnel.
Key Components of a LOTO Procedure
- Lockout Devices: Lockout devices are physical mechanisms, such as padlocks, lockout hasps, and lockout tags, used to secure energy isolation devices in the off or safe position. These devices prevent the inadvertent operation of equipment by physically preventing the activation of controls or switches.
- Tagout Devices: Tagout devices, typically durable tags or labels, are attached to lockout devices to provide additional visual indication that energy isolation procedures are in place. Tagout tags contain essential information, such as the name of the authorized employee performing the lockout, the reason for the lockout, and the expected duration of the lockout.
- Procedures for Energy Isolation: LOTO procedures involve a series of steps to safely isolate and control energy sources. This includes identifying all energy sources associated with the equipment, de-energizing the equipment using appropriate controls or switches, and locking and tagging out energy isolation devices to prevent accidental re-energization.
Legal Requirements and Standards Related to LOTO
Numerous regulatory agencies, such as the Occupational Safety and Health Administration (OSHA) in the United States and the Health and Safety Executive (HSE) in the United Kingdom, have established legal requirements and standards related to LOTO to protect workers from the hazards of hazardous energy. These requirements typically include:
- Mandating the development and implementation of written LOTO procedures.
- Training employees on proper LOTO procedures, including authorized employees responsible for performing LOTO and affected employees who work in areas where LOTO is being performed.
- Conducting periodic inspections and audits to ensure compliance with LOTO procedures and regulations.
- Providing appropriate lockout and tagout devices and equipment necessary for effective energy isolation.
Adhering to these legal requirements and standards is essential for ensuring workplace safety and compliance with regulatory obligations related to LOTO. Failure to comply with LOTO regulations can result in severe penalties, fines, and legal liabilities for employers. Therefore, it is important for organizations to prioritize LOTO compliance and establish robust procedures to protect the safety and well-being of their employees.
Risks and Consequences of Inadequate LOTO Procedures
Inadequate Lockout Tagout (LOTO) procedures can have severe consequences, endangering the lives of workers, causing financial losses, and exposing organizations to legal liabilities.
Financial and Reputational Costs of Accidents
- Medical Expenses: Accidents resulting from inadequate LOTO procedures can lead to significant medical expenses, including emergency treatment, hospitalization, and rehabilitation costs for injured workers.
- Production Downtime: Equipment-related accidents can disrupt production schedules, leading to costly downtime and delays in project timelines. The financial impact of production interruptions can be substantial, affecting revenue and profitability.
- Workplace Morale: Accidents can have a negative impact on workplace morale and employee morale, leading to decreased productivity, increased absenteeism, and turnover rates. Employees may lose confidence in the organization's commitment to safety, affecting overall morale and employee engagement.
- Reputation Damage: Accidents resulting from inadequate LOTO procedures can tarnish an organization's reputation and erode trust among stakeholders, including customers, investors, and regulatory authorities. Negative publicity and media attention can further damage the organization's brand image and market credibility.
Legal Ramifications for Non-Compliance with LOTO Regulations
- OSHA Citations: Regulatory agencies, such as OSHA in the United States, have strict regulations governing LOTO procedures. Non-compliance with LOTO regulations can result in OSHA citations, fines, and penalties for organizations found to have violated safety standards.
- Civil Lawsuits: Injured workers or their families may file civil lawsuits against employers for negligence or failure to provide a safe work environment. Legal settlements, court costs, and attorney fees associated with these lawsuits can impose significant financial burdens on organizations.
- Criminal Charges: In cases of egregious violations or willful disregard for safety regulations, employers and responsible individuals may face criminal charges, including fines, imprisonment, or both. Criminal prosecutions for workplace accidents resulting from inadequate LOTO procedures underscore the seriousness of safety violations.
Implementing an Effective LOTO Program
Implementing a robust Lockout Tagout (LOTO) program is essential to safeguard workers and prevent accidents caused by hazardous energy sources.
1. Conducting a Thorough Risk Assessment
Before implementing LOTO procedures, it's essential to conduct a comprehensive risk assessment to identify potential hazards associated with hazardous energy sources. This involves analyzing equipment, machinery, and processes to determine the types of energy present, potential hazards, and the likelihood of accidents occurring. By understanding the specific risks within the workplace, organizations can develop targeted LOTO procedures to mitigate these risks effectively.
2. Developing Comprehensive LOTO Procedures
Based on the findings of the risk assessment, organizations should develop detailed LOTO procedures that outline step-by-step instructions for isolating energy sources and performing maintenance tasks safely. These procedures should include:
- Identification of energy sources and equipment requiring LOTO.
- The sequence of steps for isolating energy sources, including the use of lockout and tagout devices.
- Verification procedures to ensure energy isolation is successful before work begins.
- Protocols for removing lockout/tagout devices once maintenance is complete.
- Emergency procedures for situations where LOTO procedures cannot be followed, or unexpected hazards arise.
LOTO procedures should be written in clear and concise language, easily accessible to all employees involved in maintenance activities, and regularly reviewed and updated to reflect changes in equipment or processes.
3. Training Employees on LOTO Protocols and Procedures
Effective training is essential for ensuring that employees understand and adhere to LOTO protocols and procedures. All personnel involved in maintenance activities, including maintenance technicians, supervisors, and affected employees, should receive comprehensive training on LOTO requirements, including:
- The purpose and importance of LOTO.
- How to identify energy sources and equipment requiring LOTO.
- Proper procedures for applying and removing lockout and tagout devices.
- Recognizing and responding to potential hazards and emergencies.
- Training should be conducted regularly, with refresher courses provided as needed, to reinforce knowledge and ensure compliance with LOTO procedures.
4. Regular Maintenance and Review of LOTO Procedures
Maintaining an effective LOTO program requires ongoing maintenance and review of LOTO procedures to ensure they remain up-to-date and effective. Organizations should establish processes for:
- Regular inspections of equipment and energy control devices to ensure they are in good working condition.
- Periodic audits of LOTO procedures to identify areas for improvement or updates.
- Reviewing incident reports and near-miss incidents to identify trends or issues that may require changes to LOTO procedures.
- Providing opportunities for employee feedback and input on LOTO procedures to enhance their effectiveness and relevance.
Integrating LOTO into Maintenance Operations Management
Incorporating LOTO into Maintenance Schedules and Planning
- Prioritize LOTO in Maintenance Planning: When scheduling maintenance activities, LOTO procedures should be given top priority. Maintenance planners should ensure that adequate time is allocated for performing LOTO steps, including equipment isolation, lockout/tagout device application, and verification of energy isolation.
- Coordinate LOTO with Production Schedules: Collaborate closely with production or operations teams to align LOTO activities with production schedules. Identify windows of opportunity for performing maintenance work when equipment can be safely shut down without disrupting production processes.
- Include LOTO Requirements in Work Orders: Ensure that LOTO requirements for maintenance tasks are clearly outlined in work orders. This includes specifying the equipment and energy sources requiring lockout/tagout, detailing the steps for energy isolation, and providing any necessary safety precautions or equipment.
- Review LOTO Procedures During Pre-Job Briefings: Conduct pre-job briefings before starting maintenance work to review LOTO procedures with the maintenance team. Confirm that all necessary lockout/tagout devices are available and that personnel understand their roles and responsibilities for implementing LOTO.
Communication and Collaboration Between Maintenance and Operations Teams
- Establish Clear Lines of Communication: Foster open communication channels between maintenance and operations teams to ensure that LOTO procedures are effectively coordinated. Designate points of contact within each team responsible for communicating LOTO-related information and addressing any concerns or questions.
- Collaborate on LOTO Planning: Involve operations personnel in the planning and execution of LOTO procedures to ensure that maintenance activities align with operational priorities and schedules. Seek input from operators who have valuable insights into equipment operation and potential risks associated with energy sources.
- Provide Cross-Training Opportunities: Offer cross-training opportunities for maintenance and operations personnel to familiarize them with LOTO procedures and promote mutual understanding of each team's roles and responsibilities. This enables better collaboration and ensures that everyone is equipped to contribute to a safe working environment.
- Conduct Joint Safety Reviews: Periodically conduct joint safety reviews or walkthroughs with maintenance and operations teams to identify potential hazards, evaluate LOTO procedures, and address any gaps or opportunities for improvement. Encourage collaboration and information sharing to enhance safety awareness and adherence to LOTO protocols.
Utilizing a CMMS for Efficient LOTO Management
Integrating Lockout Tagout (LOTO) procedures into maintenance operations requires meticulous planning, clear communication, and effective management of procedures and documentation. A Computerized Maintenance Management System (CMMS) can significantly enhance LOTO management by providing a centralized platform for organizing, tracking, and executing LOTO procedures. Here's how organizations can leverage a CMMS for efficient LOTO management:
1. Centralized LOTO Documentation
A CMMS serves as a centralized repository for storing LOTO procedures, equipment lockout/tagout instructions, and relevant documentation. Maintenance teams can access up-to-date LOTO procedures and guidelines directly from the CMMS, ensuring consistency and accuracy across the organization.
2. Automated Work Order Generation
CMMS software can automate the generation of work orders for maintenance tasks, including those requiring LOTO procedures. Maintenance planners can create work orders that include specific LOTO instructions and requirements, streamlining the scheduling and execution of LOTO-related activities.
3. Integration with Equipment Data
By integrating with equipment data and asset management modules, a CMMS can provide maintenance technicians with detailed information about equipment energy sources, isolation points, and lockout/tagout procedures. This ensures that technicians have access to critical information needed to perform LOTO procedures safely and efficiently.
4. Mobile Accessibility
Many CMMS solutions offer mobile applications that allow maintenance technicians to access LOTO procedures and work orders from anywhere using smartphones or tablets. This mobile accessibility enables technicians to review LOTO instructions on-site, capture digital signatures for LOTO verification, and update LOTO status in real time, enhancing workflow efficiency.
5. Real-Time Tracking and Notifications
CMMS software can track the status of LOTO procedures in real time, providing visibility into which equipment is currently locked out and tagged out for maintenance. Supervisors and managers can receive notifications when LOTO procedures are initiated, completed, or require verification, allowing for proactive monitoring and oversight of LOTO activities.
6. Audit Trail and Compliance Reporting
A CMMS maintains a comprehensive audit trail of all LOTO-related activities, including lockout/tagout initiation, verification, and removal. This audit trail serves as documentation for regulatory compliance and can be used to demonstrate adherence to LOTO procedures during inspections and audits.
7. Training and Certification Management
CMMS software can track employee training and certification in LOTO procedures, ensuring that only authorized personnel are permitted to perform lockout/tagout activities. Organizations can schedule and monitor LOTO training sessions, track certification expiry dates, and ensure that employees remain compliant with LOTO regulations.
8. Continuous Improvement and Analysis
With built-in reporting and analytics capabilities, a CMMS enables organizations to analyze LOTO performance metrics, identify trends, and pinpoint areas for improvement. By leveraging data insights, organizations can refine LOTO procedures, optimize workflow processes, and enhance overall safety and efficiency in maintenance operations.
Best Practices for LOTO in Different Industrial Settings
1. LOTO Procedures for Electrical Maintenance
- Identify Energy Sources: Clearly identify all energy sources associated with electrical equipment, including power supplies, circuits, and control panels.
- Isolate Energy Sources: De-power electrical circuits by switching off circuit breakers or disconnecting power sources. Use lockout devices to secure switches and control panels in the off position.
- Test for Voltage: Before starting work, use appropriate voltage testing equipment to verify that electrical circuits are shut off and safe to work on.
- Apply Lockout/Tagout Devices: Affix lockout/tagout devices to circuit breakers, disconnect switches, and other energy isolation points to prevent accidental turning on.
- Complete Electrical Safety Training: Ensure that maintenance personnel receive comprehensive training on electrical safety practices, including proper LOTO procedures and precautions for working on electrically powered equipment.
2. LOTO Procedures for Mechanical Maintenance
- Identify Mechanical Energy Sources: Identify mechanical energy sources such as moving parts, hydraulic systems, and pneumatic systems associated with machinery and equipment.
- Complete Electrical Safety Training: Ensure that maintenance personnel receive comprehensive training on electrical safety practices, including proper LOTO procedures and precautions for working on electrically powered equipment.
- Isolate Mechanical Energy Sources: Shut down machinery and equipment using appropriate controls and switches. Use lockout devices to secure energy isolation points, such as valves, levers, and control panels.
- Relieve Pressure and Tension: Before performing maintenance, release pressure and tension from hydraulic and pneumatic systems to prevent unexpected movement or activation of equipment.
- Apply Lockout/Tagout Devices: Apply lockout/tagout devices to energy isolation points to prevent accidental startup or movement of machinery during maintenance activities.
- Implement Machine-Specific Procedures: Follow manufacturer's guidelines and specific LOTO procedures for each piece of machinery or equipment to ensure safe maintenance practices.
3. LOTO Procedures for Confined Space Work
Identify Confined Spaces: Identify confined spaces within the workplace, such as tanks, vessels, and pipelines, that may require LOTO procedures for maintenance activities.
- Test Atmospheric Conditions: Before entry, test the atmosphere inside confined spaces for oxygen levels, flammable gasses, and toxic substances to ensure safe working conditions.
- Implement Machine-Specific Procedures: Follow manufacturer's guidelines and specific LOTO procedures for each piece of machinery or equipment to ensure safe maintenance practices.
- Isolate Energy Sources: Isolate energy sources, such as electrical, mechanical, or thermal energy, associated with confined space equipment using lockout/tagout devices.
- Implement Entry Control Measures: Establish entry control measures, including permits and procedures, to control access to confined spaces and ensure that only authorized personnel enter.
- Provide Emergency Rescue Equipment: Equip personnel working in confined spaces with appropriate personal protective equipment (PPE) and emergency rescue equipment, such as harnesses and lifelines, to ensure their safety in case of emergencies.
4. LOTO Procedures for Hot Work
- Identify Hot Work Areas: Identify areas where hot work, such as welding, cutting, or brazing, is performed and implement LOTO procedures to prevent accidents.
- Isolate Energy Sources: Shut down equipment and machinery that may pose ignition hazards during hot work activities. Use lockout devices to secure energy isolation points and prevent accidental startup.
- Implement Fire Prevention Measures: Implement fire prevention measures, such as removing combustible materials and providing fire extinguishers, to mitigate the risk of fires during hot work activities.
- Establish Safe Work Zones: Establish designated safe work zones for hot work activities, ensuring adequate ventilation and fire protection measures are in place to protect workers and surrounding areas.
- Provide Hot Work Training: Ensure that personnel performing hot work activities receive specialized training on fire safety, hazard identification, and proper LOTO procedures to minimize risks and ensure safe working conditions.
By implementing these best practices tailored to different industrial settings, organizations can enhance the effectiveness of Lockout Tagout (LOTO) procedures and minimize the risks associated with maintenance activities.
Overcoming Common Challenges in LOTO Implementation
1. Resistance to Change and Lack of Awareness
- Education and Training: Provide comprehensive training sessions to educate employees about the importance of LOTO procedures, the risks associated with hazardous energy sources, and the potential consequences of non-compliance. Increasing awareness can help alleviate resistance by highlighting the importance of safety protocols.
- Demonstrate Success Stories: Share success stories of organizations that have successfully implemented LOTO procedures. Highlighting the positive impact of LOTO on safety, productivity, and incident reduction can motivate employees to embrace the change.
- Engage Employees: Involve employees in the development of LOTO procedures and solicit their input on ways to improve safety protocols. By empowering employees to participate in the process, organizations can foster a sense of ownership and commitment to LOTO implementation.
- Continuous Communication: Maintain open lines of communication with employees throughout the implementation process. Address concerns, provide regular updates on progress, and encourage feedback to ensure that employees feel informed and involved in the transition.
2. Ensuring Compliance Among Employees
- Clear Policies and Procedures: Develop clear and concise LOTO policies and procedures that outline expectations, responsibilities, and consequences for non-compliance. Ensure that all employees receive copies of these documents and understand their role in adhering to LOTO protocols.
- Training and Education: Provide regular training sessions to refresh employees' knowledge of LOTO procedures and reinforce the importance of compliance. Offer certifications or incentives to employees who demonstrate proficiency in LOTO practices to encourage participation and accountability.
- Accountability Measures: Implement accountability measures, such as audits, inspections, and disciplinary actions for non-compliance with LOTO procedures. Hold employees accountable for following protocols and address any lapses in adherence promptly and consistently.
- Positive Reinforcement: Recognize and reward employees who demonstrate exemplary compliance with LOTO procedures. Celebrate achievements, acknowledge contributions to safety, and create a positive work culture that values and prioritizes safety compliance.
3. Addressing Language and Cultural Barriers in Multinational Workplaces
- Multilingual Training Materials: Develop LOTO training materials, including manuals, videos, and presentations, in multiple languages to accommodate diverse linguistic backgrounds. Ensure that all employees have access to training materials in their preferred language to facilitate comprehension and understanding.
- Cultural Sensitivity Training: Provide cultural sensitivity training to employees and supervisors to promote understanding and respect for cultural differences in safety practices. Address cultural norms, communication styles, and workplace etiquette to foster inclusivity and cooperation in LOTO implementation.
- Interpreter Services: Offer interpreter services or language support resources to assist employees who may have difficulty understanding LOTO procedures due to language barriers. Ensure that trained interpreters are available to facilitate communication and clarify instructions as needed.
- Peer Support Networks: Establish peer support networks or buddy systems where employees can assist each other in understanding LOTO procedures and overcoming language barriers. Encourage collaboration and teamwork to foster a supportive environment for learning and compliance.
By proactively addressing these common challenges in LOTO implementation, organizations can enhance safety awareness, promote compliance among employees, and create a culture of safety that prioritizes the well-being of all workers, regardless of language or cultural differences.
Monitoring and Analyzing LOTO Effectiveness
1. Data Collection
Establish systems to collect relevant data related to LOTO activities, including incident reports, near-miss incidents, and compliance metrics. Utilize a Computerized Maintenance Management System (CMMS) or other tracking tools to record LOTO usage, completion rates, and any deviations from procedures.
2. Performance Metrics
Define key performance indicators (KPIs) to assess the effectiveness of LOTO procedures, such as the frequency of incidents, time taken to complete LOTO tasks, and adherence to procedural guidelines. Regularly analyze these metrics to identify trends, patterns, and areas requiring improvement.
3. Root Cause Analysis
Conduct root cause analysis of LOTO-related incidents to understand underlying factors contributing to failures or non-compliance. Identify systemic issues, equipment deficiencies, or training gaps that may require corrective action to prevent recurrence.
4. Audit and Inspection Programs
Implement periodic audits and inspections of LOTO procedures to evaluate compliance, identify non-conformities, and assess the overall effectiveness of safety protocols. Utilize checklists, observation tools, and third-party assessments to ensure thorough evaluations.
Updating LOTO Procedures Based on Lessons Learned and Industry Advancements
1. Review Committees
Establish cross-functional review committees or safety teams tasked with regularly reviewing LOTO procedures and incorporating lessons learned from incident investigations, feedback mechanisms, and industry developments.
2. Continuous Training
Provide ongoing training and education to employees on updated LOTO procedures, revised policies, and emerging best practices in safety management. Ensure that employees are informed of changes and equipped with the knowledge and skills necessary for compliance.
3. Benchmarking and Best Practices
Benchmark LOTO procedures against industry standards, regulations, and best practices to identify opportunities for improvement. Collaborate with industry peers, participate in professional networks, and seek guidance from safety experts to stay abreast of advancements.
4. Document Control
Maintain a robust document control system to manage revisions, updates, and version control of LOTO procedures. Clearly communicate changes to all relevant stakeholders and ensure that updated documents are readily accessible to employees.
By prioritizing continuous improvement and evaluation of LOTO procedures, organizations can enhance safety performance, mitigate risks, and cultivate a culture of excellence in workplace safety. Regular monitoring, feedback solicitation, and proactive updates ensure that LOTO protocols remain effective, relevant, and aligned with evolving safety standards and industry advancements.
TABLE OF CONTENTS
Keep Reading
What happens when your most experienced maintenance leader is planning on retiring, taking 20 ...
7 Aug 2025
Today’s maintenance operations have become more complex and sophisticated. Gone are the days ...
5 Aug 2025
Modern warehouses are instrumental to maintaining the smooth operations of supply chains, ...
1 Aug 2025
Computerized Maintenance Management Systems (CMMS) have proven to be essential tools for ...
31 Jul 2025
Sometimes it feels as if technology is expanding at the speed of light. This is an ...
29 Jul 2025
Data Center downtime can have a huge negative impact ranging from damage to the data center’s ...
25 Jul 2025
Whenever a company introduces a new process or technology, it’s followed by a period of ...
24 Jul 2025
Obsolescence often comes unexpectedly, mainly because little attention is given to the ...
22 Jul 2025
Imagine a world where critical assets run smoothly without unexpected downtime, maintenance ...
18 Jul 2025
Imagine you're going through a compliance audit, and the inspector asks for maintenance ...
10 Jul 2025
Maintenance managers understand that disasters are unpredictable and can have a massive ...
4 Jul 2025
Asset lifespan is a key concern for executives and maintenance and facility management teams. ...
3 Jul 2025
Your company recently invested funds and time for new CMMS software, and six months later, it ...
1 Jul 2025
As Computerized Maintenance Management Systems (CMMS) become more connected and cloud-based, ...
1 Jul 2025
Edge computing is an innovative technology that enables data to be processed at the source, ...
24 Jun 2025
Facility management has undergone a significant transformation in recent times. Take, for ...
20 Jun 2025
A facility maintenance plan is at the core of a facility’s operations. This organized ...
19 Jun 2025
In the early days, preventive maintenance could be done effectively with a trained eye and a ...
17 Jun 2025
Sticky notes fall off, whiteboard grids get wiped, and spreadsheets never beep when a ...
13 Jun 2025
Handing a slice of your maintenance workload to a contractor is less about “giving up ...
12 Jun 2025