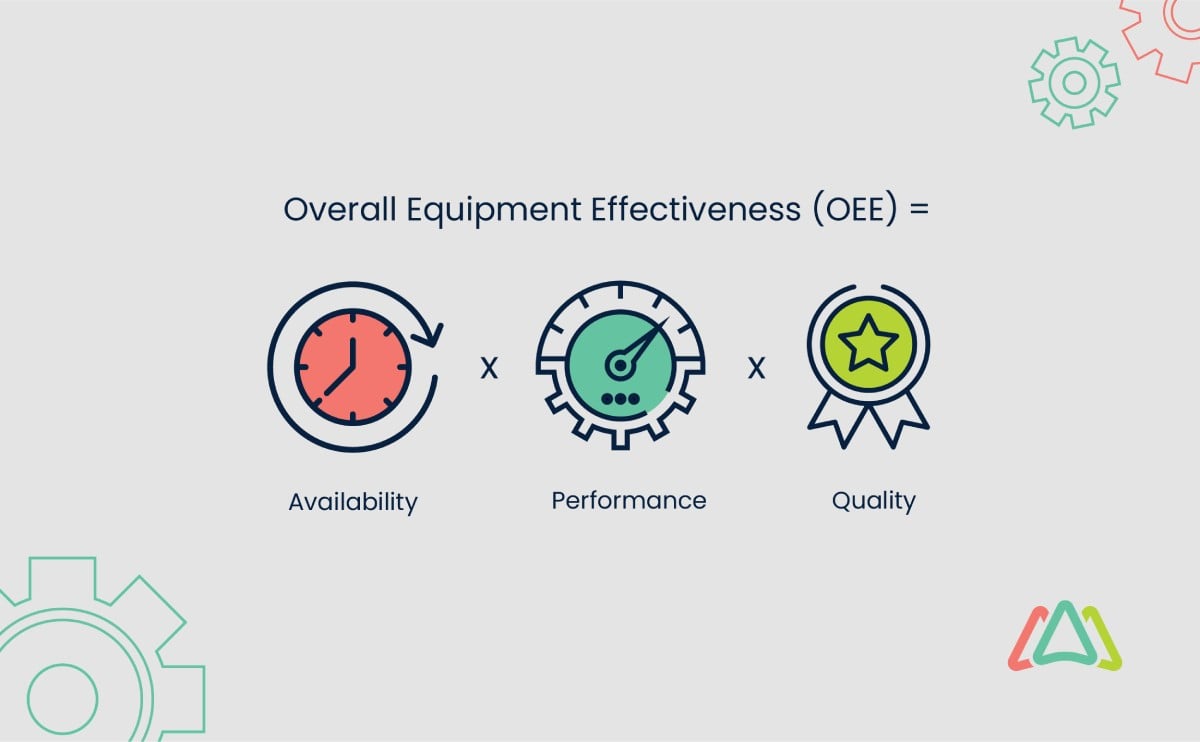
What is OEE & How It's Used to Optimize Maintenance Operations
Introduction
The field of maintenance management is continually growing. Over time, it’s become more sophisticated, more refined and more precise. An evolving development is the Overall Equipment Efficiency or OEE approach. Basically, OEE is a performance metric that is used in manufacturing sectors to measure the effectiveness of its operations or equipment. It provides insights into how efficiently equipment is being utilized in terms of availability, performance, and quality.
The OEE approach had its roots in Total Productive Management (TPM), a strategy first developed by the Japanese in the 1960s and 1970s, primarily for use in its auto industry. By the 1990s, OEE began drawing more attention as manufacturers were increasingly attracted to the leaner manufacturing model developed by the Toyota Production System.
The OEE Breakdown
Briefly, OEE provides a quantitative measure (in other words, a number) of how well a machine or system is utilized and how efficiently it performs what it is created to do. As mentioned above, it also takes into account three key factors: availability, performance, and quality. Each of these factors is assigned a numerical percentage score which is then multiplied together to calculate the OEE percentage. The bottom line is this important metric provides the percentage of good production time for any given asset.
Factors Considered in Calculating OEE
The resulting OEE percentage represents the overall effectiveness of a piece of equipment. Here's a detailed explanation of what goes into calculating each of these factors:
- Availability: This is a measure of the actual uptime of a piece of equipment compared to the planned production time. It takes into account factors such as equipment breakdowns, planned maintenance activities, changeovers, and other issues that cause the equipment to be unavailable for production.
- Performance: This factor evaluates the speed at which the equipment operates compared to its maximum or ideal speed based on its manufacturer’s specifications. It considers factors such as equipment slowdowns, idling, and minor stops that result in a reduction of the equipment's output or productivity.
- Quality: The quality of the products produced by a piece of equipment is assessed by this factor. It measures the number of defective, faulty or non-conforming units produced compared to the total number of units produced. This measure takes into account scrap materials, rework, and other quality-related issues.
To calculate the final OEE percentage, multiply the availability, performance, and quality percentages together. The equation is simple and looks like this:
Overall Equipment Effectiveness
= Availability × Performance × Quality
The resulting single metric, the OEE percentage, provides a comprehensive view of the equipment's overall efficiency and effectiveness. It helps identify areas in need of improvement and serves as a benchmark to measure progress over time.
How OEE is used to Optimize Maintenance Operations
By tracking OEE, maintenance managers are able to identify and prioritize specific areas in need of improvement. Examples of these include: reducing equipment downtime, improving equipment performance, and enhancing product quality. By comparing OEE percentages of different pieces of equipment, it helps maintenance teams focus their efforts on the most critical issues and develop strategies to optimize maintenance activities and minimize unplanned downtime.
OEE can also be used to compare the performance of different equipment or production lines to identify production bottlenecks, allocate resources effectively, and make informed decisions about equipment upgrades or replacements. This fine tuned metric provides actionable insights to direct ongoing improvement initiatives and in doing so, increase overall operational efficiency.
Overcoming OEE Identified Problems
So now that you have your OEE percentage, and you know where the trouble spots are, the question remains, what do you do about them? The following are some of the measures that can be taken to overcome low percentage scores found in availability, performance and quality categories.
Overcoming Availability Deficiencies
Equipment Breakdowns: When it comes to availability deficiencies, equipment breakdowns are the most significant source of unplanned stops and delays. Unplanned downtime can be quite costly to a manufacturer’s operations in terms of output, staffing as well as customer satisfaction.
- Develop a preventive maintenance plan.
- For the most critical production assets, sensors can be used to conduct either predictive maintenance or condition-based maintenance.
- Keep a record of equipment downtime. This type of record keeping offers a starting point from which comparisons can be made once corrective steps have been made as well as providing valuable insights into adjusting a preventive maintenance plan.
Following the above steps, it is possible to more accurately forecast and implement measures to prevent shutdowns. By careful tracking, patterns in downtime may become evident. When the patterns do surface, the conditions that caused them can be avoided. As well, by being able to anticipate breakdowns, shifts can be scheduled accordingly to limit costly resource expenditures.
Planned Downtimes: A second source of availability deficiencies is planned downtimes due to required set-ups and adjustments. The key to limiting the impact of the time needed to complete the set-up and adjustment tasks, is to choose a time that has the least effect on production operations.
- Conduct larger scaled planned downtimes by coordinating set-up and adjustments on several pieces of equipment at the same time. This translates into fewer potentially disruptive planned downtimes.
- Implement a Single-Minute Exchange of Die (SMED) technique which is derived from the lean production protocol. In short, this technique refers to reviewing the activity that takes place during a planned production stop. Look for ways to reduce the steps involved. This may involve having the needed tools readily available at stations adjacent to the equipment being serviced. Or it may require purchasing more efficient tools. In keeping with the SMED technique, the idea is to complete tasks as quickly and accurately as possible.
Overcoming Performance Deficiencies
When considering equipment performance, speed is the major variable. It can be divided into two factors that impact speed; minor stoppages and reduced time.
Minor Stoppages: On its own, a single minor equipment stoppage may not seem like a big deal. However, in a facility with many pieces of equipment running, these minor stoppages add up and can affect a manufacturer’s overall productivity.
- Begin by tracking any differences in equipment run-time
- Train machine operators to fix any minor issues right on the spot. In the long term, this saves time.
- Track patterns of performance loss to determine when they happen. Look for patterns to uncover the root cause that can then be prevented.
- Standardize processes. By following the same process every time, fewer mistakes and minor stops occur or can be more readily recognized.
Reduced speed: Wear and tear, poor maintenance or misuse are the main causes of a loss of speed on a piece of equipment. Think about your car. If it is run too hard or maybe, not at all, or it’s been in several accidents, or hasn’t had regular oil changes, it won’t operate as it should.
- Optimize your production cycle and speed through routine maintenance
- Review and revise your preventive maintenance program as needed
- Train equipment operators to use equipment properly and how to care for it at the end of every shift
Overcoming Quality Deficiencies
Simply put, quality deficiencies equate to defective products. This may be defective equipment parts or problems in the production process such as improper use of equipment by operators.
- Track the types of defects you can observe
- Pay attention to aging equipment since most defects are related to deteriorating equipment.
- Consider when it’s time to replace a piece of equipment. At some point, maintenance and repairs may not be enough if quality remains deficient.
- When replacing a piece of equipment, follow the manufacturer’s guidelines for breaking it in. It often takes several runs to produce optimal results. Once achieved, the asset can be run at its recommended speed.
- Reduce quality variation in new equipment by following the manufacturer’s regular maintenance and routine care guidelines.
A CMMS Can Make Overcoming OEE Deficiencies Easier
This is where a CMMS comes into play. Briefly, CMMS systems are an ever evolving digital utility that fully automates all maintenance management operations. Depending on a company’s size, needs and goals, the CMMS marketplace has a wide range of options and capabilities to select from. Setting CMMSs apart from traditional spreadsheet programs is that they are cloud based and accessible by all authorized users. This robust system makes it possible to run all facility operations including asset management, inventory control, preventive maintenance, work order management, real time maintenance data and reporting, safety adherence protocols, maintenance history, real time and shareable information that is captured, and cost tracking.
Here are just some ways a CMMS can facilitate overcoming the OEE deficiencies already described:
- Creates an automated preventive maintenance schedule that notifies team members assigned to the task, provides maintenance procedures, identifies tools and any parts needed to conduct a particular maintenance task
- Creates autonomous maintenance
- Integrates machine sensor data into maintenance procedures
- Creates real time reports on downtimes, quality issues, repairs, etc.
- Creates work orders for equipment deficiencies that fall outside of routine maintenance
- Tracks the history of OEE percentage scores across time
These are just a few of many benefits CMMS brings to addressing any OEE deficiencies found.
Conclusion
Overall, OEE is a valuable tool for maintenance operations as it enables data-driven decision-making, fosters continuous improvement, and helps optimize the utilization and performance of equipment in manufacturing environments. By adding a CMMS, these efforts can be put into action quickly and seamlessly.
TABLE OF CONTENTS
Keep Reading
The world of IoT is growing rapidly in almost every aspect of life across a variety of ...
29 Aug 2025
The adoption of Computerized Maintenance Management Systems (CMMS) presents a puzzling ...
28 Aug 2025
For the sake of repetition, a CMMS (Computerized Maintenance Management System) is the hub ...
26 Aug 2025
Too often, production and maintenance departments operate in silos, resulting in a lack of ...
22 Aug 2025
Many organizations struggle with scaling maintenance operations, mainly because some don’t ...
21 Aug 2025
Computerized Maintenance Management Systems (CMMS) have increasingly become the go-to tools ...
19 Aug 2025
It doesn’t seem to matter which energy provider you choose; the bottom line is that energy ...
15 Aug 2025
In FDA-regulated industries such as pharmaceuticals, medical devices, biotechnology, and food ...
14 Aug 2025
B2C businesses, such as retail, hospitality, and food service, operate in a highly ...
8 Aug 2025
What happens when your most experienced maintenance leader is planning on retiring, taking 20 ...
7 Aug 2025
Today’s maintenance operations have become more complex and sophisticated. Gone are the days ...
5 Aug 2025
Modern warehouses are instrumental to maintaining the smooth operations of supply chains, ...
1 Aug 2025
Computerized Maintenance Management Systems (CMMS) have proven to be essential tools for ...
31 Jul 2025
Sometimes it feels as if technology is expanding at the speed of light. This is an ...
29 Jul 2025
Data Center downtime can have a huge negative impact ranging from damage to the data center’s ...
25 Jul 2025
Whenever a company introduces a new process or technology, it’s followed by a period of ...
24 Jul 2025
Obsolescence often comes unexpectedly, mainly because little attention is given to the ...
22 Jul 2025
Imagine a world where critical assets run smoothly without unexpected downtime, maintenance ...
18 Jul 2025
Imagine you're going through a compliance audit, and the inspector asks for maintenance ...
10 Jul 2025
Maintenance managers understand that disasters are unpredictable and can have a massive ...
4 Jul 2025