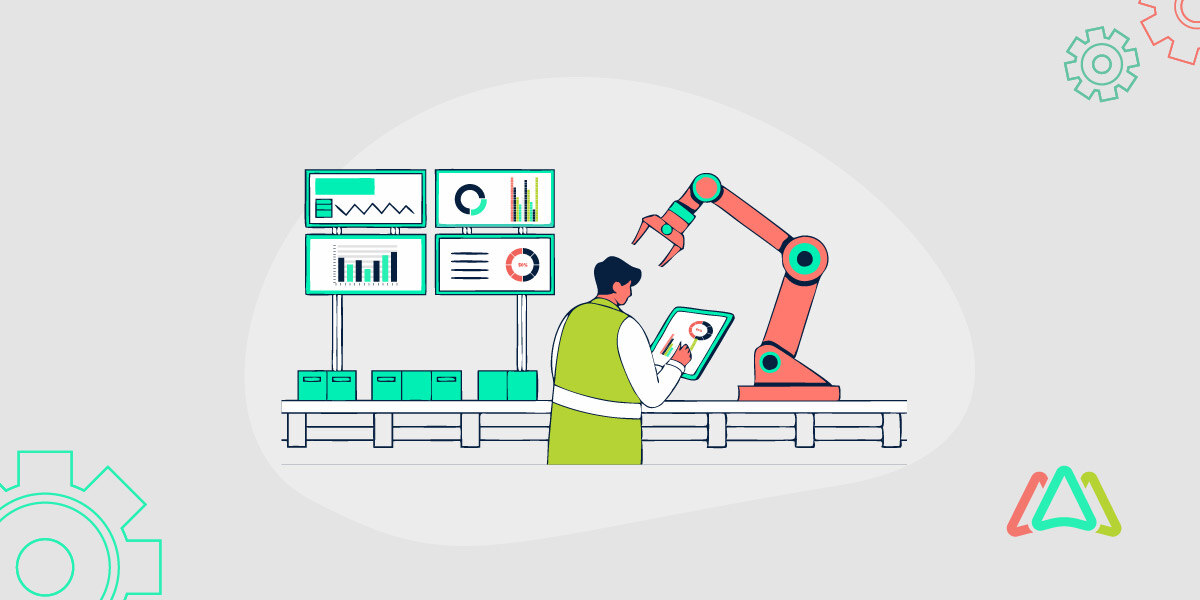
How Automated Data Collection Enables Your CMMS to Provide Real-Time Insights
A Computerized Maintenance Management System (CMMS) is a powerful software solution designed to streamline and optimize maintenance operations for assets and facilities by centralizing all maintenance-related data. This enables organizations to track work orders efficiently, manage inventory, schedule preventive maintenance, and monitor equipment performance, ultimately reducing downtime, improving asset lifespan, and enhancing operational efficiency.
One of the most transformative capabilities in modern CMMS solutions is automated data collection, which continuously captures data from assets through methods such as IoT sensors, QR code scans, and real-time system integration. This significantly reduces the need for manual data entry, providing maintenance teams with immediate access to accurate, up-to-date information. Recent advancements in IoT and machine learning have further enhanced automated data collection, allowing for more granular and predictive insights. In today’s data-driven business landscape, real-time insights are critical for informed decision-making and proactive maintenance, enabling organizations to anticipate needs and respond to issues before they escalate. By leveraging automated data collection to generate real-time insights, a CMMS empowers maintenance teams to stay ahead of issues, optimize resources, and drive continuous improvement across operations.
Evolution of Maintenance - From Manual Data Collection to Automated.
Maintenance data collection has come a long way from traditional methods like manual logs, paper records, and periodic inspections. These manual approaches often involve time-consuming processes, leaving room for human error and making it challenging to keep data up to date. Because data entry was irregular and often delayed, maintenance teams struggled with outdated information, making it difficult to predict issues or make proactive decisions with precision.
The advent of automated data collection has revolutionized maintenance management. With tools like IoT sensors, QR codes, and system integrations, data is now collected continuously and with greater accuracy. IoT sensors track equipment conditions, such as temperature, pressure, or usage, providing real-time updates directly to a CMMS. QR codes enable instant asset tracking and reporting via mobile devices, and system integrations link various platforms, creating a seamless data environment.
This shift to automation enhances data quality and timeliness. Automated data collection ensures that maintenance teams have a constant flow of up-to-date information, allowing them to monitor asset health, predict issues, and respond proactively. This enables a more strategic, data-driven approach to maintenance, reducing downtime and maximizing asset longevity.
The Role of Automated Data Collection in CMMS
Automated data collection within a CMMS is the process of gathering real-time information from assets without requiring manual input. Using technologies like IoT sensors, QR codes, and integrations with other systems, a CMMS can automatically collect diverse data types: equipment performance metrics, maintenance logs, environmental data (e.g., temperature, humidity), and usage patterns. This continuous flow of accurate data enables maintenance teams to monitor asset health in real time and make informed, proactive decisions based on the latest insights.
Compared to manual data entry, automated data collection significantly boosts efficiency, accuracy, and punctuality. Manual processes can be prone to errors, delays, and data gaps due to human involvement, while automation ensures that data is logged instantly and accurately without interruption. For example, IoT sensors can immediately report any change in equipment status, alerting teams to potential issues before they escalate. This speedy responsiveness is required for effective maintenance planning, allowing for condition-based or predictive maintenance strategies that minimize downtime and extend asset life. With automation, a CMMS software becomes a powerful tool for optimizing maintenance operations, helping organizations achieve higher efficiency, lower costs, and improved asset reliability.
Key Benefits of Automated Data Collection for Real-Time Insights
Improved Decision-Making
Real-time data empowers maintenance teams to make faster, more accurate decisions, especially in urgent situations. With instant access to current equipment conditions, teams can swiftly respond to issues as they arise, minimizing potential downtime and avoiding costly breakdowns.
Enhanced Predictive Maintenance
Automated data collection feeds predictive algorithms with a steady stream of information, enabling the CMMS to forecast maintenance needs accurately. This allows teams to address issues before they result in equipment failure, significantly reducing unplanned downtime and prolonging the lifespan of assets.
Cost Reduction
Automation reduces labor-intensive tasks like manual data entry, saving both time and labor costs. By using data to guide maintenance scheduling and resource allocation, teams can avoid unnecessary repairs, lower material expenses, and maximize the budget allocated to critical assets.
Higher Operational Efficiency
Real-time insights ensure that maintenance activities are targeted and efficient. With continuous data, teams can eliminate redundant maintenance, optimize parts replacement, and ensure that equipment is serviced based on actual needs, resulting in smoother, more streamlined operations.
Regulatory Compliance and Reporting
Automated data collection simplifies compliance reporting, as all necessary data is consistently updated and stored within the CMMS. This ready availability of accurate records ensures that audits and regulatory checks are less time-consuming and more accurate, enhancing transparency and regulatory adherence.
How Automated Data Collection Works within CMMS
Automated data collection in a CMMS relies on a range of data sources and methods, including IoT sensors, QR code scanners, PLCs, and mobile devices, which continuously gather data on asset performance. This data is then transferred in real-time from assets to the CMMS, ensuring up-to-date information. Data integration and aggregation within the CMMS combine data from various assets into one accessible platform, streamlining asset management. Integration with other business systems, like ERP or EAM, is essential for a comprehensive view of operations and smoother data flow across departments. Data processing and analysis then take place within the CMMS, with automated collection ensuring data is ready for immediate analysis, producing real-time insights with minimal manual input, and enabling faster data-driven decision-making.
Industry Applications of Automated Data Collection
Manufacturing
Manufacturing plants use real-time insights to prevent costly equipment downtime. Automated monitoring of metrics like temperature and vibration alerts teams to potential failures early, allowing for timely preventive maintenance. This approach keeps production lines running smoothly and reduces unplanned shutdowns.
Facilities Management
Facility managers rely on real-time data to maintain HVAC, lighting, and utility systems. Automated alerts help identify inefficiencies or malfunctions, enabling quick fixes that improve energy efficiency and lower operational costs while also ensuring a comfortable environment for tenants.
Healthcare
In healthcare, real-time monitoring is essential to keep critical medical equipment, like MRI machines and patient monitors, operational. Automated alerts notify technicians of potential issues, reducing equipment downtime and supporting uninterrupted patient care.
Energy Sector
The energy sector uses predictive maintenance on assets like wind turbines and solar panels to enhance performance. Real-time data on energy output and environmental conditions help anticipate maintenance needs, increase energy efficiency, reduce costs, and extend asset lifespans.
Choosing a CMMS with Strong Data Collection and Analytics Capabilities
Choosing a CMMS with robust data collection and analytics capabilities is essential for effective, data-driven maintenance management. Look for key features like real-time dashboards, customizable analytics, IoT compatibility, and proactive alerts, all of which provide valuable, instant insights into asset health. It’s also vital to choose a system that integrates seamlessly with IoT devices and business platforms (like ERP), creating a unified data ecosystem that supports smoother workflows. As your operations grow, ensure the CMMS you select can scale with your needs and manage increasing data effectively. Finally, prioritize ease of use and accessible training to help your team fully leverage the system’s capabilities from day one. Check out this list of top 10 CMMS providers to review CMMS vendors that offer these core features.
Emerging Trends In Automated Data Collection and CMMS
Advancements in AI, IoT, and mobile technology are shaping the future of automated data collection in CMMS. AI and machine learning are driving powerful predictive analytics that allow CMMS platforms to anticipate maintenance needs with increased accuracy, transforming data into actionable insights. As IoT devices become more integrated, they work alongside edge computing to capture and process data directly on-site, enabling faster response times and reducing reliance on centralized networks. Additionally, the growing emphasis on mobile and remote access means maintenance teams can monitor assets and make real-time decisions from any location, improving flexibility and responsiveness. Together, these trends are enhancing the capabilities of CMMS, paving the way for smarter, more efficient maintenance management.
Conclusion
Automated data collection and real-time insights in CMMS offer transformative benefits, from enhanced decision-making and predictive maintenance to cost savings and improved operational efficiency. By adopting these advanced features, businesses can achieve a proactive maintenance approach, gaining a competitive edge and optimizing asset performance. To experience these advantages firsthand, consider exploring our CMMS solutions and schedule a demo to see how real-time insights can elevate your maintenance strategy.
TABLE OF CONTENTS
Keep Reading
What happens when your most experienced maintenance leader is planning on retiring, taking 20 ...
7 Aug 2025
Today’s maintenance operations have become more complex and sophisticated. Gone are the days ...
5 Aug 2025
Modern warehouses are instrumental to maintaining the smooth operations of supply chains, ...
1 Aug 2025
Computerized Maintenance Management Systems (CMMS) have proven to be essential tools for ...
31 Jul 2025
Sometimes it feels as if technology is expanding at the speed of light. This is an ...
29 Jul 2025
Data Center downtime can have a huge negative impact ranging from damage to the data center’s ...
25 Jul 2025
Whenever a company introduces a new process or technology, it’s followed by a period of ...
24 Jul 2025
Obsolescence often comes unexpectedly, mainly because little attention is given to the ...
22 Jul 2025
Imagine a world where critical assets run smoothly without unexpected downtime, maintenance ...
18 Jul 2025
Imagine you're going through a compliance audit, and the inspector asks for maintenance ...
10 Jul 2025
Maintenance managers understand that disasters are unpredictable and can have a massive ...
4 Jul 2025
Asset lifespan is a key concern for executives and maintenance and facility management teams. ...
3 Jul 2025
Your company recently invested funds and time for new CMMS software, and six months later, it ...
1 Jul 2025
As Computerized Maintenance Management Systems (CMMS) become more connected and cloud-based, ...
1 Jul 2025
Edge computing is an innovative technology that enables data to be processed at the source, ...
24 Jun 2025
Facility management has undergone a significant transformation in recent times. Take, for ...
20 Jun 2025
A facility maintenance plan is at the core of a facility’s operations. This organized ...
19 Jun 2025
In the early days, preventive maintenance could be done effectively with a trained eye and a ...
17 Jun 2025
Sticky notes fall off, whiteboard grids get wiped, and spreadsheets never beep when a ...
13 Jun 2025
Handing a slice of your maintenance workload to a contractor is less about “giving up ...
12 Jun 2025