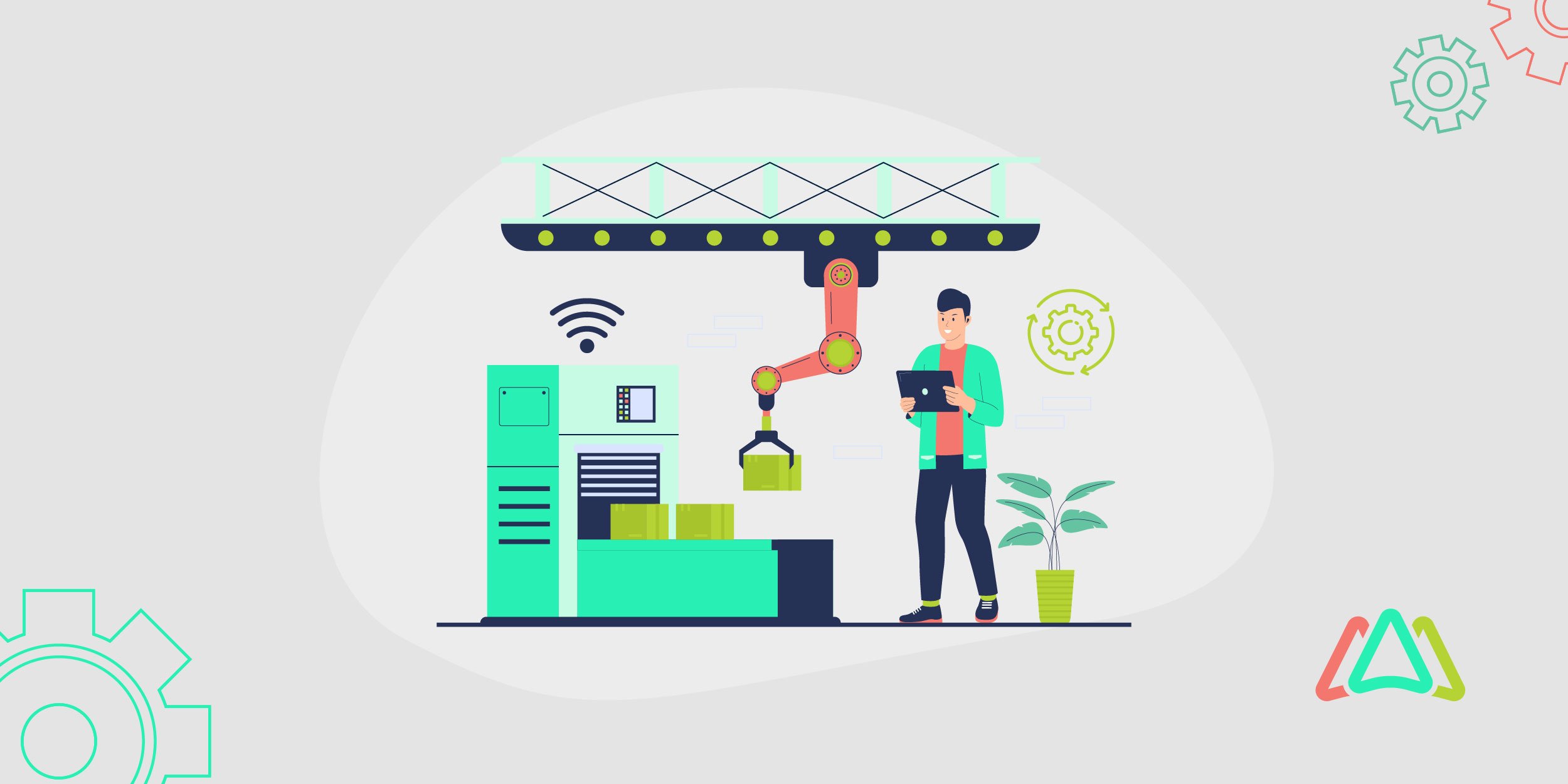
Work Order Lifecycle Automation with Work Order Software
Maintenance management faces complexities across all industries, escalating with organizational size and regulatory demands. The traditional work order process is often inefficient, characterized by phone requests, sticky notes, approval delays, and unclear timelines, often resulting in technicians receiving tasks late. This lack of visibility leads to frustration, missed deadlines, and avoidable downtime.
Work Order Lifecycle Automation transforms this convoluted process into a streamlined workflow. Every step is monitored, tasks are clearly assigned, and escalations are automated. Leveraging intuitive Work Order Software, this approach eliminates confusion and ensures team alignment.
Consider a typical asset breakdown scenario: facility managers must create a maintenance task, detail the required work, assign a technician, and set a deadline. However, common issues arise: maintenance requests accumulate in email inboxes, approvals are held up, technicians overlook crucial updates, and accountability is unclear.
This results in missed SLAs, increased downtime, dissatisfied staff, and a reactive maintenance team. This chaos isn't due to a lack of effort but rather the inability of manual processes to handle the demands of modern facilities.
Imagine a system where every stage of a work order, from submission to completion, is automated, transparent, and tracked in real-time. This is why more maintenance teams are adopting Work Order Lifecycle Automation. It improves the process of task management from request to resolution, preventing oversights. Regardless of the facility and maintenance team size, this automation streamlines operations and aligns all stakeholders, including managers, technicians, and engineers.
What Is Work Order Lifecycle Automation?
At its core, work order lifecycle automation is all about creating a structured process for handling maintenance tasks from start to finish. Every work order has a journey, and automation ensures that the journey is smooth and efficient with a structured work order management process.
A recent study found that manufacturing organizations implementing automated work order systems reduced processing time by up to 50% and improved order tracking accuracy by 75%, leading to significant gains in efficiency and productivity within just a few months.
The Work Order Lifecycle: From Request to Resolution
Let's break down what this journey looks like. A work order follows a structured path from the moment it is initiated to when it is finally closed. Understanding each stage helps identify where delays occur and how automation can help resolve them.
Request Initiation
The work order process begins with the reporting of a maintenance need, such as a failure, scheduled upkeep, or a potential hazard. However, when these requests are submitted via various methods like emails, calls, or informal notes, they can be easily overlooked, postponed, or entered multiple times. The absence of a unified system transforms what should be a straightforward submission into the initial weak link in the maintenance workflow.
Review and Approval
After a work order request is submitted, it must be validated and prioritized to ensure efficient resource allocation. However, when using manual systems, approvals are often based on availability rather than urgency. This lack of defined workflows can lead to low-priority tasks being addressed before critical issues, resulting in unnecessary delays, critical work orders being overlooked, and prolonged downtime.
Assignment
Once approved, the work order moves to assignment, ideally matching the task to a technician based on skill, location, and current workload. But without intelligent routing, assignments become guesswork, often landing with the wrong person. The result? Rework, wasted time, and delays that ripple across the maintenance schedule.
Execution
The task is carried out by a technician or team of techs who should have quick access to asset history, manuals, and inventory. But without mobile tools or digital records, valuable time is lost hunting down information or making unnecessary return trips, slowing execution and draining productivity.
Verification and Closure
Once the task is complete, it needs to be reviewed, validated, and closed in the system to ensure it was completed correctly. However, with paper-based and other manual systems, this step is often rushed or even skipped, leaving a trail of poorly documented events, unresolved issues, and unreliable maintenance records.
Documentation and Analysis
The final step is collecting and analyzing data from finished work orders to guide future planning, identify recurring problems, and assist with compliance. However, when it comes to inconsistent or manual documentation, insightful information gets lost in the process. Data is overlooked, and opportunities for improvement are missed. Streamlining this phase leads to data that is more reliable, trends that are borne out more clearly, and better-informed maintenance decisions enterprise-wide. In addition, improper documentation lacking an audit trail can result in audit failures and penalties for non-compliance.
Streamlining the Work Order Lifecycle Through Automation
Modern work order software automates every stage of the work order process, from creation to completion. Customizable forms and intelligent rules ensure accurate and standardized request submissions during intake. Conditional logic automates the approval of routine or low-risk tasks, eliminating manual delays and saving time.
Following approval, the system automatically assigns work orders to technicians based on predefined criteria such as skills, location, and workload, reducing errors and ensuring the right technician is dispatched.
Upon completion of the work, automated closure protocols are initiated, which can include quality checks and prompts for supervisor review.
The Work Order Automation Process
Approval Workflows that Fit Your Organization
Work Order Software (WOS) allows operations managers to define custom approval paths based on department, asset type, work type, criticality, cost thresholds and more. This means routine maintenance tasks can be approved instantly, while high-cost or critical work orders are routed for additional review, ensuring both speed and control.
Escalation Rules that Prevent Delays
Automation helps prevent work orders from falling through the cracks and getting missed. If a task remains unassigned or idle for a set period (e.g., four hours), the system triggers an escalation, either notifying a supervisor or reassigning the task to another technician. This ensures time-sensitive issues are addressed before they cause downtime.
Real-Time Notifications that Keep Everyone Aligned
When a new work order is assigned, updated, or reassigned, technicians are notified immediately. Supervisors get real-time updates on progress, delays, or missed deadlines. It also keeps communication tight, so everyone knows what they should be focused on.
Built-in Accountability and SLA Enforcement
These automation rules not only help to speed up processes, but they also help structure processes and improve visibility and adherence to service-level agreement (SLA) targets. Each action is logged, each delay flagged, and each task progresses with accountability baked in. Notifications and alerts are triggered as SLA due times are approaching or missed.
Benefits of Work Order Lifecycle Automation
Faster Turnarounds
Automated workflows reduce delays at every stage of the work order process. Requests are routed, approved, and assigned instantly, allowing technicians to start work sooner and complete tasks more quickly.
Reduced Backlog and Downtime
Automation also reduces downtime by expediting approvals and technician assignments. This results in a lower number of outstanding requests, reduced equipment downtime, and improved availability of assets.
Greater Transparency
Every action in the work order lifecycle is logged and can be traced. Managers can easily track progress, identify delays, and hold teams accountable with complete visibility into who did what and when.
Less Administrative Overhead
Automation handles repetitive tasks like routing, notifications, and updates. This reduces the manual workload on supervisors and coordinators, allowing them to focus on strategy and decision-making.
Better Reporting and Audit Trails
The Work Order Software logs data instantaneously, making reporting and compliance easier. This allows maintenance teams to observe trends, check performance, and improve operations on an ongoing basis.
How to Select the Best Work Order Software
Selecting quality Work Order Software is important, as it can directly affect how well your maintenance operations are managed in terms of efficiency, accountability, and responsiveness. Although many choices are available, not every platform will be flexible and extensive enough to automate the complete work order lifecycle.
No-Code Automation Builder
Seek software that enables you to build workflows without requiring coding. A no-code automation builder allows your team to customize request forms, approvals, escalations, and notifications using drag-and-drop tools.
Mobile App
Technicians are most effective when they can access and update work orders directly from the field. Choose a platform with a user-friendly mobile app that enables real-time updates, QR code scanning, access to equipment manuals, inventory lookup, and photo attachments.
SLA and Escalation Logic
Service Level Agreements (SLAs) are vital for tracking performance and setting expectations. A good work order management software should allow you to define SLA targets, monitor compliance, and escalate overdue work orders to supervisors or reassign them to available technicians.
Integration with Assets and Inventory
Work order management doesn't exist in isolation. Your chosen software should integrate seamlessly with asset registers, preventive maintenance schedules, and inventory systems. This ensures technicians have the proper context and parts available to complete tasks efficiently.
Additional Features to Look for
Be sure to select a work order management software that allows users to schedule recurring work orders for preventive maintenance and inspections. PM schedulers should have flexible options for scheduling recurring work orders and should not only support hourly, daily, weekly, monthly, and annual work orders but also seasonal schedules and work orders to be triggered by meter reading. Organizations operating in large facilities should look for a solution that has interactive floor plans and maps so users can easily view the location of work orders, requests, and assets. Also, make sure the work order software has a calendar view, which makes it easy to view and schedule work orders based on due dates and technician availability.
Choosing a Scalable Solution
Whether you're managing a single site or a multi-location enterprise, opt for a cloud-based solution that scales with your organization.
By focusing on these capabilities, you can select a work order solution that not only meets your current needs but also can support your business into the future as you grow.
Level up Work Order Management with Automation and Workflows
Manual work order management may have worked in the past, but today's fast-moving maintenance environments demand more. Relying on spreadsheets, emails, or sticky notes leaves too much room for errors, delays, and miscommunication. With modern Work Order Software, teams can move from reactive, manual processes to proactive, intelligent workflows that drive real results.
Automation not only optimizes every stage of the work order lifecycle but also imposes accountability, enhances service levels, and provides teams with real-time information to make highly informed decisions. Whether it’s automatic approvals, escalations, or mobile updates, every aspect of the maintenance pipeline gets quicker, sharper, and more trusted.
If you're still juggling work orders manually, it's time to level up. Embrace automation to improve efficiency, reduce downtime, and create a more responsive maintenance operation. Both technicians and management will be grateful, and shortly after implementation and onboarding, you’ll see positive results on work order completion performance and overall management.
TABLE OF CONTENTS
Keep Reading
What happens when your most experienced maintenance leader is planning on retiring, taking 20 ...
7 Aug 2025
Today’s maintenance operations have become more complex and sophisticated. Gone are the days ...
5 Aug 2025
Modern warehouses are instrumental to maintaining the smooth operations of supply chains, ...
1 Aug 2025
Computerized Maintenance Management Systems (CMMS) have proven to be essential tools for ...
31 Jul 2025
Sometimes it feels as if technology is expanding at the speed of light. This is an ...
29 Jul 2025
Data Center downtime can have a huge negative impact ranging from damage to the data center’s ...
25 Jul 2025
Whenever a company introduces a new process or technology, it’s followed by a period of ...
24 Jul 2025
Obsolescence often comes unexpectedly, mainly because little attention is given to the ...
22 Jul 2025
Imagine a world where critical assets run smoothly without unexpected downtime, maintenance ...
18 Jul 2025
Imagine you're going through a compliance audit, and the inspector asks for maintenance ...
10 Jul 2025
Maintenance managers understand that disasters are unpredictable and can have a massive ...
4 Jul 2025
Asset lifespan is a key concern for executives and maintenance and facility management teams. ...
3 Jul 2025
Your company recently invested funds and time for new CMMS software, and six months later, it ...
1 Jul 2025
As Computerized Maintenance Management Systems (CMMS) become more connected and cloud-based, ...
1 Jul 2025
Edge computing is an innovative technology that enables data to be processed at the source, ...
24 Jun 2025
Facility management has undergone a significant transformation in recent times. Take, for ...
20 Jun 2025
A facility maintenance plan is at the core of a facility’s operations. This organized ...
19 Jun 2025
In the early days, preventive maintenance could be done effectively with a trained eye and a ...
17 Jun 2025
Sticky notes fall off, whiteboard grids get wiped, and spreadsheets never beep when a ...
13 Jun 2025
Handing a slice of your maintenance workload to a contractor is less about “giving up ...
12 Jun 2025