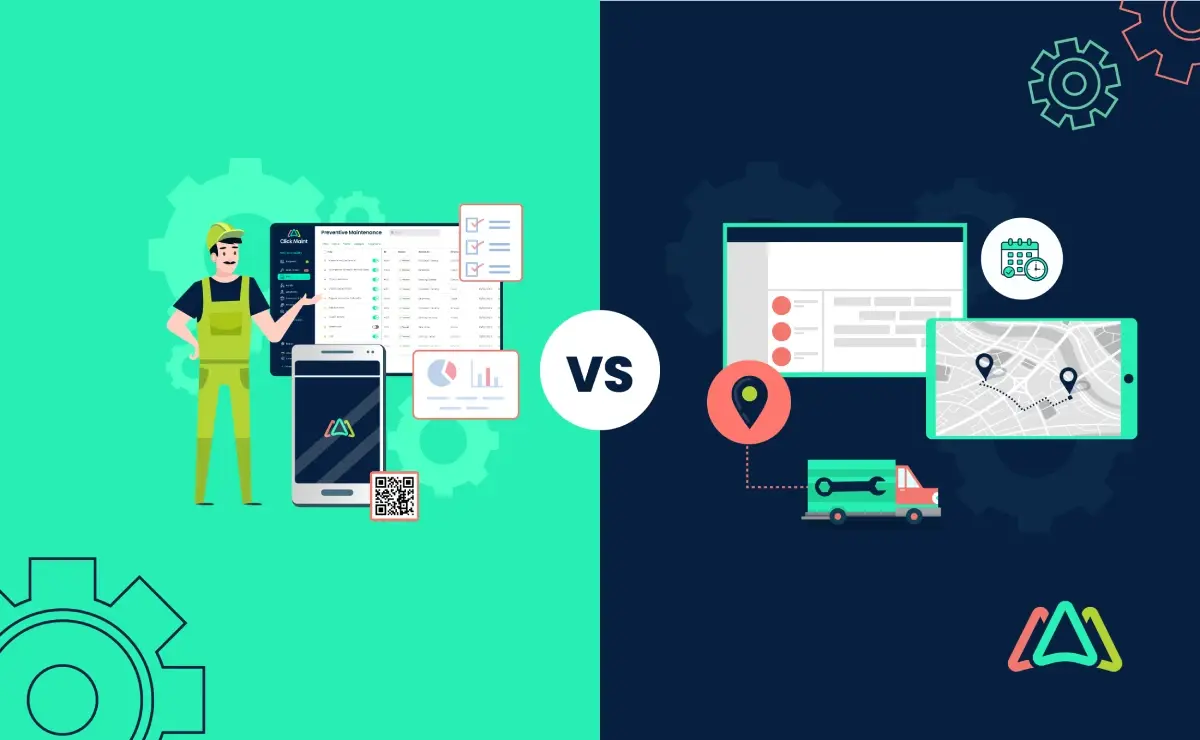
CMMS vs. Field Service Management Software: How to Choose Your Ideal Solution?
Introduction
More than ever, companies need help to keep up with industry innovations, mounting competition and tightening margins. Given these challenges, having the right tools and software can give operations managers a much-needed edge, especially in the maintenance and service sectors.
You might already know of two popular systems: CMMS (Computerized Maintenance Management System) and FSM (Field Service Management) software. Both aim to streamline operations and boost efficiency, but they do so differently.
Here, we’ll break down the differences between CMMS and FSM software and highlight the benefits of each, helping you figure out which suits your needs best. So, let's dive in!
Understanding CMMS and FSM Software
Let’s begin with a brief overview of CMMS and FSM systems.
CMMS Software:
CMMS manages asset maintenance schedules, work orders, inventory, and equipment history. It organizes maintenance tasks and ensures smooth operation. Here are the core functionalities of a CMMS:
1. Asset Management
- Equipment and Facility Management
- Asset Tracking
2. Maintenance Scheduling
- Preventive Maintenance
- Predictive Maintenance
3. Work Order Management
- Order Creation and Tracking
- Priority Management
4. Inventory Management
- Spare Parts Management
- Automated Reordering
5. Equipment History
- Maintenance History Logs
- Analysis and Reporting
6. Compliance and Safety
- Regulatory Compliance
- Safety Protocols
CMMS is best known for assisting maintenance teams in being proactive rather than reactive in their maintenance approach. This maintenance solution improves overall operational reliability and extends the life of critical assets.
FSM Software:
FSM systems are essential for managing and optimizing the activities of teams working outside the company's premises. Here is a list of the core FSM functions:
1. Dispatching Technicians
- Automated Scheduling
- Route Optimization
2. Managing Service Contracts
- Contract Management
- Warranty Tracking
3. Providing Real-Time Updates on Job Progress
- Real-Time Monitoring
- Instant Communication
4. Work Order Management
- Work Order Creation and Assignment
- Mobile Access
5. Inventory and Parts Management
- Field Inventory Tracking
- Parts Availability
6. Customer Relationship Management (CRM)
- Customer History and Preferences
- Customer Notifications
7. Performance Analytics and Reporting
- Job Performance Metrics
- Data-Driven Insights
8. Compliance and Safety
- Regulatory Compliance
- Safety Protocols
An FSM system’s strength is its ability to significantly improve the efficiency and effectiveness of field operations by managing and supporting a mobile workforce. In doing so, FSM software improves customer satisfaction through timely and effective service delivery and provides valuable data for continuous improvement.
Critical Differences Between CMMS and FSM Software
While CMMS and FSM software aim to enhance the efficiency of maintenance and service operations, they cater to distinct operational needs. Understanding these differences is crucial for maintenance managers to select the appropriate maintenance management tool for their business objectives and operational requirements.
CMMS
CMMS is best viewed as the primary tool for managing and maintaining assets and equipment within a facility. It excels at organizing and tracking work orders, scheduling preventive maintenance to minimize downtime, and managing inventory levels to ensure necessary parts and materials are always available. CMMS focuses on in-house maintenance, ensuring that equipment and assets operate smoothly, efficiently and for the long term.
FSM
Conversely, FSM is tailored to managing field operations and mobile workforces. It is designed to optimize technician scheduling and dispatching, handle service contracts efficiently, and provide real-time updates on job progress. FSM is particularly beneficial for businesses that rely on field service teams, as it ensures timely service delivery, enhances communication between the field and the office, and improves overall service coordination and customer satisfaction.
Maintenance managers are exploring digital operations solutions by determining whether their primary need is detailed asset management and preventive maintenance (CMMS) or optimizing field operations and service delivery (FSM). Now, we’ll look at the benefits and usefulness of each solution.
Evaluating the Benefits of CMMS for Your Organization
CMMS software offers a comprehensive suite of tools designed to streamline and optimize every aspect of asset management. Let’s explore CMMS’s key features.
Preventive Maintenance
A CMMS helps prevent unexpected equipment failures by planning and scheduling routine maintenance tasks, reducing downtime and extending the lifespan of company assets. This proactive approach ensures that maintenance is performed at optimal intervals as determined by maintenance managers. This strategy not only preserves the condition of equipment but also enhances overall operational reliability.
Work Order Management
The CMMS work order management feature lets maintenance managers create, assign, and track work orders, ensuring that maintenance tasks are completed promptly and effectively. With a CMMS, maintenance managers can prioritize tasks, allocate resources appropriately, and monitor the progress of each job in real time. This level of oversight helps ensure that maintenance activities are carried out with the right tools, parts, and personnel, thereby improving the efficiency and effectiveness of maintenance operations.
Inventory Management
Inventory management capabilities help maintenance managers to track the availability and usage of spare parts and supplies. This real-time feature ensures that the necessary items are always in stock to support ongoing maintenance activities. By managing inventory levels efficiently, CMMS reduces the risk of stockouts and overstock situations, leading to cost savings and better resource utilization. It also minimizes manual errors and streamlines procurement processes.
Reporting
The CMMS reporting functionality generates detailed insights into maintenance activities and associated costs. These reports provide real-time data on equipment performance, maintenance history, and expenditure, aiding in informed decision-making.
Maintenance managers can analyze trends, identify areas for improvement, and justify maintenance budgets with accurate, real-time data. Reporting data is central to strategic planning and demonstrating the value of maintenance activities to stakeholders.
Overall, CMMS software can help organizations substantially improve all maintenance strategies, enhance efficiency, reduce costs, and ensure the longevity and reliability of critical assets.
Benefits of Implementing FSM Software for Field Operations and Service Delivery
FSM software takes managing field services to the next level by providing powerful tools to enhance efficiency and service delivery.
Scheduling and Dispatching
FSM software uses advanced algorithms to schedule appointments and dispatch technicians based on skill sets, availability, and proximity to the job site. This feature ensures that the right technician is assigned to the right job at the right time, reducing travel time and maximizing productivity. The automated scheduling capabilities minimize manual intervention and errors, leading to more efficient and reliable service operations.
Real-time Tracking
Real-time tracking lets field managers monitor service requests and job progress in real time, providing visibility into the status of each task. This real-time oversight ensures that any issues or delays can be promptly addressed, improving response times and service reliability. Moreover, customers are kept informed about the status of their service requests, enhancing transparency and satisfaction. Tracking real-time field activities is critical to making data-driven decisions and optimizing field operations.
Mobile Capabilities
Field technicians directly benefit from access to all necessary information and tools on their mobile devices. They can receive job details, update statuses, communicate with the back office, and access customer history and documentation from the field. This seamless communication and access to information increase efficiency, reduce downtime and improve the accuracy of service delivery. Having mobile capabilities contributes to higher customer satisfaction because technicians can resolve issues quickly and effectively.
Performance Metrics
With FSM’s performance metrics, field managers can analyze data and gain insights into operations. They can identify areas for improvement using key performance indicators such as response times, job completion rates, and customer satisfaction scores.
By doing so, organizations can refine their strategies, enhance operational efficiency, and ensure that their field service teams deliver the highest level of service possible.
Overall, these FSM benefits enhance the efficiency and effectiveness of field operations, resulting in better resource utilization, improved service quality, and higher customer satisfaction.
Considerations for CMMS and FSM Integration and Scalability
When deciding between CMMS and FSM software, it's crucial to consider integration and scalability.
Integration
Both CMMS and FSM solutions offer integration capabilities that make it possible to seamlessly connect with an organization’s existing systems, such as ERP or CRM systems. CMMS integration eliminates data silos by providing a unified view of operations, enabling smoother workflows across different departments. Proper integration is crucial for informed decision-making and coordinated efforts across the organization.
Scalability
As a business grows, scalability becomes critical in handling increased workloads and expanding functionalities without compromising performance. Scalable software can accommodate a growing number of assets, users, and service requests, ensuring that it remains effective as a company’s operational demands increase. Selecting a scalable CMMS or FSM solution ensures it will continue to support a business’s needs and goals over the long term.
By prioritizing integration and scalability capabilities, CMMS and FSM solutions can remain valuable in driving operational success and efficiency well into the future.
Making an Informed Decision for Your Industry Needs
In addition to the information provided, the following will help determine an organization’s strategic reasons for maintenance management software or FSM.
Regulatory Compliance
Different industries have their regulatory requirements that must be adhered to. These may include safety standards, environmental regulations, and quality controls. To avoid costly legal issues and enhance your organization's credibility, ensure that your chosen CMMS or FSM software includes features that help you track and document compliance activities. These may consist of automated compliance reporting, audit trails, and adherence to industry-specific standards.
Industry Best Practices
Software that supports industry best practices can significantly enhance operational efficiency and effectiveness. For example, in manufacturing, best practices include preventive maintenance schedules and real-time equipment health monitoring. In field service, best practices involve optimizing technician routing and efficient work order management. By selecting software designed with these practices in mind, managers can feel confident that their operations are compliant and optimized according to the highest standards in their industry.
Unique Challenges
Every industry has its pain points—whether it's managing a large fleet of field technicians, maintaining a vast array of industrial equipment, or ensuring quick response times to customer service requests. Identifying software that can handle these unique challenges will provide tailored solutions to address your most pressing issues. If downtime is a significant concern, look for CMMS features that provide predictive maintenance capabilities. If field coordination is critical, prioritize FSM tools with robust scheduling and real-time tracking functionalities.
Using a Collaborative Approach
A collaborative approach that involves gathering insight from company stakeholders helps capture a comprehensive view of the operational requirements and challenges. Engaging maintenance teams, IT, operations, and finance departments in the decision-making process ensures that the software selected optimizes efficiency and effectiveness across all facets of the business. By doing so, managers can increase the likelihood of choosing a solution well-suited to the entire organization's needs, facilitating smoother implementation and greater overall satisfaction with the new system.
Conclusion
Selecting the right CMMS software is critical to achieving long-term success in maintenance and field service operations. By aligning CMMS or FSM software features with specific requirements, managers can streamline workflows, enhance productivity, and foster sustainable growth. Engaging with team members, considering regulatory and industry standards, and making a well-informed decision tailored to an organization’s goals are also key. With the right software, managers will be well-positioned to boost efficiency and drive success in their company’s operations.
TABLE OF CONTENTS
Keep Reading
What happens when your most experienced maintenance leader is planning on retiring, taking 20 ...
7 Aug 2025
Today’s maintenance operations have become more complex and sophisticated. Gone are the days ...
5 Aug 2025
Modern warehouses are instrumental to maintaining the smooth operations of supply chains, ...
1 Aug 2025
Computerized Maintenance Management Systems (CMMS) have proven to be essential tools for ...
31 Jul 2025
Sometimes it feels as if technology is expanding at the speed of light. This is an ...
29 Jul 2025
Data Center downtime can have a huge negative impact ranging from damage to the data center’s ...
25 Jul 2025
Whenever a company introduces a new process or technology, it’s followed by a period of ...
24 Jul 2025
Obsolescence often comes unexpectedly, mainly because little attention is given to the ...
22 Jul 2025
Imagine a world where critical assets run smoothly without unexpected downtime, maintenance ...
18 Jul 2025
Imagine you're going through a compliance audit, and the inspector asks for maintenance ...
10 Jul 2025
Maintenance managers understand that disasters are unpredictable and can have a massive ...
4 Jul 2025
Asset lifespan is a key concern for executives and maintenance and facility management teams. ...
3 Jul 2025
Your company recently invested funds and time for new CMMS software, and six months later, it ...
1 Jul 2025
As Computerized Maintenance Management Systems (CMMS) become more connected and cloud-based, ...
1 Jul 2025
Edge computing is an innovative technology that enables data to be processed at the source, ...
24 Jun 2025
Facility management has undergone a significant transformation in recent times. Take, for ...
20 Jun 2025
A facility maintenance plan is at the core of a facility’s operations. This organized ...
19 Jun 2025
In the early days, preventive maintenance could be done effectively with a trained eye and a ...
17 Jun 2025
Sticky notes fall off, whiteboard grids get wiped, and spreadsheets never beep when a ...
13 Jun 2025
Handing a slice of your maintenance workload to a contractor is less about “giving up ...
12 Jun 2025