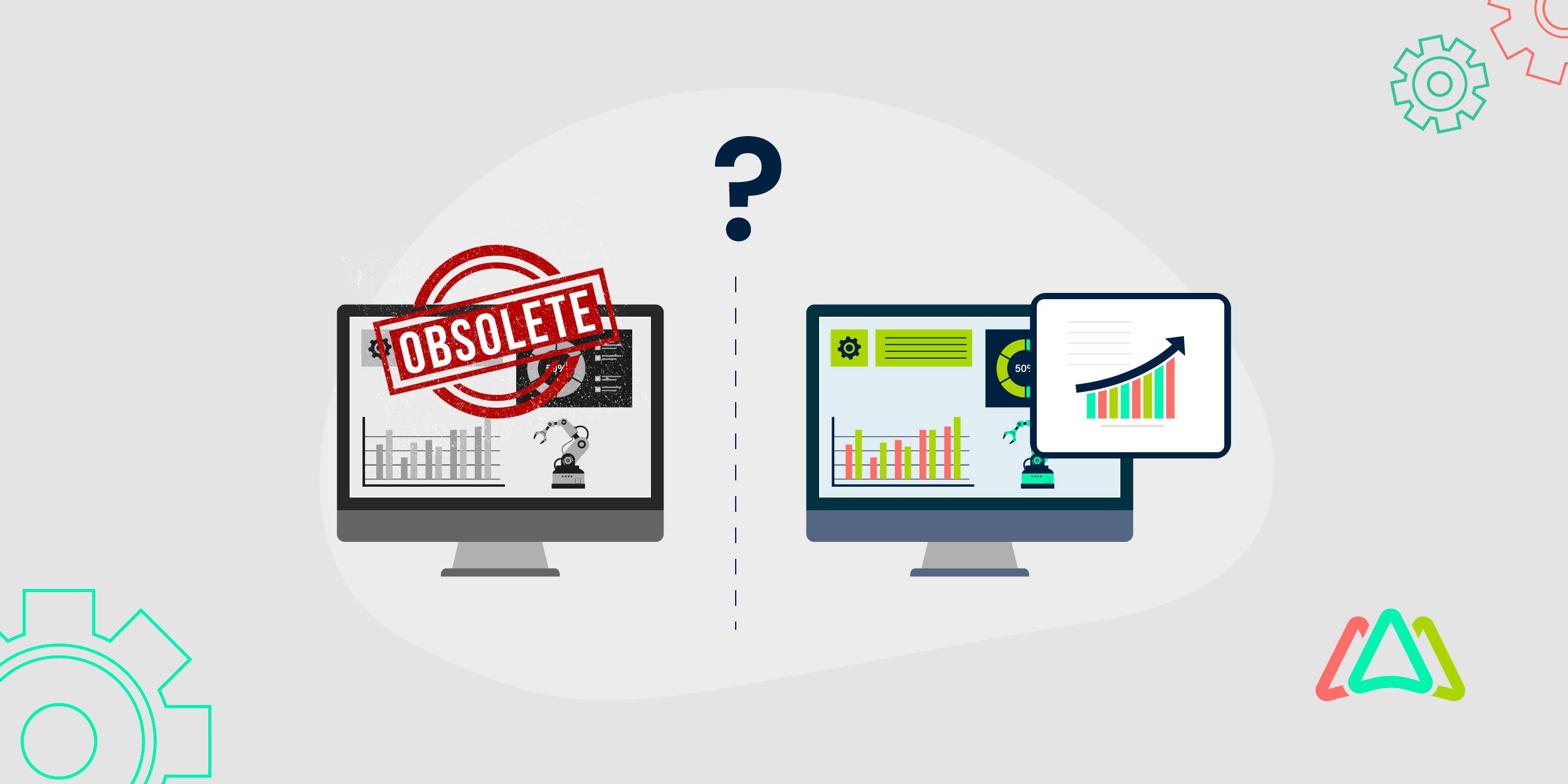
Will CMMS Software Stand the Test of Time or Become Obsolete?
In today's digital world, every decision needs to pass the test of strategic and operational alignment. This condition changes how maintenance software is used. Once considered the backbone of manufacturing operations, traditional Computerized Maintenance Management Systems (CMMS) now face an inflection point. With the rise of AI, IoT, and predictive analytics, many industry leaders are asking: Is the traditional CMMS still equipped to meet the demands of modern businesses, or is it becoming obsolete? As industries shift toward proactive, customer-centric maintenance strategies, the future of CMMS hinges not on its past success but on its ability to adapt, integrate, and drive measurable value across increasingly complex operational landscapes.
CMMS Continues to Provide Customer Value in the Age of Disruption
While new technologies emerge, CMMS software is still relevant. It ensures operations run smoothly and offers consistent value to customers. Modern CMMS platforms are the foundation of daily maintenance operations, assisting teams in organizing, prioritizing, and carrying out activities to maintain critical equipment.
Work order management remains one of the core functions of CMMS platforms. It serves as a link between identifying maintenance issues and promptly addressing them. CMMS software promotes efficient and effective work completion with automated task assignments, prioritization, and modifications. Teams can respond with speed and precision, reducing delays, preventing quality issues, and keeping operations on track.
CMMS platforms also play a key role in asset tracking and management. They go beyond basic record-keeping to give teams a complete view of asset health, usage, and performance. With this visibility, maintenance teams can make better decisions that lead to extending asset life, reducing downtime, and avoiding unexpected failures. CMMS software helps ensure critical systems run smoothly by centralizing data on equipment history.
Maintenance scheduling is another area where CMMS shines, particularly in its proactive approach to automating preventive maintenance tasks and routine inspections. Teams can utilize condition, usage, or time-based schedules to schedule work, reducing the likelihood of equipment breakdowns. These preventive measures allow production to proceed as planned, preventing costly interruptions and ensuring customer satisfaction.
The Imperative for Evolution: From Traditional CMMS to Predictive Maintenance
Traditional CMMS continues to offer value, but today’s assets are complex and require more precise and accurate maintenance intervention. The need for operational excellence calls for advanced strategies. Even with a properly managed CMMS, unplanned downtime still occurs. This may lead to delivery delays, affect production, and decrease customer satisfaction. That is where the power of Predictive Maintenance (PdM) comes into play.
The Winds of Change: Technologies Driving Customer-Centric Maintenance
The Internet of Things (IoT): Real-time insights for proactive customer assurance. IoT sensors provide a continuous stream of data on asset health, offering unprecedented insight. This real-time data allows organizations to find potential issues ahead of time and prevent failures that could interrupt customer operations.
Artificial Intelligence (AI) drives customer satisfaction: AI can study large datasets from IoT sensors and previous maintenance logs. It helps predict failures, improve maintenance schedules, and find the reasons behind incidents..
Predictive Maintenance (PdM): Anticipates disruptions in advance. PdM combines IoT and AI. It helps organizations predict when an asset may fail. This proactive approach lets maintenance teams step in before a breakdown happens and reduces disruptions to production delivery.
The Need for Traditional CMMS to Adopt Predictive Maintenance
Old-fashioned maintenance systems are good at tracking and planning preventive maintenance and inspections. Still, they often depend on outdated information and set schedules. This information can cause problems, like not keeping up with maintenance, which leads to unexpected failures. Over-maintenance (performing PMs and inspections when not needed) increases costs and drives prices up. On the flip side, insufficient maintenance causes breakdowns, delays, and ultimately leads to issues that negatively impact customer satisfaction.
The future of traditional CMMS software can thrive if it shifts to a next-gen AI/IoT-driven predictive tool. This evolution doesn’t aim to replace CMMS's core functions. Instead, it enhances them using predictive analytics.
CMMS in Transition: Becoming a Proactive Partner in Delivering Customer Value
Modern CMMS vendors are actively integrating IoT connectivity, AI-powered analytics, and predictive maintenance capabilities to enhance their platforms and, by extension, their users' ability to deliver consistent customer value. Here's how CMMS is adapting to become a more modern customer-focused tool:
● Mobile-First Design: Giving personnel mobile access to work orders and information guarantees prompt resolution of possible problems while reducing adverse effects on customer service.
● Cloud-Based Deployment: Cloud-based CMMS provides accessibility and scalability, enabling smooth integration with other enterprise systems like CRM and ERP that affect customer experience.
● Enhanced Analytics and Reporting: Modern CMMS platforms offer sophisticated abilities to monitor future maintenance performance and visualize IOT data, directly impacting customer happiness and operational efficiency. The table below showcases that predictive maintenance will dominate, reducing reliance on traditional preventive CMMS-based methods.
Table 1: Maintenance Strategy Adoption Trends (2024)
Maintenance Approach |
Adoption Rate (2024) |
Expected Growth by 2026 |
Reactive (Breakdown) |
30% |
↓ 10% |
Preventive (Scheduled) |
50% |
→ 55% |
Predictive (AI/IoT-Driven) |
20% |
↑ 35% |
(Sources: Technavio, Deloitte, Authorea, Markets & Markets)
Market Signals Demand a Customer-Focused CMMS
The CMMS market will keep expanding from 2025 to 2034, showing that a central system for managing maintenance is still essential. This growth is increasing due to the need for CMMS systems that clearly improve the reliability of the equipment and how well operations run, as these things are essential to customers. Companies want CMMS software that can reduce equipment downtime, ensure consistent quality, and lower costs, all of which satisfy customers. The shift toward using predictive methods, now commonly found in modern CMMS systems, also supports this trend.
Traditional vs. Modern: The Shift Towards Proactive Customer Assurance
The limitations of traditional CMMS highlight the necessity of embracing the modern, evolving approach that prioritizes customer value:
Table 2: Traditional Vs Modern CMMS
Feature |
Traditional CMMS |
Modern CMMS with IoT & AI |
Impact on Customer Value |
Data Collection |
Manual, periodic checks |
Real-time data from IoT sensors |
Early detection of issues prevents disruptions to production/service, ensuring consistent customer delivery. |
Analytics |
Basic reporting, limited insights |
AI/ML for predictive insights |
Proactive maintenance minimizes downtime, ensuring reliable product/service availability for customers. |
Maintenance Scheduling |
Time-based or reactive |
Predictive based on real-time data |
Reduced unexpected failures mean fewer disruptions to customer orders and service schedules. |
Mobility |
Limited or no mobile access |
Mobile apps for on-the-go access |
Faster response times to potential issues minimize delays and impact on customers. |
Integration |
Standalone or limited integration |
Seamless with IoT, ERP, CRM, etc. |
A holistic view of operations ensures maintenance alignment with customer needs and delivery schedules. |
(Sources: IBM, Microsoft, Siemens, Oracle, SAP, McKinsey)
Unlike standalone AI Tools, modern CMMS uses connectivity, data, and AI to turn maintenance into a strategic function that directly enhances customer value. The table below shows that modern CMMS costs more upfront but delivers faster ROI via AI-driven efficiency.
Table 3: Cost-Benefit Analysis: Traditional vs. Modern CMMS
Factor |
Traditional CMMS |
Modern CMMS (AI + Cloud) |
Upfront Cost |
$10K–$50K |
$20K–$ 100 K+ |
Downtime Reduction |
10–20% |
30–50% |
Implementation Time |
3–6 months |
1–3 months (cloud-based) |
ROI Period |
12–18 months |
6–12 months |
(Sources: Logic Line, Click Maint, MicroMain)
The industry adoption of CMMS & next-gen solutions table highlights that industries with a strong emphasis on operational uptime and complex assets are leading the way in AI/IoT adoption within their CMMS strategies, recognizing the direct link between proactive maintenance and consistent customer value. Furthermore, the cost-benefit analysis demonstrates that while modern CMMS may have a higher initial investment, the faster ROI driven by significant downtime reduction ultimately translates to better long-term value and the ability to meet customer demands consistently.
CMMS Future Outlook
Let us look at some stats that showcase the outlook of CMMS software. The table below shows that AI-enhanced CMMS is gaining market share while traditional CMMS is declining.
Table 4: CMMS vs. Alternatives Market Share
Year |
Traditional CMMS |
Modern CMMS (AI/IoT) |
EAM Systems |
Standalone AI Tools |
2020 |
65% |
15% |
15% |
5% |
2024 |
40% |
35% |
18% |
7% |
2028* |
20% |
50% |
20% |
10% |
(Sources: Markets & Markets, Verdantix, IOT-Analytics, Market research Future)
The growing use of AI and IoT in CMMS indicates a clear route towards more proactive and effective maintenance procedures that directly increase customer value. The ROI comparison further emphasizes the economic sense of transitioning to modern CMMS solutions. Lastly, the industry reliance data shows that CMMS is still an important tool, especially in sectors with many assets. Instead of replacing it entirely, AI should be used to improve its capabilities.
Modern vs. Traditional CMMS: Feature Comparison
A core feature comparison table between modern and traditional CMMS highlights a distinct evolutionary path in maintenance management software, moving from foundational organizational tools to sophisticated, data-driven platforms. Traditional CMMS systems often establish the baseline by digitizing work orders and asset records primarily through manual input and calendar-based scheduling. With its embrace of cloud architecture and integration of IoT sensors for real-time data collection, modern incarnations mark a substantial advancement. This situation offers a more proactive approach using AI for early predictive maintenance capabilities and enabling more dynamic, mobile-first operations.
The next generation expands on this advancement by focusing on specialized predictive and prescriptive analytics. These cloud-native tools employ deep learning and potent AI to accurately identify anomalies, predict errors, and provide targeted solutions. This increasing sophistication—from basic tracking to real-time monitoring and AI-driven foresight—correlates with suitability, scaling from managing static assets in smaller facilities to optimizing complex, critical equipment in large industrial plants.
Table 5: Core Feature Comparison
Feature |
Traditional CMMS (e.g., MP2, DIMO) |
Modern AI/IoT CMMS (e.g., Click Maint, Fiix) |
Next-Gen Predictive Tools (e.g., Augury, Senseye) |
Work Order Management |
Basic scheduling |
Mobile-first, automated workflows |
(Focuses on alerts only) |
Asset Tracking |
Manual data entry |
IoT sensor integration (real-time data) |
AI-driven anomaly detection |
Maintenance Approach |
Preventive (calendar-based) |
Predictive (AI-powered recommendations) |
Prescriptive (AI suggests fixes) |
Cloud-Based |
Often on-premise |
Fully cloud-native |
Cloud-only |
AI Capabilities |
Minimal |
Failure prediction |
90%+ accuracy with deep learning |
Best For |
Small facilities with static assets |
Mid-size manufacturers |
Fortune 500 plants with critical equipment |
(Sources: Click Maint, Fiix, MVP One, DIMO Maint, Augury, Senseye)
The above table shows how modern CMMS platforms like Click Maint improve upon traditional CMMS limitations by absorbing new technology like mobile, AI/IoT/cloud, being less costly than standalone AI technologies, and integrating failure prediction capabilities.
CMMS Is Evolving—But Not in the Same Way for Everyone
The idea that CMMS is becoming obsolete overlooks a nuanced reality. CMMS platforms are changing due to the need for better asset reliability, improved operational efficiency, and greater customer value.
However, this evolution is not linear or uniform across the industry.
Organizations adopt CMMS based on their size, complexity of operations, and level of digital maturity. For smaller businesses, traditional CMMS platforms are key. They centralize work orders, simplify asset tracking, and help with preventive maintenance. These organizations often focus on digitizing manual tasks. They build basic workflows first, then add advanced analytics or AI.
Mid-sized manufacturers are ready to expand their use of CMMS. They might pay attention to condition-based support, mobile features, or access to the cloud. With these features, daily maintenance activities can be linked to long-term planning.
Presently, CMMS is being tested by big companies with complicated processes and critical assets. Predictive repair, AI insights, and IoT integration are becoming vital to them. The goal of this change is not only to eliminate downtime and costly repairs but also to improve real-time performance across global sites.
Customer maturity also plays a crucial role. Organizations with a culture of continuous improvement and strong data governance are better positioned to embrace next-generation CMMS tools. Others may need to first build confidence in core capabilities before advancing.
In reality, CMMS isn’t disappearing; it’s evolving and diversifying. The future won't just be one solution replacing another. Instead, it will be an ecosystem of tools that grows with companies and helps them progress. CMMS needs to move from a back-office tool to a key driver of customer value.
For any organization—whether just getting started or at an advanced stage of fine-tuning predictive models—the question is no longer “Will CMMS survive?” but rather, “How will we evolve our maintenance strategy to stay competitive?” Investing wisely is key. Those who align their CMMS with operational goals and technology-led customer outcomes will lead the next era of resilient, data-driven manufacturing.
TABLE OF CONTENTS
Keep Reading
Computerized Maintenance Management Systems (CMMS) have increasingly become the go-to tools ...
19 Aug 2025
It doesn’t seem to matter which energy provider you choose; the bottom line is that energy ...
15 Aug 2025
In FDA-regulated industries such as pharmaceuticals, medical devices, biotechnology, and food ...
14 Aug 2025
B2C businesses, such as retail, hospitality, and food service, operate in a highly ...
8 Aug 2025
What happens when your most experienced maintenance leader is planning on retiring, taking 20 ...
7 Aug 2025
Today’s maintenance operations have become more complex and sophisticated. Gone are the days ...
5 Aug 2025
Modern warehouses are instrumental to maintaining the smooth operations of supply chains, ...
1 Aug 2025
Computerized Maintenance Management Systems (CMMS) have proven to be essential tools for ...
31 Jul 2025
Sometimes it feels as if technology is expanding at the speed of light. This is an ...
29 Jul 2025
Data Center downtime can have a huge negative impact ranging from damage to the data center’s ...
25 Jul 2025
Whenever a company introduces a new process or technology, it’s followed by a period of ...
24 Jul 2025
Obsolescence often comes unexpectedly, mainly because little attention is given to the ...
22 Jul 2025
Imagine a world where critical assets run smoothly without unexpected downtime, maintenance ...
18 Jul 2025
Imagine you're going through a compliance audit, and the inspector asks for maintenance ...
10 Jul 2025
Maintenance managers understand that disasters are unpredictable and can have a massive ...
4 Jul 2025
Asset lifespan is a key concern for executives and maintenance and facility management teams. ...
3 Jul 2025
Your company recently invested funds and time for new CMMS software, and six months later, it ...
1 Jul 2025
As Computerized Maintenance Management Systems (CMMS) become more connected and cloud-based, ...
1 Jul 2025
Edge computing is an innovative technology that enables data to be processed at the source, ...
24 Jun 2025
Facility management has undergone a significant transformation in recent times. Take, for ...
20 Jun 2025