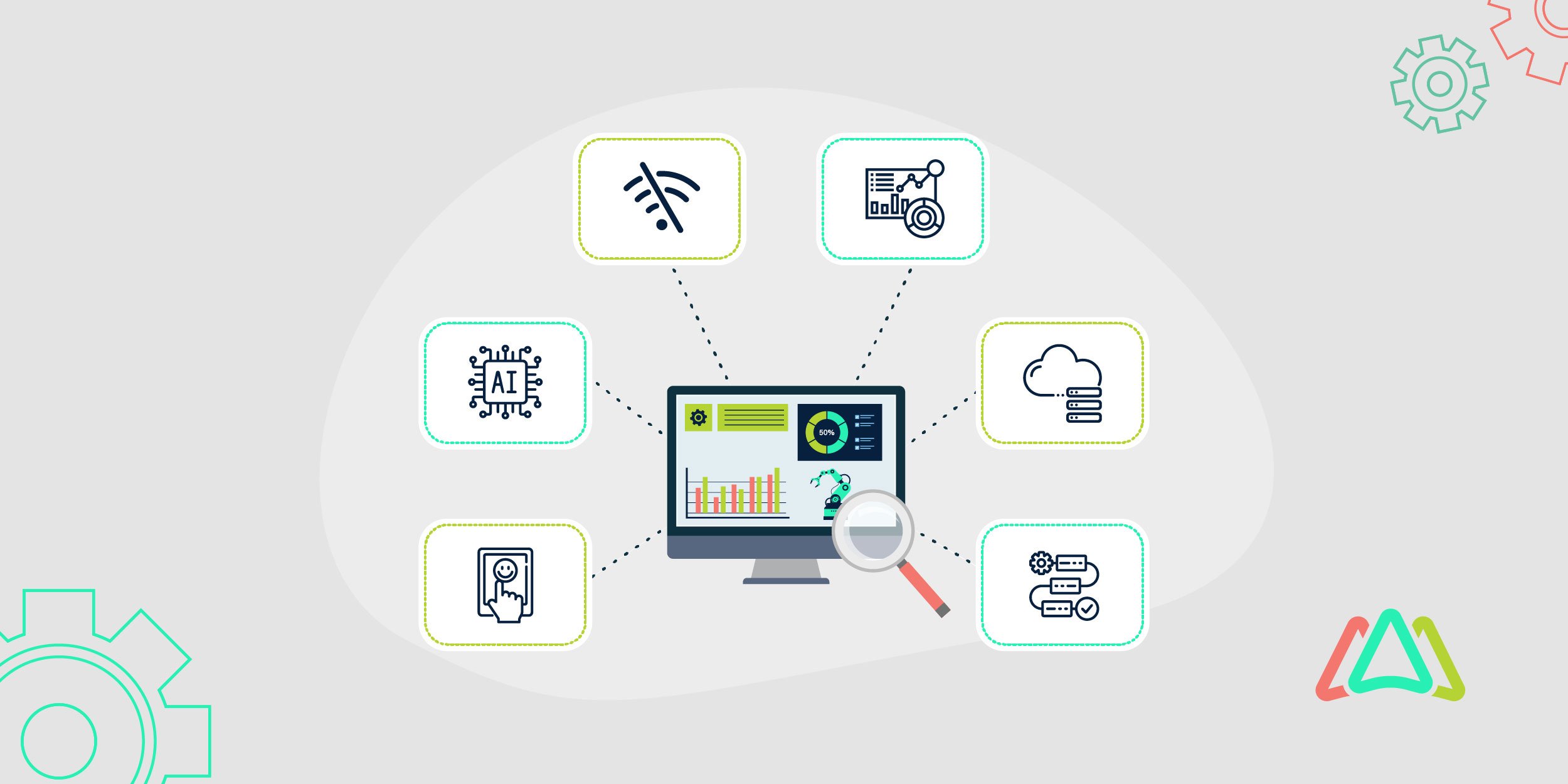
10 Things Businesses Should Look for When Evaluating CMMS in 2025
The business world is very different from a decade ago. Technological advancements have grown so rapidly that what was considered cutting-edge a couple of years ago is now considered dated and obsolete. As it relates to maintenance and facilities departments, increasing economic challenges have motivated businesses of all sizes and industries to find a maintenance management solution that can stand the test of time.
For these reasons, choosing the right Computerized Maintenance Management System (CMMS) is paramount. Whether you're overseeing maintenance operations for a large manufacturing facility or managing critical assets in healthcare, hospitality, or a school campus, the criteria for evaluating CMMS solutions have evolved to meet the demands of modern businesses where change is a constant.
We are well into 2025, and businesses understand its fiscal challenges. This means increased efficiency and lower costs are more critical than ever. With this in mind, this article explores ten essential factors organizations should consider when selecting a CMMS solution.
1. User-Friendly Interface (UI/UX)
Nothing deters maintenance team members more than a cumbersome and difficult-to-navigate CMMS. For this reason, having a user-friendly interface is one of the most critical factors in successfully adopting any CMMS.
User-friendly means having a clean, intuitive design that helps reduce the learning curve, allowing tech-savvy users and less experienced team members to understand how to navigate the system quickly. When screens are clutter-free, menus are logically organized, and workflows are easy to follow, it leads to faster onboarding, fewer errors, and higher engagement from maintenance teams. This means less time spent in training sessions and more time focused on actual maintenance tasks.
Usability expectations will increase in 2025, especially as digital tools become more common across front-end roles. A well-designed CMMS should feel self-explanatory and intuitive. This interface type will naturally guide users through tasks like logging work orders, checking asset history, or assigning jobs.
It’s important not to overlook the importance of mobile responsiveness, which is no longer a luxury but a necessity. The introduction of mobile accessibility for field technicians marked a considerable breakthrough in CMMS's ability to improve efficiency wherever maintenance team members were. However, to get the most out of CMMS solutions, they need to offer the same smooth experience on tablets or phones that they do on desktops.
2. AI-Driven Insights and Predictive Maintenance
As maintenance operations become more data-driven, AI-powered features are increasingly important in modern CMMS platforms. This is especially the case for larger organizations with critical, high-value assets. AI's undeniable benefit is its ability to sift through vast amounts of equipment data, historical work orders, and sensor inputs to identify patterns that human eyes might miss. These insights allow businesses to shift from reactive maintenance to predictive strategies, which help prevent costly breakdowns before they occur.
Predictive maintenance schedules, powered by AI algorithms, reduce unplanned outages, extend the life of assets, improve safety, and help optimize spare parts inventory. With AI assistance, a CMMS can recommend ideal maintenance intervals based on actual usage patterns instead of relying on generic manufacturer guidelines.
AI's predictive insights can lead to significant cost savings and improved operational resilience in manufacturing, energy, or healthcare industries, where equipment reliability is mission-critical. This translates into an overall improvement in operational efficiency and an uptick in a company's bottom line. Organizations investing in these capabilities will be better positioned for long-term success as AI evolves.
3. Customizable Workflows & Automation
Creating customizable workflows and automation capabilities is critical to ensure glitch-free maintenance operations with a CMMS. With these capabilities, maintenance operations will run smoothly, especially in larger or more complex organizations.
A robust CMMS with this capability allows businesses to tailor approval processes, task assignments, and notification settings to match their internal procedures. This means automatically routing work orders based on criteria like equipment type, job priority, technician skill set, or even geographic location. The idea behind this is that the more granular the analysis, the better the system can reflect the real-world workflow within your organization.
Furthermore, automation can dramatically reduce delays and miscommunications for teams managing high volumes of requests or operating across multiple departments.
For example, a faulty AC vent might be automatically flagged as urgent and routed to the HVAC team, while a routine HVAC inspection could be scheduled during off-peak hours. These automated rules relieve managers from micromanaging tasks and allow them to focus on strategic maintenance oversight, knowing that the right person is always assigned to the right job at the right time.
4. Offline Mobile Capability
We briefly touched on the benefits of CMMS mobile accessibility. However, there's another side to this capability: offline mobile functionality. This, too, is a must-have feature for maintenance teams operating in areas where internet connectivity is unreliable or nonexistent. These include remote facilities, basements, mechanical rooms, or large industrial sites.
A CMMS with offline functionality allows technicians to view work orders, access asset information, and log completed tasks even when disconnected from WiFi or direct cell service. It also lets technicians focus on their tasks by recording their maintenance activities in real time instead of relying on memory or handwritten notes to be entered into a desktop later. This reduces the risk of delays, missed updates, or lost information. Once the device regains a connection, the data is automatically synced, ensuring the system remains up to date without disrupting workflow.
5. Strong Asset Management Capabilities
When thinking about asset management in a CMMS context, we're referring to a system of tracking, organizing, and maintaining physical equipment and infrastructure throughout its lifecycle. The purpose is to ensure optimal performance, reliability, and cost-efficiency. To achieve this end, asset management involves storing detailed information about each asset, including its location, condition, maintenance history, and documentation.
It follows that strong asset management features are fundamental to any effective CMMS. A well-organized asset list makes it easier for maintenance teams to find equipment, see related parts, and restock as needed. This helps technicians fix problems faster and ensure nothing gets missed during checkups or routine maintenance. If the CMMS includes barcode or QR code scanning, teams can quickly access equipment details on a mobile device; this saves time and avoids the hassle of digging through paper files or long lists.
A robust asset management module also serves as a digital hub for everything related to any piece of equipment and its related information entered into the CMMS's database. This can include manuals, wiring diagrams, photos, past work orders, and detailed maintenance history. Having all this digitized information readily available in one place helps technicians make informed decisions, speeds up diagnostics and repairs, and improves continuity when teams change or expand. Over time, asset management functionality also supports better lifecycle planning and capital investment decisions by giving managers a clearer picture of asset performance, health, and total cost of ownership.
6. Advanced Reporting & Dashboards
Advanced reporting and dashboards are central for transforming raw maintenance data into actionable insights. Many modern CMMSs offer real-time tracking of key performance indicators (KPIs) such as Mean Time to Repair (MTTR), Mean Time Between Failures (MTBF), and planned vs. unplanned maintenance ratios.
These vital metrics help maintenance teams monitor equipment performance, identify inefficiencies, and measure progress toward maintenance goals. In addition, their dashboards are customizable and visually clear, displaying a snapshot of performance relevant to their role. This means that the status of an organization's maintenance operations is available at a glance.
Beyond generating these snapshots, advanced reporting capabilities let maintenance managers drill down into specific data sets and create custom or exportable reports. This means they can analyze downtime trends for a particular asset, review technician productivity, or prepare compliance documentation for audits.
These reports help organizations make better, data-driven decisions. More specifically, maintenance leaders can uncover patterns and justify budget needs, elevating maintenance to a strategic business function.
7. Integration Capabilities (APIs & Webhooks)
CMMS integration capabilities refer to the software's ability to connect and share data with other systems (like ERP, IoT sensors, HR applications, or accounting software). These capabilities translate into streamlined workflows, improved data accuracy, and centralized control over maintenance operations.
Integration capabilities are a key consideration when choosing a CMMS, especially for organizations that rely on multiple systems to manage operations. A CMMS with robust APIs (Application Programming Interfaces) and webhooks can seamlessly connect with enterprise resource planning (ERP) systems, building management systems (BMS), IoT sensors, procurement tools, and HR platforms.
Having these integrations eliminate data silos because information can flow freely between systems, reducing the need for manual data entry. While integration capabilities are a time-saver, they also improve overall accuracy.
8. Cloud-Based with High-Security Standards
Most IT departments prefer cloud-based CMMSs with strong security standards. In fact, for organizations concerned about handling sensitive data or operating in regulated industries like healthcare, defense, or pharmaceuticals, having a secure cloud-based maintenance solution is a non-negotiable issue.
The reasons are straightforward. Cloud-based platforms offer the advantage of accessibility from anywhere, automatic updates, and lower infrastructure costs, and many CMMSs are built with robust safeguards.
When researching CMMS solutions, look for those that adhere to security frameworks such as SOC 2 compliance, ensuring the provider has controls to protect data confidentiality, availability, and integrity.
Additional security features like Single Sign-On (SSO), Multi-Factor Authentication (MFA), and routine data backups are critical for protecting against unauthorized access and minimizing the risk of data loss. SSO streamlines user access while reducing password fatigue, and MFA adds an extra layer of protection against breaches.
Regular backups ensure that an organization's data remains safe and recoverable in the event of a system failure or cyberattack. Unfortunately, in this technological age, threats to data integrity remain a daily concern. By investing in a CMMS with enterprise-grade security, organizations can have peace of mind while maintaining compliance with internal and external data protection standards.
9. Scalability & Configurability
When it comes to ensuring that a CMMS can grow and transform with an organization's changing demands, scalability and configurability stand out. Scalability refers to the system's ability to grow with an organization by handling more assets, users, locations, and data without compromising performance. Configurability, however, is the system's flexibility to adapt to specific workflows, user roles, and operational requirements without complex coding.
A scalable CMMS allows you to add users, assets, and locations without overhauling the platform or migrating to a new system. This ensures consistency in tracking and managing maintenance, even as an organization's operations grow and evolve.
On the other hand, configurability allows maintenance managers to tailor roles, permissions, and workflows. This means the system can be adapted to match a team's structure and the organization's specific processes without having to move to a next-generation CMMS.
A flexible CMMS empowers maintenance teams to work efficiently and maintain control over how data is shared and tasks are managed, independent of a company's size or industry.
10. Strong Onboarding, Support & Product Enablement Tools
A CMMS is only as good as how it is used. Proper use and full team engagement are paramount in achieving operational goals. For this reason, having strong onboarding and support can make or break the success of a CMMS implementation.
A vendor that offers structured onboarding—complete with guided setup, data import assistance, and role-based training—helps maintenance teams get up and running quickly and confidently.
Even for tech-savvy users, there is still a learning curve when new technology is introduced. When an organization is shifting from paper-based systems to outdated software, where data migration and user adoption are needed, comprehensive onboarding and support are even greater.
Seek out enablement tools like searchable help centers, how-to videos, and responsive customer support. All of these will ensure users can find answers and solve problems as they arise. Whether a technician in the field needs help with the mobile app or a manager looking to create a custom report, having access to timely, user-friendly support resources will ensure uninterrupted CMMS use.
A strong CMMS support system helps build trust in the software, encourages teams to use it to its full potential, and assists organizations in achieving the results they seek.
Conclusion:
We've covered a lot of ground here, and that's because there's a lot to know about how to proceed when making a CMMS investment in 2025. However, the most important takeaway is to select a CMMS with capabilities that not only meet your current needs but can also meet your future needs over time. For organizations looking for an affordable, user-friendly, modern CMMS that has first-class customer support, check out Click Maint CMMS.
TABLE OF CONTENTS
Keep Reading
Computerized Maintenance Management Systems (CMMS) have increasingly become the go-to tools ...
19 Aug 2025
It doesn’t seem to matter which energy provider you choose; the bottom line is that energy ...
15 Aug 2025
In FDA-regulated industries such as pharmaceuticals, medical devices, biotechnology, and food ...
14 Aug 2025
B2C businesses, such as retail, hospitality, and food service, operate in a highly ...
8 Aug 2025
What happens when your most experienced maintenance leader is planning on retiring, taking 20 ...
7 Aug 2025
Today’s maintenance operations have become more complex and sophisticated. Gone are the days ...
5 Aug 2025
Modern warehouses are instrumental to maintaining the smooth operations of supply chains, ...
1 Aug 2025
Computerized Maintenance Management Systems (CMMS) have proven to be essential tools for ...
31 Jul 2025
Sometimes it feels as if technology is expanding at the speed of light. This is an ...
29 Jul 2025
Data Center downtime can have a huge negative impact ranging from damage to the data center’s ...
25 Jul 2025
Whenever a company introduces a new process or technology, it’s followed by a period of ...
24 Jul 2025
Obsolescence often comes unexpectedly, mainly because little attention is given to the ...
22 Jul 2025
Imagine a world where critical assets run smoothly without unexpected downtime, maintenance ...
18 Jul 2025
Imagine you're going through a compliance audit, and the inspector asks for maintenance ...
10 Jul 2025
Maintenance managers understand that disasters are unpredictable and can have a massive ...
4 Jul 2025
Asset lifespan is a key concern for executives and maintenance and facility management teams. ...
3 Jul 2025
Your company recently invested funds and time for new CMMS software, and six months later, it ...
1 Jul 2025
As Computerized Maintenance Management Systems (CMMS) become more connected and cloud-based, ...
1 Jul 2025
Edge computing is an innovative technology that enables data to be processed at the source, ...
24 Jun 2025
Facility management has undergone a significant transformation in recent times. Take, for ...
20 Jun 2025